Detailed Discussion of CNC Machining Challenges
The demand for precision manufactured or machined parts, whether in standard or custom sizes, is increasing across all industries. OEMs and manufacturers look for advanced manufacturing technologies to stay ahead of the competition and meet application demands. Among all the manufacturing technologies, CNC machining is the most popular and favored one. This technology uses computer numerical control to produce parts or products of desired shapes, sizes, etc. from plastic or metal sheets. CNC machining has high efficiency and can manufacture complex parts with extremely high precision. Moreover, it performs mundane and repetitive manufacturing tasks with the same accuracy, regardless of the quantity. Having said that, CNC machining standard and complex parts certainly comes with various challenges. This post highlights some of the common CNC machining challenges. So, stay tuned.
CNC machining is a subtractive manufacturing process that produces desired parts with intricate details. It is more challenging than other manufacturing processes as it requires a high level of accuracy and precision. Moreover, there are several other factors that affect the outcome of the machining process. Some of the common challenges in CNC machining include:
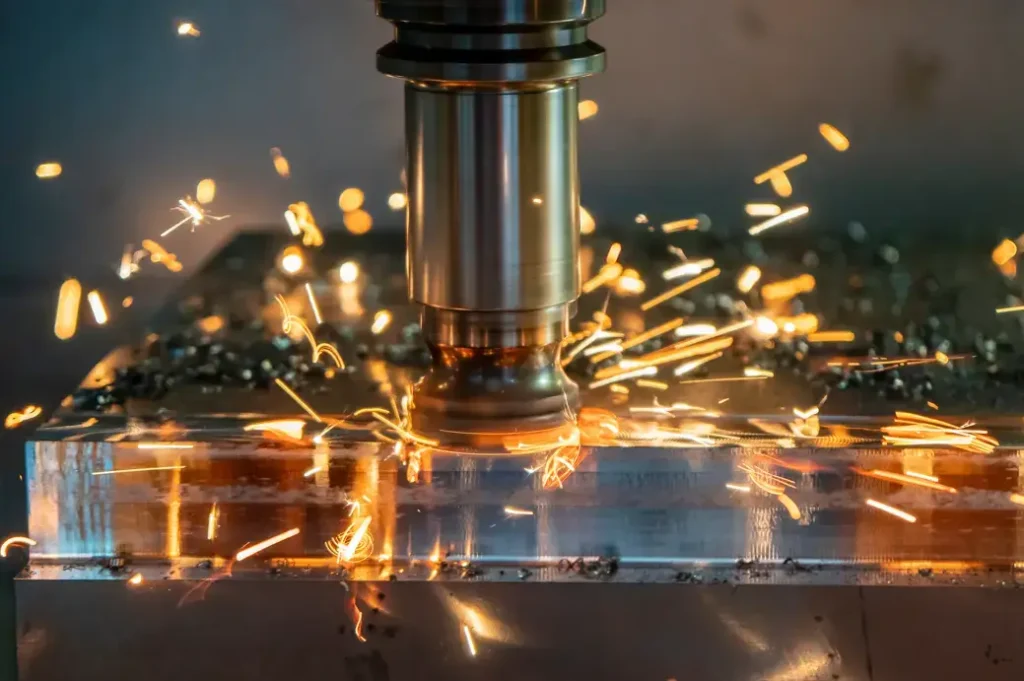
1.Complex Geometries
One of the major challenges faced by OEMs when doing CNC machining is producing parts with complex geometries. As a result, machine operators tend to take shortcuts in part fixturing or fixtures, or eliminate certain elements of the part design. This can result in a certain amount of deformation and increased stress. It can also negatively impact overall productivity.
2.Heat
Next is the generation of heat. Every material has its limitations. With the growing demand for strong, compact, and complex machined parts, experts are constantly on the lookout for new alloys and composite materials that are suitable. It is inevitable that materials sometimes exceed their limits, which can lead to overheating and subsequent damage. This can severely affect the overall quality of the desired product.
3.Tools
When designing parts using CNC machining, it is critical to use the right tools and settings. The wrong cutting tools can result in poor quality machined parts, such as burn spots or rough edges. In addition, the wrong cutting tools can also cause thermal and mechanical damage to the material. This problem can be solved by choosing the right CNC equipment after a thorough understanding of the application requirements. In addition, operators must refer to the instruction manuals provided by the machine manufacturer that detail the various parameters of different tools.
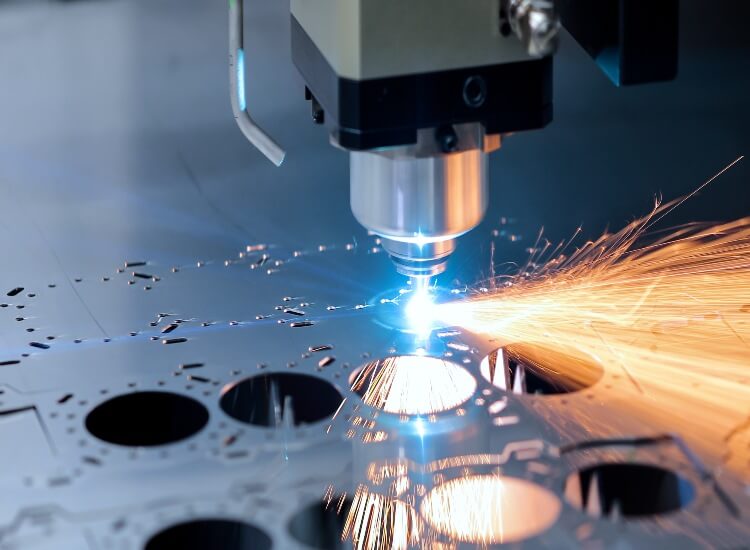
4.Programming
Improper programming is another big challenge in CNC machining that affects the entire production. As mentioned earlier, all CNC equipment is controlled by advanced automation programs, and incorrect programming can directly affect the accuracy of the machined parts. To avoid such situations, the operator should have enough experience and knowledge to use the correct CNC program.
5.Power Supply
Inadequate power supply is the most fundamental issue faced by some OEMs. CNC machining services are quite complex compared to other manufacturing processes and require adequate and seamless power supply. To achieve the desired results, adequate and continuous power and voltage supply must be ensured. Here, location and grid capacity along with backup power facilities play a major role.
Considering the above-mentioned points, it is crucial to consult a machinist with enough experience to handle the challenges in CNC machining services. This is beneficial in many ways. By hiring an experienced and knowledgeable CNC machining service provider, you can easily avoid these common mistakes that may otherwise result in losses or product recalls in the future. Moreover, this helps save money and time and ensures that the parts are produced to the highest standards.