The Basics of Anodized Aluminum and Its Advantages
When you need a metal prototype or part with excellent mechanical properties and professional aesthetics, anodized aluminum is an excellent choice. The anodizing process forms an oxide layer on the metal part that effectively improves corrosion resistance while enhancing visual quality and protecting the surface from scratches.
Anodized aluminum is an extremely durable post-treatment method. Not only does it enhance the performance and appearance of the part, it also improves the adhesion of paint primers and glues. The technology uses the anodic film to provide unique aesthetic effects, such as a clear coating that reflects light or a thick coating that absorbs the mold.
Although anodized aluminum affects the mechanical properties of the metal part, it does not destroy the natural appearance of the material. Although the anodizing process can also be applied to other metals such as titanium, zinc and magnesium, aluminum is by far the most widely used metal.
As part of Xavier’s high-quality surface treatment services, you can enhance the function and appearance of your metal parts and prototypes with our anodized aluminum services. To help you make the right post-treatment decision, here is everything you need to know about anodizing aluminum.
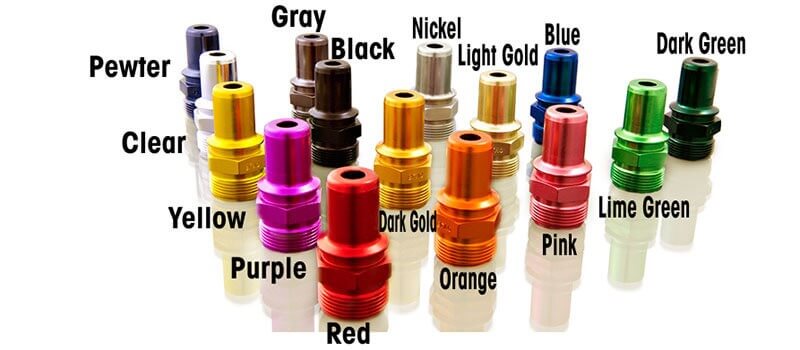
1.How the Anodized Aluminum Process Works
In order to properly anodize an aluminum part, the surface must first be cleaned and rinsed, then placed in an electrolyte, which is primarily sulfuric acid or chromic acid. This creates a conductive coating that contains a large number of positive and negative ions.
So how exactly does the process work? Once the anodizing process begins, a positive charge is passed through the aluminum, while a negative charge is applied to the plates in the electrolyte. Basically, the current forces the positive ions to be attracted to the negatively charged plates, while the negative ions are attracted to the aluminum part, the positive anode. From here, the electrochemical reaction forces the pores on the aluminum surface to open so that the positive ions can escape. These pores extend deep into the component’s substrate in a uniform geometric pattern. The combination of the aluminum surface and the negatively charged ions creates a barrier, which in the anodizing aluminum process is called a surface layer, which makes the part resistant to corrosion.
Currently, the aluminum anodizing process is available in four different forms, each with its own unique advantages:
①Anodizing Type I
This is the most basic type, using chromic acid to produce a thin, ductile anodized layer on the aluminum part.
②Anodizing Type II
Instead of using chromic acid, Type II utilizes sulfuric acid to produce a thicker anodized layer on the part, making it more suitable for coloring.
③Anodizing Type III
Similar to Type II, this method also uses sulfuric acid, but produces a thicker anodized layer that is also suitable for coloring. It is also commonly referred to as “hard anodizing.”
④Chemical Film/Anodic
This method requires the part to be coated with anodized to produce an effect comparable to anodizing.
While chromic acid was widely used by manufacturers when the anodizing process was developed in the early 20th century, most parts are now anodized with sulfuric acid (Type II and Type III).
Anodized aluminum parts also offer a variety of options when it comes to adding color. The coloring process works by injecting pigment into the empty pores of the part. Once the colored pigment reaches the surface, it is sealed to retain the selected color. This creates a visual effect that will not fade and cannot be scratched off, keeping the part’s appearance at its best.
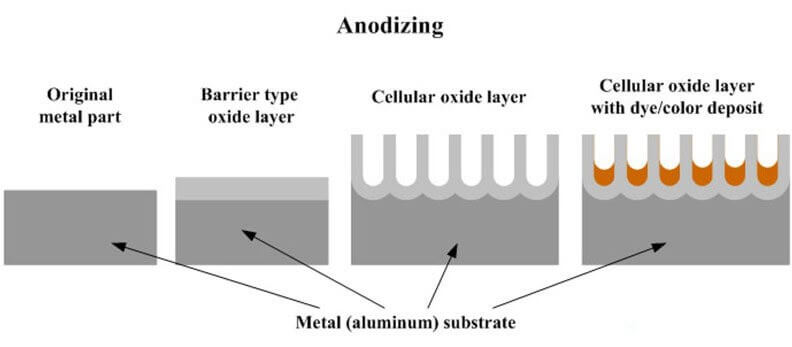
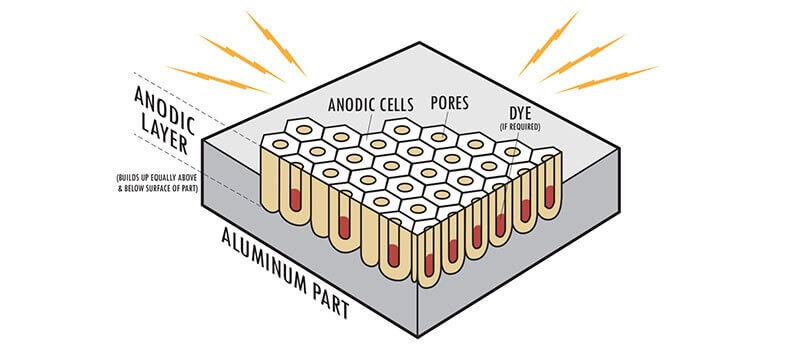
2.Benefits of Anodized Aluminum Parts
You may not realize it, but you probably come into contact with anodized products and parts every day. The anodizing process is commonly used in a variety of applications to produce common parts such as aircraft, consumer products, sports equipment, and electronics.
There are many benefits to anodizing aluminum parts, both cosmetically and mechanically. First, anodized aluminum parts are extremely durable and hard. It offers increased wear and corrosion resistance, making it ideal for parts placed in harsh environments. It also provides excellent thermal insulation for metal parts. The anodizing process can make metal parts last longer than the original. The coating is much thinner than paint and powder, while still providing a harder surface.
Another benefit of anodizing aluminum parts is that it provides an environmentally friendly finish, making them easy to recycle. Perhaps most importantly, this post-processing technique is affordable compared to painting and powder coating.
3.Should You Anodize Your Aluminum Parts?
Now that you know more about anodizing aluminum, you can decide if this process is right for your parts. If you need functional aluminum parts that face corrosion or wear, such as aircraft parts or consumer products, this post-processing technique will meet your needs. Anodizing aluminum is also visually appealing, especially since you can add color to the part while maintaining the metallic shine.