The Importance of Precision Components
In the world of precision engineering, complexity and innovation intertwine, and the pursuit of superior precision parts drives the industry forward. B&B Machining, Inc.’s experience with a wide range of components and CNC processes allows it to serve a diverse and evolving industry.
But at Xavier, we don’t just build parts, we build reliability and precision. Prepare to dive into the world of precision parts with us and explore nuances, complexity, and the path to excellence.
1.What are precision components?
Precision components are the epitome of engineering excellence, carefully designed and manufactured to exacting standards. These components, from microscopic gears to complex medical implants, adhere to extremely tight tolerances to ensure seamless integration within complex systems. Whether it’s aerospace, automotive, medical, or electronics, precision components are the backbone that determine the functionality and reliability of the end product.
Precision engineering goes beyond mere manufacturing; it’s an art form that requires mastery of materials, cutting-edge technologies such as CNC machining, and a deep understanding of the end application. Each component embodies a harmonious union of precision, durability, and performance, engineered to operate seamlessly in critical systems where accuracy is paramount.
2.Types and Uses of Precision Components
Precision components span a wide range of categories, each targeting specific applications and industries. These categories include:
1) Mechanical Precision Components
From gears and shafts to bearings and couplings, these components power machinery, ensuring smooth operation and precise motion control.
2) Electronic Precision Components
Integrated circuits, connectors, and sensors are at the heart of modern electronics, where nanometer-level precision is non-negotiable for performance and reliability.
3) Medical Precision Components
Implants, prosthetics, and surgical instruments require uncompromising precision to ensure compatibility, functionality, and biocompatibility within the human body.
4) Automotive Precision Components
Critical components such as fuel injectors, engine components, and transmission components require precision engineering to improve fuel efficiency, performance, and safety.
Each category showcases its unique challenges, materials, and manufacturing techniques. For example, electronic precision components require nanometer-level precision, while their medical counterparts prioritize biocompatibility and durability.
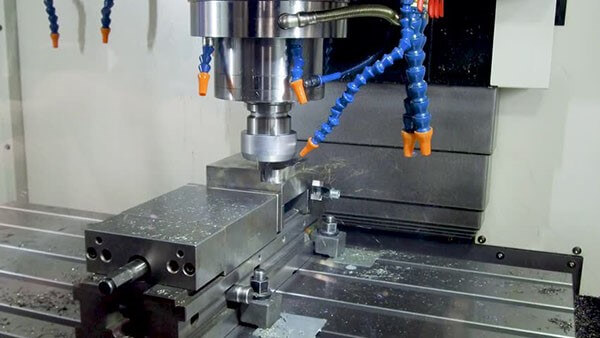
3.Making Precision Components: Art and Science
The manufacturing of precision components goes beyond traditional manufacturing processes. It is a combination of art and science, relying on advanced technology and processes to achieve perfection. Computer-aided design (CAD) plays a key role, allowing components to be accurately visualized and simulated before actual production. This minimizes errors and optimizes the functionality and manufacturability of the design.
The manufacturing process itself often involves CNC machining, a versatile technology that is highly regarded for its precision, repeatability, and ability to process a wide range of materials. Whether it is CNC milling, CNC turning, or grinding, CNC machining ensures that high-quality, complex parts are produced to precise specifications.
Achieving precision is not just about machining, either; it is a holistic approach that involves rigorous quality control measures, material selection, and a deep understanding of how each component integrates into the larger system.
4.Sourcing Precision Components
1) Finding a Reliable Supplier
In the quest for quality precision components, it is critical to find a trusted supplier. The process involves strategic steps to ensure that quality, reliability, and delivery requirements are met.
① Define requirements accurately
Outline the technical specifications, tolerances, materials, and quantity requirements. This clarity is the foundation for a successful partnership with a supplier.
② Explore various avenues to discover potential suppliers
Online catalogs, industry shows, and recommendations can be gold mines. Assess their expertise, production capabilities, and adherence to quality standards.
2) Evaluate supplier capabilities
Once potential suppliers have been identified, it is critical to evaluate their capabilities. This involves a multi-dimensional assessment:
① Quality standards
Evaluate certifications (ISO, AS9100, etc.) and quality control processes. Seek reliability and consistency in delivering high-quality components.
② Capacity and scalability
Analyze production capabilities to ensure that suppliers can meet your current and future needs. Scalability is critical for long-term partnerships.
③ Technology and innovation
Consider suppliers that use innovative and modern manufacturing technologies. Those that leverage advanced technologies such as additive manufacturing or AI-driven quality control may offer a competitive advantage.
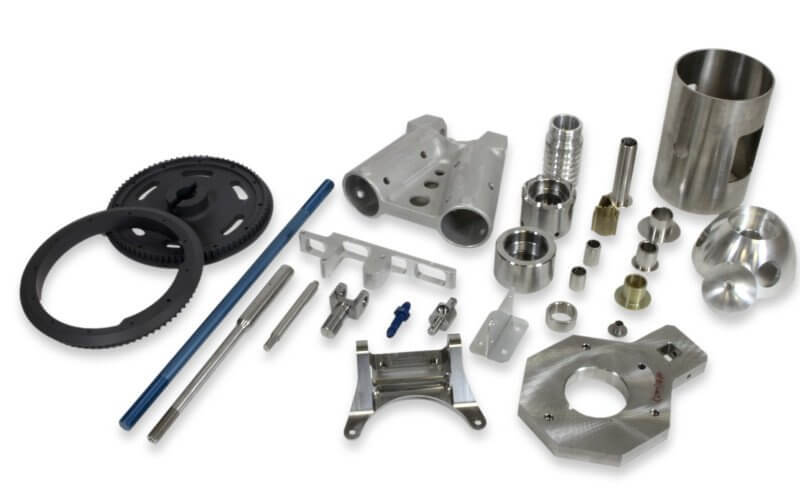
5.Key indicators for supplier selection
Building a strong supply chain depends on selecting suppliers that meet your standards. When developing a scoring matrix, consider the following key factors:
① Quality assurance
Rate suppliers based on product quality, specification compliance, and defect rate.
② Reliability and timeliness
Evaluate on-time delivery performance and their ability to consistently complete tasks on time.
③ Cost and value
Consider pricing structure while weighing additional value-added services such as post-processing, technical support, and inventory management.
By assigning weights to each metric, you can objectively compare suppliers and make informed decisions.
6.Supplier Collaboration and Communication
It is critical to establish clear communication channels and build collaborative relationships with selected suppliers. Clearly outline expectations, maintain an open dialogue, and provide constructive feedback. This facilitates smoother operations, promotes innovation, and strengthens partnerships for mutual growth.