The Basics of Lightweight Metals and Their Applications
Steel is the most widely used metal in the world today, offering a balance of material properties and low cost. However, when steel, with a density of 7.8g/cm³, is too heavy for an application, product designers must turn to one of the lighter materials available. While there are many plastics that can reduce the load, lightweight metals are a popular and sturdy choice.
The most popular lightweight metals and alloy alternatives to steel are aluminum, titanium, and magnesium. To help designers evaluate these lightweight metals, we have created a short guide comparing the pros and cons of each metal as well as some common applications.
1.Titanium Metal – 42% Lighter Than Steel
Titanium alloy is by far the strongest metal on this list. Titanium also has excellent corrosion resistance, performs well at high temperatures, and is well suited for implants due to its high biocompatibility. But it also has some disadvantages.
Titanium is the heaviest of the three lightweight metals we listed, weighing 4.51g/cm³. Titanium is also the most expensive and difficult metal to process. Therefore, titanium is often used in more demanding applications that require a stronger material.
Common applications for titanium include:
- Chemical processing equipment that requires high chemical resistance.
- Long-lasting medical implants, devices and prostheses.
- Strong yet lightweight aerospace components.
- Corrosion-resistant ships.
2.Aluminum – 65% lighter than steel
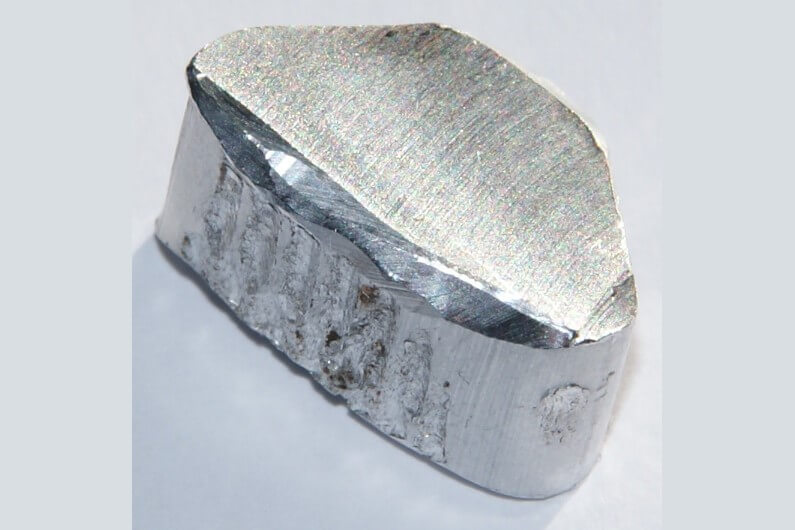
Almost one-third the weight of steel (2.70g/cm³), aluminum is the world’s most widely used nonferrous metal. Aluminum is highly resistant to corrosion, and some alloys can approach the strength of carbon steel. Although more expensive than steel, aluminum is cheaper than both magnesium and titanium.
Aluminum has extremely high formability and machinability, good weldability, and high ductility. It has high thermal and electrical conductivity. Despite this, it is susceptible to wear, has a lower strength-to-weight ratio than titanium, and does not perform well at high temperatures. Aluminum and magnesium have similar melting points, 660°C (1220°F) and 650°C (1202°F), respectively.
Due to its wide range of uses, aluminum has a wide range of applications, including:
- Electronic components and wires.
- Radiators for efficient heating and cooling.
- Aircraft fuselages and many other aerospace components.
- Durable, affordable consumer goods such as furniture and cookware.
- Architectural elements such as railings and siding.
- Cast and extruded aluminum automotive parts.
3.Magnesium – 77% Lighter Than Steel
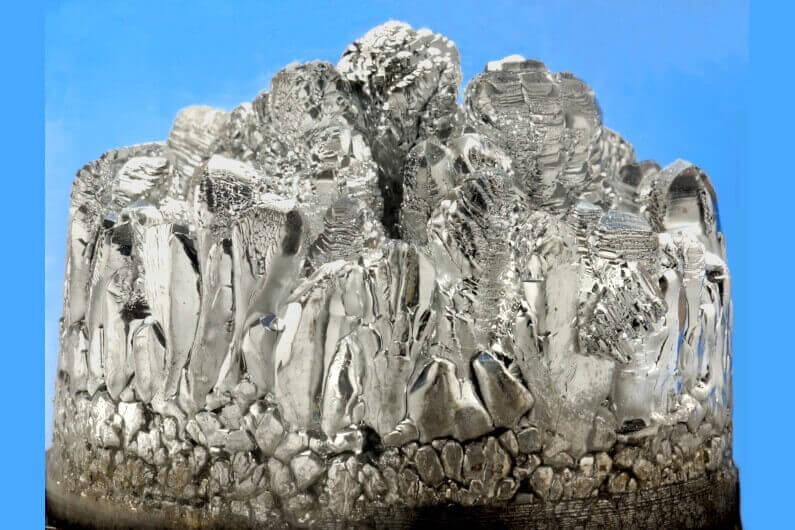
More expensive than aluminum but cheaper than titanium alloys, magnesium is the basis for the lightest structural alloys currently available. Magnesium itself is susceptible to corrosion and chemical degradation, and is also weaker than the other metals in this article. However, modern magnesium alloy and coating technologies are helping to improve the strength and durability of magnesium products.
Magnesium is highly machinable, but is usually only accessible to specialized shops willing to accept the dangers of highly flammable magnesium powder. It also has unique damping capabilities and can be used to reduce vibrations on sensitive equipment.
Most magnesium applications are designed to take advantage of its extremely light weight (1.74g/cm³), including:
- Components of consumer goods such as luggage, ladders, and cameras.
- High-performance sports and recreational equipment, such as bicycle frames.
- Weight-reducing components in gears and equipment.
- High-performance automotive parts, such as magnesium alloy wheels and transmissions.
4.Choosing the Best Lightweight Metals
All three of the metals discussed in this article are great ways to reduce the weight of your product. You might consider using them if you want to make a product that is easier for consumers to hold and use, or if you want to improve performance and reduce friction by reducing the overall assembly weight. The choice of which one to use ultimately depends on factors such as cost, strength, and durability requirements.
- Titanium offers excellent durability, but is expensive and difficult to process.
- Magnesium is extremely lightweight and can be alloyed with other elements to form a stronger metal while also improving performance.
- Aluminum is the most cost-effective and commonly used nonferrous alloy, offering very good durability in a wide range of applications.