Aerospace CNC Machining: Benefits, Applications, and Materials
The aerospace industry is a giant of modern technology and innovation that relies heavily on precision and efficiency. Key to achieving these attributes is CNC machining, a process that significantly improves the productivity of critical aerospace components.
This article introduces and explores how CNC machining is a part of the aerospace industry and a key element to its continued growth and success.
1.What is aerospace?
The aerospace industry covers a wide range of sectors, including commercial aviation, space exploration, and military applications, with a global market value of approximately $800 billion. In the United States, key stakeholders such as the Department of Defense and NASA are the main purchasers of aerospace components, which highlights the importance of the industry.
Aerospace manufacturing involves a wide range of technologies, from traditional casting and welding to advanced metal additive manufacturing processes. In between these two extremes is aerospace CNC machining, which is known for its precision and ability to innovate materials and design processes, which is essential to the dynamic needs of the industry.
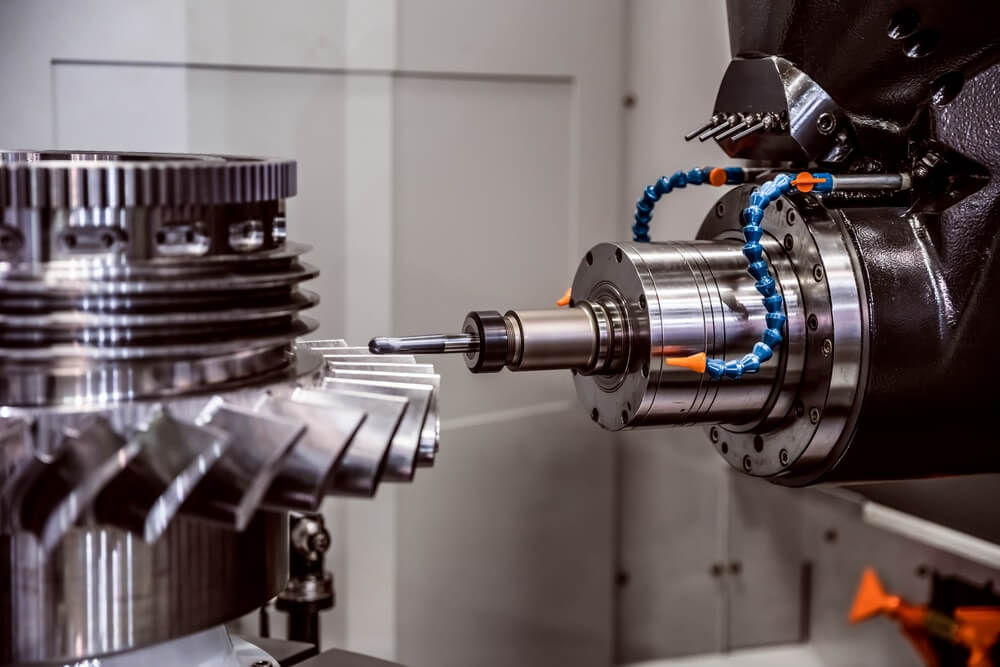
2.What is aerospace CNC machining?
Aerospace CNC machining is one of the many applications of CNC machining technology and is a specialized manufacturing technology. It combines advanced digital technology with precision engineering to produce critical components for the aerospace industry.
Since its introduction around 1942, CNC machining has played a major role in manufacturing critical aerospace components such as bulkheads and wing skins that require high precision and consistency.
The process involves removing material from a workpiece using a computer-controlled, powered cutting tool. Digital technology allows for the rapid and precise production of new parts.
Today, aerospace CNC machining processes have evolved to include a wide variety of components such as gearboxes, landing gear, and electrical components. The technology is also essential for adding detailed features to existing parts or engraving critical information such as serial numbers.
The precision requirements of the aerospace machining process are very demanding, especially for some components such as jet engines, which require tolerances as low as 4 microns, which is much tighter than standard CNC machining tolerances. Such components are often produced using high-quality 5-axis CNC machining centers, highlighting the role of the technology in producing end-use parts and prototyping for research and development. This dual capability ensures that CNC machining remains at the forefront of aerospace manufacturing, meeting both current production needs and future technological advances.
