A Detailed Guide to CNC Machining Quality Control
Computer numerical control (CNC) machines have become standard in the machining industry. Their accuracy, speed, and ease of use make them an indispensable tool for manufacturers. However, nothing is perfect. Quality control remains an important factor in detecting and preventing defects.
Although CNC machining is much less prone to errors than traditional manual manufacturing processes, mistakes can still occur. These errors can have significant knock-on effects, including bottlenecks and material waste, and if not caught in time, can have a damaging effect on customer relationships due to poor product quality. However, these negative consequences can be mitigated by implementing an effective quality management system.
With this in mind, manufacturers can take the following steps to improve their CNC quality control:
1.Choosing the Right Type of CNC Machine
Not all CNC machines have the same capabilities, and manufacturers must keep this in mind when approaching quality control. It is critical to select the right machine for a specific task, as using the wrong machine to perform a task can lead to increased errors. Therefore, facilities need to choose carefully when assigning orders to specific machines. The complexity of the product or part is directly related to the complexity of the machine required.
Three-axis CNC machines are the most common choice for mechanical components and are more than adequate for simpler designs. When working with more complex parts or products, it’s best to use four- or five-axis machines. These additional axes increase the accuracy of the machines, allowing them to perform more complex tasks without error.
Still, a shop shouldn’t rely entirely on four- or five-axis machines. Striking a balance between different machines can help alleviate bottlenecks and keep overall operational efficiency. When shops distribute workloads, they should assign more complex designs to machines with more axes.
2.Check Raw Materials Before Machining
Unfortunately, many in the manufacturing industry tend to view quality assessment as the last stage of the production process. While final inspections are undoubtedly critical, the pursuit of quality should be conducted at a much earlier stage. Detecting errors after machining has begun can make costs unrecoverable, while early inspections can prevent waste.
One of the most critical measures to ensure quality from the outset is to check the quality of the materials. CNC machines can all but eliminate human error, but this becomes irrelevant if they use low-quality or defective materials. Even impeccably precise systems can produce substandard products when using inferior materials.
Therefore, it’s imperative that employees assess the quality of the raw materials before they begin work. Sourcing materials from reputable suppliers can alleviate many material-related issues, but machinists cannot take any chances in this regard. By diligently inspecting materials for cracks, holes, or other defects, workers can ensure that they are using their CNC machines to their full potential.
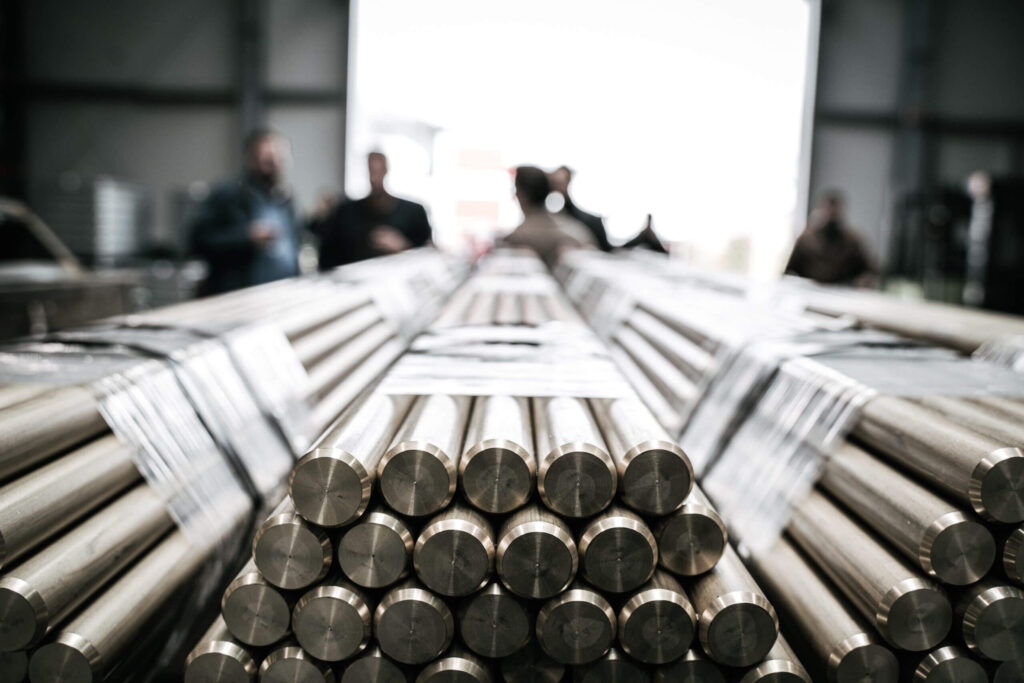
3.Implementing On-Machine Inspection
Quality control can also be integrated into the CNC machining process itself. Devices called machine tool probing systems can be attached to CNC machines to check quality in real time while the machine is running. This on-machine inspection allows facilities to detect and resolve issues as they arise, thus preventing errors in the final product.
