CNC Machining: Material Selection Considerations
This article summarizes the main factors to consider when selecting the right material for your CNC machining project, from the part application to the core properties of the material itself. Considerations for precious metals such as silver machining are included.
Computer numerical control (CNC) machining is a fast, efficient, accurate, and versatile process. This manufacturing method is suitable for a wide range of hard and soft engineering materials, including metals, plastics, semiconductors, elastomers. It can be used for both prototyping and producing fully functional end-use products. The success of a CNC machining project and the functionality of the produced parts depends largely on the materials used. This is why material selection is an important step in CNC manufacturing that must be carefully conducted.
Multiple factors and requirements determine the right material for a CNC machining project. For example, do you need a material with excellent mechanical properties? On the other hand, is high production speed a priority? Typically, multiple factors are considered to determine the suitability of a material. The following factors are not exhaustive, but will provide a solid foundation when selecting CNC machining materials.
1.Material Selection Process
To successfully select the best material for CNC machining, you can follow these basic steps:
Step 1
Determine the material requirements. Consider the properties such as functionality, electrical properties, strength, and hardness that the material should possess in order to be the best candidate for your project. Also, consider the environment and exposure conditions in which the part will be used.
Step 2
Identify potential material options. Screen out all suitable materials based on your requirements, including design specifications.
Step 3
Choose the most suitable material. Choose the material that best meets your requirements. Sometimes compromises need to be made, such as choosing a material with good machinability over a lower-cost material, to ensure the quality of the part.
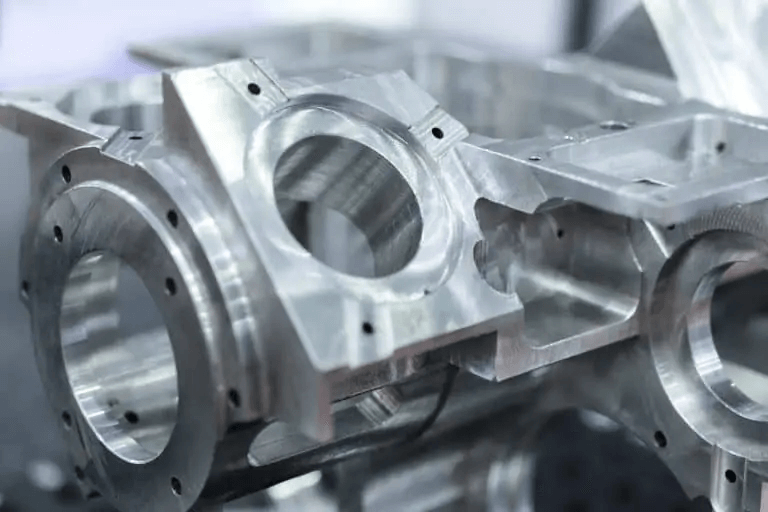
2.CNC Machining Material Selection Guide
Here are the most important factors to consider when choosing the right material for your CNC machining project.
1) Part Application
This is one of the most important considerations when choosing a material for CNC manufacturing. Different applications require different materials. Parts used in aerospace applications must be lightweight compared to parts used for building structural support. For example, aluminum 3.3211 is commonly used in the aerospace industry because of its good strength-to-weight ratio.
The application area will determine the material’s physical properties, such as tensile strength, strength-to-weight ratio, crack resistance, rigidity, or flexibility. Generally speaking, heavier materials can withstand more pressure, but in weight-sensitive applications, lighter materials with a good strength-to-weight ratio must be selected. Steels 1.0503 and 1.0038 are relatively heavy materials compared to lighter aluminum alloys such as aluminum 3.3206.
2) Operating environment
The environment in which the part will be used is a key factor in determining the material. Operating conditions include temperature, corrosive chemicals, UV exposure, constant contact with water and even flames. The melting temperature of any selected material must be safely above the operating temperature. If this is not the case, the part may undergo structural changes when exposed to high operating temperatures.
In addition, the selected component must be able to withstand the heat generated by machining. Steel 1.4404 has an extremely high heat resistance of up to 861°C. The temperature or humidity conditions to which the material will be exposed when used indoors can be easily predicted with a high degree of accuracy. This makes the selection of materials much easier.
However, in outdoor applications, it is better to choose a material such as stainless steel that can withstand high humidity and rust while maintaining its appearance and structure. In addition, extreme weather changes are more likely to occur outdoors; this can cause structural distortions in some materials.
3) Dimensional stability and tolerances
Industries such as aerospace require components with extremely precise dimensions and excellent stability. Such conditions require materials with good dimensional stability, i.e., low deformation coefficients. Different materials react differently to the forces generated by the cutting tool. Therefore, the selected component must be able to achieve the tight tolerances required. The higher the machinability of the material, the easier it is to achieve tighter tolerances.
For example, the high machinability of aluminum allows the production of parts with very high tolerances using this material. Note that the tighter the tolerance, the higher the production cost. Therefore, when dimensional tolerances are not a critical requirement, it is recommended to use less stringent tolerances to reduce the time and expense required to machine the part.
