Learn How Custom Auto Parts Manufacturing Works
The automotive parts manufacturing process involves a wide range of operations including the design, development, marketing, sale, repair, and modification of different internal components used in motor vehicles, which can be observed through machining pictures. SMT machining has certain strengths in the field of custom motorcycle wheels, parts and accessories.Meanwhile, Global Gear & Machining LLC’s business scope includes the manufacturing of motor vehicle parts and accessories.
The automotive industry is one of the most prominent industries in the world and accounts for a significant share of global economic revenue. The industry is known for its mechanical technological advancements and continues to improve over time.
Custom auto parts manufacturing plays a key role in vehicles when it comes to upgrading and has a huge advantage for hybrid conversions.
Moreover, it enables vehicles to operate at optimal efficiency with just a few adjustments to the internal components. These additional features make custom auto parts manufacturing a top choice for most customers due to their versatility and durability in the global market.
This article will discuss custom auto parts manufacturing in detail, focusing on its benefits and workflow.
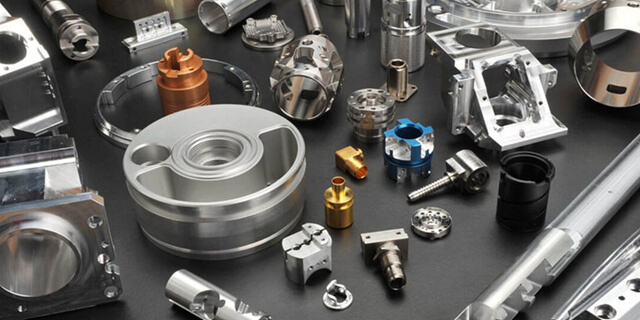
1.What is custom auto parts manufacturing?
As the name suggests, custom auto parts manufacturing is the process of manufacturing high-quality parts that take the efficiency of motor vehicles to the next level.
Custom auto parts manufacturing involves the use of different materials and techniques to produce components such as fasteners, shock absorbers, gaskets, seals, and accessories.
Many car manufacturers have associations with other companies that manufacture these custom parts. Customization is a key aspect as each manufacturer orders parts that meet their standards.
Custom auto parts manufacturing also has many protocols to follow. For example, compatibility with a specific vehicle, durability, and efficiency. All of these aspects are directly dependent on the type of machining solution and the type of material used in manufacturing.
2.Processing Technologies for Auto Parts Manufacturing
When it comes to custom auto parts manufacturing, various technologies can be used to manufacture different auto parts, such as CNC machining, additive manufacturing, injection molding, and metal stamping, among others.
Let’s take a closer look at the commonly used machining technologies in auto parts manufacturing:
1) Injection Molding
Injection molding is a technology widely used in the automotive industry to produce a variety of plastic parts such as interior trims, dashboards, door handles, bumpers, and exterior body parts such as grilles and dashboards.
Injection molding has advantages for auto parts manufacturing because it can produce a large number of parts with complex geometries and tight tolerances at a relatively low unit cost.
In addition, it offers design flexibility, with the ability to integrate features such as ribs, bosses, and complex textures directly into the part design.
