Introduction to the Basics of Aerospace Precision Machining
1.Introduction to Precision Machining
Precision machining is a method of manufacturing parts with tight tolerances and high precision. This level of accuracy is essential in producing pharmaceuticals, machine parts, and different components for the aerospace industry. TMD machining is suitable for precision machining in the air, on land, or at sea.
To produce a finished product, unwanted material needs to be removed from the workpiece through precision machining processes. This method produces high-quality products with precise specifications and tight tolerances.
Precision machining can be used to manufacture products of different materials such as metals, plastics, copper, rare alloys, titanium, ceramics, glass, bronze, stainless steel, etc.
Depending on the requirements, different combinations of tools can be used in precision machining to produce the finished product. To produce a large number of products with precision, computer numerical control (CNC) machines are used for precision machining.
For the aerospace industry, ensuring the quality standards of the components is key to avoid any failure during flight. Since even a poor quality of a component can lead to a disaster for the entire aircraft, the quality of all the mechanical components of the aircraft needs to be ensured.
In aerospace applications, different components with higher strength and lower weight are manufactured through precision machining processes.
The process is also promising for the production of mechanical parts with complex shapes and tight tolerances. CNC precision machining is used in the aerospace industry to produce complex shaped parts cost-effectively with a safer production method.
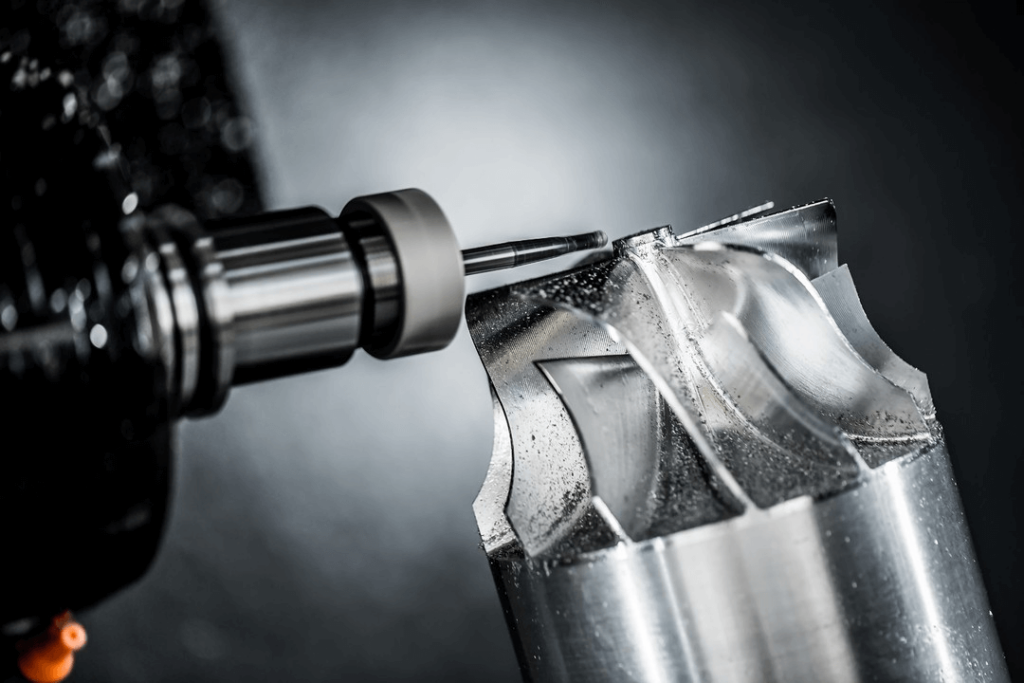
2.Importance of Precision Machining in Aerospace Manufacturing
Precision machining has impacted every sector, as CNC equipment has been repeatedly proven to increase the efficiency of a wide range of standard processes in manufacturing. Learn how it is a particularly important addition to the aerospace manufacturing industry.
1)Save Money, Time, and Lives
Computer numerical control machines make precision machining possible, as the technology makes it easier to increase manufacturing speeds while maintaining the quality of work.
These machines use computers and the right commands to ensure that each step is completed perfectly. These machines use all three dimensions to handle nearly any material or pattern, making them one of the most versatile solutions in the manufacturing field.
And because the material is cut by the machine, the error rate is lower than that of human hands, so there is much less waste. This expansion allows more projects to be completed with less labor and in less time.
