CNC Parts: Important Factors Affecting Customization
1.Confirmation of CNC part drawings
One day we received an inquiry from a buyer (Mr. A) on tuofa-cncmaching.com. As usual, we asked the buyer’s basic information and obtained the 2D/3D drawings of the parts (pdf, dwg, stp, step format, etc.) from the buyer according to the buyer’s inquiry content. The drawings usually include the part name, size, material, tolerance, quantity and surface treatment, etc.
If the buyer does not indicate all the information in the drawing, we need to take the initiative to contact the buyer to confirm that Mr. A needs to process the optical lens housing this time. The material is 6061 T6 aluminum, the size and other details are all on the drawing, and the tolerance meets the ISO 2768 standard. After confirming with Mr. A, we will send the drawing to our engineering department.
2.Instant Quote for CNC Parts
The engineering department will look at the drawings and confirm that the parts are within our processing range. Our quotation department will give me a quotation based on the drawings, including the unit price of each part, delivery time, precautions, etc.
After getting the quotation, I need to make a quotation and send it to Mr. A. Usually, our quotation is valid for 7 days. Mr. A said the price is acceptable, and then I contacted the transportation company to calculate the freight and communicate the customs declaration of the order.
After confirming these contents, I issued a pro forma invoice to Mr. A, which contains detailed information such as fees and the company’s collection account.
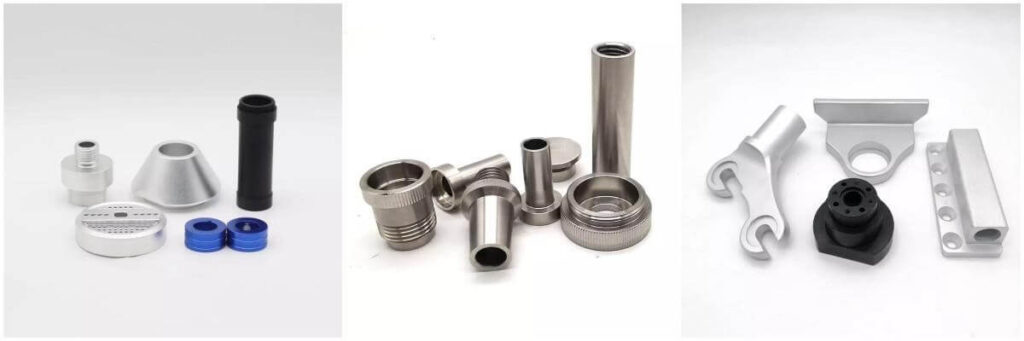
3.CNC parts materials
After Mr. A completes the payment, I will place a production order within the company and send it to our planning department together with the buyer’s drawings. After receiving the production order, the planning department arranges the purchase of raw materials according to the customer’s drawing information.
This order requires the purchase of 6061 T6 aluminum bars, which will be slightly larger than the buyer’s drawing size. The drawings will be sent to the engineering department for programming. After completion, they will be copied to our CNC machine for subsequent processing.
After the materials come back, our technical workers will load the written program into the CNC machine tool and debug it, and then conduct trial production.
4.CNC parts processing process
The aluminum strip is turned on a CNC lathe to the same length as the aluminum segment for later use, and then the aluminum segment is mounted on the fixture. The outermost surface of the aluminum strip will be cut off from the lathe, and this step can obtain an appearance without defects such as bulges and depressions.
After that, simply outline the appearance of the buyer’s drawing. At this time, the aluminum profile still has a margin of the buyer’s drawing. This is for the subsequent finishing lathe forming.
After this step is completed, the aluminum needs to be left for a period of time so that the material can release stress well and prevent dimensional deviations due to material problems in subsequent processing. After that, the aluminum profile needs to be cut out of a smooth surface and the groove is also cut out.
There are two places on the lens housing that need to be embossed. One embossed pattern will be rougher, which is convenient for consumers to adjust the focal length, and the other embossed pattern will be more delicate, which can provide a better look.
After this step is completed, the internal aluminum needs to be removed. The technician will cut the internal threads according to the drawings. The internal threads are the slide rails that adjust the focal length of the optical lens. We need to use a multi-head screwdriver head to process to get the desired effect, and then process and chamfer the sharp corners and burrs. After the angle is completed, the parts will enter the CNC milling machine for processing.
As shown in the figure, there are 4 threaded holes at the bottom of the lens housing. We use tools of corresponding sizes to mill and chamfer the threaded holes, and then need to transfer the parts to the tapping machine for tapping. The completion of the above steps means that the CNC processing process has been completed, and the next step is the surface treatment process.
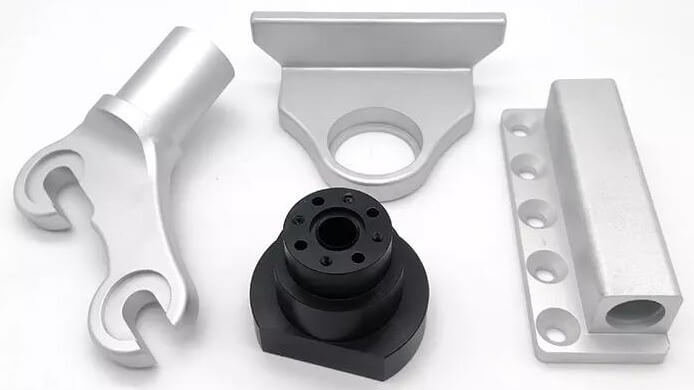
5.CNC Parts Surface Finishing Service
According to Mr. A’s needs, we first sandblasted the parts. After completing this step, we need to check whether there are bumps and scratches on the surface.
This time we use visual inspection, and only qualified parts will enter anodizing. We use a special fixture to support the inside of the part. Because the part has high requirements for appearance and function, anodizing will inevitably form a “shadow” at the contact point between the fixture and the part.
To this end, we improved the fixture, reduced the contact point between the fixture and the part, and minimized the “shadow” area. After this step, we got a black camera lens housing.
6.CNC Parts Quality Control
CNC metal parts suppliers need to inspect the parts in subsequent processes. For parts with high precision requirements such as lens housings, we usually use full inspection.
We use height gauges for dimensions and screw gauges for threaded holes. The dimensions must be within the tolerance range to be qualified. Parts that fail the inspection need to be reworked or redone. Qualified products will be affixed with a qualified mark and packaged.
The packaging staff needs to check the appearance of the parts and can find that the parts have been bruised or scratched during packaging and handling. We will wrap qualified products in paper and protect them with bubble bags.
At the same time, we will affix labels with the drawing name, quantity, code and place of origin on the packaging. After all the parts of the order are packaged, they will be packed into a specific outer box. The outer box must first be strong and reliable to prevent the product from being damaged during transportation.
7.Transportation type
Completing the above steps means that our order is more than half completed. The next final work is transportation and customs declaration. We need to prepare customs declaration materials for the transportation company so that the buyer can also better declare customs after receiving the product. After completing customs clearance, the follow-up is to wait for the buyer to receive, inspect and feedback on the product.