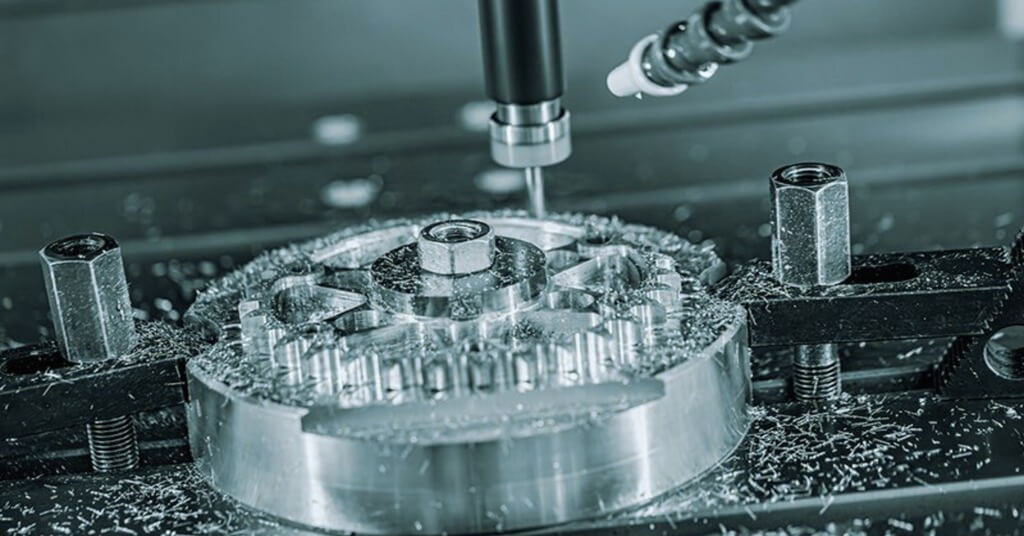
2) CNC Machining
CNC machining is used to manufacture a variety of metal automotive parts, including engine parts, cylinder heads, pistons, crankshafts, transmission parts gears, shafts, suspension parts, control arms, bushings, brackets, and mounts.
Because CNC machining is highly accurate, it can produce automotive parts with tight tolerances and complex geometries. It is also suitable for the production of small to medium batches of prototypes and production parts.
At the same time, CNC machining is also very versatile and can process a variety of metals, including aluminum, steel, titanium, and alloys, enabling the manufacture of durable and high-performance automotive parts.
3) Sheet Metal Stamping
Sheet Metal Stamping is used to produce a variety of automotive parts, including body panels, hoods, doors, fenders, frame rails, floors, brackets, hinges, and other sheet metal parts.
Sheet Metal Stamping is beneficial to automotive parts manufacturing because it is able to produce parts with high strength, rigidity, and dimensional accuracy.
And, because it has high productivity, it can produce large and complex parts while minimizing material waste.
In addition, sheet metal parts can be easily coated, painted, or welded to meet specific automotive design requirements.
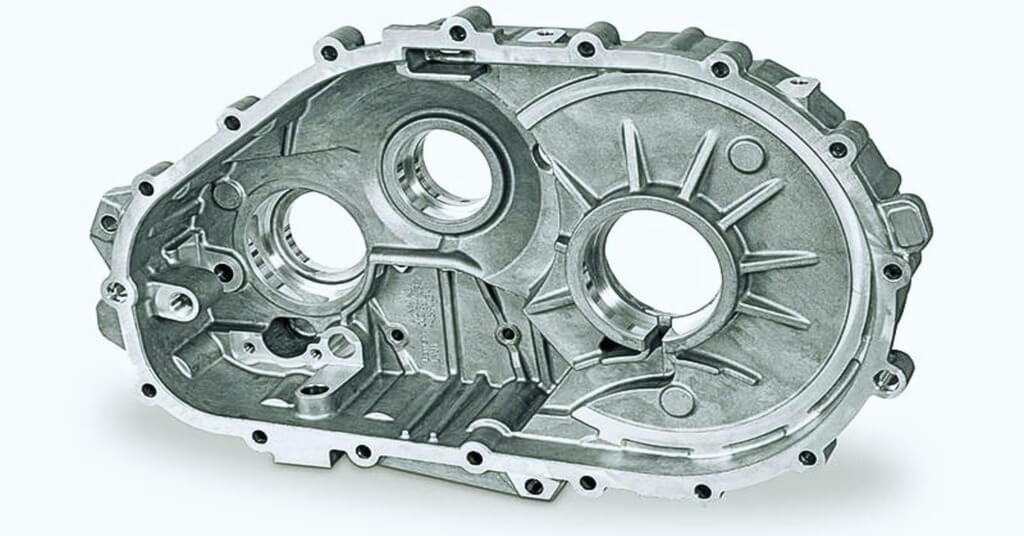
4) Die Casting
Die casting involves injecting molten metal such as aluminum or zinc alloy into a steel mold cavity under high pressure. The molten metal then fills the mold cavity, solidifies, and the part is ejected from the mold.
