A Comprehensive Introduction to Die Casting
Die casting is a manufacturing process where molten metal (usually a non-ferrous alloy such as aluminum or zinc) is injected into a mold or die to create precise and complex metal parts. This method is known for its ability to efficiently produce large quantities of high-precision parts. This article explains what die casting is and how it works.
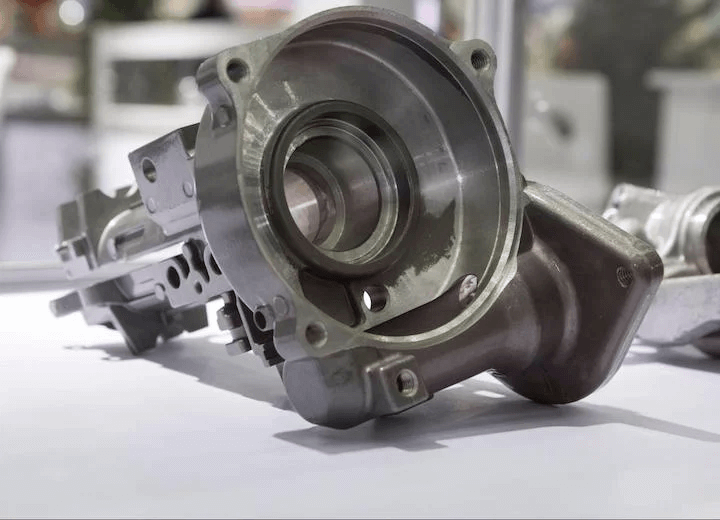
1.Overview of Die Casting Dies
Die casting works by injecting molten metal into a mold. Die design and manufacturing are key elements of the die casting process. The die cavity is made of two hardened/tempered steel or cast iron molds that are machined to the net shape of the desired part. Pressure die casting involves injecting molten metal into the die cavity at high pressure and speed, while low-pressure die casting dies and gravity die casting dies fill much more slowly.
Low-pressure die casting is generally less expensive (less tooling is required) and produces castings with less porosity. However, high-pressure die casting is suitable for thin-walled parts (less than 3 mm thick) because the high pressure is able to force the molten metal into the thin mold cavity. Once the molten metal is injected into the mold, it solidifies rapidly, producing complex and detailed parts with high dimensional accuracy.
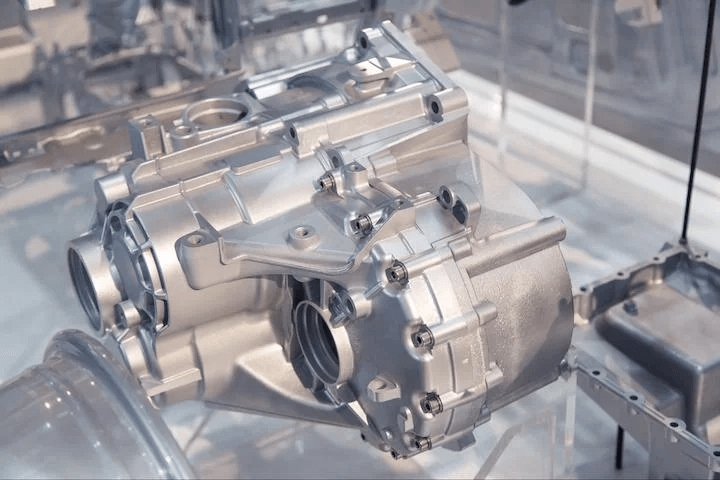
2.What are the two types of die casting?
Die casting can also be classified based on the temperature of the die or chamber. The two most common methods of metal die casting classified by temperature are cold chamber die casting and hot chamber die casting.
1) Cold Chamber Die Casting
Cold chamber die casting involves introducing molten metal at room temperature into a separate shot chamber using a ladle or pouring method. The shot chamber contains a ram that presses the molten metal vertically into a steel die (mold) with movable and fixed parts. The ram applies a pressure of 2,000 to 20,000 PSI to push the molten metal into the die. The pressure is maintained until the metal cools and solidifies, and then the finished product is ejected from the die. This method is suitable for high melting point alloys such as aluminum.
2) Hot Chamber Die Casting
Hot chamber die casting is a metal casting process that is specifically used to cast low melting point alloys such as zinc, tin, lead, and magnesium. This process is the most common and faster method than cold chamber die casting. In this method, the metal is melted inside a casting machine (in a furnace connected to the machine). A hydraulic system injects the molten metal into the mold under high pressure. The process is effective in producing complex shapes using high-quality materials with lower melting points. However, it is not suitable for alloys with higher melting points due to the risk of damaging the pump that injects the molten metal.
