Dos and Don’ts When Injecting Molding
Like any manufacturing process, injection molding has its pros and cons. Some parts are easier to mold than others, and if you don’t know what you’re doing, things can go wrong quickly. For a novice trying to injection mold a part for the first time, or even an experienced engineer who normally works with other processes, it’s easy to fall into certain traps that result in a brittle, ugly, or deformed part. This article looks at five common mistakes in the injection molding process and offers advice on how to avoid them.
1.Wall Thickness Variation
Unlike CNC machined or 3D printed parts, which come in many forms, injection molded parts often look similar: thin, shell-like objects without any deep sections of solid material. This is because of how injection molding works. When a mold is filled with liquid material, that material must cool before it becomes solid; if some areas cool faster than others, the cooler areas solidify and shrink before others, creating stresses that cause the part to warp.
One way to avoid this warping is to make sure no area is much thinner than others because the thinner areas cool faster. The ideal situation is to have completely uniform wall thickness, but if that’s not possible, the transition between thin and thick walls should be as gradual as possible.
Rules to follow:
- Thin wall thickness should not be less than 40% of the adjacent wall thickness
- Materials such as polyurethane and long fiber reinforced plastic cannot accommodate thin walls
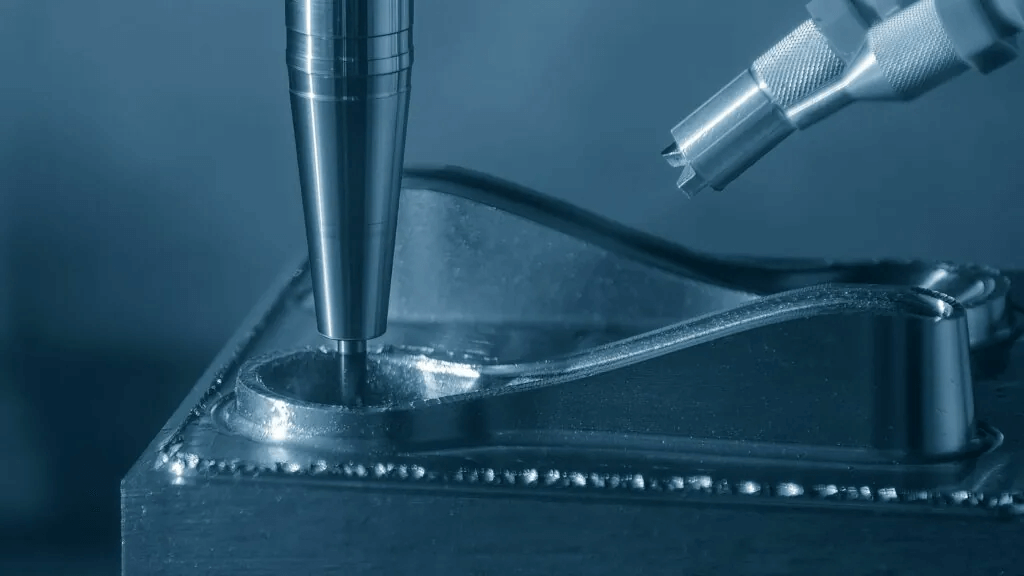
2.CAD files converted from other formats
When designing injection molded parts, you need to start from scratch and tailor each step of the product life cycle to the injection molding process. This means that you cannot directly convert a 3D printed file such as .STL to an injection molding format. Even if you convert the .STL to a .STEP file, the result will still be a 3D object that was originally composed of triangles, while injection molding interprets the shape as a series of curves. While there are reverse engineering packages for converting .STL files (back) to different formats, they require as much or even more expertise than designing a new part.
3.Parting line position error
In the injection molding process, the parting line is the dividing line between the core mold and the cavity mold. Its position affects the success rate and appearance of the molded part. Improperly placed parting lines can cause the following issues:
- Flash, material leaking out of the tiny gap between the core and cavity
- The need for an additional ejection step
Parting lines are best placed along sharp edges. This makes the parting line less noticeable and reduces the likelihood of burrs and other undesirable effects. Many CAD packages include parting line analysis features to help you determine the ideal location. However, your software may not understand the actual end application of the part, which is also an important factor in determining the location of the parting line.
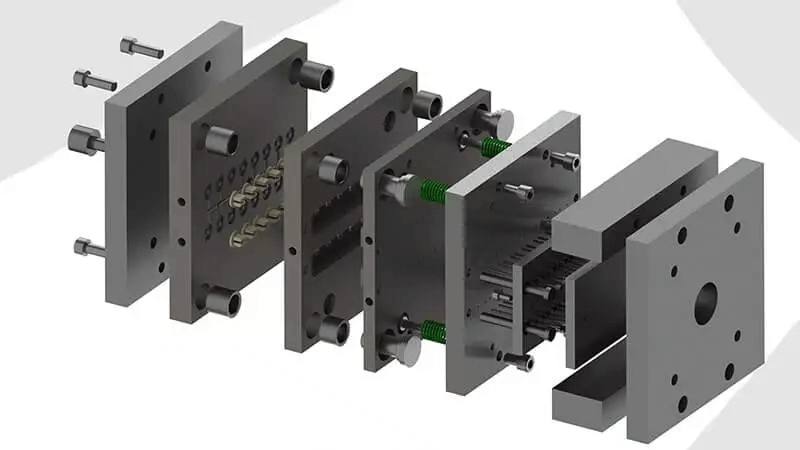
4.Use vents less than 1 degree
In the injection molding process, draft angle or taper is an angle incorporated into the design to make it easier to demold. Draft angle can also reduce warping or breakage of the part. One of the most common mistakes in injection molding design is to forgo draft or not incorporate it until late in the design process, which can negatively affect the final design.
Rules to follow:
- For every inch of cavity depth, draft angle will increase by 1 degree
- 0.5 degrees on vertical
- 3 degrees above shut
Also remember that draft angle is related to the parting line: the parting line must be positioned to split, thereby minimizing draft angle.
5.Undercuts
An undercut is a raised, recessed area, or other feature that prevents a part from ejecting from a simple two-part mold. Examples of undercuts include connecting clips on plastic containers and threads on fasteners. Injection molded parts are easier (and cheaper) to manufacture if they are not in the design, so every effort should be made to eliminate them from the design. If the feature is critical to the part, there are workarounds, including side action, stamping, and telescoping shutoffs, but these methods increase cost and lead time. Changing the parting line may alleviate undercut issues.
Undercuts can also be problematic in CNC machining, where the end mill cannot reach a feature due to its location. Some prototypes with difficult undercuts may be suitable for 3D printing with support structures.
1 Comment
What’s up to every body, it’s my first pay a quick visit of this webpage; this weblog consists of remarkable and genuinely excellent
information in favor of visitors.