Die casting can be used to produce a variety of automotive parts, including parts such as cylinder heads, engine blocks, housings, clutch covers, brackets, and connectors.
Because of its high dimensional accuracy, excellent surface finish, and high strength-to-weight ratio, die casting is suitable for producing complex and durable automotive parts. In addition, die casting is cost-effective for medium to large-volume production and allows for tight tolerances and complex designs.
5) Silicone Casting
Silicone casting is a good choice if you need 2-10 high-quality plastic parts.
First, make a master model made of wood or plastic. Then pour liquid silicone on the master model and wait for it to solidify. Cut the silicone in half to get a half mold to make more copies of the master model.
Therefore, the quality of the automotive parts process obtained depends largely on the quality of the master model.
6) Additive Manufacturing (3D Printing)
Additive manufacturing or 3D printing is the layer-by-layer construction of parts based on digital 3D models. 3D printing is used in the automotive industry for prototyping, machining and manufacturing of small batches of customized parts such as brackets, chassis, internal components and complex geometries.
3D printing provides design flexibility, rapid prototyping capabilities and the ability to produce complex geometries that are difficult or impossible to achieve with traditional manufacturing methods.
In addition, it reduces the lead time and tooling costs of prototype development and enables on-demand production of customized automotive parts.
7) Composite Manufacturing
Composites manufacturing involves combining two or more materials, usually fibers such as carbon fiber or fiberglass, and a resin matrix such as epoxy resin, to form a composite structure.
Composites are used in the automotive industry to produce lightweight and highly resilient parts such as body panels, hoods, spoilers and structural reinforcements.
Composite materials are ideal for reducing vehicle weight and improving fuel efficiency, performance, and durability in automotive parts manufacturing because of their high strength-to-weight ratio, corrosion resistance, and design flexibility.
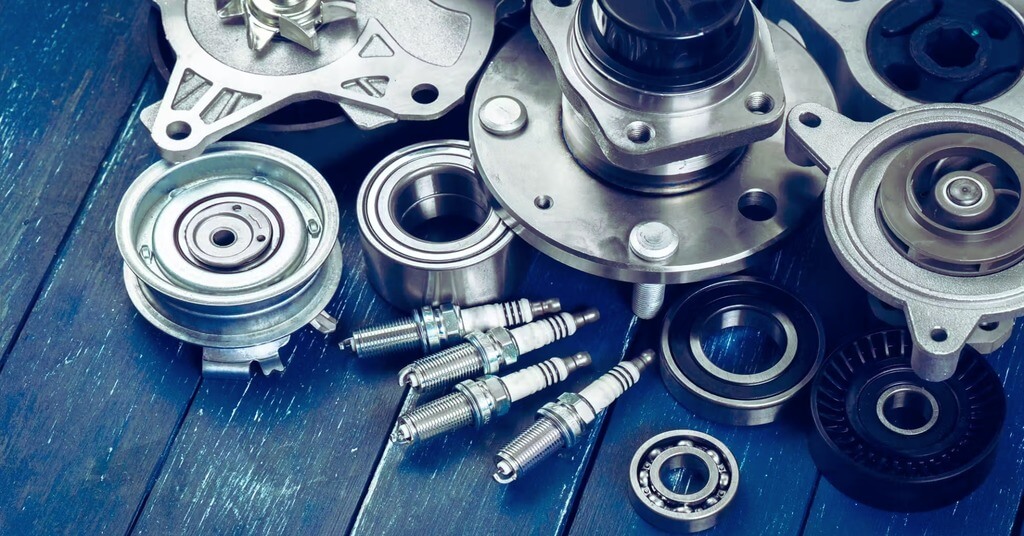
3.Surface Treatment Technologies for Custom Auto Parts Manufacturing
1) Powder Coating
Painting is one of the most common customization methods in custom auto parts manufacturing. Because most customers want their cars to have another color, a matte finish, some cool patterns, or specific pictures.
2) Anodizing
Anodizing is often used to finish custom aluminum auto parts manufacturing. If you see the great car customization ideas in this post, you will find some colorful parts that retain their metallic luster. Those are probably anodized.
