Process Types, Materials, and Requirements for Metal Parts Manufacturing
Metal parts fabrication plays a vital role in almost all industries when it comes to manufacturing mechanical components. These components are essential to ensure that machines and tools function as intended, and their demand continues to increase due to their durability and strength.
But how exactly do you fabricate metal parts? In this blog post, we will cover the three key considerations involved in the process of manufacturing metal parts, including material selection, manufacturing methods, and part requirements. And take a deep dive into the pros and cons of existing technologies and metals, as well as key points to keep in mind when choosing among metal part fabrication options.
1.What is Metal Parts Manufacturing?
Metal fabrication is a mix of different processes that focus on metal materials and produce products or final parts. It is systematic and starts with design, followed by a series of activities that end with a metal part or assembly that meets the preset requirements.
Metal fabrication processes include popular techniques such as joining, bending, cutting, and finishing. The professional use of these techniques produces a variety of products ranging from decorative parts to structural parts.
In a metal fabrication project, especially if it is a custom type, there are several steps that are crucial. These are product design, metal material selection, metal cutting, forming, joining, welding, and finishing.
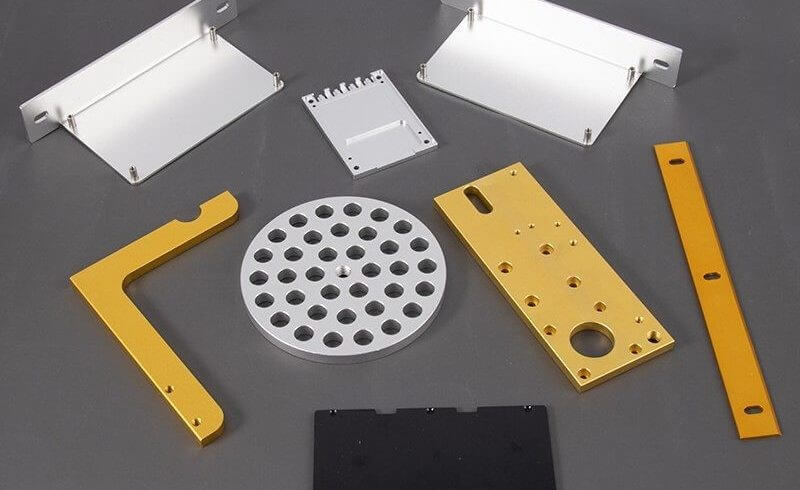
2.Types of Metal Materials
There are limitations on the different types of metal raw materials that can be used for metal part fabrication. Despite the wide range of choices, you will realize that some metals are more commonly used than others. This is because of the favorable characteristics and properties they have.
Manufacturers are influenced by many factors when choosing any particular metal material. It can be hardness, ductility, impact strength, corrosion resistance, etc. So each metal material has some or all of the characteristics that the manufacturer needs, or none of the characteristics that the manufacturer needs.
Now let’s look at a few categories of materials used in metal parts manufacturing:
1) Hard Metal
This is one of the two main classifications of metals used in metal parts manufacturing. This type of metal is known for its wear resistance and hardness. Due to its stacked atomic structure, hard metals can overcome deformation and heavy loads.
When shaped for tasks such as drilling and cutting, hard metals can maintain that shape. Here are some examples of cemented carbides:
① Steel
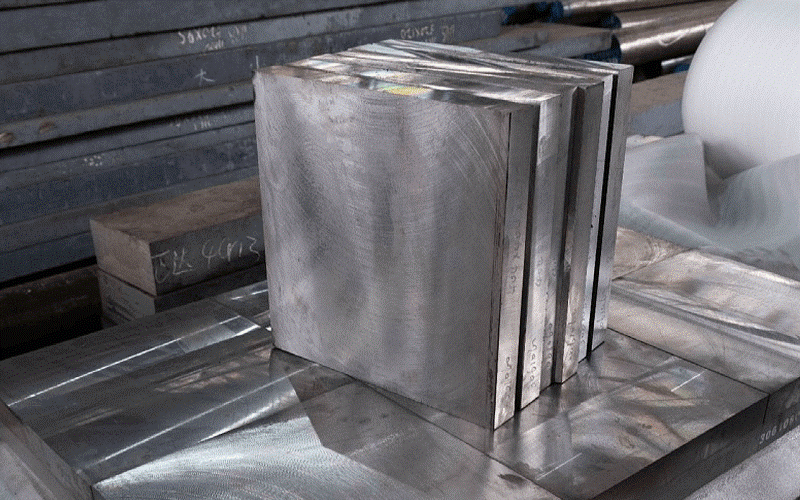
Steel is an alloy of different elements, including manganese, silicon, and carbon. Carbon exists in the form of iron carbide (Fe3C), which makes steel very strong and hard.
Depending on the carbon content, steel can be classified as low carbon steel, medium carbon steel, or high carbon steel. Low carbon steels such as mild steel have a carbon content of up to 0.25%. For medium carbon steel, the carbon content can be up to 0.55%. High carbon steels have a carbon content of up to 2.1%, which makes them relatively harder and stronger.
Steel can also be classified based on the manufacturing method, metal properties, and alloying elements contained. For example, the difference between cold-rolled steel and hot-rolled steel is the temperature level during processing.
