Importance of CNC Machining in the Energy Industry
Before the Industrial Revolution, humans didn’t have a great need for energy. For example, we happily used the sun to heat our homes, horses for transportation, wind to travel around the world, and water power to drive simple grain grinders. 17 That all changed in the 1980s, when steam-powered power plants proliferated, and most of the components of those plants were manufactured using high-speed machine tools. Challenge Machining happens to be a full-service machine shop that serves a variety of industries, from defense and transportation to agriculture and energy.
However, since the beginning of rapid industrialization, energy systems and technologies have become increasingly complex as energy demand has continued to grow. As a result, it became increasingly difficult for manufacturers to meet the manufacturing requirements of the energy industry until the advent of CNC machining technology in 1952. In this article, we will introduce CNC machining in the energy industry. We will cover three things you must know about CNC machines and their role in today’s energy sector. Let’s get started!
1.CNC Machining Helps Manufacture Hydroelectric Turbine and Generator Components
Hydroelectric turbines and generators are huge and consist of hundreds of thousands of parts. These parts vary in design and size, with some parts smaller than an index finger and others larger than a car. Regardless of the size variations, the key requirement is that these parts must be precisely machined to ensure seamless assembly. CNC machines are one of the key machining technologies that energy industry product designers use to meet these requirements. For example, some manufacturers rely on 7-axis CNC milling machines to manufacture most of the components that make up their 36-foot-long, 25-ton hydroelectric systems.
The reason for such heavy reliance on CNC machines is understandable. First, CNC machines can machine tolerances as small as 4 μm, which is almost the tolerance limit for many hydroelectric components (such as simple shafts, impellers, and bushings). Second, multi-axis CNC machines are particularly suitable for manufacturing extremely large and complex geometries. However, the application of CNC machines is not limited to the renewable energy industry.
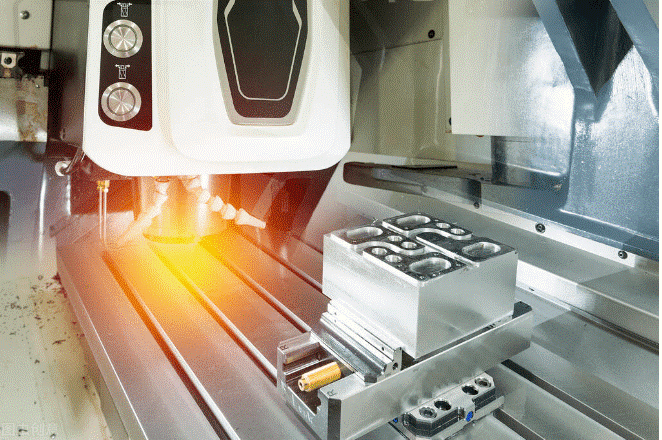
2.CNC machining helps to manufacture difficult-to-machine materials in traditional generators and turbines
Like hydroelectric systems, traditional turbines and generators (which rely on fossil fuels to generate electricity) have thousands of parts. However, unlike renewable energy systems, traditional generator components are subjected to extremely high heat conditions of up to 2,300°F, so engineers must rely on high-strength and heat-resistant materials to manufacture these parts.
For product designers, finding a material with high strength and high heat resistance is not a problem. Instead, the challenge is to find the right manufacturing methods for these metals. For example, high-strength materials such as titanium and its alloys have poor (or average) machinability and tend to chatter during metal cutting.
Since CNC machines can process a wide range of materials, machining manufacturers rely on them to create metals that are difficult to machine in traditional generators and turbines. For example, skilled machinists typically use CNC machines to machine titanium alloys at a recommended cutting speed of 59 m/min for roughing and above 180 m/min for finishing.
3.CNC machining is contributing to research on solar and wind energy systems
Solar and wind energy systems are gradually taking center stage on the global stage, replacing traditional energy systems that rely on fossil fuels and contribute to climate change. As a result, research is being conducted to improve the efficiency and performance of these systems. For example, many research scientists are studying new wind turbine blade designs and the energy efficiency and performance of solar panels.
As you might have guessed, CNC machines are one of the rapid prototyping technologies used in most of these studies for blades and solar panels. One of the main reasons for this preference is the ease of modifying designs in CNC machining.
With Xavier’s CNC machining services, you simply modify the dimensions on your 3D CAD software and our CNC machinists will quickly manufacture your new blade (or solar panel design) without any difficulty. This is not the case with traditional manufacturing methods such as injection molding, where you would have to re-make the mold from scratch.