4) Electrical conductivity
Some materials, such as copper and silver, are excellent conductors. On the other hand, PTFE is a good insulator. For components for electrical applications, the choice of material will depend on the electrical properties required of the component. Therefore, it is crucial to consider the conductivity of the selected material. Metals are generally good electrical conductors, while plastics are generally good insulators.
5) Machinability
If the part needs to be produced in large quantities, it is more appropriate to choose a material that is easy to machine to reduce time and expense. Materials such as aluminum and brass are easier to machine than tool steel, even though the latter is stronger. Only when production quantities are low and product turnaround time is flexible enough should materials with lower machinability be selected. Machining such materials requires more resources, time and effort.
Note that machinability is a secondary consideration in material selection and should not be at the expense of other core considerations such as part application.
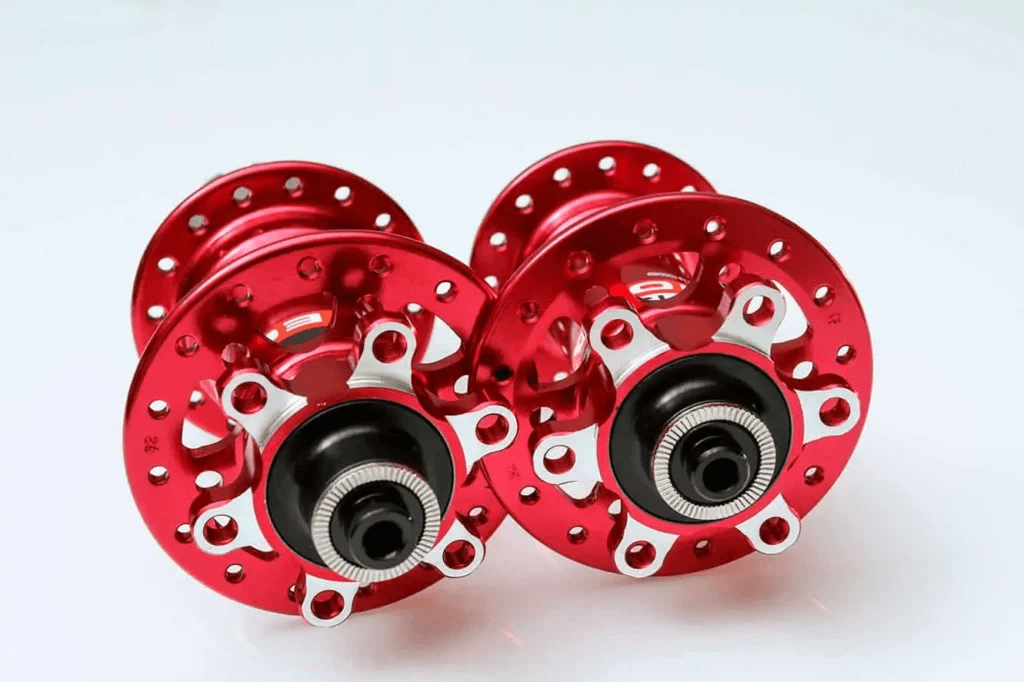
6) Appearance
Aesthetics is usually not a primary consideration in material selection. However, in some cases, it is very important. For some products, appearance will determine the general acceptance of such products by consumers. Consumer products may require specific physical characteristics such as color or smooth surface finish. Metals usually have a good surface finish after machining, so less work is required when polishing. Plastics usually come in different colors, while metals require post-processing for coloring.
7) Material Cost
Sometimes, the best material for a part is expensive. The price of purchasing such a material far exceeds the production budget. Therefore, it is necessary to look for other low-cost materials. However, functionality, strength, hardness, chemical resistance, electrical properties and other properties must be carefully considered to determine whether such a material is a viable low-cost alternative to the best suitable material. For example, steel 1.4571 has excellent wear and corrosion resistance, as well as good machinability.
However, it is twice as expensive as 1.7131 steel, which also has excellent wear resistance. For uses where wear resistance is the primary consideration, 1.7131 steel is an excellent alternative to 1.4571 steel.
8) Availability
When choosing a material for CNC machining, availability is an important consideration. Sometimes, the most suitable material may not be available in sufficient quantities to sustain production. On the other hand, sourcing such a material may be difficult. It is wise to choose a material that meets the functional requirements and is readily available, especially if the part will be produced in large quantities. Easily accessible materials ensure that CNC machining is completed efficiently in the shortest possible time.
3.Conclusion
The choice of material affects nearly every stage of the product life cycle, from prototyping to full production to the performance of the part in the final application. The key to obtaining a fully optimized finished part lies in choosing the right material. Therefore, material selection is an important part that needs to be carefully considered before starting a CNC machining operation. With the above considerations, it is easy to narrow down the list of materials that are most suitable for the part and make an informed material choice.