② Stainless Steel
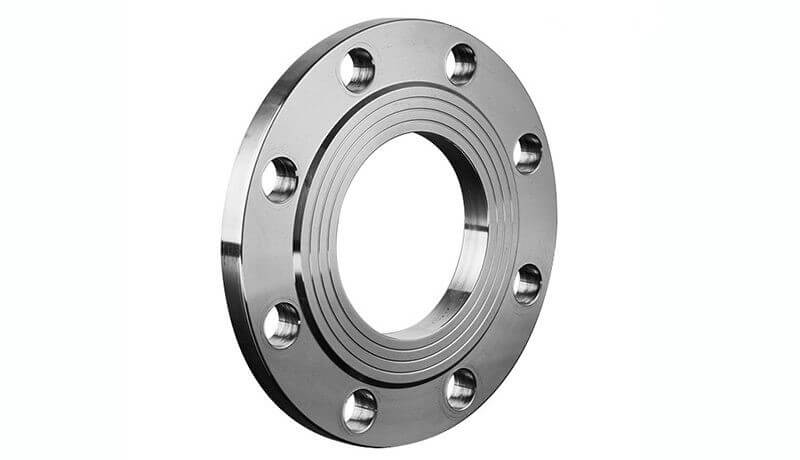
Stainless steel differs from steel in that steel is based on iron, while stainless steel contains chromium. At the same time, stainless steel also has a unique silver mirror coating.
Its easy-to-use characteristics are also the reason why many manufacturers use it for metal parts manufacturing. At the same time, stainless steel is also easy to weld and bend. Due to its chromium content, the metal is not easy to corrode, so it is suitable for projects that require corrosion resistance.
③ Inconel
Inconel is one of the strongest metals that can be used for metal parts manufacturing. It is particularly popular for its ability to operate in high-temperature environments. To better understand the strength of this metal, consider that the tensile strength of stainless steel is only 73.2 kilograms per square inch (KSI), while the tensile strength of Inconel is 160 KSI.
Consider using this metal for parts in jet engines, oil and gas equipment, and heat treatment equipment. This is because it performs well in rapid temperature changes, corrosive environments, and fatigue associated with the aerospace industry and similar industries.
④ Chromium Series
Chromium is a hard and brittle transition metal with a gray color. It is very corrosion resistant and does not react with the environment to form a chromium oxide layer on stainless steel.
The Mohs hardness of this metal is 8.5, which is even higher than the hardness of titanium. Given its strength and corrosion resistance, chromium is widely used in areas where beauty and durability are crucial. A good example is chrome plating.
⑤ Titanium
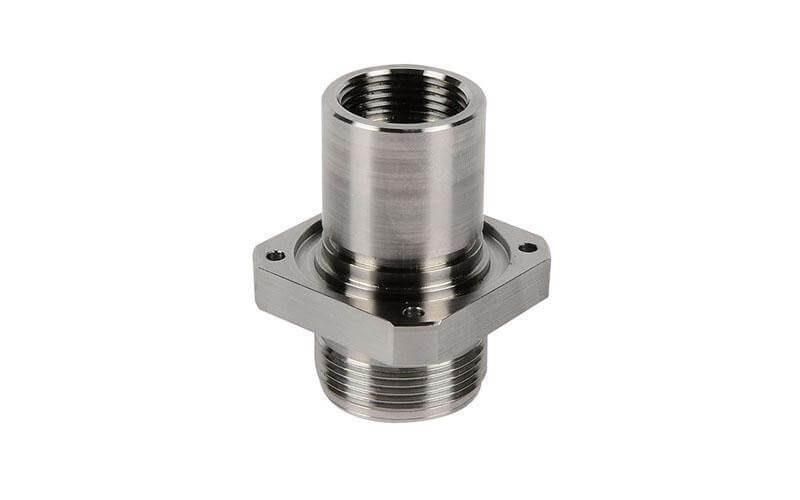
As one of the most abundant materials, titanium has perfect mechanical properties and is also popular in the metal parts manufacturing industry. Here are some of the properties of this metal with an atomic number of 22:
- High strength-to-density ratio
- Relatively high elasticity
- Corrosion resistance
- Low thermal expansion coefficient
2) Soft Metals
Metals with low melting points and can be easily formed, or molded into different shapes belong to the category of soft metals. Unlike hard metals with tightly packed atomic structures, atoms in this type of metal are easily manipulated, and ductility comes from loosely packed atomic structures.
① Aluminum
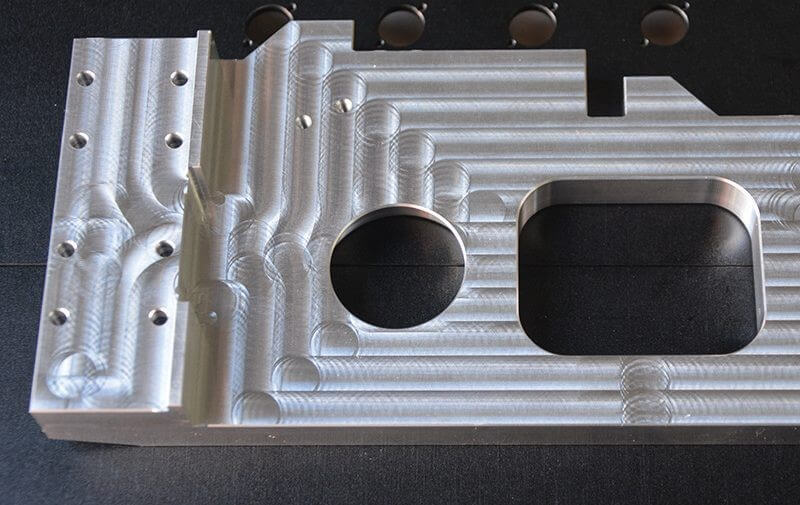
When a metal parts manufacturing project requires a combination of low weight and high strength, lightweight aluminum becomes a good choice. Industries seeking a high strength-to-weight ratio will rely heavily on aluminum materials, including the aerospace and automotive industries.