While many industries use CNC to manufacture parts and products, aerospace is one of the most delicate industries that cannot afford to make mistakes. In addition, manufacturers can achieve the same results using CNC machines, whether the production quantity is a single part or thousands of parts.
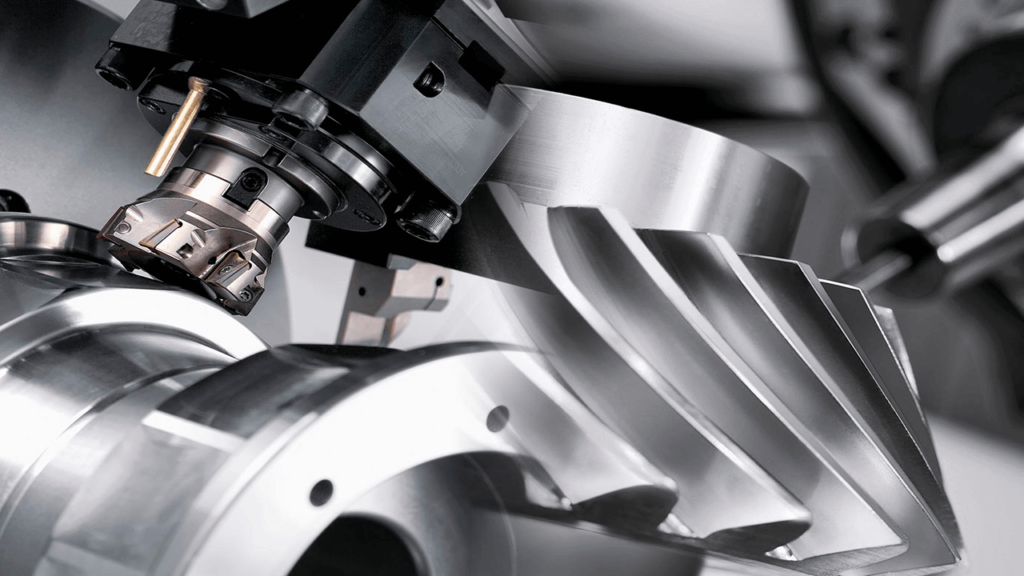
3.What Materials Are Used in Aerospace CNC Machining?
Aerospace CNC machining is a highly adaptable process. However, not all metals and plastics are suitable for manufacturing aerospace parts. Here are the materials used in aerospace machined parts:
1) Carbon Steel
Carbon steel is highly valued in aerospace machining for its versatility and strength. It is mainly used to manufacture structural components due to its high tensile strength and ability to withstand huge stresses without deformation.
The material’s robustness makes it ideal for manufacturing parts that are critical to the safety and stability of aerospace vehicles, such as landing gear assemblies and parts of aircraft frames.
2) Brass
Brass is another commonly used material in aerospace machining, especially for parts that require corrosion resistance and electrical conductivity. It is often chosen for electrical connectors, terminals, and housings in aerospace engineering.
Brass’ machinability allows for precise dimensions and clean surfaces, which are critical for precise and high-risk aerospace applications.
3) Bronze
Bronze stands out in aerospace CNC machining for its corrosion resistance and resistance to metal fatigue. These properties make it suitable for bearings, bushings, and similar components that are subject to considerable mechanical wear and need to maintain a long service life under harsh operating conditions.
Bronze’s durability and strength ensure that these components can withstand the rigors of aerospace operations without frequent replacement.
4) Copper
Copper is indispensable in the aerospace industry for its excellent thermal and electrical conductivity, making it a must-have material for cooling systems and electrical components.
In aerospace CNC machining, copper is often used in heat exchangers, wiring, and other heat-dissipating components that play a key role in maintaining the operational integrity of aerospace systems. Its efficient thermal conductivity helps manage the extreme temperature changes encountered during flight and space exploration missions.
5) Aluminum and aluminum alloys
Aluminum is one of the most commonly used metals in machining aerospace parts, mainly due to its high tensile strength and light weight. In addition, aluminum is very formable, which makes it easy to process with CNC machines.
The most popular aluminum alloy for CNC machining in the aerospace industry is 7075 aluminum, whose main alloying component is zinc. It has good fatigue strength. The material has been used to produce several wings, fuselages, and supporting structure components.
