Types of 3D Printing Materials in the Medical Industry
This article provides an overview of the medical-grade 3D printing materials available in the market and how their use has led to tremendous innovation. The use of 3D printing in the medical industry has led to tremendous innovation, discovery, and industry growth. This manufacturing process was once considered novel, but is now an indispensable and widely used technology in the medical industry. 3D printing has many characteristics that are critical and beneficial to the medical industry. These include speed, versatility, the ability to use a variety of materials, customization, repeatability, and the ability to manufacture highly complex parts.
Applications of 3D printing in the medical industry include the manufacture of custom prosthetic and orthodontic devices, implants, custom anatomical models for surgical preparation, anatomical research models, medical aids, prototypes, medical tools, and general medical devices.
1.Requirements for Materials Used in the Medical Industry
3D printing is a widely used manufacturing technology that is compatible with a wide range of plastics, elastomers, and metals. However, not all 3D printing materials are suitable for the production of medical products. Materials must possess certain properties to be ideal for the medical industry. Some of the required properties of medical 3D printing materials are as follows:
1) Biocompatibility
Materials used to manufacture products such as implants and internal medical devices must be biocompatible. This means that they must be completely unreactive when in contact with biological systems. Biocompatibility is essential for implants, dentures, organ/bone replacements, pacemakers, and other medical products that come into contact with human tissue.
2) Sterilizability
The medical industry has extremely high requirements for hygiene, so sterilization is essential in most cases. This makes sterilizability an important property of medical 3D printing materials.
3) Bioavailability
For replacement body parts such as prostheses, dentures, implants, and artificial organs, it is not enough for the materials to be biocompatible. They also need to have similar physical properties to the original body part. For example, bone replacement materials must be hard, strong, and have high compressive strength. Similarly, materials used to print human ears must be relatively soft.
Note that the desired properties may vary depending on the application of the product to be manufactured.
2.Plastics suitable for the medical industry
1) PA 12 (Nylon)
This is a lightweight, corrosion- and chemical-resistant material with a wide range of uses. It is also tough and flexible, with high tensile and impact strength. Nylon PA12 can be sterilized using ethylene oxide, chemicals, gamma rays, gas plasma, and steam autoclaves. It is printed using MJF or SLS 3D printing. As a medical-grade material, Nylon PA12 is ISO certified and USP Class I-IV certified and is often used in prosthetics.
2) ABS M30i
ABS M30i is another widely used thermoplastic in the medical industry. In addition to being biocompatible, it can be sterilized using gamma rays, ethylene oxide, and gas plasma. This material is ISO certified and USP Class I-IV certified and is often used to produce medical devices and detailed anatomical models. It can also be used in prosthetics. ABS M30i is tough and has high tensile and impact strength. It is printed using FDM.
3) PC ISO
This material is often used to make molds, prototypes, and custom surgical guides. Although PC ISO’s surface quality is not as good as Nylon PA12, it is strong, heat-resistant, and has high tensile strength. PC ISO is also biocompatible (albeit short-term) and can be sterilized by gamma radiation and ethylene oxide. PC ISO is printed by FDM.
4) ULTEM 1010
Compared to other FDM thermoplastics, ULTEM 1010 is one of the strongest, most heat-resistant and chemically-resistant materials. It is also highly biocompatible and can be sterilized using gamma radiation, ethylene oxide, gas plasma and steam autoclaves. ULTEM 1010 is used to print surgical guides, prototypes and prosthetics.
5) SIL 30
Silicone is a heat-resistant, tear-resistant and highly flexible biocompatible elastomer. It is often used to make wearable devices that come into contact with the skin, such as respiratory masks. It can also be used to print implants. Silicone can be printed using Carbon DLS 3D printing.
