3 Common Tool Cutting Problems in CNC Machining Discussed
Tool deformation and material damage are common problems faced by CNC machine users. There are several factors that contribute to tool damage and deformation used in CNC machines. Therefore, it is important to properly inspect the tool to prevent it from getting damaged. Before that, it is important to understand the factors that cause tool deformation and material damage in CNC machines. This post discusses the types of Tool cutting problems that lead to tool deformation and material damage in CNC machines.
CNC machining is a computer-controlled process; but the machine tool may not work as expected. Irregular cutting of the workpiece is one such problem. Given below are three common tool cutting problems faced by CNC machine operators.
1.Impact tools in CNC tool cutting
This is a situation where the cutting tool cuts a large amount of workpiece material and hits the workpiece during machining. The collision between the workpiece and the cutting tool not only creates high vibrations but also damages the workpiece. See the reasons and tips to avoid tool impact given below.
1) High Cutting Volume
The large tool diameter is one of the reasons for the large amount of cutting, and the amount of cutting can be easily reduced by selecting a tool with a small cutting diameter. The CNC machining method can set the amount of cutting, such as finishing and semi-finishing requires a smaller tool diameter.
2) Improper machining method
It is important to select the appropriate machining method based on the tool type and job requirements. For example, if the tool diameter is small, contour milling can be performed, but if the tool diameter is large, it is better to choose cavity milling.
3) Improper safety height
It is very important to choose the right safety height to avoid hitting the clamping device when lifting the tool. Therefore, it is best to keep the safety height higher than the clamping height.
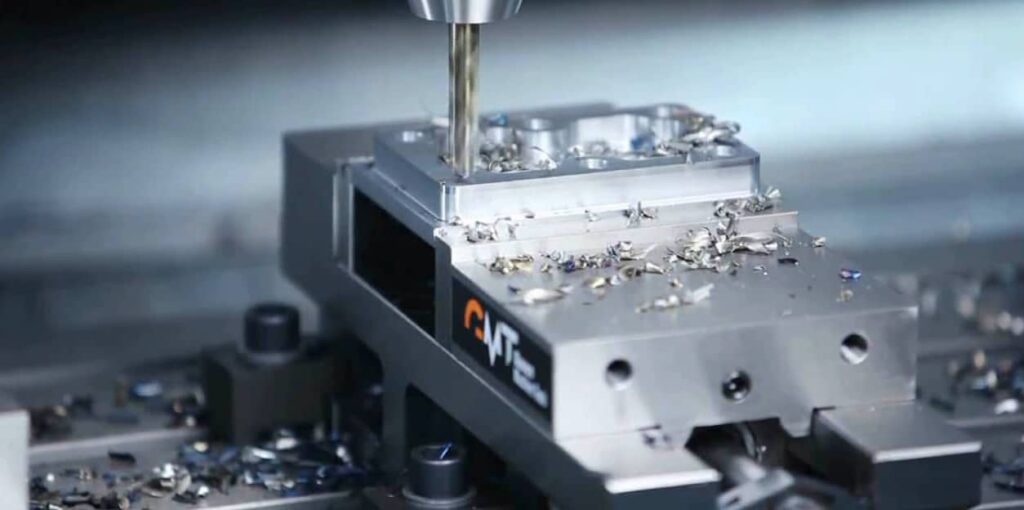
2.Problems during tool cutting: tool jumping
Tool jumping can cause tool deformation and material damage in CNC machines. This usually occurs due to significant vibration caused by excessive force on the tool. The main reasons that affect tool jumping are as follows:
1) Tool diameter
If you choose a tool with the same length and diameter and reduce the diameter by half, this will accelerate the deformation at least four times. Therefore, it is always better to choose a tool with a diameter greater than the length because this helps avoid vibration.
2) Tool length
If you choose a tool with the same diameter and length, and then increase the length, the deformation will increase three times. Therefore, to avoid this, use a tool that is shorter than the diameter.
3) The force to which the tool is subjected during cutting is proportional to its deformation
While it is impossible to eliminate force from the process, it can be reduced to avoid tool jumping.
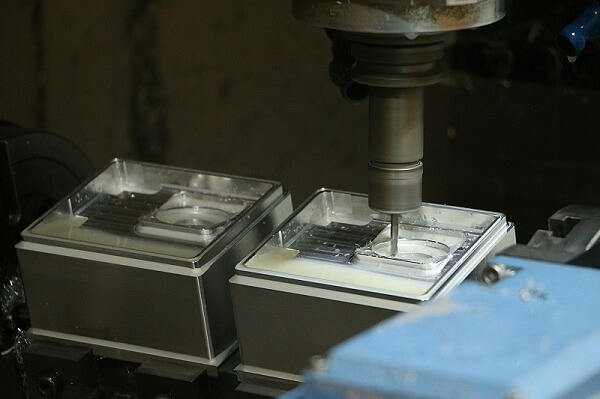
3.Overcutting
This means cutting a portion of the workpiece more than required. This can damage the workpiece. To avoid overcutting, it is always advisable to keep a close eye on the tool cutting path. In addition to this, it is also very important to be careful when cutting with the tool.
These considerations must be kept in mind to minimize the risk of tool failure and material damage during CNC machining, which could result in production downtime.