Anodizing is a simple process that makes the oxide layer of aluminum thicker. It is made by inserting the part into an electrolyte and placing it in the anode of the current.
This removes ions from the metal surface and forms deep microscopic pores on the surface. The oxide film thickens around the pores. After that, fill the pores with paint and you get the metallic luster effect.
3) Polishing
Polishing requires the use of abrasive paste and soft tools to achieve a perfect surface finish. We usually think that only metal parts can be polished.
However, you can actually polish the painted elements of the car body as well. If you want your car to sparkle like a mirror and reflect your image, you can get some polishing services to add extra charm to your custom car.
4.Custom Auto Parts Manufacturing Workflow
Across the globe, the automotive industry follows different production lines and workflows. Custom auto parts manufacturing is also a part of these lucrative businesses.
But overall, the basic principles of manufacturing are pretty much the same. There are multiple steps involved in the custom auto parts manufacturing process. Here are the core stages from early prototyping to final assembly and shipping.
1) Prototyping
In the first stage of custom auto parts manufacturing, a proof-of-concept prototype is developed in addition to a visual model. This prototype is then submitted to the development team for further refinement and performance analysis.
Since custom auto parts have to be more versatile and efficient than OEM parts, the prototypes are rigorously tested in various scenarios.
The engineering team evaluates the performance of the CAD model, and after completing all the test cycles, the prototype is approved for design and production. Depending on the complexity of the part, the prototyping stage can take weeks or even months until the final design is approved for the next stage.
2) Design and Production
The subsequent phases of custom auto parts manufacturing involve transitioning from approved prototypes to design and production. This phase is the integration of assembly lines and industrial automation, with automation being particularly important as machines handle tasks such as painting and welding for each part produced.
During the design phase, companies utilize a variety of metals and raw materials to create custom parts. Each production company meticulously executes these processes as they directly impact the efficiency of the final product.
3) Quality Inspection and Evaluation
The third phase of custom auto parts manufacturing is just as important as production. During this phase, the final deliverables undergo rigorous real-world testing to ensure quality.
Once the custom parts are installed in the vehicle, they are evaluated for quality and performance, a critical step before they are released to the market. These evaluations confirm that each part operates as planned, meets performance standards, and adheres to vehicle compatibility guidelines.
4) Shipping
In the final phase of custom auto parts manufacturing, the parts are shipped through authorized dealers and manufacturers for public use.
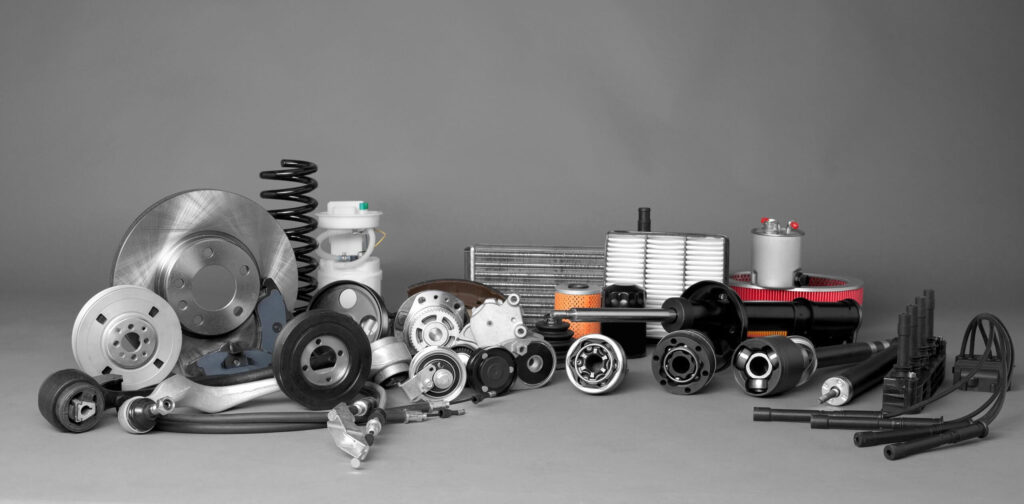
5.Raw Materials for Custom Auto Parts Manufacturing
Raw materials play a key role in the entire workflow of custom auto parts manufacturing. The use of each material and its grade determines the final product. These materials also determine the performance and quality of the components.
