CNC machining: Which machining symbols are most important?
CNC machining is a precision process that requires strict quality control. To ensure the quality of the final part, metalworkers devised a quality control symbol system for machining called Geometric Dimensioning and Tolerancing (GD&T), which can be viewed from the machining symbols chart.CNC machining: Which machining symbols are most important?
There are 14 GD&T symbols in total – here’s what you need to know:
What are GD&T machining symbols?
For starters, GD&T is a system for defining and communicating engineering tolerances and relationships. It is a set of symbols on an engineering drawing that represent different aspects of the final product. Each of the 14 CNC machining symbols represents a specification, rather than writing out a defined specification. Geometric tolerances are applied to features through a control framework. The most commonly used tolerance categories are Form, Orientation, and Position; these 3 categories contain 10 of the 14 symbols.
1) Form Tolerances
Form tolerances control the general “shape” of a feature and are often used to refine dimensions. There are four GD&T symbols in form tolerance:
① Flatness
Flatness refers to how flat a surface is, unsurprisingly, independent of any other datums or features. Flatness is useful if you are defining features on a drawing that need to be uniformly flat.
② Straightness
The standard form of straightness is a two-dimensional tolerance that is used to ensure that a part is uniformly consistent across a surface or feature. Straightness can be applied to planar features, such as the surface of a block.
③ Cylindricity
In the simplest terms, cylindricity describes how well a part fits a true cylinder. In a tolerance sense, there are two concentric cylinders running the length of the feature: one inside and one outside. As long as the entire length of the part fits between the two cylinders, it meets the specification.
④ Roundness
Very similar to cylindricity, roundness describes how well an object fits a true circle. Cylindricity describes how well a part fits a 3D cylinder, while roundness is only related to how well a part fits a 2D circle.
2) Directional tolerances for CNC machining
Direction tolerance controls the “tilt” of a feature and is always associated with a basic angular dimension, usually used as a refinement of position. When applied to a surface, direction tolerance also controls form. There are three symbols suitable for direction tolerance; they are:
① Perpendicularity
Perpendicularity requires that a reference surface or line is perpendicular (or 90°) to a datum surface or line.
② Parallelism
Parallelism, not surprisingly, describes the direction in which a reference feature is parallel to a datum surface or line.
③ Angle
If parallelism describes how two parts align with each other, and perpendicularity describes how parts meet at a 90° angle, then angularity is a symbol used to describe the specific orientation of one feature relative to another at a reference angle.
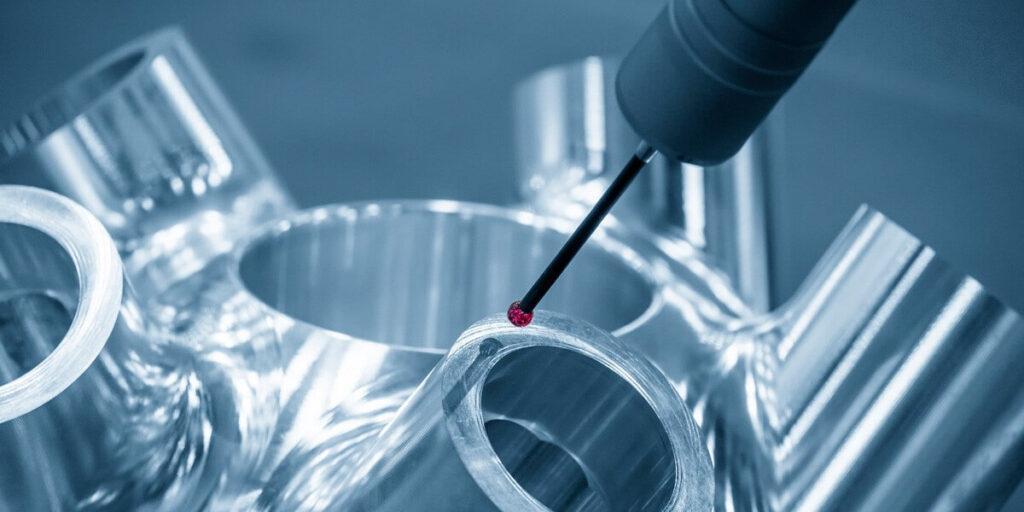
3) Position Tolerance
Position tolerance controls position and is always associated with a basic linear dimension. Position locates and orients the midplane or axis of a feature. Profile locates the surface of a feature. Profile is the most powerful of the bunch because it also involves both direction and form tolerances. There are three symbols under position tolerance, which are:
① Position
Position (or true position) is one of the most useful but also the most complex of all GD&T machining symbols. The two methods of using position are usually used “regardless of feature size” or in material conditions. Position is always used with size features.
② Surface profile
The surface profile describes the 3D tolerance area around a surface (usually a curve or shape). If defined on a surface, the entire surface where the radius lies must be measured within the tolerance area.
③ Line profile
The line profile describes the tolerance area around any line in any feature, usually a curved shape. The line profile is a 2D tolerance range that can be applied to any linear tolerance. If called on a surface (such as the radius of a part), the line profile specifies how much the cross section differs from the true curve radius.
Metal CNC machining by its very nature requires extreme precision. The parts must be able to fit together within the space allowed, which is why the design of any manufacturing process is just as important as what happens when we shape the blanks on our CNC lathes and CNC milling machines. GD&T is a universal language that helps save time and money while still providing the high quality required.