Advantages of CNC Machining Services in China
China has positioned itself as a global powerhouse for high-quality, cost-effective CNC machining services. As a leading destination for precision manufacturing, China has huge untapped potential in everything from prototypes to mass production, and is generally qualified for iso machining.
With advantages such as lower labor, material and infrastructure costs, CNC machining in China can save more than 20-30% compared to Western suppliers.
However, realizing the full savings and quality potential requires proper vetting of partners, optimizing specifications, and implementing a strong quality assurance program. This guide explores the advantages of CNC machining in China while outlining best practices to ensure manufacturing success. Read on to unlock the huge potential that China offers!
- China offers huge cost savings for high-quality CNC machining, up to 20–30% over Western factories.
- Chinese suppliers have invested heavily in advanced machining equipment and quality control to meet global precision standards.
- Extensive manufacturing networks offer diverse solutions tailored to complexity, size, material, and industry.
- Effective communication and a trusted partnership with suppliers are critical to reducing risk.
- Conduct a thorough vetting and factory audit before settling on a CNC machining partner.
- Prioritize detailed specifications, multi-stage inspections, and transparent collaboration.
- Realistic timelines, win-win negotiations, and long-term agreements optimize efficiency and savings.
- Best practices such as DFM, digital tools, and consistent feedback loops can expand success.
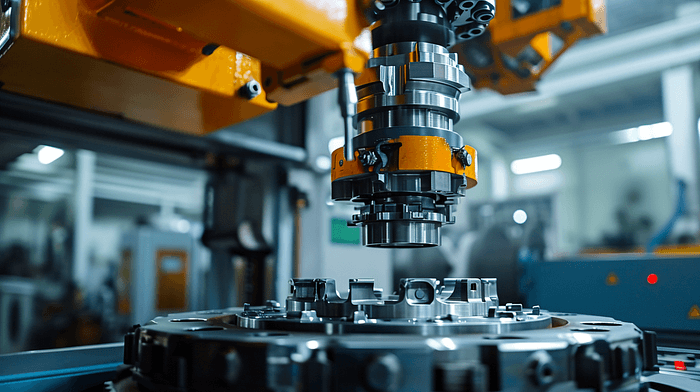
1.Unleash the potential of CNC machining in China
China has positioned itself as a global powerhouse of high-quality, cost-effective CNC machining services. As a result, as a major destination for precision manufacturing, China has huge untapped potential in everything from prototypes to mass production.
2.Achieve significant cost savings
With advantages such as lower labor, material, and infrastructure costs, Chinese CNC machining can save more than 20-30% in costs compared to Western suppliers. Carefully vetting partners ensures quality while maximizing value.
3.Meet global quality standards
Investing in advanced equipment and sound quality management enables Chinese factories to provide parts that meet global standards of accuracy and consistency. At the same time, strict procedures also help comply with regulations and assist in the production of high-precision parts.
4.Leverage flexible customized solutions
Strong manufacturing capabilities and extensive expertise enable Chinese factories to provide customized CNC solutions that meet technical specifications and unique production requirements. This flexibility enables factories to better adapt to market conditions.
5.Overcoming Perceived Risks
While intellectual property and communication barriers are common issues, proper due diligence when selecting suppliers can minimize risks. Peace of mind can be achieved by establishing transparency and closely monitoring quality.
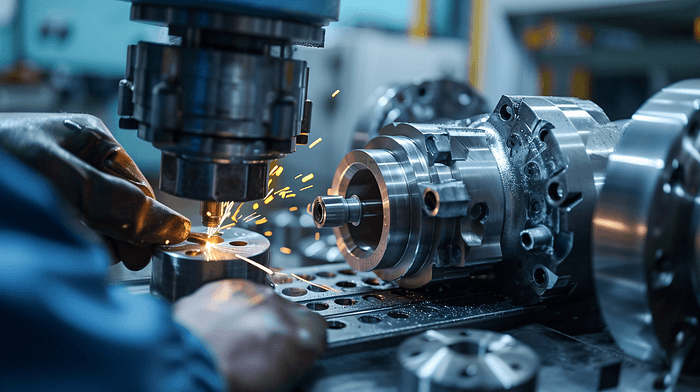
6.Why Choose China for CNC Machining?
China has become a global hub for high-quality, cost-effective CNC machining services. China has several key advantages that make it an ideal destination for your machined parts.