1) Steel
Steel and its various types play a vital role in the production of custom auto parts. It is the most widely used raw material and will directly affect the efficiency of the parts.
The key difference between competitors producing similar custom parts often lies in their choice of steel type and complementary elements. Steel manufacturers offer different grades of steel targeted to the automotive industry, providing different degrees of stiffness for different vehicle parts.
2) Aluminum
Aluminum has become a staple metal in auto parts manufacturing, and one of its main ores, bauxite, plays a vital role in custom auto parts production.
Aluminum is lightweight and ductile, making it ideal for manufacturing a variety of custom auto parts, improving fuel efficiency, and extending the battery range of electric vehicles (EVs).
According to some sources, the automotive industry uses about 466 pounds of aluminum in a typical car production. In custom auto parts manufacturing, aluminum can often replace steel in applications such as engine blocks.
3) Rubber
From tires to internal engine seals, rubber plays an important role in automotive production. It is an essential component of custom auto parts manufacturing.
Rubber helps companies to manufacture a large number of customized hoses, belts, and engine seals that determine the working nature of the machine. Moreover, it is a durable component that can be customized into different shapes. The demand for different types of rubber is increasing every year, and more than 65% of it is consumed by the automotive industry.
4) Plastic
The raw material used to make automotive parts is plastic. This material is obtained through chemical processing of petroleum. According to research, 8% to 10% of the weight of each car is plastic.
Due to its durability, this plastic is widely used in construction. Auto parts manufacturers use plastic in air conditioning vents, floorboards, switches, handles, and many parts inside the engine also use plastic in their construction. This material is used to replace steel due to its high load-bearing capacity and wide range of uses.
5) Glass
In the manufacturing industry, the role of glass cannot be ignored, especially from the perspective of observation. Different types of glass are used in cars in the form of lenses to get a clear view of the surroundings.
Glass is used to make windshields, which protect the driver’s safety during storms and other small wind objects. With the advancement of technology, glass is used to make rear lenses, which also help to get a clear view from the rear. To prevent more injuries in traffic accidents, laminated glass is also used in the manufacturing of different parts of cars.
6) Fiberglass
Fiberglass is widely used in the manufacturing of auto parts to replace steel as it is not prone to rust. This material is very different from fiberglass in terms of structure and usage.
Fiberglass is mainly woven in small strands of air and coated with a resin coating to provide tensile strength and heat resistance. This material is widely used to make your car fireproof.
Moreover, it is also essential in the manufacturing of bumpers and wheels. The main use of fiberglass in the automotive industry is to provide insulation.
7) Lead
When it comes to stability and weight balance, the only metal used is lead. The most critical use of lead in the automotive industry is in batteries.
Even auto and electric car batteries have lead in their structure as they maintain the temperature and keep it at a safe level. Since this metal is a bit heavy and can bear weight, different proportions of lead are added to fiberglass tires to increase its load-bearing capacity.
8) Titanium
Any auto parts manufacturer can use titanium to manufacture different parts of the car due to its corrosion resistance and low density. Titanium is mainly used in the manufacturing of internal combustion engine components.
The use of this metal reduces fuel consumption and improves the efficiency of cars. Apart from this, this metal also helps in reducing the noise level when the engine burns. Due to its high price, only a few manufacturers use this metal.
9) Magnesium
A widely used raw material in the automotive parts manufacturing industry is magnesium because of its light weight. This metal is used in the manufacturing of steering wheels and many interior parts, the lighter the weight, the better the performance. This metal is used in the front end of the car to help in better handling and cornering.
10) Copper
Although copper is not used in large quantities, it plays a vital role in the wiring process. This metal has better thermal conductivity and is used in radiators and other electrical connections in cars.
Apart from this, it is also used in starters, radios, and other safety systems.
