Stainless Steel Milling : Benefits, Applications, and Processing Techniques
Stainless steel is a material that is widely used in industries such as construction and manufacturing. However, it is important to note that not all steels are created equal. Only a few may be suitable for your application, and it is not recommended to use unmachined material in any application. Machined stainless steel, or milled steel, is different from other types of stainless steel and offers many different benefits. In this comprehensive overview, you will discover the advantages of machined steel, explore the steel milling process, and learn why Xavier Custom Metal Milling Services in China is a good fit for your steel milling needs.
1.Milled Stainless Steel Definition
Stainless steel milling refers to the process of producing components from an alloy of iron and carbon (known as milled metal or milled stainless steel). It is performed using stainless steel milling tools (manual milling machines and CNC milling machines). The machining process involves removing excess material from a steel workpiece to produce the desired shape and size. The method involves using steel milling tools that are precisely designed to effectively cut the properties of stainless steel.
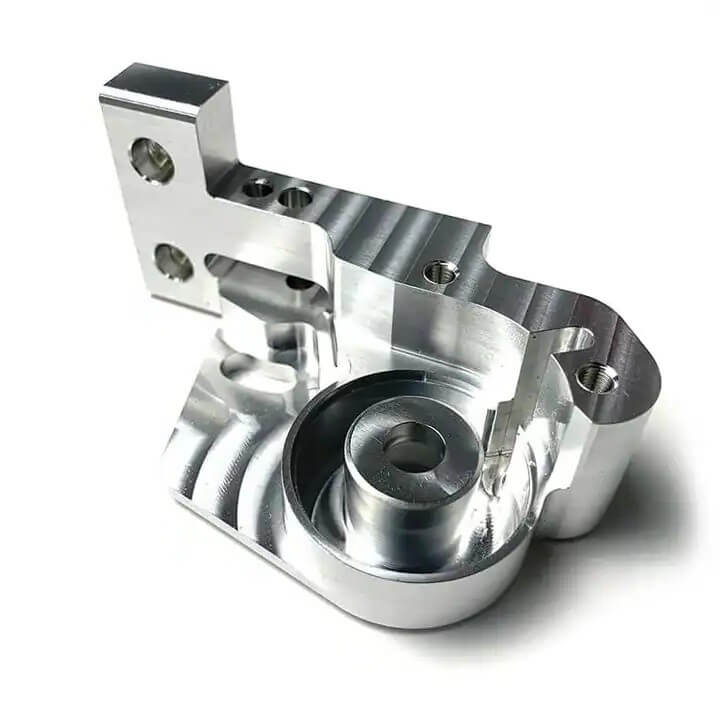
2.Advantages of Milled Steel
Machinery stainless steel has advantages that make it suitable for a variety of uses. Some of these benefits include:
- Stainless steel milling can control shape, size, and reduce the risk of error, thereby improving overall precision and efficiency, which is required by the automotive, aerospace, and other manufacturing industries.
- In some fields where aesthetics and surface finish are the main concerns, steel milling can provide flat, smooth, shiny and polished surfaces with long-lasting effects. Therefore, it can make the product look valuable and attractive.
- In addition, milled metals are stronger and more durable. Any defects or scratches on the surface are removed by machining so that no crack initiation is observed when the material is subjected to stress or cyclic loading. This makes milled metals more suitable for applications where strength is the main concern.
3.Features of Common CNC Milled Stainless Steel Materials
CNC milling services are a precise method of machining parts from a variety of materials, including different grades of stainless steel.
4.Limitations or Challenges of Stainless Steel CNC Milling
In addition to the advantages of milling steel, there are some limitations that must be acknowledged.
- It is sometimes not economical or affordable for low-budget applications because specialized tools are required.
- For precision machining, skilled operators with proper knowledge and CNC equipment are required.
- In addition, the hardness of steel can cause difficulties during milling. It requires powerful tools as well as certain precision machining standards. This standard involves appropriate speeds and feed rates.
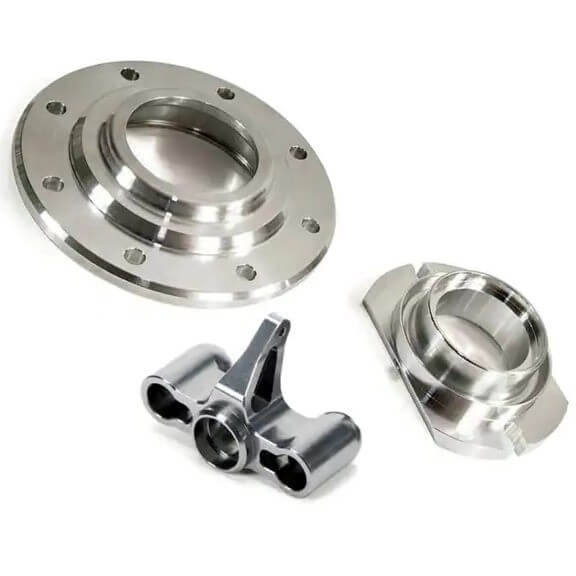
5.Steel Milling Process: Steps
The steel milling process consists of various processes used to give shape and size to the unmachined steel workpiece. Here are all the details of the steel milling process:
1) Workpiece Preparation
The procedure starts with preparing the steel workpiece for milling. Surface cleaning, contaminant removal, and proper clamping to hold the metal piece during machining are all part of the process.
2) Tool Selection
The right steel milling tool is essential for successful steel milling. Tool selection is influenced by factors such as the type of steel, the required cutting parameters, and the complexity of the machining operation.
3) Machine Setup
Once the workpiece and tool are ready, the milling machine must be set up. This includes changing the machine settings such as spindle speed, feed rate, and depth of cut as required for the milling operation.
4) Milling
Once everything is in place, the milling process begins. The cutting tool removes excess material from the workpiece in an orderly manner following the specified tool path and cutting parameters. This process is repeated until the desired shape and size is achieved.
5) Finishing
After milling, the milled steel parts are finished by polishing or coating to improve their surface finish and appearance. Quality control tests are performed to verify dimensional accuracy and standardization.
6.Speeds and Feeds for Stainless Steel Milling
Due to its high hardness and limited thermal conductivity, milling stainless steel requires careful consideration of speeds and feed rates to produce the best results. Consider the following elements:
1) Cutting Speed
Stainless steel milling should be performed at a slower speed than other materials to avoid overheating and excessive tool wear. It is recommended to start with a moderate cutting speed and then adjust based on results and tool life.
2) Feed Rate
For stainless steel milling, lower feed rates are generally required to control chips and reduce the potential for work hardening. Slower feed rates aid in chip evacuation and reduce heat generation.
3) Cutting Fluid
Selecting the right cutting fluid is essential for efficient stainless steel milling. Cutting fluids aid in cooling the tool and workpiece, lubricating the cutting zone, and flushing away chips. It is best to use a high-performance cutting fluid designed specifically for stainless steel machining.
For hard materials, tool speeds should be kept low to avoid tool breakage. On the other hand, the ratio is relatively high for soft materials. The table below shows tool speeds for some materials.