1) Unlocking Cost Competitiveness
China’s CNC machining industry has a huge cost advantage over its Western counterparts. By understanding the drivers behind China’s cost benefits, foreign companies can make informed decisions when selecting Chinese suppliers.
2) Lower Material and Labor Costs
Both raw materials and wages are much cheaper in China than in Europe and North America. It costs 20-30% less to source steel, aluminum, and industrial polymers directly from Chinese suppliers. Add in machining labor fees of about $10-15 per hour, and outsourcing to China can result in significant savings.
3) Efficient Production Infrastructure
Decades of investment in advanced CNC machine tools and streamlined facilities have enabled Chinese factories to operate at a higher level of efficiency. An extensive network of suppliers also facilitates timely procurement of materials and components. These factors reduce production costs.
4) Access to a vast manufacturing network
The concentrated manufacturing ecosystem in major Chinese centers offers thousands of workshops that provide auxiliary processes such as heat treatment, electroplating and finishing. This facilitates an integrated production chain, shortens delivery times and reduces logistics expenses. Because China’s CNC machining places great emphasis on efficiency, infrastructure and supply chain integration, it is able to promise to provide components at very competitive prices without compromising quality. To analyze the exact cost-saving potential, it is necessary to work closely with suppliers at the quotation stage.
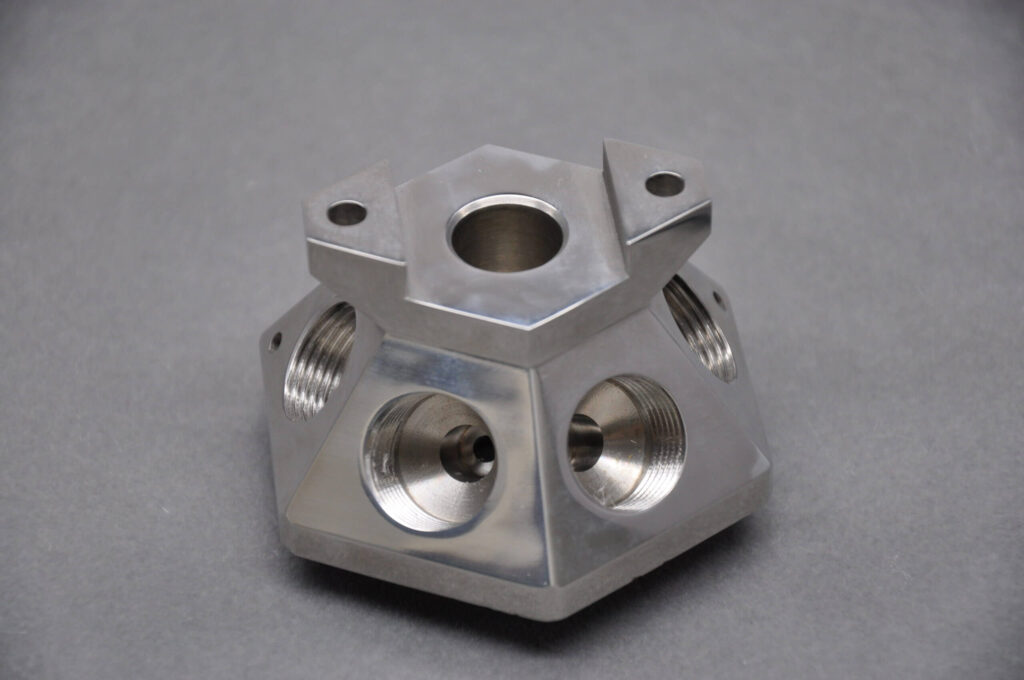
7.Unlocking high precision and high quality
China’s CNC machining capabilities have developed rapidly and are able to achieve global standards of high precision, quality and consistency. By investing in advanced equipment, processes and talents, Chinese suppliers are able to offer very attractive price standards.
1) Invest in cutting-edge technology
Chinese CNC factories continue to adopt the latest machining technologies. Multi-axis CNC machines with precision control capabilities can achieve complex part geometries, smooth surface finishes and tight tolerances. At the same time, smart factory solutions also help process monitoring and quality control. China’s CNC factories’ focus on emerging technologies ensures their global competitiveness.
2) Implementing robust quality management
To earn the trust of international customers, Chinese manufacturers have invested heavily in quality management systems. Many major CNC machining suppliers have globally recognized certifications such as ISO 9001. They follow strict procedures for supplier selection, machine calibration, process inspection, final testing, etc. These stringent measures ensure consistent, high-quality output.
