Milling: 10 important operating guidelines
Milling is one of the most common machining processes in the metalworking and fabrication industries. You may be surprised to learn that milling is not just one procedure in itself, but there are many types of milling operations, each with different complexities that make it more suitable for the needs of the finished part. Let’s take a look at some of these operations.
1.Slot Milling
In this process, the width of the tool is smaller than the width of the workpiece: it is used to make grooves in the workpiece. Thin tools make thin grooves. To cut a workpiece in half, very thin grooves can be made to penetrate the depth of the workpiece.
2.Vertical Milling
A vertical milling machine has a spindle in a vertical position or parallel to the column, mounted on a sliding head for added complexity. The most commonly used tool is an end mill or flat end mill. In some cases, it may also refer to a circular end mill.
3.Horizontal Milling
Horizontal milling machines are best suited for machining flat surfaces, dovetails, keyways and gears. The metal is fed into the cutter in the opposite direction to the direction of rotation of the cutter. Compared to vertical milling, horizontal milling allows the greatest force to be applied to the jaws holding the workpiece.
4.Side Milling
Side milling is the best choice when the goal is to machine a flat vertical surface on the workpiece. The depth of cut can be controlled by rotating the table’s vertical feed screw.
5.Group Milling
When two or more cutters are mounted together on a spindle and cut horizontal surfaces, this is called combination milling. The usual method is to mount cutters of different diameters, shapes and/or widths on the spindle. The potential combinations of cutters are endless and depend on the job requirements.
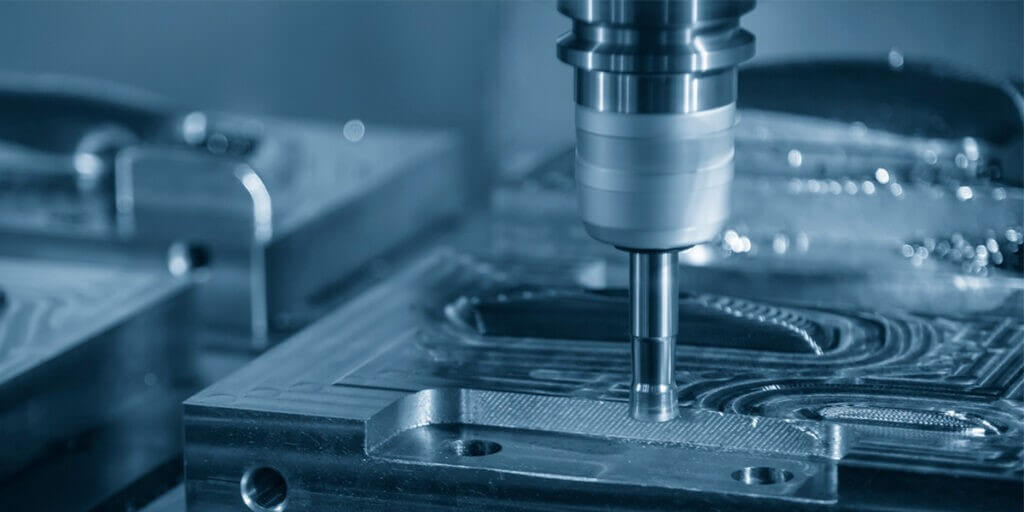
6.Straddle Milling
It is the best choice when you need to machine two or more parallel vertical surfaces at the same time. The process is accomplished by mounting two side milling cutters on the same spindle and positioning them apart so that they straddle the workpiece.
7.Up (and Down) Milling
Up milling is when the tool rotates in the opposite direction to the table feed. This is the opposite of down milling, where the tool rotates in the same direction as the table feed. What is the difference between the two? In up milling, the chip load on the teeth gradually increases, while in down milling, the chip load on the teeth decreases.
8.Profile milling
It allows special profiles consisting of curved and straight lines (or possibly only curved lines) to be machined in one cut. This can be done using a profile milling cutter or a fly cutter that is ground specifically for this purpose. The more common profile milling involves milling a semi-circular groove in the workpiece.
9.Face milling
The size and nature of the workpiece during its machining determines the type and size of tool required. The teeth on the periphery of the tool do most of the work, but if the tool is properly ground, the face teeth remove small amounts of excess material left behind by the workpiece or tool elasticity, producing a better finish.
10.Turret milling
It is done by drilling, cutting and shearing. During milling the spindle is stationary while the table moves along the X and Y axes. This process is usually used for “lighter” operations.
As you can see, the world of milling is diverse and encompasses many different techniques, tools, and results. The next time you think about milling a part, remember that an experienced machinist has a variety of methods available to get the job done.