Aviation aluminum alloys 4047, 6951, and 6063 are also machined. Therefore, 6000 series alloys are generally considered easier to machine than other alloys.
6) Titanium and Titanium Alloys
Aerospace is the field that uses the most titanium alloys in the world. This metal is resistant to high temperatures, corrosion, and has a high strength-to-weight ratio. Therefore, the use of titanium in aerospace manufacturing has become very common.
Commercial and military aircraft such as the Airbus A380 and Boeing B787, as well as helicopters such as the F-22, F/A-18, and UH-60 Black Hawk require a large amount of titanium materials to manufacture various components. Fuselage and jet engine components are made of titanium, including discs, blades, shafts, and casings.
Since titanium is harder than aluminum, CNC machining of titanium can be more difficult, which often results in tool wear and heat buildup, which can cause the material to deform. Therefore, titanium aerospace machining requires running at lower machine speeds and higher chip loads.
7) Inconel
Inconel, especially Inconel 718, plays a vital role in aerospace machining due to its excellent heat resistance and high-temperature strength.
Developed by Specialty Metals, Inconel 718 is a nickel-chromium-based high-temperature alloy designed for demanding applications. It was originally used in jet engine diffuser housings for the Pratt & Whitney J58 engine, which powers iconic aircraft such as the Lockheed SR-71 Blackbird.
The properties of this alloy are also used in modern aerospace projects, including SpaceX’s Falcon 9 launch vehicle, where it is used in the engine manifold of the Merlin engine. Its use also extends to various aerospace components such as turbine blades, ductwork, and engine exhaust systems.
But machining Inconel 718 requires care to minimize work hardening; therefore, it is typically machined with slow but aggressive cutting, using hard tools to control its toughness and reduce tool wear. Despite these challenges, its excellent weldability and durability make it a top choice for aerospace applications, where reliability under extreme pressures and temperatures is critical.
8) Engineering Plastics
Plastics can be a valuable alternative to metals due to their extremely low weight, excellent impact and vibration resistance, strong sealing, and good chemical resistance. In addition, plastics have better electrical insulation than metals, making them ideal for prototype CNC machining. PEEK, polycarbonate, and Ultem are high-performance polymers used for aerospace machining.
Aerospace engineering plastics can be CNC machined to create aircraft parts such as cabin interiors, tray tables, wear pads, armrests, backlit instrument panels, valve components, housings, pipes, and insulation.
But not all engineering plastics are suitable for aerospace CNC machining, as aircraft polymers must comply with specific toxicity, smoke, and flame standards. So this is a crucial factor.
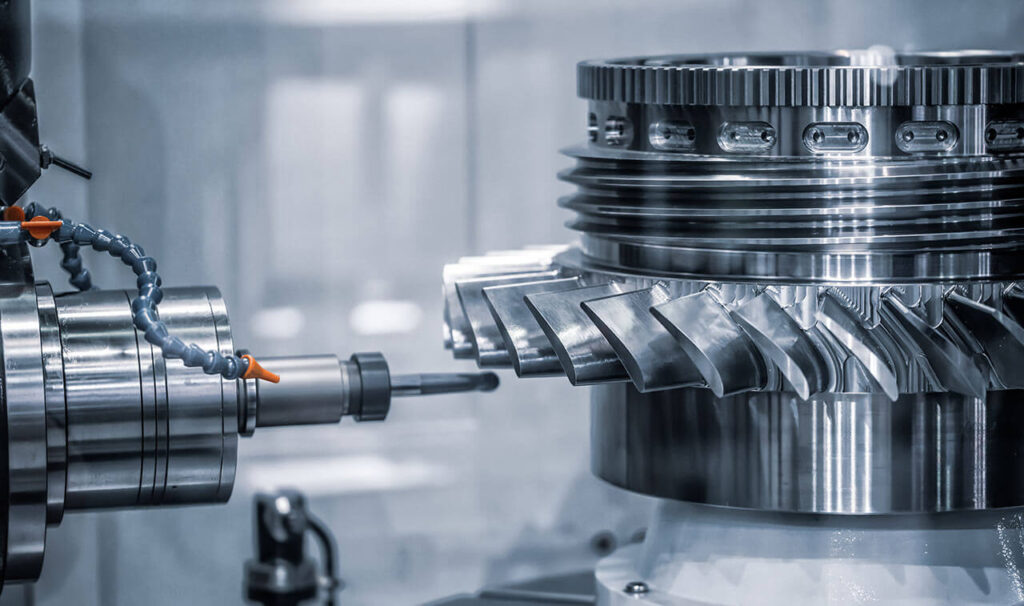
4.Advantages of CNC machining parts for aerospace
CNC machining has significantly improved the manufacturing process and enhanced the performance of aerospace parts. This section explores the many advantages of CNC machining, with a particular focus on its contribution to the manufacture of lightweight, error-free, and highly consistent components.