3) Cultivating professional talent
Experienced CNC machining workers are essential for precision manufacturing. Top Chinese factories train technicians extensively in programming, setup, inspection, and maintenance. By cultivating professional talent and best practices in complex CNC processes, they are able to achieve excellent repeatability and quality. Operators also take pride in their work and pay close attention to detail.
With cutting-edge equipment, strict quality control, and skilled staff, China’s leading CNC machining suppliers have proven their ability to deliver high-precision components in a cost-effective manner. Continued investment in emerging technologies and talent will only strengthen China’s value proposition as a preferred destination for precision CNC machining needs, laying a solid foundation for future market competition.
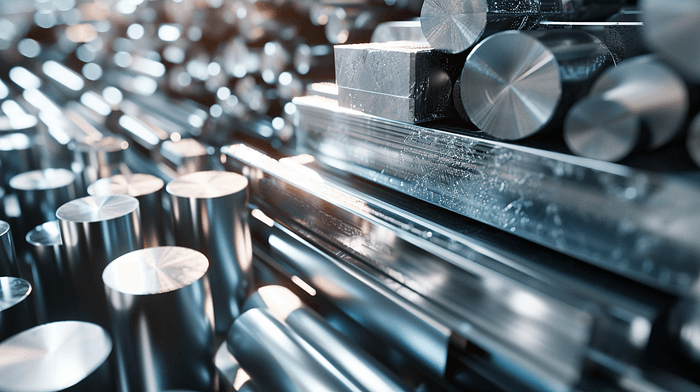
8.Unleashing flexibility and customization
China’s CNC machining capabilities are extremely diverse and can meet a wide range of product needs. And Chinese CNC factories have experience serving industries ranging from medical devices to aerospace, and have developed flexible production capabilities.
1) Customized complexity
Chinese CNC manufacturers invest heavily in advanced machine tools to handle complex problems. At the same time, their expertise also empowers creativity. For example, 5-axis CNC machining can produce complex geometries through its rotational function. This allows greater design freedom, and with experience and advanced equipment, Chinese CNC workshops can turn complex prototypes and products into reality.
2) Adjust output scale
China’s vast manufacturing network provides CNC machining services suitable for small-batch prototypes to large-volume production. Whether you need 1 part or 10,000 parts, Chinese suppliers have the infrastructure to deliver. Their production flexibility and just-in-time principles can effectively adapt to fluctuating order volumes.
3) Exploiting material diversity
From versatile plastics to high-performance alloys, Chinese CNC manufacturers are able to provide expertise in a variety of materials. They continue to expand their capabilities and focus on materials required by industries such as aerospace, automotive, and medical. Whether your application requires lightweight metals, durable steels, or biocompatible plastics, the right CNC partner in China can deliver parts that meet your specifications.
At the same time, by offering custom services for varying project complexities, sizes, and material requirements, CNC machining in China offers customers flexibility and customization. This flexibility caters to a wide range of product development needs, unlocking the potential for innovation.
9.Explore the Chinese CNC Market Landscape
For first-time buyers, entering China’s massive CNC machining industry can seem daunting. However, by thoroughly researching suppliers, clearly communicating your specifications, and building strong relationships, you’re sure to find your ideal partner.
10.Perform Due Diligence on Potential Suppliers
Before selecting a CNC shop in China, it’s critical to conduct thorough due diligence. Key areas to check include:
1) Capabilities and Specialization
Do they have experience handling the materials, tolerances, and production volumes you require? Can they meet your unique needs?
2) Quality Certifications
Do they have key ISO certifications or industry-specific quality badges? This demonstrates a commitment to quality.
3) Customer References
Talking to existing customers can provide insight into communication, quality, and reliability.
4) Factory Infrastructure
A site visit can provide insight into production capabilities, quality control, and workforce expertise.
Thoroughly vetting suppliers at the outset can save headaches later, and don’t be afraid to ask lots of questions early on. It’s all necessary to ensure that you’re on track.
11.Communicate Designs and Specifications Clearly
Miscommunication is a common pitfall when outsourcing CNC work to China. Spend enough time communicating every detail of your requirements, including:
- Technical Drawings: Provide complete 2D drawings and 3D models to avoid assumptions.
- Material Selection: Specify the alloy grade and treatments required to achieve the material properties.