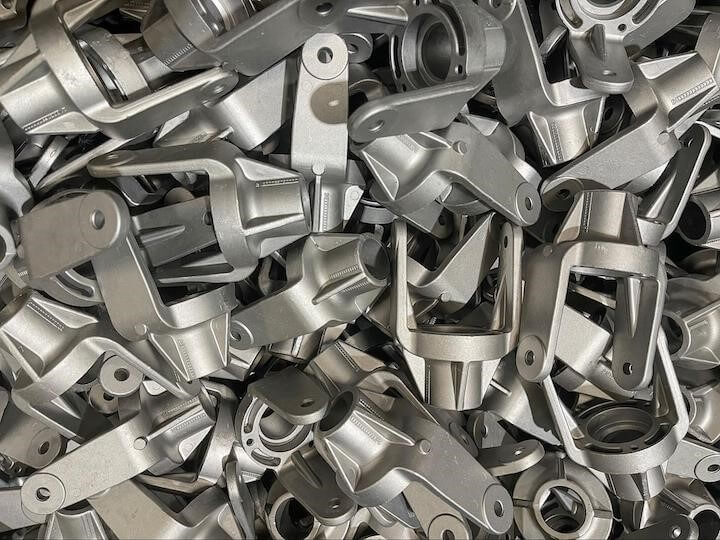
3.What are the steps involved in die casting?
Die casting involves the following steps:
1) Preparing the mold
The first step is to make the mold. The mold is usually made of steel and can withstand high temperatures and pressures. The mold design starts with a CAD (computer-aided design) drawing of the mold. This file is used to make the mold using CNC (computer numerical control) machining. Once the mold is made, it is prepared with a release agent or lubricant. This helps to release the casting. The mold is then clamped and closed with high pressure.
2) Metal preparation
Next, the metal is prepared for the injection process. The metal is usually an aluminum, zinc or magnesium alloy, which is melted using a furnace and poured into a ladle.
3) Metal injection
The molten metal is poured into the shot chamber. The shot chamber is hot in hot chamber die casting and cold in cold chamber die casting. After that, the molten metal is injected into the mold using high pressure.
4) Cooling
Allow the mold to cool and solidify into the shape of the mold.
5) Ejection
After cooling, the part will be hard and fully solidified and can be removed from the mold.
6) Trimming
The last step in die casting is the trimming step. This involves removing excess metal from the product. This is done by using a saw or trimming the mold.
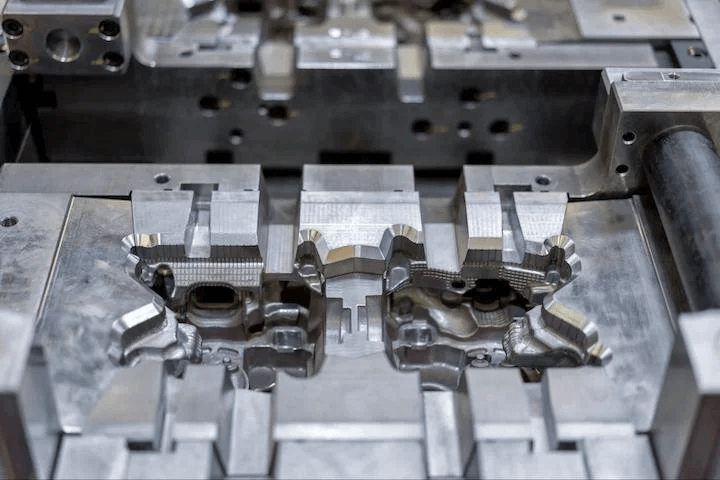
4.What are the best materials for die casting?
Many different metals, mainly non-ferrous alloys, are suitable for die casting. The three most common materials are:
1) Aluminum Alloys
Aluminum alloys are widely used in die casting due to their unique properties. Well-known alloys such as 380, 360, 390 and 413 have high operating temperatures, excellent corrosion resistance, low density, excellent strength and good thermal conductivity. In addition, aluminum alloys also have good stiffness, good strength-to-weight ratio, EMI and RFI shielding properties, and recyclability. They can also withstand high temperatures and maintain dimensional stability with thin walls.
2) Zinc Alloys
Zinc alloys, including Zamak #2, #3, #5, #7, ZA8 and ZA27, offer a balance of strength, toughness, robustness and cost-effectiveness. These alloys are known for their improved castability, reduced cycle times and extended die life. The mechanical properties of zinc alloys rival or even exceed those of other common die casting materials such as aluminum, magnesium and bronze. Their excellent casting fluidity facilitates thin-wall casting, resulting in smaller, lighter and more cost-effective components.
3) Magnesium Alloys
Magnesium, especially AZ91D alloy, stands out for its toughness, durability, lightness and good castability. 75% lighter than steel and 33% lighter than aluminum without compromising strength, magnesium alloys are the first choice for applications requiring complex castings with tight tolerances. The material’s excellent corrosion resistance further enhances its appeal. Magnesium alloys in die casting offer a valuable combination of strength and weight reduction, making them suitable for a variety of industrial and automotive parts.
4) Other Die Casting Alloys
In addition to the main materials, die casting can also involve other alloys such as bronze, copper, brass, lead and tin. For example, tin is known for its high fluidity and low melting point, which causes minimal wear on the mold. On the other hand, bronze, especially white bronze, is used in the jewelry industry due to its low melting point, similar to platinum and stainless steel alloys.