When you add the versatility, machinability, and thermal properties of certain aluminum alloys to the mix, it’s easy to understand why aluminum is one of the most popular metals for sheet metal parts, structural components, metal plates, and more.
② Magnesium
If there is a metal that is closely associated with low weight and fire risk, it’s magnesium. But in terms of strength-to-weight ratio, this metal is more practical than most die casting metals. It has a variety of alloys to choose from, and die casting tools have a long life.
Magnesium is also very versatile and suitable for both large and small casting projects. Due to its light weight, magnesium is suitable for many metal parts manufacturing projects that aluminum can be used. This is because the two have a lot in common. This metal is popular in the automotive industry and is used to make the following parts:
- Steering wheels
- Effectors
- Panels
- Brackets
Magnesium alloys are also used in the aerospace industry, such as helicopter gearboxes. The metal’s corrosion resistance and superior strength are evident in this area. Other applications include beverage cans, mechanical parts, desulfurizers in steel manufacturing, and cathodic protection in pipelines.
③ Brass
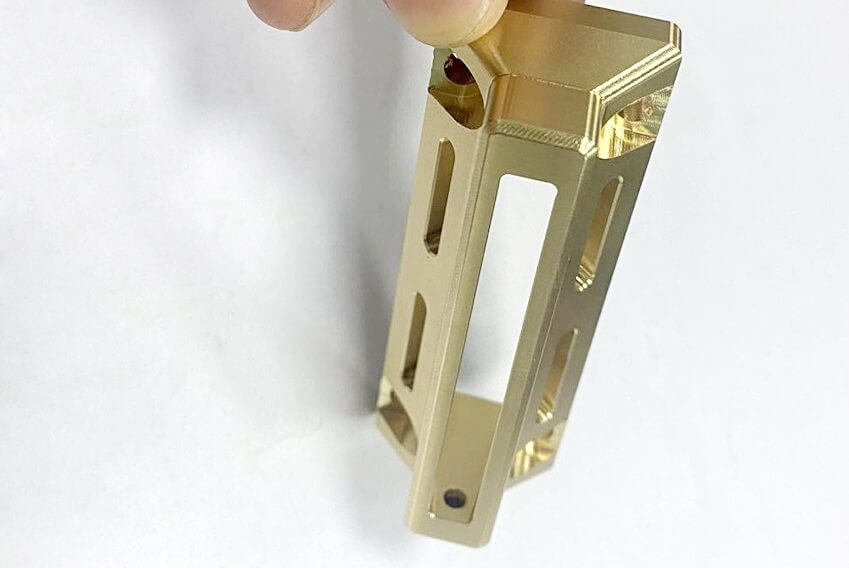
This metal is mainly composed of copper and zinc. The result of this combination is a ductile metal that melts at low temperatures.
The unique reddish-yellow hue of brass makes this metal a popular choice for decorative projects. In terms of antimicrobial properties, brass is found in medical parts that are often exposed to bacteria and diseases.
Like many other metals, brass can be processed to improve its chemical and physical properties, including corrosion resistance and strength.
④ Copper
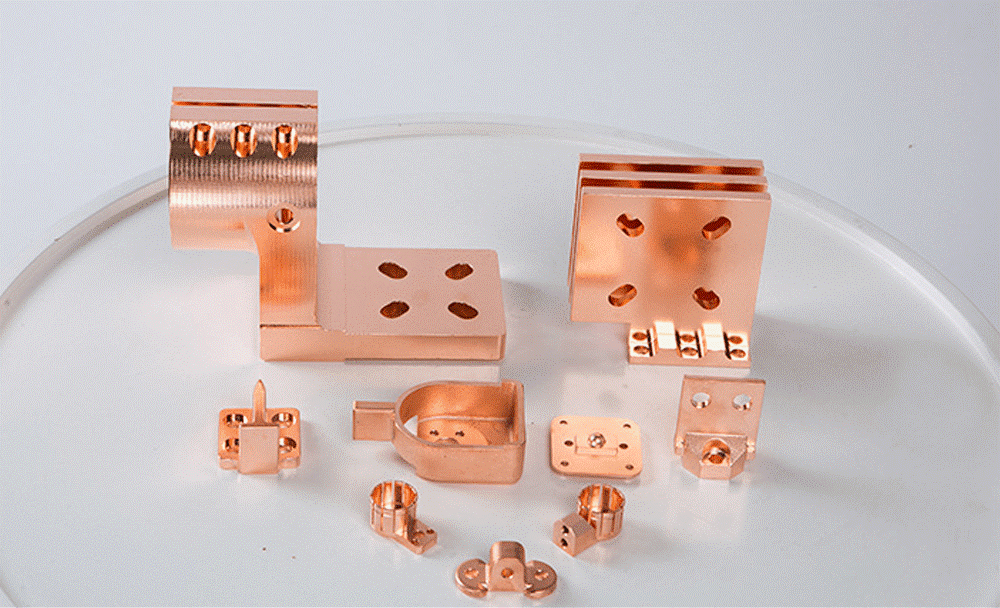
This naturally occurring metal is known for its use in metal parts manufacturing even in its raw state. You don’t need to obtain copper through subsequent steps to use it. It has some of the most important properties of metals, which are softness, ductility, and thermal conductivity.