- Tolerances: Set clear standards for precision and consistency.
- Surface Finish: Specify precise roughness or appearance requirements.
- Inspection Standards: Establish inspection points and quality control expectations.
Try not to leave any room for misunderstandings.
12.Build Strong Supplier Relationships
Treat your Chinese CNC partner as an extension of your team. Cultivate transparency and trust through:
- Ongoing communication: Maintain open channels for collaboration during all project phases.
- Onsite visits: Visiting facilities in person strengthens relationships and accountability.
- Feedback loops: Suggestions are welcome to improve manufacturability and protect IP.
- Win-win negotiations: Seek reasonable terms to maintain long-term relationships.
By proactively strengthening supplier relationships, you can expand your success.
13.Unveiling the scope of CNC services
China’s CNC machining capabilities cover a wide range of services to meet your manufacturing needs. From rapid prototyping to mass production, Chinese factories can deliver parts and components in a variety of material types using a variety of technologies.
1) From Prototype to Production
Prototyping can quickly and cost-effectively turn ideas into reality. Chinese factories use CNC efficiency to produce prototypes that demonstrate form, fit, and function. Once validated, low-volume and high-volume production can be ramped up using optimized workflows. This makes China an ideal choice for custom metal manufacturing or scaling up production from 1 part to 10,000+ parts.
① Rapid prototyping
Turning concepts into 3D prototypes is essential for testing. And China’s CNC machining combines the speed and savings of iterative prototyping, which can verify ideas through affordable prototypes before investing in production.
② Small and large-scale production
Efficient CNC processes can adapt to the scale of projects. For less than 1,000 parts, small-batch production can reduce indirect costs. For large-volume needs of more than 5,000 parts, streamlined workflows can be used to achieve economies of scale.
③ Custom metal processing
Use extensive metal processing expertise to manufacture steel, aluminum, titanium or other metals to specifications. Chinese factories can provide custom metal processing services, including milling, turning, casting, stamping, etc., for one-off artwork or mass production.
14.Mastering a Variety of Materials
China’s machining capabilities span metals, plastics, wood, and composites. Material selection is customized based on application requirements such as strength, corrosion resistance, conductivity, and more.
1) CNC Aluminum Machining
Aluminum’s strength-to-weight ratio and corrosion resistance make it widely used across industries. China can provide specialized CNC aluminum machining that utilizes multi-axis precision and advanced cutting methods.
2) CNC Steel Machining
Steel’s high strength and durability are necessary for applications that demand durability. Chinese factories leverage decades of steel machining expertise to perform precision CNC steel manufacturing, ensuring that steel parts are produced to the task.
3) CNC Titanium Machining
Titanium is popular in the aerospace and medical fields for its strength and biocompatibility. As a major producer of titanium, China is able to provide both supply and precision machining capabilities for this expensive metal.
4) CNC Plastic Machining
Plastics have a variety of mechanical properties and a wide range of applications. China has the ability to process a variety of engineering plastics, from ABS and PEEK to ULTEM or PTFE, to meet exacting specifications.
5) CNC Wood Machining
CNC precision engraves hardwoods and softwoods for furniture, decoration, patterns, models, and more. China offers both imported and domestically produced wood, while utilizing 5-axis machines for complex woodworking needs.
15.Explore Advanced Technologies
In addition to basic CNC milling and turning, Chinese factories offer expertise in multi-axis machining, EDM, laser cutting, and more. These advanced technologies enable the machining of complex parts with tighter tolerances.
