Aerospace parts processing guide
The aerospace industry has always been one of the pinnacles of technology and engineering. It relies on precision-made aerospace parts to ensure the high reliability and safety of aerospace systems. The manufacturing of these parts involves challenges in material selection, high-precision processes, and complex engineering requirements. In this article, we will explore the knowledge of various aspects of aerospace part processing.
1.Material requirements
The manufacturing of aerospace parts begins with specific material requirements. These parts usually need to have high strength, low density, high thermal stability, and corrosion resistance to cope with extreme operating conditions. Common aerospace materials include:
1) High-strength aluminum alloys
High-strength aluminum alloys have the characteristics of light weight, corrosion resistance, and easy processing. They are ideal materials for manufacturing aircraft structural parts. For example, 7075 aluminum alloy is widely used in the manufacture of aerospace components.
2) Titanium alloys
Titanium alloys have excellent strength-to-weight ratios and are widely used in aerospace engine components, fuselage components, screws, etc.
3) High-temperature alloys
High-temperature alloys maintain strength and stability at high temperatures and are used in engine nozzles, turbine blades, and other high-temperature components.
4) Composite materials
Carbon fiber composites have excellent performance in reducing structural weight, improving strength, and reducing corrosion. They are often used to manufacture aerospace components and the outer shell of spacecraft components.
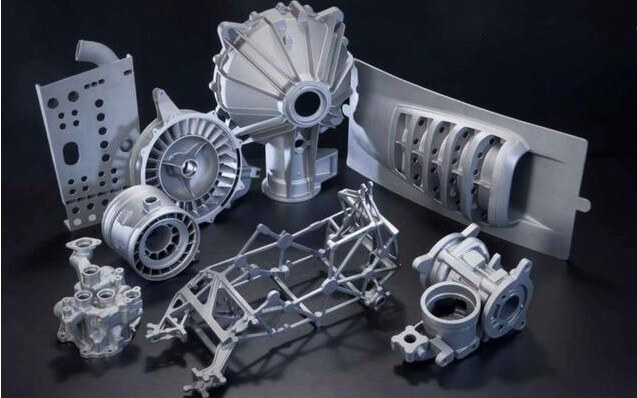
2.Process requirements
The manufacturing of aerospace parts requires very complex parts processing processes to ensure performance and reliability. For example, CNC machine tools; CNC machine tools are the core tools for processing aerospace parts. They can perform CNC milling, CNC turning, drilling and other operations with high-precision control. Secondly, there are heat treatment, welding and riveting, and surface quality, which directly affect the hardness, strength, wear resistance, high load resistance and high temperature resistance of aerospace parts. At the same time, extremely high requirements are required in terms of shaft accuracy, thermal stability, etc.
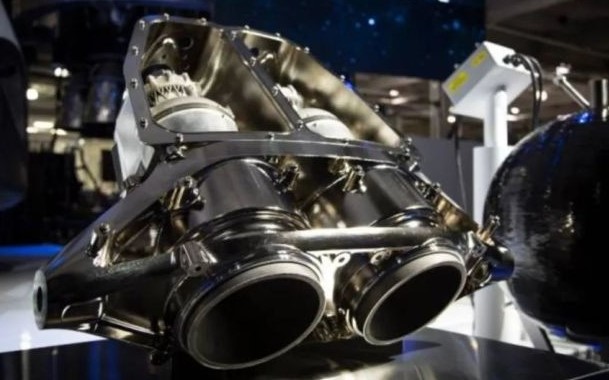
3.Difficult processing
The processing of aerospace parts is full of challenges, mainly manifested in the following aspects:
1) Complex geometry
Aerospace parts usually have complex geometries and require high-precision processing to meet design requirements.
2) High-temperature alloy processing
High-temperature alloy processing is difficult, and special tools and processes are required to handle these hard materials.
3) Large components
Spacecraft parts are usually huge in size and require large CNC machine tools and special processing equipment.
4) Quality control
The aerospace industry has extremely high requirements for part quality, and strict quality control and inspection are required to ensure that each part meets the standards. Precision and reliability are the key to aerospace parts processing. A deep understanding and fine control of materials, processes, precision and processing difficulty are the key to manufacturing high-quality aerospace parts.