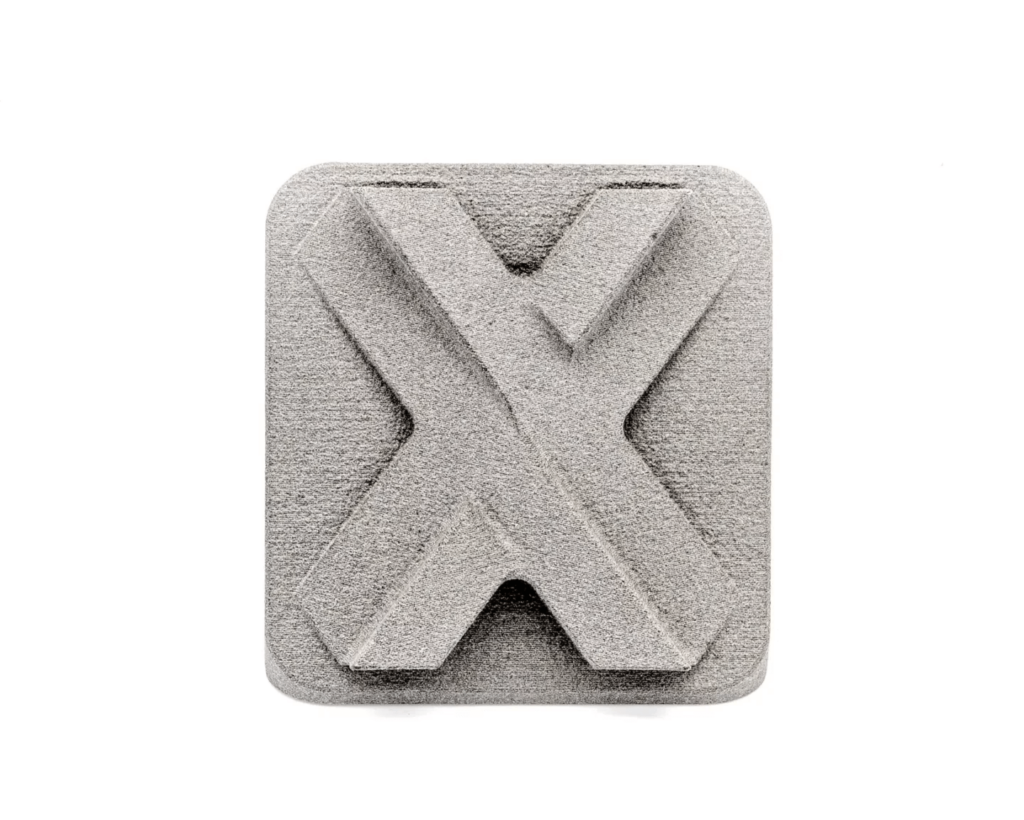
3.Metals for the Medical Industry
1) Grade 5 Titanium Alloy (Ti6Al4V)
Titanium is one of the most common metals used in the medical industry. This material is favored because of its numerous beneficial properties and similarity to human bone. Titanium is very strong, heat-resistant, hard, corrosion-resistant, non-reactive, sterilizable by various methods, and highly biocompatible.
This material is widely used in the medical industry to make custom orthopedic implants such as bone and joint replacements, dental implants, and skull plates. It is also used to make medical tools. Titanium is printed using DMLS.
2) Cobalt-Chromium (CoCr28Mo6)
Like titanium, cobalt-chromium alloys are widely used in the medical industry to make orthopedic implants such as replacement teeth, bones, and heavily used joints such as hips, shoulders, and knees. Cobalt-chromium alloys are biocompatible and highly resistant to heat, corrosion, wear, and chemicals. It also has high strength and hardness and is relatively lightweight. Using direct metal laser sintering technology, parts can be printed with this material.
3) Stainless Steel (17-4PH)
Stainless steel is a high-strength metal that is biocompatible and can be sterilized by various sterilization methods. However, its corrosion resistance is short-term and therefore inferior to that of titanium and cobalt-chrome, especially for implants. This material is well suited for surgical tools and temporary implants. Printing stainless steel with DMLS is also cheaper than titanium and cobalt-chrome.
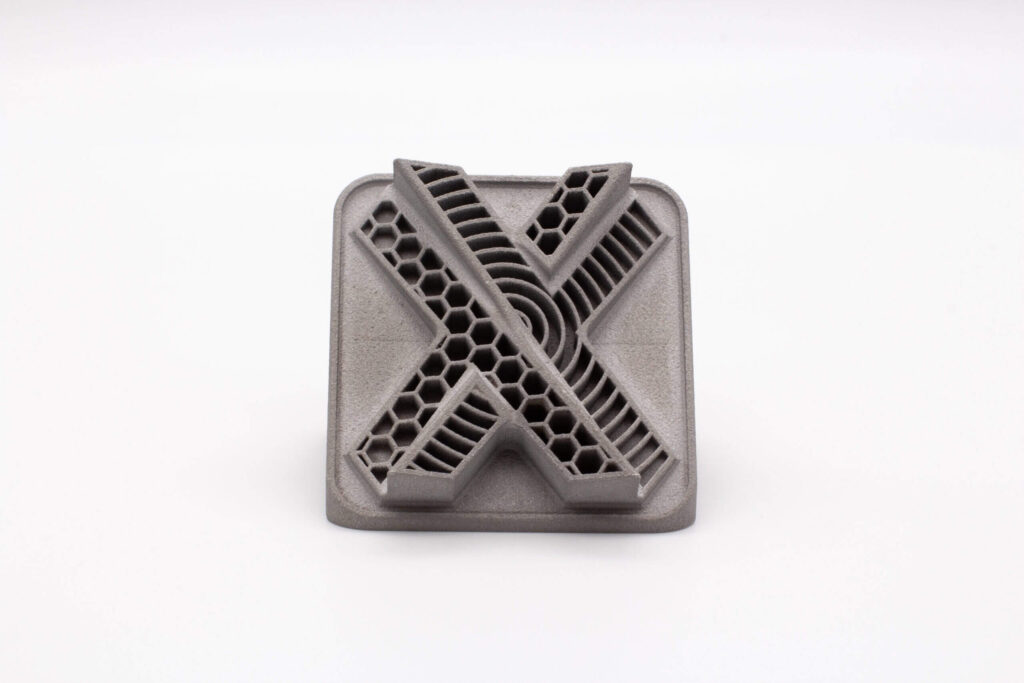
4.Conclusion
At Xavier, we offer fast, reliable and high-precision 3D printing services for thermoplastics, elastomers and metals that are of great benefit to the medical industry. We also offer a wide range of post-processing operations to ensure the highest quality. Regardless of the quantity, precision, complexity and required delivery time, we always have the manufacturing capabilities to deliver