Vacuum casting: Discover its flexibility and economy in production
Vacuum casting is a versatile and cost-effective manufacturing process that is widely used in a wide range of industries, including automotive, aerospace, and medical device manufacturing. This article delves into the intricacies of vacuum casting, shedding light on its benefits and its multiple applications across various industries. Let’s explore and uncover why manufacturers around the world prefer it.
1.Basic Introduction
Vacuum casting technology goes beyond traditional manufacturing techniques, enabling the manufacture of complex parts with amazing precision and accuracy. It is particularly suitable for small batch production, providing a more economical alternative to injection molding while meeting the needs of companies that need to produce output quickly. These characteristics make it ideal for experiments and small-scale manufacturing work in different industries
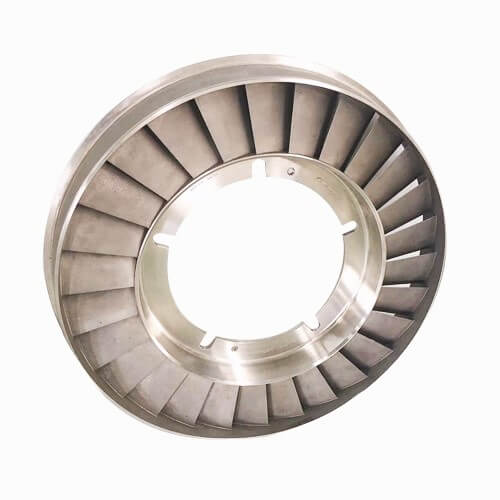
2.Vacuum Casting Process
The origins of vacuum casting involve making a mold based on a master pattern, which is usually made of plastic, metal, or wax. A silicone rubber mold is then carefully crafted around the master pattern in a casting chamber, where air bubbles are expelled through a vacuum chamber. Subsequently, the casting material (composed of silicone, epoxy, or other suitable material) is introduced into the mold without leaving any air gaps in between. After casting, the material is cured for a certain period of time depending on its composition. After curing, the mold and final part are removed from the vacuum chamber for cleaning, finishing and inspection to ensure that they meet strict standards.
3.Vacuum Casting Benefits
Known for its advantages over traditional production methods. It has many advantages, including:
- High precision
- High-quality parts
- Time and cost savings
Due to its excellent accuracy and precision, it is well suited to areas where complex geometries are required.
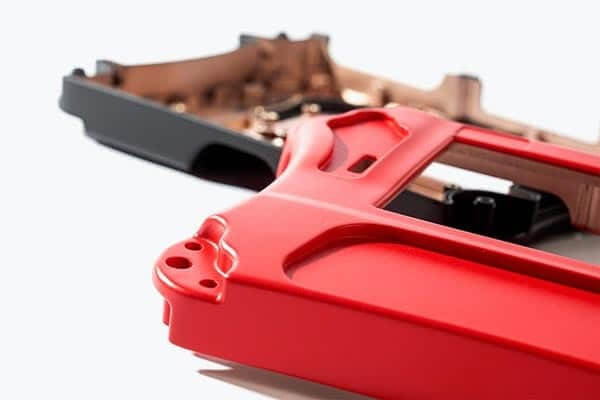
4.Applications of Vacuum Casting
It is favored by many industries and has a wide range of uses in the process field:
- Automotive: small to medium-sized engine hoods, dashboard components and interior parts.
- Aerospace industry: manufacturing pipes, brackets and housings.
- Medical device sector: manufacturing prosthetics, orthotics and surgical instruments.
- Consumer goods sector: production of toys, electronics and household appliances.
5.Conclusion
In essence, vacuum casting has revolutionized the manufacture of complex geometries, providing a cost-effective and precise solution for a variety of industries such as automotive, aerospace, medical and consumer goods. As the number of industries with requirements for complex geometries continues to increase, vacuum casting tables will play an increasingly important role. Its manifold benefits and countless applications ensure its enduring relevance in the manufacturing sector for many years to come. Indeed, vacuum casting represents a cost-effective, adaptable and efficient method of producing complex geometries, ushering in a new era of excellence in manufacturing.