1) Lightweight components
One of the most significant advantages of CNC machining in the aerospace field is its ability to manufacture lightweight components. Aerospace engineers are also constantly seeking ways to reduce the weight of components to improve fuel efficiency and aircraft performance.
CNC machining can produce complex geometries that are not only strong but also much lighter than those made by traditional manufacturing methods. And by utilizing materials such as aluminum and titanium, which are known for their strength-to-weight ratio, CNC technology ensures that aerospace components are in optimal use without compromising durability.
2) Minimizing part errors
The inherent precision of the CNC machining process is essential to minimizing errors in the production process of aerospace parts. This is because advanced CNC machine tools have high repeatability and tight tolerances, which is critical in the aerospace field where every micron is critical.
This precision reduces the risk of part failure, thereby improving the safety and reliability of aerospace components. By automating the machining process, CNC technology also minimizes human error, ensuring that each part is produced to exact specifications.
3) Accuracy and Precision
CNC machining offers unparalleled accuracy and precision, which is indispensable in the aerospace industry. The ability to adhere to strict manufacturing standards and achieve tolerances accurate to a few microns makes CNC machining ideal for aerospace applications.
This level of precision is critical for components that must withstand extreme conditions and pressures to ensure they perform reliably in critical applications, such as in engines and structural components of spacecraft and aircraft.
4) Consistency
Another advantage of CNC machining is the consistency it brings to part production. Whether it is a single part or thousands of parts, CNC machines can produce each component with the same accuracy and specifications, reducing the variability that can affect the performance of aerospace parts.
This consistency is essential to maintaining the quality and reliability of different batches of parts, supporting the aerospace industry’s need for consistency in a high-volume production environment.
5) Efficiency
CNC machining stands out in the aerospace field because of its efficiency. Because the integration of CNC machines facilitates automation of the production process, allowing for continuous operation without the inconsistencies associated with manual labor. This not only speeds up the manufacturing cycle, but also maximizes the utilization of materials and resources.
The precision of CNC machinery ensures that each part is produced with minimal waste, thereby optimizing the use of precious materials such as titanium and aluminum alloys. This efficiency is critical in an industry where time and resource management directly affect financial and operational success.
6) Reduced Manufacturing Costs
The implementation of CNC machining in the aerospace manufacturing industry can significantly reduce costs. By automating many processes that are traditionally done by hand, CNC machines reduce the need for a large labor force, which is a significant expense in any industry.
In addition, the high precision of CNC machining minimizes material waste and reduces the incidence of errors that can result in costly rework or scrap. The ability to quickly and accurately produce parts also reduces time to market, further reducing overhead costs and increasing the profitability of aerospace manufacturing operations.
7) Achieve Complex Geometries
CNC machining is able to achieve complex geometries, which is particularly useful in the aerospace industry. Because aerospace components often require complex designs with precise dimensions and tolerances, which are difficult to achieve with traditional manufacturing methods.
CNC machines, especially those with 5-axis capabilities, can create detailed, complex shapes that meet the stringent requirements of aerospace parts. This capability allows for the design and production of more advanced and efficient aerospace systems, which helps to improve aircraft performance and functionality across the board.
8) Speed
Speed is another key benefit of CNC machining. CNC machining can produce parts significantly faster than traditional manufacturing methods, which is critical in an industry where meeting project deadlines can make or break an aerospace project.
The rapid production capabilities of CNC machines also speed up prototyping, allowing aerospace engineers to test and improve their designs more quickly. This speeds up development cycles and brings innovations to market faster, providing a competitive advantage in the rapidly evolving aerospace sector.