Due to these properties, the metal is a common feature of electrical wires. Copper also plays an important role in the manufacture of industrial machinery. Brass and bronze alloys contain copper as one of their components.
3.Determine the Method for Metal Parts Manufacturing
Once the material has been selected, the next step is to manufacture the metal part. Manufacturing methods vary depending on the type of part to be produced, and there are many factors to consider when choosing the right method for a specific job.
Various manufacturing methods can produce different shapes and sizes to meet the required specifications. Some common methods of part manufacturing include precision sheet metal manufacturing, machining, joining, and welding.
Understanding the advantages and disadvantages of each method is essential to choosing which method is best for its specific application. Popular metal part manufacturing technologies include the following:
- CNC milling and turning
- Extrusion
- Casting
- Forging
- Metal injection molding
- Sheet metal and stamping
- Metal 3D printing
1) CNC Machining – Milling and Turning
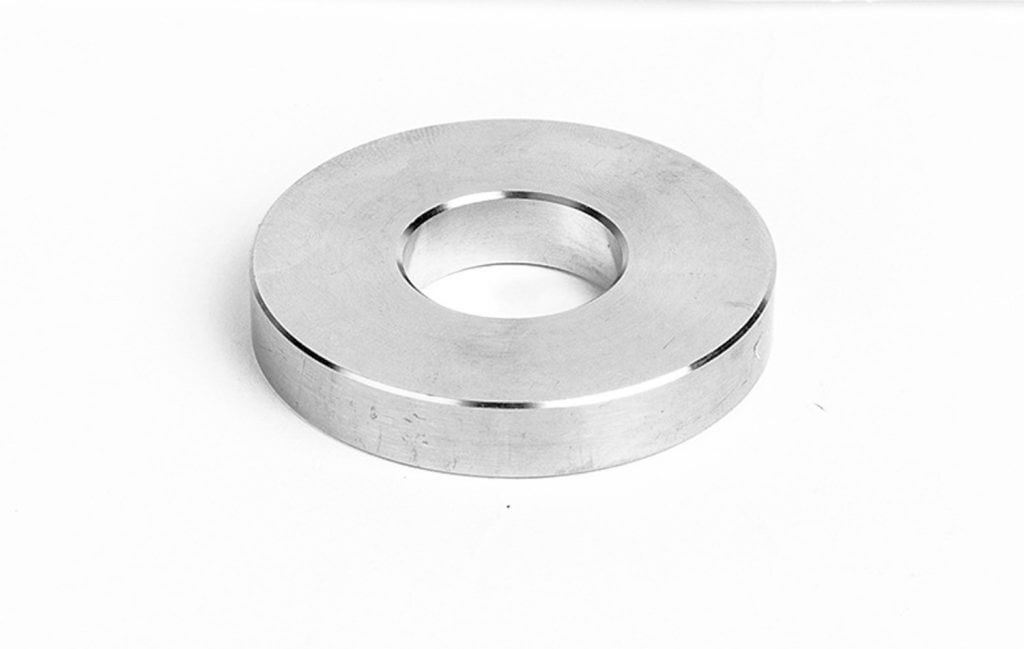
① Introduction to CNC Machining of Metal Parts
CNC milling and turning are metal part manufacturing processes that use CNC machine tools or CNC machining technology to remove material from metal parts. In addition to milling and turning, another popular machining process is drilling.
Milling methods can be used to remove excess material from the parent metal material by incorporating a multi-point cutting tool into the CNC machining setup.
CNC milling and turning are relatively new methods. The older methods were manual, but the concept is the same. Typically, milling is a secondary metal fabrication process.
Turning produces cylindrical metal parts and is done on lathes. Lathes are equipped with single-point cutting tools that remove material from the rotating metal. CNC lathes are a recent development, but manual turning processes are still an option. Turning using CNC machining methods is preferable for many things, including greater accuracy of results.
CNC milling and turning are better suited for manufacturing metal parts with high dimensional tolerances and operating speeds. The versatility of CNC machining and the fact that it can run continuously for 24 hours are significant advantages.
Unfortunately, CNC machining through milling and turning has size limitations and is costly, which can hinder the manufacturing of metal parts with this technology.
②Application of CNC Machining Metal Parts
CNC turning and milling metal parts are used in almost every industry in the world today. These parts are the workhorse of modern industry.
With CNC turning, the automotive, telecommunications, electrical, mechanical and electronic industries produce a wide range of parts. For example, CNC turning helps to make bushings, shafts, pins, rods, gearboxes and heads.
CNC milling is also a well-known machining operation in metal manufacturing. Aerospace, car models, medical parts and any metal parts you can think of can be made by CNC milling.