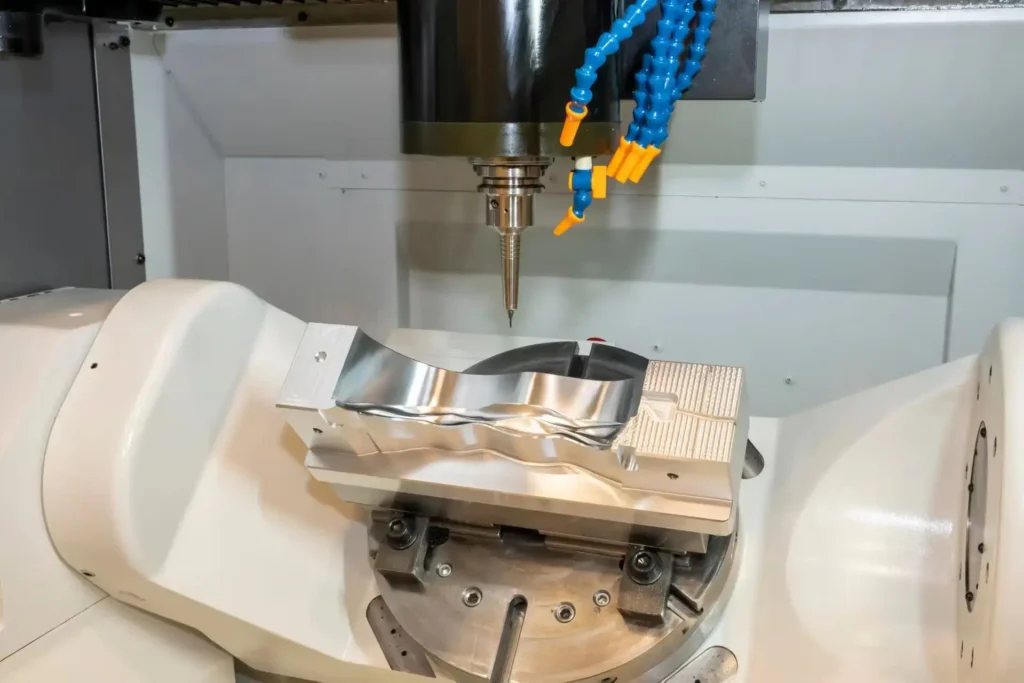
1) 5-Axis CNC Machining
5-axis CNC machining allows parts to be manipulated across multiple planes in a single setup. Faces can be precisely positioned for primary contours, complex 3D geometries, multi-faceted shapes, and spatial features.
2) CNC Turning
CNC turning produces rotationally symmetrical parts by removing material from the outside diameter or inside bore of a workpiece. High-precision diameters, inside and outside dimensions, and surface finishes can be achieved.
3) CNC Milling
CNC milling uses a rotating tool to precisely shape metal and other material workpieces by removing chips. Possess the ability to master tight tolerances, superior surface finish, and complex 3D features.
4) CNC Wire Cutting
Wire EDM uses an electrically charged wire to cut complex parts with a precision that is unmatched by traditional machining. Use special, hardened, or difficult-to-machine materials to make complex parts.
16.Industry-specific solutions
China’s strong manufacturing capabilities enable a wide range of industries to customize CNC machining solutions. By leveraging China’s infrastructure, expertise, and cost advantages, companies can optimize manufacturing to their specific needs.
1) Revolutionizing automotive CNC machining processes
The automotive industry relies on precision engineering components to optimize vehicle performance. China’s CNC manufacturing partners are able to produce prototypes and mass production of engine and drivetrain parts, interiors, exteriors, and more.
① Optimized performance parts
China’s investment in advanced CNC equipment and quality control has made optimized automotive parts production possible. This includes lightweight chassis and suspension components, turbochargers, transmission gears, and other complex components that improve efficiency and performance.
② Streamlining mass production
China’s CNC factories have a vast network of factories that offer streamlined production processes to produce large quantities of automotive parts. Strategic partnerships facilitate timely delivery of parts such as brake calipers, wheel hubs, pump housings, etc.
③ Customizable styles and brands
CNC processes excel at providing unique shapes and surface treatments to customize styling. Chinese partners offer customized grilles, trims, brand elements, wheels, etc. to match the unique styling of automakers.
2) Pioneering innovation in electronic CNC machining
China’s expertise in high-tech manufacturing meets the needs of the rapidly growing electronics industry for continuous innovation.
① Complex component manufacturing
Precision CNC machining capabilities shape the complex components that drive electronic innovation—heat sinks, housings, insulators, connectors, etc. At the same time, China also provides advanced 5-axis CNC equipment to handle increasingly complex problems.
② Proficient in multiple materials
Chinese factories have demonstrated their expertise in processing conductive, insulating, and specialty materials required to manufacture electronic components. This enables them to provide tailored solutions.
③Supporting the trend of miniaturization
With the demand for smaller and more powerful devices, CNC machining processes are able to produce miniature, high-precision electronic parts. China has strong manufacturing capabilities and is able to scale up micromachining technology. By leveraging China’s CNC capabilities for key industries, companies can obtain dedicated manufacturing solutions for their market segments. This can drive innovation and unlock value.
3) Achieving cutting-edge innovation in aerospace CNC machining
The development of the aerospace industry relies on breakthroughs in materials science and engineering technology. Chinese CNC machine tool factories are driving innovation in the aerospace industry through precision manufacturing.