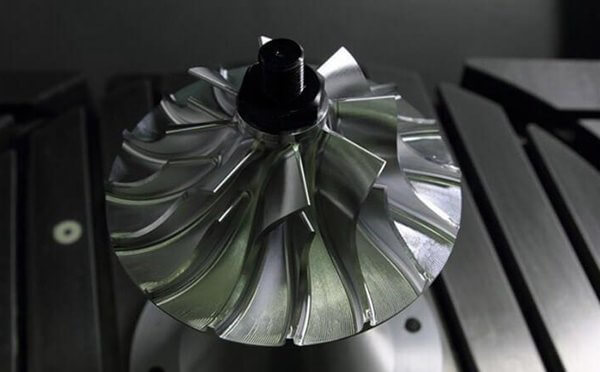
5.Aerospace CNC Machining Processes
CNC machining processes are an integral part of aerospace manufacturing, providing the precision and flexibility required to produce complex components that meet stringent industry standards. Let’s explore how different CNC machining processes are used in the aerospace sector and why they are particularly well suited to this field.
1) CNC Milling
CNC milling is a versatile process used extensively in the aerospace industry to manufacture complex parts such as fuselages, engine mounts, and aerospace prototypes. The process involves using a rotating multi-point cutting tool to remove material from the workpiece, resulting in precise shapes and details.
Capable of machining a wide range of materials, including aluminum alloys, titanium, and advanced composites, CNC milling is ideal for aerospace applications where lightweighting and strength are critical. Its precision allows for the production of parts with tight tolerances, which is essential for the safety and functionality of aerospace components.
2) CNC Turning
CNC turning is another technology used in the aerospace industry, particularly for the production of round or cylindrical parts such as shafts, pins, and bushings. The process involves a single-point cutting tool that runs parallel to the material being cut, allowing for high-precision machining.
The turning process is valued in the aerospace industry for its ability to achieve an excellent surface finish and meet the tight tolerances required for parts that must withstand high stresses and temperatures during flight.
3) CNC Drilling
CNC drilling is used to drill holes in aerospace components, which are often used to fix parts or hydraulic systems. The process uses a multi-point drill to accurately and efficiently drill holes into materials.
CNC drilling can be performed on flat or curved surfaces, making it highly adaptable to aerospace applications, where drilling precise holes is often critical to both the structural integrity and functionality of a part.
4) 5-axis CNC machining
What makes 5-axis CNC machining so popular in the aerospace manufacturing industry is its ability to machine the extremely complex geometries that modern aerospace designs often require. Unlike traditional 3-axis machining, 5-axis machines can rotate on two additional axes, allowing the cutting tool to approach the workpiece from any direction.
This capability reduces the need for multiple setups, increases productivity and significantly reduces machining time. At the same time, 5-axis CNC machining is particularly useful for parts such as turbine blades, fuselage components and wing panels, which require complex shapes and deep cuts with the highest precision.
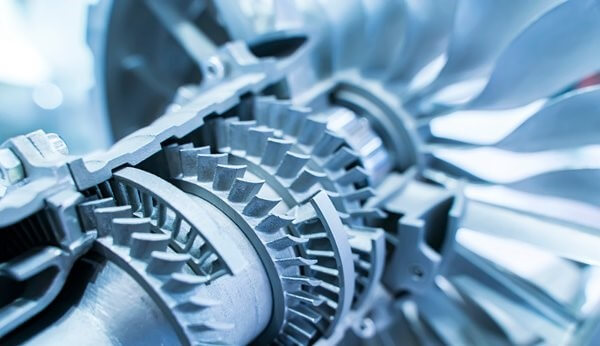
6.Typical Surface Treatments for CNC Aircraft Parts
Surface treatments for CNC machined aircraft parts are important to improve the durability, performance, and aesthetics of the parts. At the same time, these surface treatments also protect the parts from environmental factors and reduce wear. Here is an overview of 8 standard surface treatments used in aerospace machining.
1) Anodizing
Anodizing is a process that enhances corrosion and wear resistance by electrochemically converting the metal surface into a durable, corrosion-resistant anodized coating. This coating is particularly suitable for aluminum parts, and anodizing aluminum as a surface treatment can protect aerospace parts from corrosion and improve their resistance, helping aerospace parts withstand the harsh conditions of the aerospace environment.