2) Extrusion: Pushing Metal into A Die
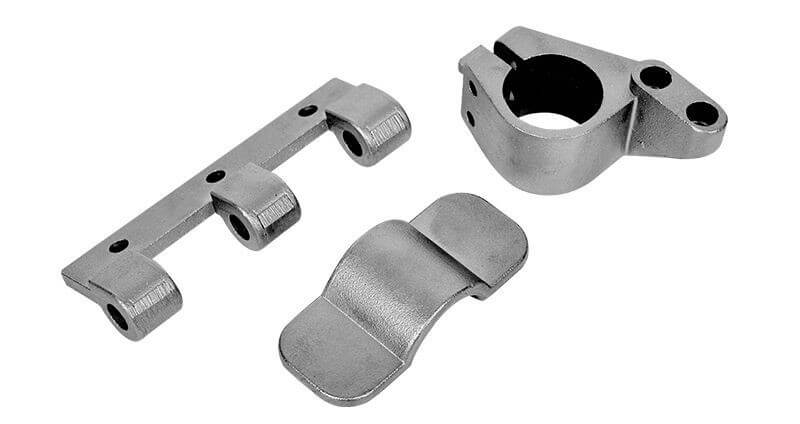
①Introduction to Extruded Metal Parts
The process involves pushing heated metal into a die, which then forms the metal into a tubular or L-shape. With this technology, metal can be constructed into more complex shapes.
But usually metal parts produced by extrusion require post-processing such as drilling, cutting and machining. This is an ideal process that requires a constant cross-section.
Hot extrusion can produce larger parts and extreme complexity. In contrast, cold extrusion can produce smaller parts with less complexity.
During this process, a cylindrical bullet is forced to flow through a closed cavity that has a die with the desired cross-section. These cross-sections shape the metal part and are pressed out with a hydraulic or mechanical press. The metal part has the desired shape.
Extrusion includes three different types of operations: hot extrusion, cold extrusion, and friction. Hot extrusion is performed at high temperatures to prevent the material from hardening. Cold extrusion involves room temperature because the material may be less oxidized, have tighter tolerances, and higher strength. Finally, the friction process requires force to push the material toward the die.
② Application of Extruded Metal Parts
Extrusion provides a smooth surface for paint and finishes. This property makes it ideal for cosmetics and precision parts. The aerospace and automotive industries use this process for their parts. At the same time, it is also suitable for window, railing, and floor applications.
3) Casting: A Manufacturing Process with A Long History
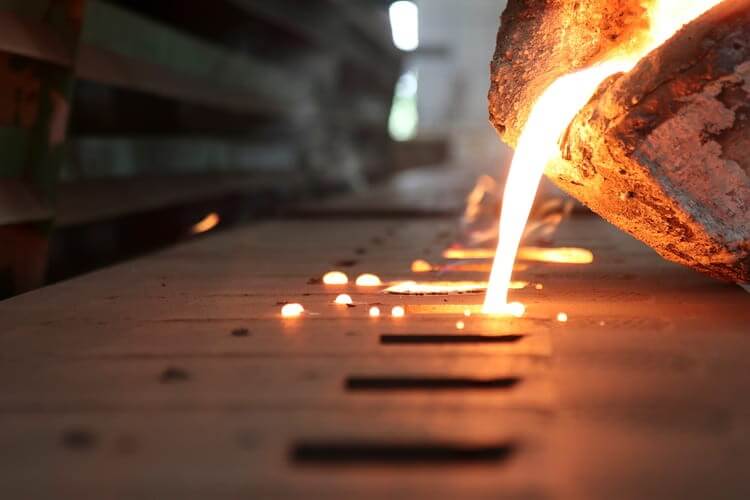
① Introduction to Cast Metal Parts
It is one of the most flexible metal parts manufacturing processes. Casting is ideal for a variety of complex shaped metal structures. It can be said that this is an economical solution to metal manufacturing problems that otherwise require multiple methods to solve.
The process pours liquid material into a mold, which is a prefabricated cavity of the desired structure. It can then cool the material and solidify, and then eject from the mold to obtain the cast metal part.
There are two well-known casting methods. Let’s take a look at each one separately.
- Investment Casting: Investment casting uses a wax model of the final product. The wax is coated with ceramic, and once the ceramic hardens, the wax is heated and ejected. The hardened ceramic shell becomes the mold of the desired metal part. The molten metal is poured into the mold, cooled and separated from the mold. This process ensures the production of fine and complex parts. Investment casting can meet the needs of small batch production.
- Die Casting: This process uses hydraulic pressure to press liquid metal into a mold. The steel mold is manufactured in a way that can produce complex shapes, ensuring repeatability and accuracy as well as effectiveness. Therefore, die casting is suitable for large-scale production of small and medium-sized castings with extremely high complexity.
② Application of Casting Metal Parts
This process is able to manufacture almost all commercially manufactured mechanical equipment today. In addition, in terms of production, casting is superior to CNC machining in terms of cost and other aspects. Therefore, this metal manufacturing method often manufactures washing machines, metal pipes and automotive parts.
