Basics of rapid prototyping parts
If you’ve recently come up with a product design, then you’ve probably answered some of the common questions that manufacturers might ask you. For example, what is your chosen material, what are the dimensions, strength, and tolerance requirements, and how many units do you expect to produce?
However, even if you answer all of these questions, you can’t rule out the possibility of failure when you start mass-producing your final product. One of the ways top product designers mitigate these risks is through rapid prototyping. This article introduces rapid prototyping and provides helpful tips to help you choose the ideal method for rapid prototyping parts.
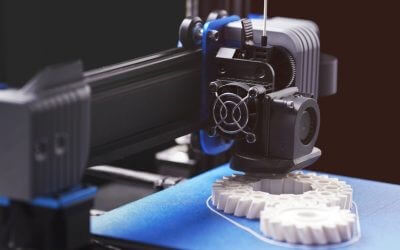
1.What is rapid prototyping parts technology?
Rapid prototyping involves manufacturing sample parts of a product to test the fit, function, manufacturability, appearance, and strength of the components. It allows you to identify design flaws early in the product development process so that steps can be taken to correct them. However, with several rapid prototyping technologies currently available, you may be confused about choosing the ideal rapid prototyping technology and method for your project.
2.Choosing the Ideal Rapid Prototyping Method
Three common methods of rapid prototyping include:
- 3D Printing
- Injection Molding
- CNC Machining
1) 3D Printing
3D printing is an additive manufacturing process – meaning it involves adding material layer by layer to form the desired prototype. It is the most common method for rapid prototyping due to its high precision, material compatibility, and low cost (especially for small batches of parts). However, there are many types of 3D printing technology, each with its own features and suitable for different prototyping needs. For example, three commonly used 3D printing technologies include:

- Fused Deposition Modeling (FDM)
- Stereolithography
- Selective Laser Sintering (SLS)
① Fused Deposition Modeling
Fused Deposition Modeling (FDM) is the most popular 3D printing method for rapid prototyping. FDM 3D printers extrude thermoplastic filaments (such as PLA and ABS) layer by layer through a heated nozzle. Its maximum build size is usually 320 x 132 x 154 mm, which is suitable for creating prototypes that need to be tested for form fit. However, the size of the extrusion nozzle determines the resolution of FDM printed parts. Therefore, FDM may not be an ideal method for creating prototype parts that require intricate details.
② Stereolithography (SLA)
Stereolithography 3D printers use high-precision lasers to make prototypes. This laser solidifies the liquid resin, eliminating the low-resolution challenges common in FDM 3D printing. As a result, SLA 3D printers can achieve higher precision and finer details than FDM 3D printers. If you want to create detailed visual prototypes that require tight tolerances, extreme precision, accuracy, and a smooth surface finish, you should choose SLA 3D printing. But keep in mind that the maximum build size for SLA 3D printing is typically 145 x 145 x 175 mm.
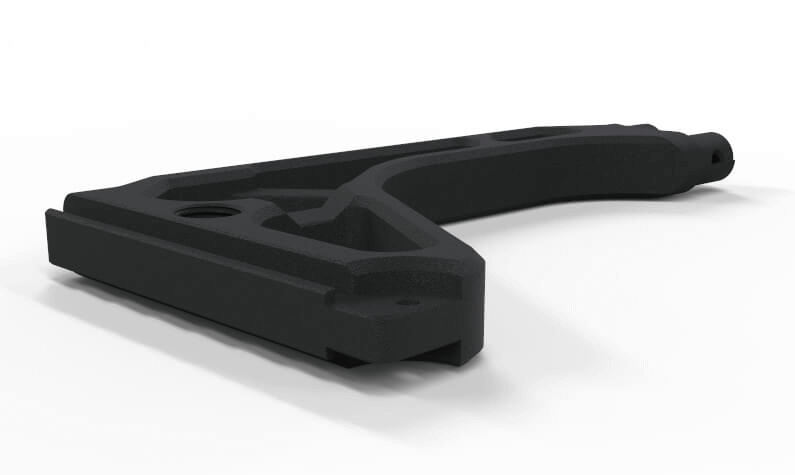
③Selective Laser Sintering (SLS)
In Selective Laser Sintering (SLS), a laser is used to sinter powdered materials (usually polyamide or nylon) in layers to create the desired prototype. SLS 3D printing is ideal for creating fully functional prototypes that require good mechanical properties. It offers a larger build size (300 x 300 x 300 mm) than SLA 3D printing, but produces parts with a rougher surface finish.
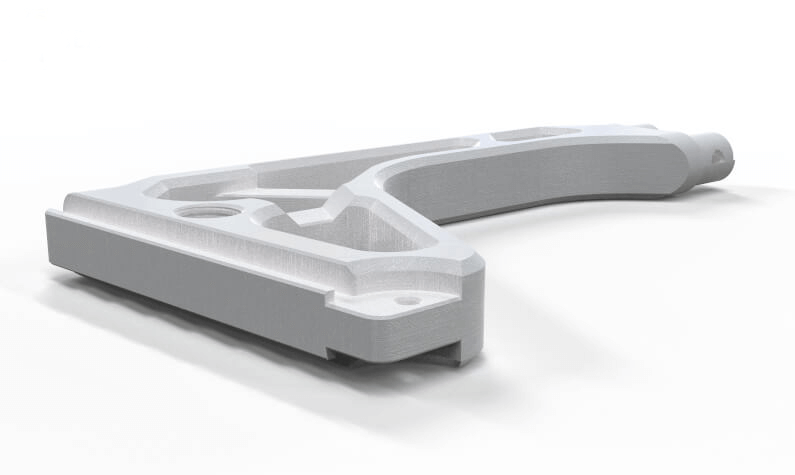
2) Injection Molding
Injection molding is a manufacturing method that uses a mold to create a prototype. To create a prototype using an injection molding machine, the manufacturer first creates a mold based on the shape of your desired product. Next, the manufacturer heats the thermoplastic polymer to turn it into a molten fluid. This fluid is then injected into the mold cavity through a runner system to form the desired shape.