This surface treatment requires immersing the aerospace part in an electrolyte solution to form a uniform oxide layer on the surface of the part.
There are two types of anodizing used for aerospace parts: Type II and Type III. Type II anodizing forms a decorative layer on the surface of the part. This layer is usually thin, causing the surface and aerospace parts to be susceptible to corrosion and wear when exposed. Type III anodizing, on the other hand, forms a more protective hard coating on the surface of the part.
2) Passivation
Passivation is a common post-processing method used in aerospace CNC machining to enhance the functionality and surface quality of the product. This is because after the machining process, the surface of the part may contain micro-roughness or surface impurities, which may negatively affect the performance of the part.
However, with passivation, these challenges are no longer an issue because the process improves the corrosion resistance of aerospace parts and reduces the need for maintenance.
3) Polishing
Polishing is one of the most suitable surface treatment methods for aerospace parts. It is a simple procedure that uses the principles of abrasion to make any surface smooth. The process usually starts with the roughest aerospace part surface and gradually progresses until a smooth, beautiful surface finish is left.
In addition, polishing can also improve the durability of aerospace materials. It does this by reducing the possibility of chipping or cracking. The disadvantage is that polishing aerospace parts takes a long time and is costly.
4) Powder coating
The most typical surface treatment for metal aerospace parts is powder coating, which is known for its functional versatility and durability. Powder coated aerospace parts are scratch-resistant and will not fade over time.
Additionally, this surface treatment offers a rich array of colors, giving aerospace part manufacturers greater flexibility and improved aesthetics.
5) Painting
Painting is used to coat aerospace parts with specific colors or protective layers. It is corrosion-resistant and solar-reflective, and can also be used to apply company colors or visibility markings that are critical to safety and branding.
6) Hard Coating
Hard coating is the application of a hard, durable film to a part substrate to improve wear resistance and service life. In the aerospace industry, this can mean a ceramic coating that also provides thermal insulation.
7) Thermal Spray Coating
Thermal spraying involves spraying molten or semi-molten material onto a surface to form a coating. The process is used to improve or restore the properties or dimensions of a surface, thereby extending the service life of aerospace parts by providing heat, corrosion, and wear protection.
8) Electroplating
Electroplating is the addition of a metallic coating to an object by applying a negative charge to it and then immersing it in a solution containing the metal salt to be deposited. The process is used in aerospace to improve conductivity, reflectivity, corrosion resistance, or reduce friction on a part.
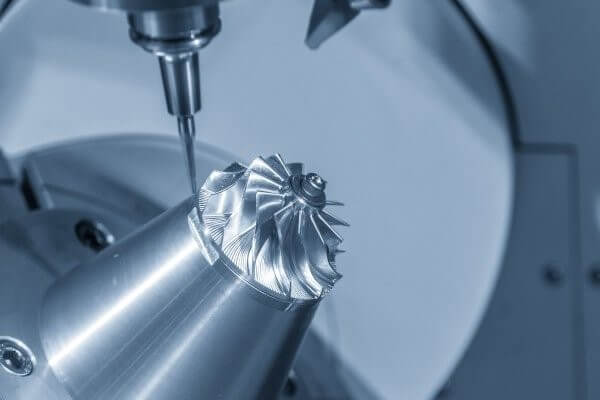
7.Tips to Know When Machining Aerospace Parts
Machining aerospace parts with CNC is a daunting task. However, here are a few tips to keep in mind during machining or before heading to an aerospace CNC machine shop.
1) Run a Simulation
Before actually producing an aerospace part, make sure everything is perfect from start to finish by utilizing CNC machining simulation software. With simulation software, you can visually understand how an aerospace part will work before you commit to production.
2) Use the Right Machine and Cutting Tools
There are a variety of CNC machines and cutting tools, but not all of them are suited to machining aerospace parts. That’s why it’s best to use the right tools and machines for the job. It’s usually best to scale up your equipment with a large, high-speed milling machine designed for the task.
3) Break Production into Specialized Sections
It can be daunting to think of a product as a whole, so it’s best to split up your production line. Split your production system into specialized sections based on the quality and components of your product. This helps streamline the production of aerospace parts when you choose the right equipment for the task at hand.
4) Commit to Proper Design
The design phase is one of the most important steps in product development. Proper machining design can save time required for workpiece preparation and improve productivity, efficiency and reliability.