4) Forging: Shaping Metal
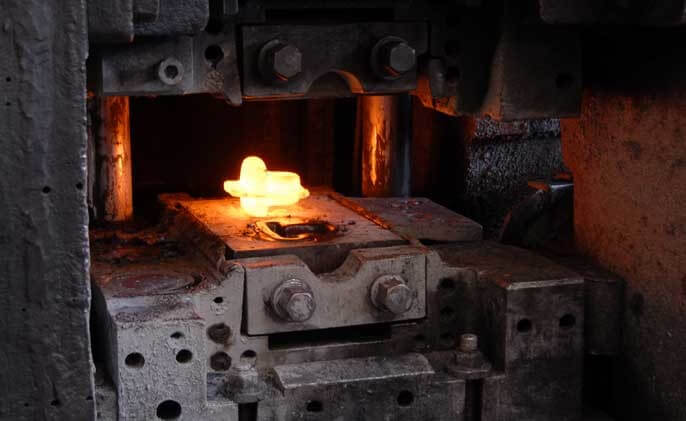
① Introduction to Forged Metal Parts
This is a manufacturing process that uses localized compressive forces to shape metal. In short, it is the process of heating and shaping metal.
In addition, it is a popular automated industrial process. The weight of forged parts ranges from a few kilograms to a hundred metric tons. Modern industry uses high-impact forging machines to shape metal into ideal structures.
Forging produces stronger metal parts than casting and machining. This process is economical and produces less waste.
It is a simple process that includes five steps, namely heating, machining, forging, cooling and finishing. In addition, this process does not require reducing the metal in a liquid, and only heating the metal to a forgeable state is sufficient for forging, making the metal parts stronger.
② Application of Forged Metal Parts
Forged metal parts are needed in various industries around the world. The automotive industry uses these parts to withstand impact and pressure, such as wheel spindles, kingpins, shafts, torsion balls, etc. These parts can also be used in surgical instruments, electrical transmissions, household hardware, and general industrial equipment.
5) Metal Injection Molding: Mass Production Process
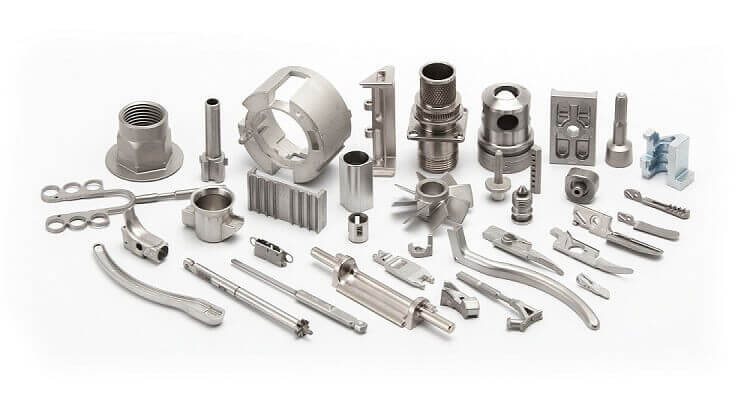
① Introduction to Injection Molded Metal Parts
The application of plastic injection molding methods to metal parts manufacturing is called metal injection molding (MIM). This technology introduces the automation and simplicity of plastic manufacturing to metal manufacturing. It is capable of producing metal parts with tight tolerances and complex shapes.
② Application of Injection Molded Metal Parts
This process is an innovative technology in the field of metal parts manufacturing, capable of mass and stable production of complex parts. Many parts in the automotive industry are produced using this technology.
This manufacturing process can also be used to manufacture many other products such as aircraft, medical equipment, accessories, decorations, computers, office supplies and home appliance parts.
It is worth noting that plastic injection molding technology is also a very effective method for manufacturing medical equipment.
6) Sheet Metal Stamping: Cutting and Bending Parts
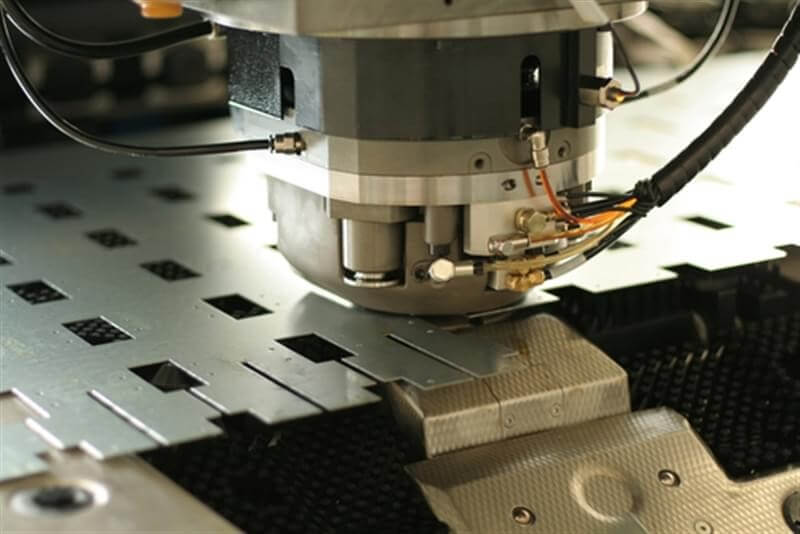
① Introduction to Sheet Metal Stamping Metal Parts
Sheet metal stamping is characterized by the use of a punch consisting of a die and tool to apply pressure to a metal sheet to obtain the desired shape. The result is the formation of a new shape or the removal of a piece of metal from the sheet.
This sheet metal manufacturing technology is suitable for situations where smaller parts, larger volumes, repeatable sizes and complex shapes are required.
Sheet metal stamping is common in the manufacture of electrical appliances, electrical components, fasteners, and building equipment. You’ll find such components in automotive engines, aircraft parts, telecommunications products, and electronics.
