Is Aluminum Machining Parts Easy?
A general term for aluminum-based alloys. The main alloying elements are Cu, Si, Mg, Sn, and the minor elements are nickel, titanium, chromium, lithium, etc. Aluminum alloys have low density, good plasticity and can be processed into molded materials. They have excellent electrical conductivity, thermal conductivity and corrosion resistance. The alloy formed by adding certain elements can maintain the advantages of pure aluminum’s light weight while also having high strength. This makes its “specific strength” better than many alloy steels, making it an ideal structural material. Aluminum CNC machining services are widely used in the automotive industry, consumer electronics, energy equipment and aerospace.
1.Machinability of CNC Aluminum Machining Parts
1) Precision aluminum machining manufacturing process
Industrial machining of aluminum parts places high demands on tools, especially aluminum alloys. These tools must meet the needs of high-quality aluminum machining parts while also being cost-effective. Solid carbide tools have very sharp cutting edges and grooves, so they have low cutting forces in aluminum finishing, and have the advantages of large chip space and smooth chip evacuation. Therefore, solid carbide tools have gradually replaced traditional high-speed steel tools.
2) Aluminum CNC Processing
Due to the relatively low strength and hardness of aluminum alloy, small plasticity, small tool wear, high thermal conductivity and low cutting temperature, aluminum alloy has good machinability and is an easy-to-process material with high cutting speed and suitable for high-speed cutting. However, the melting point of aluminum alloy is low, and the plasticity increases after the temperature rises. Under the action of high temperature and high pressure, the friction at the cutting interface is very large. It is easy to stick the knife; especially for annealed aluminum alloy, it is not easy to obtain a small surface roughness.
In order to obtain a smooth workpiece surface, a combination of rough cutting and fine cutting is used as much as possible, because the blanks of various qualified workpieces always have some oxide layers, which will cause the tool to wear to a certain extent. A considerable degree. If the final cutting process uses a polished sharp tool for fine cutting, the above requirements can be met.
Among them, the appropriate tool material is selected according to the silicon content in the aluminum silicon alloy. The silicon content is less than 12%. ISO K10-K20 tungsten steel tools can be used, and diamond tools can be used when the silicon content is greater than 12%. During cutting, the oxidized aluminum oxide chips will have a chemical affinity with the tool, resulting in adhesion and chip accumulation, which will increase friction resistance and accelerate wear.
Once the chip nodules are formed, they will replace the cutting edge for cutting, and the sharpness of the tool blade in ultra-precision machining will lose its meaning. Moreover, the bottom of the chip nodules is relatively stable, while the top is very unstable and easy to break. After breaking, part of it is discharged with the chips, and the other part remains on the machined surface, making the machined surface rough. The concave and convex parts other than the convex edge of the chip nodules will directly make the machined surface rough, and the friction between the chip nodules and the machined surface will also increase the surface roughness.
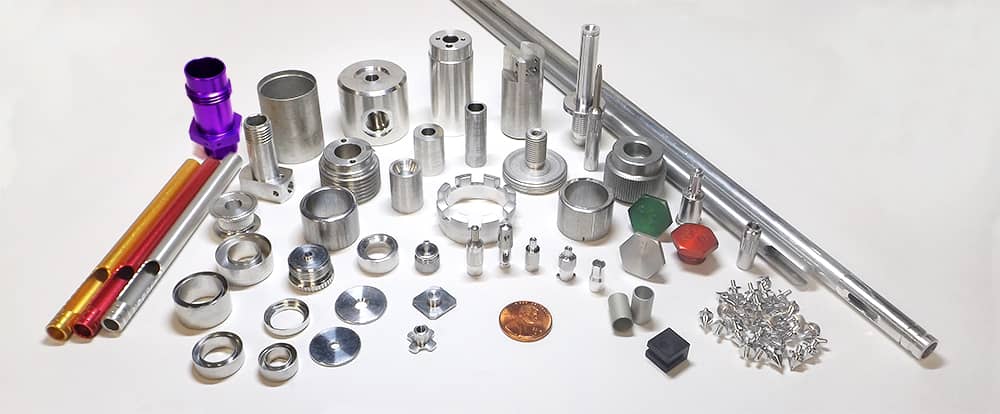
2.Selection of aluminum processing materials
The most commonly used aluminum alloys are 6061 T6 and 7075. With the popularity of energy conservation and environmental protection, soft aluminum parts have a high degree of plasticity and recyclability, making them the best choice for mechanical purposes. On the contrary, if aluminum is mixed with other specific elements such as magnesium, silicon, copper, zinc, etc., it can form an aluminum alloy after heat treatment. Aluminum alloys have good strength, super-hard aluminum alloys can reach 600Mpa, and the tensile strength of ordinary hard aluminum alloys is 200-450Mpa. Aluminum machining parts have been widely used in the manufacturing industry. Aluminum is a commonly used machining material for Chinese machining manufacturers and is one of the 50 materials we can provide.
3.Advantages of aluminum CNC machining parts
1) 6061-T6
It is a corrosion-resistant type with good strength and uniformity. Among aluminum parts, 6061-6 is mainly used for material processing, which is not easy to deform and has almost no tolerance problems. In the process of machining aluminum parts, good anodizing post-treatment effect can be achieved.
2) 7075 aluminum plate
It is Al-Zn-Mg Cu, a good super-hard aluminum series. It has good mechanical properties and wear resistance and is easy to machine. Aluminum parts are also machined, with good anodizing treatment, corrosion resistance and anodizing resistance. 7075 aluminum is a classic material used in the aviation industry. Precision aluminum machining parts have complex structures and high precision requirements.
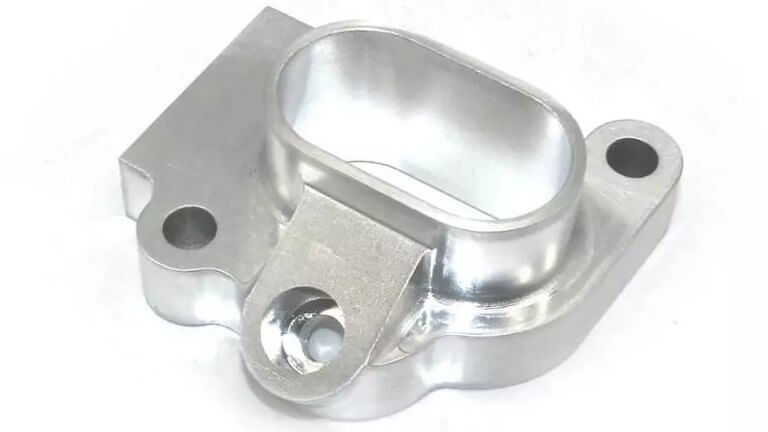
4.CNC machining aluminum parts application
Precision machining aluminum machining parts Throughout the design to processing process, programmers can efficiently complete the review of each project. Precision machining workshop Xavier CNC machining Shenzhen manufacturer, People’s Republic of China. Ensure that each design fits perfectly by accurately evaluating cost, plasticity and complexity. One-off parts, high machining, modern molded products for complex space surface operations such as automotive parts and aircraft structural parts can be perfectly processed. Therefore, CNC machining aluminum parts are widely used in machinery manufacturing, transportation machinery, power machinery and aviation industries.
Based on your CAD data, CNC machining manufacturers can cut materials in any shape. No matter how many parts your assembly consists of, Xavier can quickly produce high-precision aluminum machining parts while meeting strict tolerance standards. Aluminum is commonly surface treated, including anodizing, passivation, brushing, sandblasting, powder coating, and printing.