8.Applications of Aerospace CNC Machining
Aerospace CNC machining plays an important role in various fields of the aerospace industry.
1) Rapid Prototyping
CNC machining plays an important role in the rapid prototyping of aerospace components. The process can quickly, accurately and cost-effectively produce parts to test form, fit and function. Engineers can also quickly iterate designs and make necessary adjustments based on test results, which is invaluable in high-risk industries where every detail is important.
Rapid prototyping not only speeds up the development process, but also improves the overall safety and functionality of aerospace systems by conducting thorough testing before mass production.
2) Aviation
In the aviation field, CNC machining is used to produce structural and non-structural components. From machining complex engine components that must withstand extreme conditions to accurately manufacturing flight control systems and landing gear, CNC technology achieves critical tight tolerances and high-quality surface finishes.
The reliability provided by advanced CNC machining processes supports critical safety requirements and helps maintain the stringent performance standards required for commercial, military and private aviation.
3) Space Travel and Exploration
The role of CNC machining is not limited to the atmosphere, but also extends to space travel and exploration. CNC machining is necessary to manufacture parts that can withstand the harsh conditions of space with extreme temperature fluctuations and radiation, and can be used to manufacture space shuttle components, satellite parts, and space station modules.
The precision and adaptability of CNC machining make it ideal for producing complex parts that are critical to the operation and success of missions beyond Earth.
4) Aerospace Mechanical Parts
Aerospace machining is responsible for many aerospace parts, from important titanium jet engine components to lightweight plastic interior cabin parts. Parts suitable for aerospace CNC machining are usually low-volume parts that require high strength and fine features.
The size of such parts is usually limited by the size of the CNC machining center, but a variety of different materials can be used, usually titanium or aluminum alloys. But there are other options, such as engineering plastics and composites. Some parts may only be post-processed after casting or extrusion.
Aerospace machining can be used for prototypes and end-use parts. However, end-use parts must meet strict safety standards and certifications.
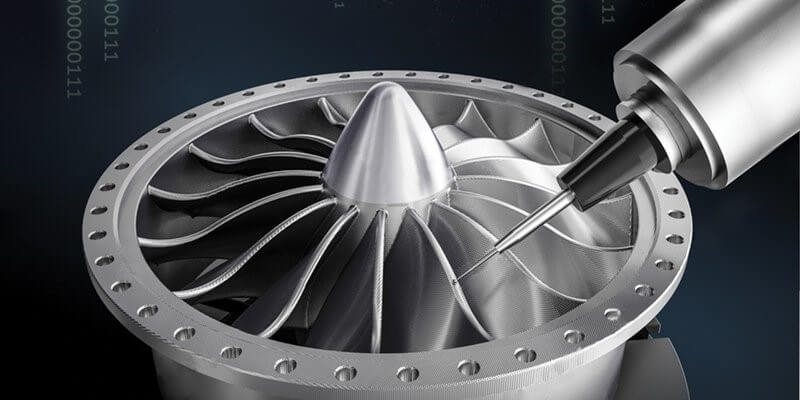
Machinable aerospace parts include, but are not limited to:
- Landing gear components
- Electrical connectors
- Valve components
- Oxygen generation components
- Shafts
- Turbine blades and other jet engine components
- Engine casings
- Oxygen generation systems
- Filter elements for liquid and air filtration systems
- Electrical connectors for electrical systems
- Motion control
- Actuators
- Fuselage components
- Wing ribs
- Optical discs
- Power transmission shafts
- Missile casings and other components
- Cabin components
- Seats, armrests and trays
9.How important is precision when CNC machining aerospace parts?
Precision in CNC machining of aerospace parts is not only a requirement, but also a fundamental aspect that determines the safety, performance and reliability of aerospace vehicles. Whether manufacturing structural components of aircraft or complex components of spacecraft, the margin of error is minimal.
1) Safety
Aerospace parts are critical to the safety of aircraft and their occupants. Because even the smallest deviation from the design specifications can lead to catastrophic failure. Precision machining ensures that parts meet exact dimensions and tolerances, which is essential to maintaining structural integrity and operational safety.