For custom sheet metal stamping, cost challenges can be a barrier, especially when preparing dies for sheet metal parts.
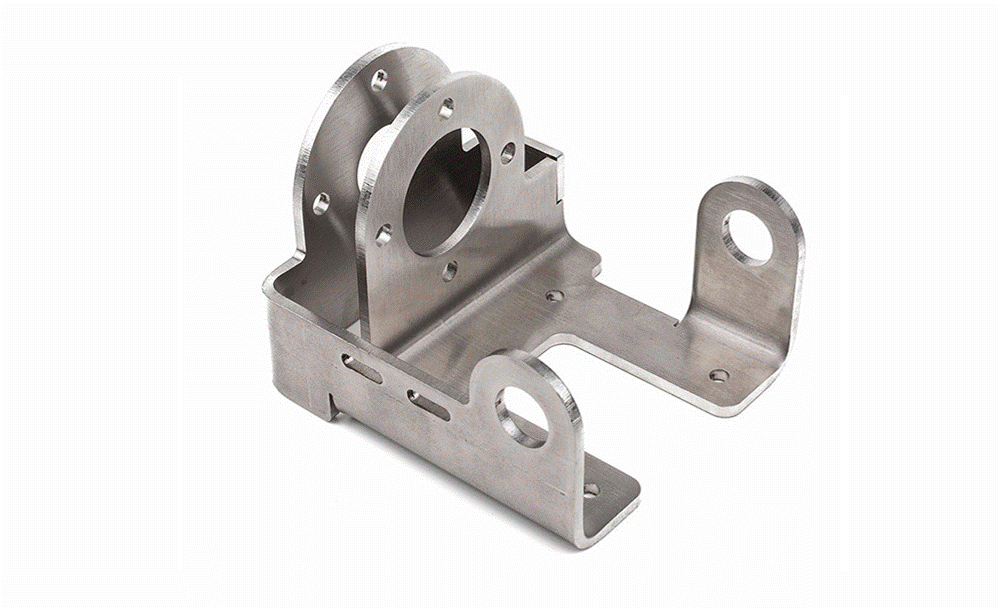
② Applications of Stamped Metal Parts
Stamping is a process used by the electronics, appliance, and automotive industries to manufacture millions of parts each year. This method is suitable for manufacturing high-volume functional parts such as housings, brackets, and chassis. It is also the best choice for the robotics industry.
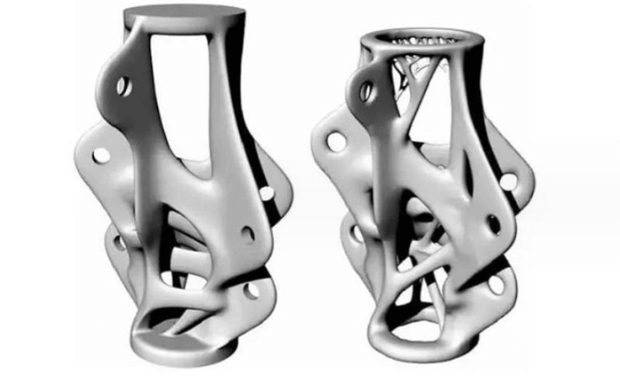
7) Metal 3D Printing: Complex Geometries and Small Batch Parts
① Introduction to Metal 3D Printing Metal Parts
Metal 3D printing for metal part manufacturing exists. This is an additive manufacturing process in which metal is deposited in a precise form to create metal parts.
Some metals that can be turned into powder and used in 3D printing technology are tungsten, aluminum, copper, and cobalt-chromium alloys. Others are nickel-based alloys, steel, and stainless steel.
The media and methods used by various metal 3D printing may vary, but there are two elements in common: metal in powder form and a high-energy-based printing process.
Such metal part manufacturing technologies include EBM (electron beam melting), direct metal laser sintering (DMLS), and (selective laser melting). Less commonly used methods are binder jetting, metal injection molding, and laser metal deposition (LMD).
Manufacturers looking for the most complex metal parts should consider metal 3D printing. For example, cooling channels and other complex internal shapes can be perfectly realized with this metal part manufacturing technology. The method rarely produces waste and has high reliability.
Please note that the risk of hazardous substances produced during metal 3D printing is very common. Metal powders may enter wounds or eyes and cause serious health problems. Carbon monoxide and other harmful gases are produced. Fires caused by metal powders are also a hazard.
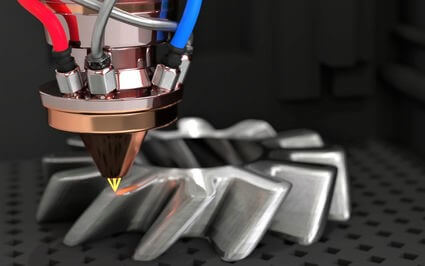
② Applications of 3D Printed Metal Parts
Metal 3D printing can quickly and cheaply manufacture a variety of industrial parts. However, it is best known for the large-scale production of customized tools and small-batch production of specialized instruments.
Therefore, the technology is an excellent way to produce fully functional prototypes, rigid housings, piping systems, spare parts, production tools, surgical and dental implants, jewelry and decorations, and many other components into different modern industries.