Probing procedures do not interrupt or interfere with the machining process, so they do not affect efficiency. Instead, they automatically redirect the machine to correct any problems detected in real time. By identifying and resolving errors at an early stage, costly mistakes can be avoided, reducing the number of defects or rejected parts in subsequent production stages.
In addition to reducing scrap, on-machine inspection reduces the likelihood of quality control bottlenecks. Given that machining time is a major cost driver in this field, optimizing the efficiency of these operations is imperative. Tool probing systems reduce the need for rework, shorten overall machining time, and improve quality consistency by minimizing disruptions caused by end-of-line quality checks.
4.Employ Multiple Quality Control Methods
Just as CNC machining itself is not foolproof, neither are individual quality inspection methods. Each method has its own unique strengths and weaknesses, and no single process can catch every possible error. To combat this, shops should employ a variety of quality control methods to ensure that errors overlooked by one process do not propagate further down the line.
The order in which quality control methods are applied is equally important. Manual inspection should always be the last checkpoint, and this principle should apply to all processes that rely on automation. Automated inspections are highly effective, but technical glitches can affect their accuracy. Positioning manual inspections at the end of the production process can uncover potential errors that might otherwise be overlooked.
It’s critical to maintain a balance, as too many different methods can create bottlenecks. After all, there can be too much of a good thing. Shops don’t need to implement every conceivable quality control method, but they should at least use a variety of methods. As a general guideline, one material inspection before machining, one on-machine inspection procedure, and one manually driven post-machining inspection are sufficient.
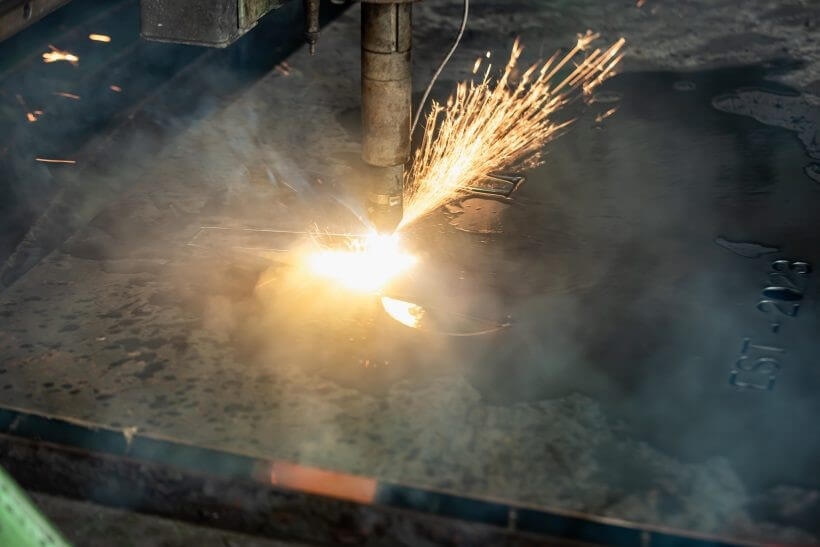
5.When outsourcing, look for certified suppliers
Not all shops perform CNC machining in-house, but CNC quality control is still critical. To guarantee high-quality outsourced CNC operations, companies should look for suppliers that hold the necessary certifications. While specific certifications may vary by industry, all suppliers should at least adhere to ISO 9001, a comprehensive quality management certification.
For certain industries, manufacturers should also seek additional certifications. For example, ISO 13485 indicates compliance with medical-grade product standards, which is essential for the healthcare industry. Similarly, ISO 16949 applies to automotive parts, so manufacturers in the transportation industry should work with suppliers that adhere to this standard.
While these certifications do not guarantee 100% avoidance of potential errors, they can significantly reduce risk. Obtaining these certifications requires strict adherence to the standards, making them a reliable benchmark for selecting quality production partners. Therefore, any factory that outsources machining processes should be aware of the relevant quality standards.
6.Reliable Quality Control
An enhanced quality management system not only reduces waste, but also produces a better quality product. As a result, companies can save costs and improve their reputation among customers. Ignoring quality management can have the opposite effect, which highlights the importance of this aspect in any machine shop operation.
By following these steps, machining processes can ensure that their quality control is both precise and efficient. This optimization allows them to fully exploit the potential of these exceptional machines and differentiate themselves from their competitors. As long as companies using CNC machining adhere to strict quality control standards, it can prove to be a valuable resource. Achieve optimal CNC quality control by implementing these basic steps. Maximize the potential of the machining process and set your brand apart from the competition. Viewing CNC machining as a valuable resource depends on whether a company adheres to strict quality control standards.