2) Performance
Aerospace vehicles operate under extreme conditions, and every component must perform its function perfectly. The precision of CNC machining ensures that components such as turbine blades, fuselage panels, and navigation instruments operate efficiently, thereby improving the overall performance of the aircraft or spacecraft.
3) Compliance with standards
The aerospace manufacturing industry is highly regulated and must adhere to international and national standards. Precision machining helps ensure that parts meet strict industry standards, such as those set by the Federal Aviation Administration (FAA) and the European Aviation Safety Agency (EASA).
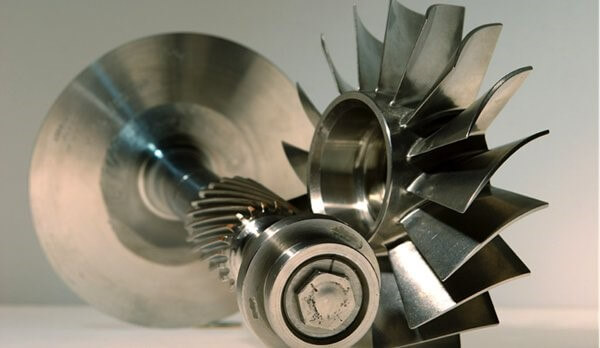
10.Tips for Optimizing CNC Machining Processes
1) Leverage Advanced CNC Machinery
The precision of aerospace parts can be significantly improved by using state-of-the-art CNC machinery with enhanced capabilities, such as 5-axis CNC machining. These machines allow complex shapes to be machined with fewer setups, reducing the risk of human error.
2) Choose the Right Cutting Tool
The choice of cutting tool has a profound impact on the precision of the final product. Tools designed specifically for aerospace materials such as titanium and high-strength alloys ensure better tolerances and surface finish.
3) Implementing Rigorous Quality Control Measures
Strict quality checks at every stage of the machining process help detect deviations early and prevent tolerance accumulation. Using advanced measurement and inspection systems such as coordinate measuring machines (CMMs) ensures that each part meets the required specifications.
4) Expert Programming for CNC Operations
Skilled CNC programmers play a vital role in machining precision parts. Detailed and accurate programming ensures that machine paths are optimized for specific materials and geometries, minimizing errors and material waste.
5) Regular Equipment Maintenance
Regular maintenance of CNC machines and tools prevents potential failures and avoids inaccurate machining of parts. Regular calibration and maintenance ensures that the machining process remains accurate and efficient.
6) Using Quality Materials
The quality of the raw materials used in aerospace machining has a significant impact on the results. Advanced metals and composites reduce problems such as tool wear and material deformation that can affect the accuracy of CNC machining.
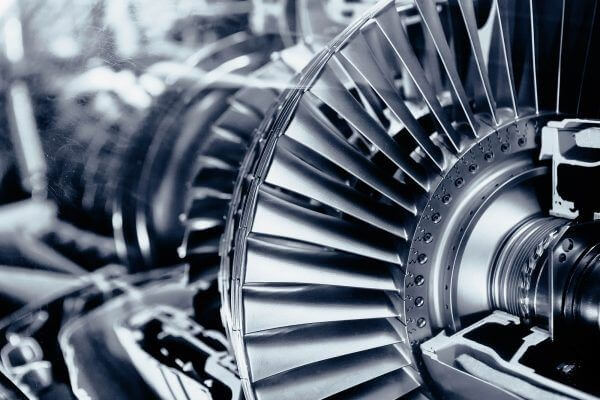
11.What does the future hold for aerospace CNC machining?
Technology is constantly evolving and innovating at an incredible rate. Aerospace manufacturers must keep up with these trends to compete. Several important trends are likely to drive the future of CNC machining in the aerospace industry:
1) Additive Manufacturing
Combining additive manufacturing (3D printing) with traditional CNC machining can produce complex parts with unique geometries that were previously impossible or too expensive to produce.
2) Smart Manufacturing
Industry 4.0 technologies, such as IoT devices, will allow real-time monitoring, data collection, and analysis during the CNC machining process. This will enable manufacturers to optimize operations, improve quality control, and reduce waste.
3) Digital Twins
Creating a digital replica of a physical CNC machine to analyze and optimize its performance is another technology that has received a lot of attention. This process can facilitate more efficient machine setup, preventive maintenance, and remote troubleshooting.