Advantages and production process of vacuum casting
Consider using vacuum casting to produce fast, flexible, and cost-effective plastic parts. Vacuum casting uses a vacuum chamber to create parts from silicone molds. It has advantages over injection molding, 3D printing, and CNC machining.
1.Vacuum casting saves product development time
1) Reduces preparation time for prototyping and testing
It is faster than other methods, taking only hours or days instead of weeks or months. It can produce multiple copies of a part from a single mold, which speeds up testing and validation.
2) It can achieve complex shapes and geometries that other methods cannot achieve
It produces fine, smooth, and precise parts without additional steps. It can produce parts with a variety of colors, textures, and finishes without painting or coating.
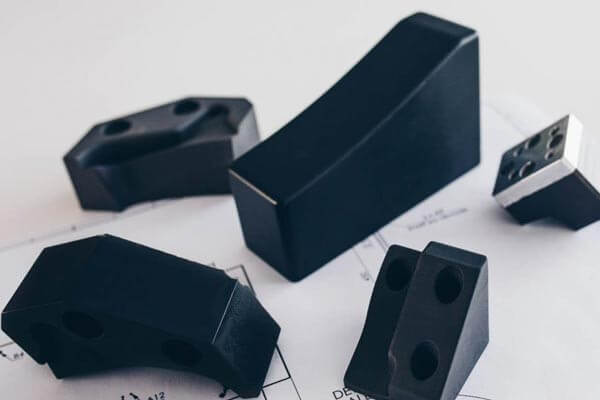
3) It allows for easy design changes
It can create flexible or rigid parts depending on the material and process parameters. Vacuum casting can create parts with a variety of electrical and thermal properties. It allows for easy design changes by changing the mold or material.
4) Improves product quality and service life
It is able to produce parts that are biocompatible, sterilizable, impact-resistant, corrosion-resistant, and UV-resistant. Vacuum casting not only produces highly functional parts, but also beautiful parts. It saves money by reducing faults, failures and recalls.
5) The final product is highly adaptable and varied
Custom parts are made according to the specific requirements of customers. It can reflect the identity and values of your brand, thereby improving your competitiveness and customer satisfaction.
2.Vacuum Casting Process
To start vacuum casting, make a master model using 3D printing or CNC machining. Make a master model for silicone molding using heat- and pressure-resistant materials.
Step 1
Pouring liquid silicone around the master model and then removing all bubbles in a vacuum chamber is the first step in making a silicone mold. Remove the silicone mold attached to the master model to make room for the casting.
Step 2
To remove bubbles from the casting material, the preparation process starts with mixing the material and then degassing it in a vacuum chamber. This ensures that the final product has a flawless surface.
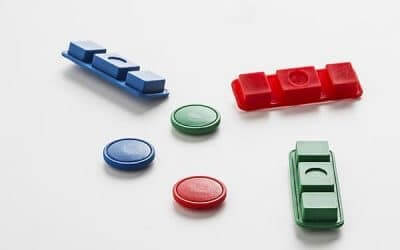
Step 3
Pouring the casting material into the vacuum silicone mold helps to remove bubbles from the material. Apply pressure to the mold to force the casting material into all features and cavities.
Step 4
Before demolding, the casting material must first cure at room temperature or in a hot oven. After the part has cured, remove excess material from the part and remove it from the silicone mold.
Step 5
Post-processing steps such as painting, polishing, or assembly may be required to achieve the desired effect and make the product usable.
Vacuum casting uses a vacuum chamber to create plastic parts from silicone molds. It saves time and money in product development by producing complex shapes, allowing design changes, reducing costs, improving quality, and providing customized services.