11) Petroleum
Petroleum is the raw material for the production of plastics, which are an essential component in the manufacturing of custom auto parts. These plastics usually account for about 8% of the total weight of the car.
Various auto parts including door handles, airbags, and dashboards use these petroleum-derived plastics because of their versatility, light weight, and long-term durability.
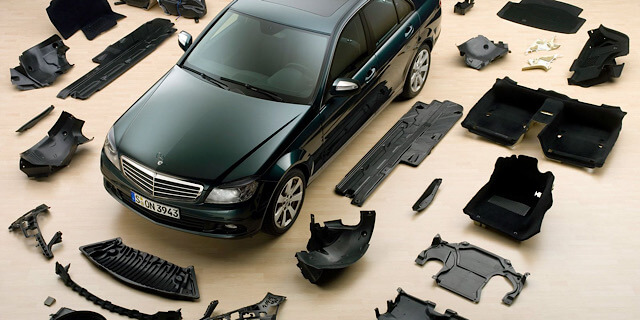
6.What custom car parts you can get
1) Interior
You can equip your car with proper seats like leather or leopard print seats, a cool steering wheel, different car panels with nice sensors or a whole LED screen TV. Whereas tuning the interior of a car is mostly about the exterior.
2) Exterior
We are usually talking here about spoilers, roof racks because maybe you want to carry your bike or boat around, and a rear rack for the spare tire.
3) Performance
This is the most complex and expensive part of car modification. Performance modification usually involves installing a better intake manifold, exhaust pipes, and if you want to be a real connoisseur of car design, you can install a turbocharger to increase your top speed on the straights. But be careful in the turns.
4) Lighting
Lighting customization is very rare because it requires reverse engineering of the old brackets to produce a new design. To make new custom lighting, you have to create clear optical lenses, reflectors and choose some light guides.
5) Wheels and Tires
Wheels and tires modification is one of the most common custom car parts options. There are many wheels available in the aftermarket, but if you have a unique design, you will have to order some CNC machining services to mill them out of a solid piece.
6) Repairs
Some unusual, rare, or vintage models may not be supported by any service or manufacturer. If certain parts need to be replaced, your repair will become a full-on customization.
7) Bodywork
Body customization usually involves swapping out the body panels for carbon fiber. This can make the car lighter by about 20%, making it more flexible and agile. Or you can replace the springs under the wheels to make the car softer.
8) Sound
Sound systems are coveted by enthusiasts all over the world. However, other people who happen to live on the same street as those enthusiasts don’t buy these speakers.
If you want to install a tuned sound system, you may have to replace the interior panels on the car doors, which makes the customization more complicated.
7.Advantages of using custom auto parts manufacturing for vehicle modification
Custom modifications of vehicles can improve performance, which affects the efficiency of the machine. Installing custom auto parts can significantly improve speed, suspension, fuel use, and carbon consumption within the engine.
Apart from these advantages, here are some of the main benefits of using custom auto parts manufacturing for vehicle modification:
1) Cost
Everyone thinks that vehicle modification is a very expensive task, but with the help of custom auto parts manufacturing, it can be made affordable.
Aftermarket parts are built for custom performance and are usually more affordable than OEM components. In some cases, the difference between custom parts and pre-installed vehicle components is more than 50%.
2) Choice
The second most important aspect of using custom components is choice. Yes, choosing different types of components from different companies can change the performance of your vehicle.
For example, installing a different size fuel cylinder can increase consumption while drastically increasing speed. The choice of different components also increases the positive competition in the market as custom manufacturers strive to create the best for their vehicles.
3) Safety
Safety reasons also make this list as many people are more cautious and they add extra features like roll cages and side airbags to increase safety in case of any accidents.
But these are not internal safety modifications. Improving the suspension and braking system of your car by installing custom parts is more beneficial than any other customization when it comes to the engine. Custom auto parts manufacturing also plays a big role in the safety and prevention department.
4) Convenient replacement
For most car owners, using custom parts is very convenient because OEM parts are not available everywhere, so it is easy to replace them on the go.