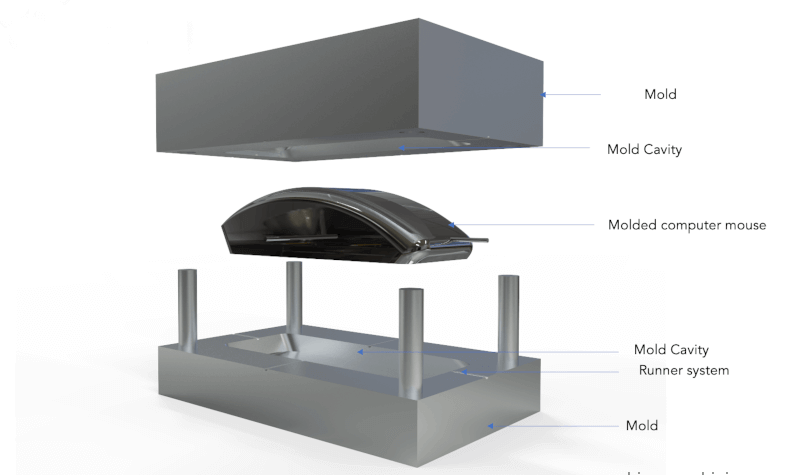
Injection molding is compatible with a wide range of materials (thermoplastics, metals, and liquid silicone rubber) and can create complex product designs. However, it is often ideal for producing multiple copies of a prototype, especially when you need to run a series of tests on those prototypes. As shown in the figure, a computer mouse prototype (made of silicone rubber) without any electrical system is shown.
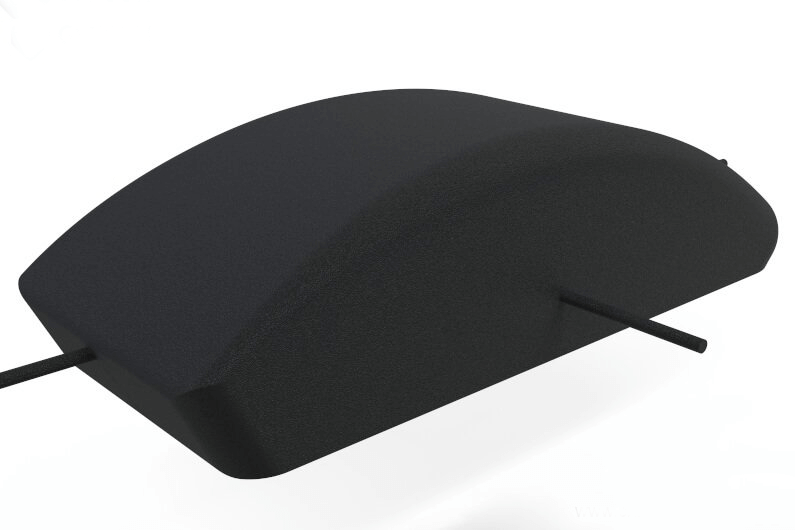
In this case, you can create multiple prototype units to test ergonomics – meaning you want to test how this computer mouse affects the user’s ability to work comfortably and efficiently. For example, you can determine whether the design of this mouse fits your hand well, or how it restricts arm movement or blood circulation. The results of this test can help you take product design measures to reduce the risk of rat arm syndrome and carpal tunnel syndrome.
3) CNC machining
CNC machining is a subtractive manufacturing method, which means it creates the desired prototype by removing part of the material from the workpiece using cutting tools. Computer numerical control (CNC) technology automates the sequence of movements of the cutting tool and workpiece to create your prototype.
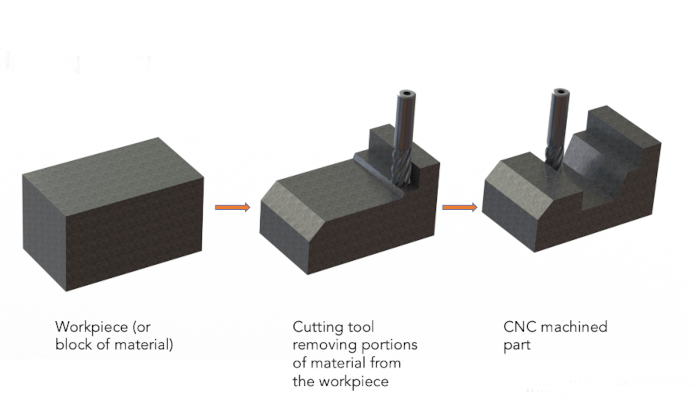
CNC machining is often the best rapid prototyping method for metal parts, especially when you need to make high-precision functional prototypes such as jigs and fixtures and components for end-use applications. For example, CNC machines can achieve tolerances as small as 0.004 mm and mechanical strengths as high as 136 MPa. However, the subtractive nature of CNC machining means that some features can be difficult to manufacture (such as undercuts).
3.Rapid Prototyping Services: Xavier Can Help
3D printing, injection molding, and CNC machining enable rapid prototyping of parts for a wide variety of product designs. However, the success of your rapid prototyping parts project depends greatly on the machine shop you work with. Not only do we have 3D printing, injection molding, and CNC machining capabilities, we also have highly trained engineers and quality control experts who work together to ensure your product is perfect. Learn more about our rapid prototyping parts services.