Principles of CNC Machining Process
On CNC machines in general, and machining centers in particular, parts and operations are processed as intensively as possible, and CNC machining near me can do just that. Supreme Machining has a wide range of equipment options and the engineering experience to know which process is best suited.
That is, the parts can complete most or all of the processes that can be processed by this CNC machine tool in one clamping.
1.The principle of maximum process concentration and one-time positioning
In CNC machining, process concentration can reduce the number of machine tools used and the number of workpiece clamping times, reduce unnecessary positioning errors, and improve productivity.
For hole system processing with high coaxiality requirements, after one clamping, the entire processing of the coaxial hole system should be completed by sequential continuous tool change, and then the holes in other positions should be processed to eliminate the influence of repeated positioning errors and improve the coaxiality of the hole system.
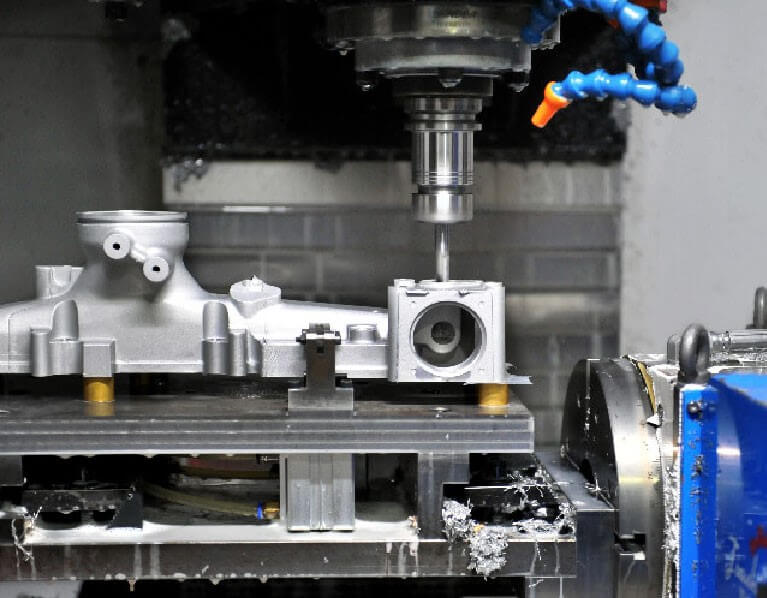
2.The principle of roughing first and then finishing
In CNC machining, when dividing the process according to the machining accuracy, rigidity, deformation and other factors of the parts, the process should be divided according to the principle of separation of roughing and finishing, that is, semi-finishing and finishing should be carried out after all roughing is completed.
For a certain CNC machining surface, finishing should be carried out in the order of roughing-semi-finishing-finishing. During roughing, the performance of the machine tool and the cutting performance of the tool should be fully utilized under the conditions of ensuring the machining quality, tool durability, and the rigidity of the machine tool-fixture-tool-workpiece process system.
Before finishing, try to use the maximum number of cutting times to make the machining allowance of each part as uniform as possible. During finishing, the machining accuracy and surface quality of the parts should be guaranteed.
Therefore, during finishing, the final contour of the part should be completed continuously by the last cutting. To ensure the machining quality, the finishing allowance should generally be 0.2-0.6mm. It is best to leave a period of time between roughing and finishing to allow the deformation of the parts after roughing to be fully restored, and then finish to improve the machining accuracy of the parts.
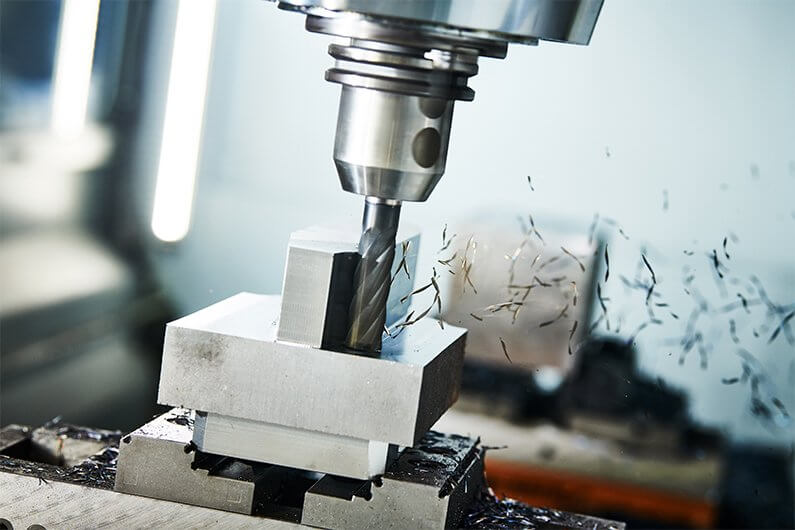
3.The principle of near first and far later, face first and hole later
According to the distance between the processing part and the tool setting point, in general, the part close to the tool setting point is processed first, and the part far away from the tool setting point is processed later, so as to shorten the tool moving distance and reduce the idle travel time.
For turning, processing near first and far later is also beneficial to maintain the rigidity of the blank or semi-finished product and improve its cutting conditions.
For parts that need both flat milling and boring, the order of flat milling first and boring later can be followed.
Due to the large cutting force during flat milling, the parts are prone to deformation. Milling the surface first and then boring can give the parts a certain recovery time. Boring after the deformation is restored is beneficial to ensure the processing accuracy of the hole.
Secondly, if the hole is bored first and then the plane is milled, burrs and burrs will appear at the hole, affecting the assembly of the hole.