①Lightweight and high-strength alloys
China’s expertise is suitable for machining lightweight alloys such as aluminum, magnesium, and titanium to improve strength and fuel efficiency. At the same time, 5-axis CNC milling can also shape complex aerospace components.
②Reliability and safety testing
CNC manufacturing partners support prototyping, simulation, and testing to ensure reliability. Chinese factories also assist in certifying compliance with aerospace standards.
③Customized engines and structural elements
CNC processes can efficiently produce engine casings, bulkheads, wings, and fuselages that meet specifications. China’s production capacity is suitable for small batch customized production for testing and optimization.
4) Simplify CNC machining of medical devices
Medical device manufacturing has strict quality requirements and biocompatibility needs. Chinese CNC factories can provide integrated solutions to meet unique needs.
① Biocompatible materials and surface treatment
Machining services provide medical-grade stainless steel, titanium and polymers to ensure body compatibility. At the same time, purity can be guaranteed through clean room and aseptic technology.
② High precision and high consistency
As medical devices become increasingly miniaturized and complex, CNC technology ensures strict tolerances for complexity, reliability and patient safety. China has invested heavily to meet growing expectations.
③ Comply with strict regulations
Chinese machinery factories assist in designing compliance, testing, auditing and certification in accordance with different global regulatory regimes, which undoubtedly speeds up the time to market. At the same time, CNC manufacturing solutions built for key vertical industries enable companies to focus on innovation, while China is responsible for efficient production. Therefore, establishing strategic partnerships with professional suppliers is the key to success.
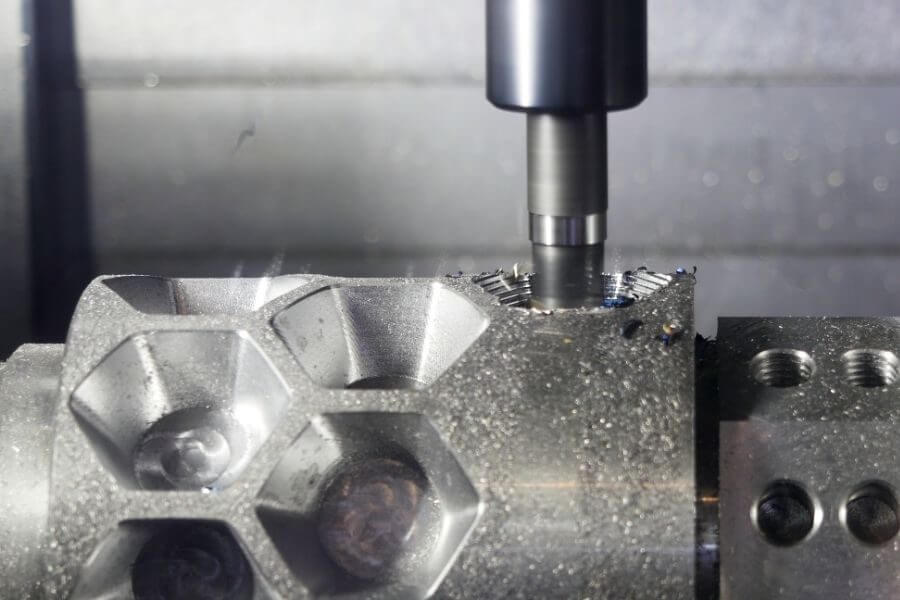
17.Optimize Your CNC Journey in China
Working with a Chinese CNC machine shop can unlock tremendous value, but it also comes with unique considerations. But by proactively addressing key areas and working closely with your supplier, you can set yourself up for project success.
1) Build Trust and Communication
Open communication and mutual understanding are the foundation for a strong partnership.
- Clarify specifications, timelines, quality requirements, and more in advance to avoid misunderstandings. Revisit these as needed.
- Implement regular communication channels, such as weekly conference calls or online project dashboards, to ensure transparency.
- Conduct factory visits and audits to directly observe operations, build relationships, and ensure consistency.
2) Embrace Quality Control and Assurance
Strong quality management is essential to ensure precision and consistency.
- Understand your supplier’s procedures and certifications (such as ISO standards) to assess their capabilities.
- Inspect parts at key production stages and implement incoming inspections to quickly identify any defects.
- Consider independent inspection services for unbiased assurance and expert technical evaluations.