As mentioned above, custom parts are also less expensive (depending on the production company) compared to OEM parts. With custom auto parts manufacturing, automotive companies can significantly improve the global customer experience, drive sales, and improve overall convenience and comfort.
8.How can Xavier help your custom car manufacturing project?
Xavier’s first-class metal cutting services help companies make the right parts for their vehicles. When it comes to providing molding raw materials for custom auto parts manufacturing, we focus on precision.
From small batch component prototyping to large-scale production, the Xavier platform provides companies with the best on-demand cutting. Choose our precision cutting services at an affordable price to build your next product.
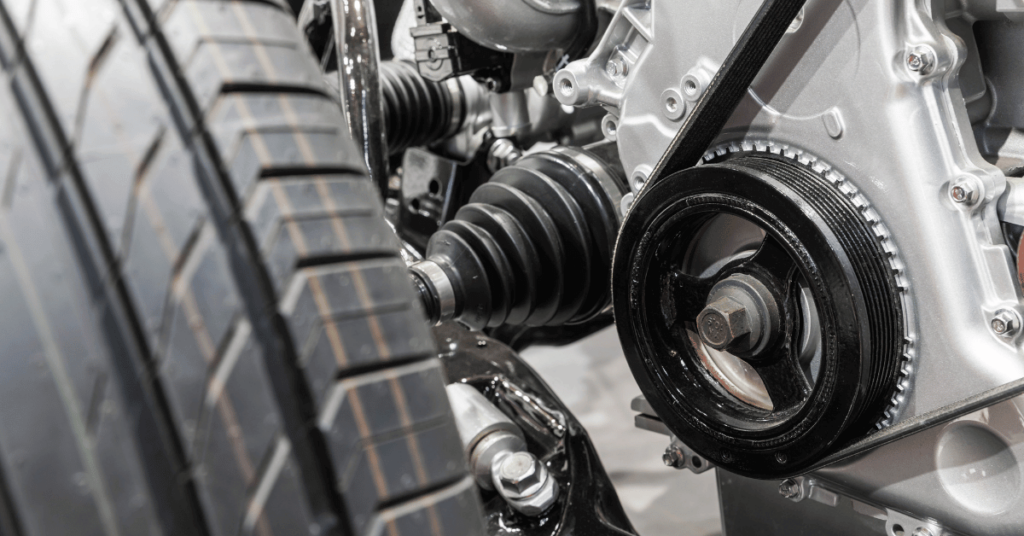
9.Common Questions and Answers
1) What are the steps of custom auto parts manufacturing?
Custom auto parts manufacturing involves different stages. The core parts are prototyping, design and production, actual quality inspection, and shipping.
2) What are the safety regulations for custom production?
Performing a safety checklist when manufacturing different parts helps prevent risks and failures. Other safety provisions include training, reporting, and the use of safety equipment.
3) How is quality maintained in custom auto parts manufacturing?
Quality control is a core phase of the custom auto parts manufacturing cycle, with different tests being performed on parts to identify defects and eliminate them before final assembly.
4) What role does automation play in parts manufacturing?
Automation in manufacturing refers to the use of technology to perform various tasks. Automated robots aid in the design and production phases of manufacturing, improving accuracy and reducing human error.
5) Which plastics are used to produce auto parts?
- Polypropylene is the material of choice for interior parts such as dashboard trim and door panels, the most commonly used plastic for auto parts.
- Polyethylene can be used for parts such as fuel tanks and underbody guards.
- Polyurethane is used for flexible foam parts such as seat pads and armrests for its comfort and shock-absorbing properties.
- ABS (Acrylonitrile Butadiene Styrene) is commonly used for interior and exterior parts, including trim and wheel covers.
10.Summary
Custom auto parts manufacturing has become the most important process for manufacturing top-notch parts designed to optimize vehicle performance. Manufacturers use a variety of materials and technologies to produce specialized parts such as fasteners, washers, and accessories.
Partnering with a specialized company is essential to ensure customized solutions meet exacting standards. In addition, this article contains important details on technologies, benefits, raw materials, and strategies to leverage them for efficient and optimal operations to meet your needs.