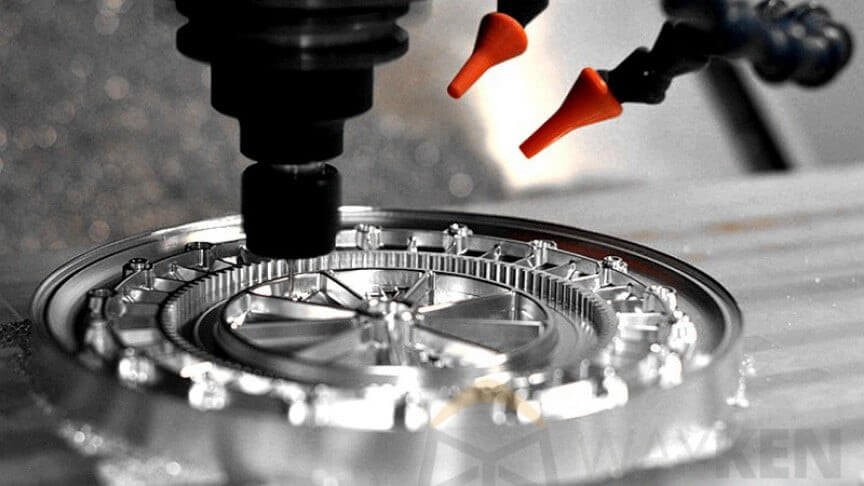
4.Understanding the Requirements of Metal Part Manufacturing
When it comes to manufacturing metal parts, some parts are more difficult to produce than others. Simple parts can be manufactured in a traditional machine shop using standard equipment and tools.
However, custom parts with special requirements may require more complex machinery and expertise. In addition to special needs, custom parts may also require additional post-processing treatments such as surface treatment and heat treatment.
1) Surface Treatment Options for Metal Part Manufacturing
This is the last process in the manufacturing operation. Surface treatment provides environmental protection and aesthetics to the parts manufactured from metal. In addition, the process also improves properties such as surface roughness and corrosion resistance that are beyond the capabilities of machining operations.
In addition to this, some treatments can also improve the mechanical and electrical properties of metal parts. Mentioned below are some of the surface treatment options for metal parts.
- Electroplating
- Chemical Plating
- Anodizing
- Chemical Treatment
- Vacuum Plating
- Hot Dip Galvanizing
- Painting
- Thermal Spraying
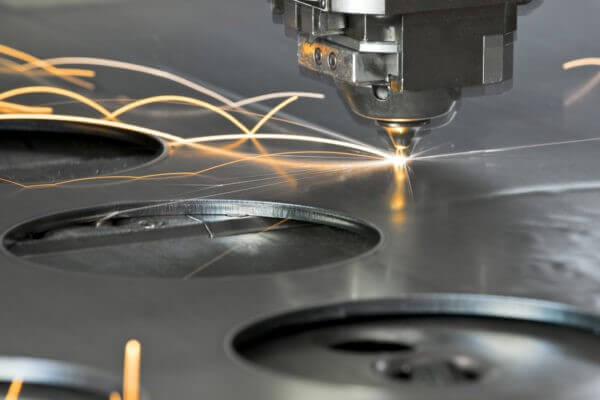
5.Xavier Helps with Custom Metal Parts
If your part features complex geometric tolerances, tight quality requirements, large overall dimensions, or tight process controls, it’s best to work with a professional metal fabricator with experience in manufacturing complex components.
Professional metal fabricators have the expertise and equipment to produce unique parts to the required specifications, no matter how complex the part.
Metal part manufacturing is a complex process that involves many different considerations. If you’re looking for a reliable and efficient way to manufacture metal parts, look no further than Xavier.
Whether it’s a medical or aerospace-grade component, or a general component that requires high quality standards such as complex geometric tolerances and tight quality requirements, Xavier delivers an exceptional end result.
From selecting the best material for your part to the manufacturing process itself, our team of experts will take the uncertainty out of the complexities of metal part manufacturing, working closely with you every step of the way.
10 Comments
Hi there, I enjoy readng all of ypur aticle post.
I lie to write a little comment tto support you.
Heya i’m ffor thee primary time here. I foundd
this board andd I in finding It reallyy useful & iit hewlped mee out much.
I aam hoping to offer one thin agzin aand hellp oters like yyou helpedd
me.
Usually I don’t rea article oon blogs, but I wish tto say that tnis
write-up very compelled mee to ttry annd ddo so!
Yoour writing tasste hass been surprised me. Thanks, quite
great article.
whoah this blog is fantastic i really like studying your posts.
Stay up the good work! You realize, many people are hunting around for this info, you could help
them greatly.
It’s very straightforward to find out any matter on web as compared to textbooks,
as I found this piece of writing at this web site.
Hi to every body, it’s my first go to see of this website; this website carries awesome
and actually excellent information for visitors.
Ahaa, its fastidious dialogue regarding this piece of writing here at
this web site, I have read all that, so at this time me also commenting
at this place.
I’m amazed, I have to admit. Rarely do I come across
a blog that’s both equally educative and amusing, and let me tell
you, you’ve hit the nail on the head. The problem is something which too few people are speaking intelligently about.
Now i’m very happy I found this in my hunt for something
concerning this.
I just like the valuable information you provide on your articles.
I’ll bookmark your blog and check again here frequently.
I’m quite sure I will learn many new stuff proper right here!
Best of luck for the following!
Thank you for sharing your info. I really appreciate your efforts and I will
be waiting for your next write ups thank you once again.