3) Balance Cost and Efficiency
The best solution improves quality and reduces lead times without overspending.
- Negotiate win-win pricing that rewards suppliers for their efforts while controlling expenses.
- Explore bulk order discounts for high-volume projects to maximize savings.
- Optimize logistics and transportation by combining shipments to improve efficiency.
18.Addressing Common Concerns and Questions
1) Is CNC machining in China cheaper?
Compared to Western countries, CNC machining in China has a significant cost advantage, mainly due to lower labor, material and overhead costs. However, quality and communication must also be optimized to truly maximize savings. Because while price is the main inducement, resist the temptation to select suppliers based solely on cost. At the same time, vetting processes, expertise, certifications, and quality control procedures are equally important. Exceptional value and quality can be achieved through careful due diligence.
2) What are the risks of using a Chinese CNC machine shop?
If not managed properly, the main risks of using a Chinese CNC machining partner include:
- Communication barriers arising from language differences and cultural differences.
- Intellectual property issues involving unauthorized use of proprietary designs.
- Quality control issues due to lack of visibility or non-compliance with specifications.
Mitigating these risks requires selecting reputable suppliers that ensure safety protocols are in place, conduct thorough due diligence, and implement strong quality assurance procedures.
3) How can I ensure the quality of CNC machined parts imported from China?
Strategies to maximize quality with Chinese CNC machining partners include:
- Select suppliers with ISO certifications and mature quality management systems.
- Conduct factory audits and process reviews before finalizing selections.
- Provide extremely detailed specifications and drawings.
- Implement checkpoints during key production stages.
Although it takes extra effort, the rewards of high quality and cost savings are huge if best practices are followed.
4) What is the lead time for Chinese CNC machining?
Due to the high efficiency of the manufacturing system, the lead time for Chinese CNC machining is generally shorter than that of Western factories. However, considerations of part complexity, material availability, production planning, and shipping logistics can have a significant impact on timing. It is therefore critical to clearly communicate expectations for lead times and project timelines to suppliers. Be realistic about what can be achieved to avoid quality issues or delays due to excessive pressure.
5) How to communicate effectively with Chinese CNC machine shops?
The keys to effective communication with Chinese CNC machining shops include:
- Use clear, concise language in all technical specifications and communications.
- Hire bilingual translators or consultants to overcome language barriers when necessary.
- Establish multiple points of contact and a regular communication rhythm.
- Strive to gain a deep understanding of cultural differences in business interactions.
With patience and effort to adapt to language and cultural differences, excellent collaboration can be achieved.
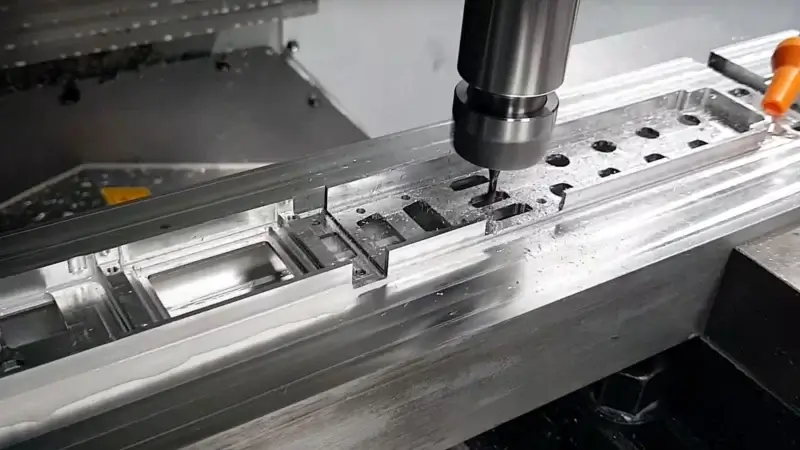
19.Optimizing Your Success – Best Practices for CNC Machining in China
Successful CNC machining in China requires optimizing communication, quality, and collaboration with suppliers. By implementing a few key best practices, you can ensure that your projects go smoothly.
1) Invest in Design for Manufacturability (DFM)
Carefully evaluating your product design can reveal opportunities for more efficient and cost-effective CNC machining.
- Simplify geometry to minimize complex machining steps.
- Standardize components to speed up production.
- Discuss design ideas with your machining partner early to improve manufacturability.
Small DFM adjustments can reduce material waste, tighten tolerances, and shorten production time.
2) Embrace Digital Collaboration
Remote communication and file sharing with overseas partners has never been easier.
- Use cloud platforms such as Dropbox for efficient file sharing and version control.
- Collaborate in real time through Skype, WhatsApp, or WeChat.
- Track project timelines, assign tasks, and collect data through project management software.
Digital tools pave the way for a transparent, streamlined, and well-documented CNC machining workflow.
4) Build a Long-Term Partnership
Finding a trusted CNC machining partner lays the foundation for current and future success.
- Take the time to properly vet potential suppliers.
- Cultivate open communication and cultural understanding.
- Negotiate long-term contracts to ensure better pricing and consistent quality across multiple projects.
By building a strong relationship with a Chinese CNC partner, you can rely on responsive service and support over the long term.
20.Reflect on key takeaways
China CNC machining has great potential in terms of cost savings, quality, and customization. However, finding the right partner is critical. Take the time to vet suppliers, optimize specs, and establish strong communication channels, and approach pricing negotiations and production timelines realistically. Once you find a reliable CNC shop, you can benefit from a wide range of materials, technologies, and industries.
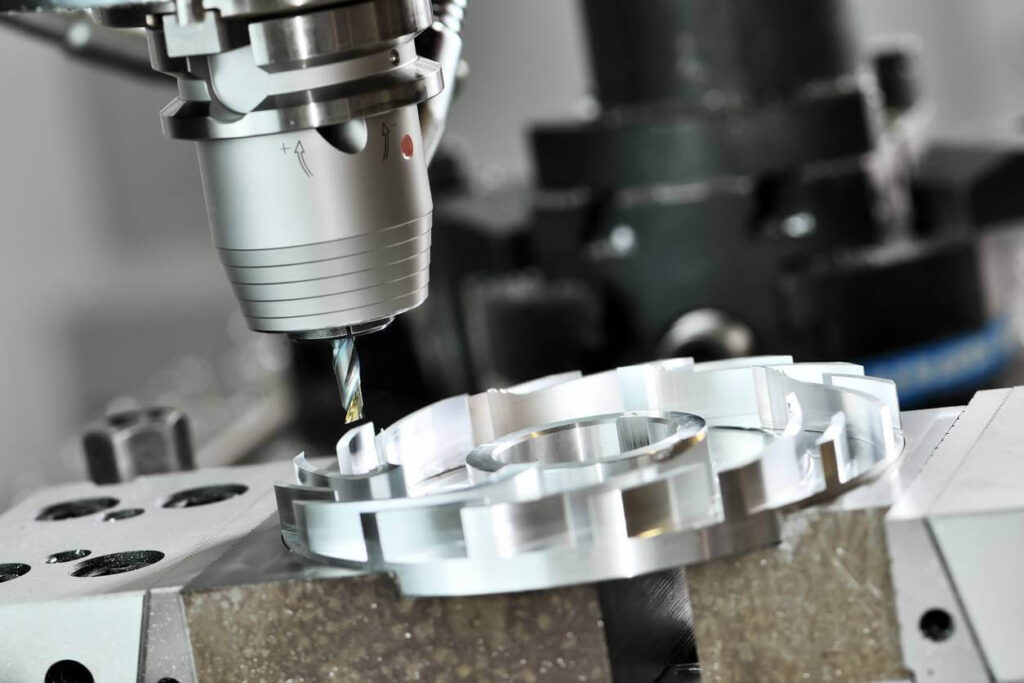
21.Implementing Best Practices
Follow best practices like DFM, digital collaboration, and long-term contracts. Reducing manufacturing inefficiencies saves money, while cloud tools enable real-time coordination. The mutual trust that comes with a lasting partnership ensures consistency. Regular quality checks and timely resolution of issues are necessary actions to maintain the practice.
22.Looking Ahead
While there are risks such as intellectual property theft, proper due diligence can minimize them. Weigh your priorities and risk tolerance when deciding between China or the United States for CNC machining. Overall, optimized processes, realistic expectations, proactive communication, and win-win relationships with suppliers pave the way for success in CNC machining in China.
23.Final Thoughts
China’s extensive manufacturing ecosystem offers tremendous CNC machining capabilities. However, realizing its full potential requires overcoming communication and cultural barriers. Patience, transparency, and collaboration allow us to tap into a wealth of skills and infrastructure. With the right approach, China can guarantee high-quality CNC machining at a competitive cost to meet a variety of needs.