This means that humans will make more discoveries and push more boundaries over time in terms of space travel. At the same time, the field of precision machining will continue to place a high priority on accuracy and safety.
3.Challenges of Precision Machining Parts for Aerospace
Manufacturing aerospace parts is not as simple as people think. There are different challenges in the process of manufacturing aerospace parts using precision machining.
Such as machining large parts with thin walls, handling complex part geometries, and high-mix low-volume production.
1) Tight Tolerances
Aircrafts are made up of millions of small parts. These small parts are manufactured individually using different machining processes and then assembled for proper function.
For an aircraft to function properly, all parts must have tight tolerances. Parts that require tighter tolerances are difficult to manufacture and expensive.
In some cases, using tighter part tolerances can justify the overall cost. For example, in the case of tighter tolerances in aircraft engines, the need for piston rings can be eliminated without affecting the proper functioning of the engine.
In order to produce high-quality products with tight tolerances, computer numerical control (CNC) machines must be used. Although tight tolerances make part production more expensive, safety factors are an important factor that must be considered in the aerospace industry.
In aircraft manufacturing, precision machining must be used to produce different parts of engines, avionics, sensors, fuselages, connectors, and seats.
The choice of CNC machining also depends on your requirements for product tolerances. Parts can be made with precision machining to a tight tolerance of ±0.0001”.
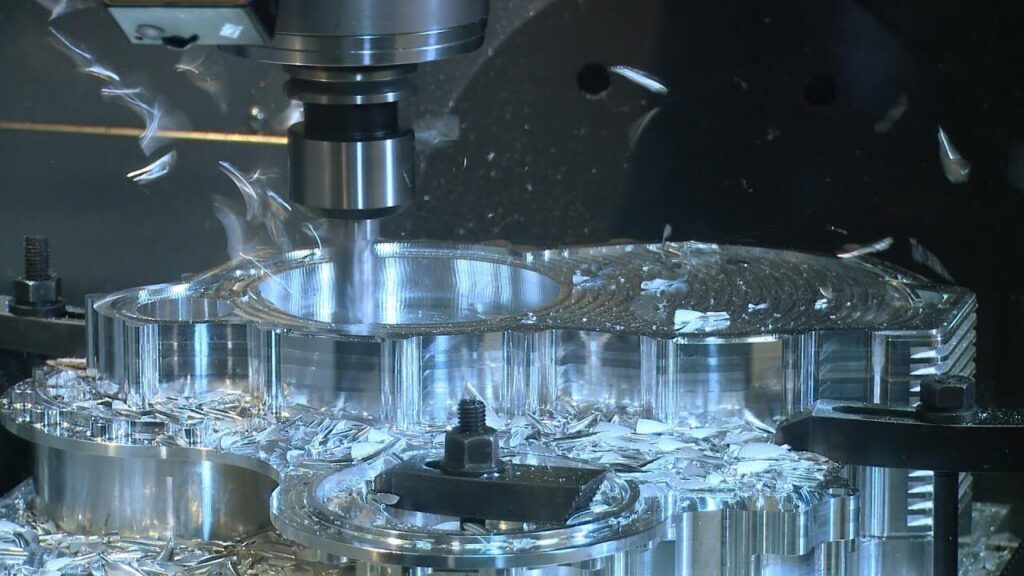
2) Handling Difficult Materials
Choosing the right material to manufacture aircraft parts is one of the important issues in precision machining. Many parts are made of different materials that require different machining processes depending on their properties.
In the aerospace field, people want to manufacture parts with light weight, higher strength and durability. Aluminum, as one of the most readily available materials on earth, and the machinability and ductility of aluminum alloys, is mainly used in aerospace applications.
In other cases where higher strength or even increased weight is required, aerospace and aircraft applications use stainless steel, titanium, high stress alloys, and carbon.
Another problem with materials in the aerospace industry is that different materials such as aluminum, carbide, titanium, steel, ceramics, and other alloys are used to manufacture parts in aerospace applications.
Therefore, in order to manufacture high-quality products with high and tight tolerances, professional CNC operators are required to handle different materials. Experienced employees can easily machine and shape different materials.
3) Handling complex designs
The complexity of aircraft parts is a major problem in the manufacturing process. In order to reduce weight and increase the strength of the parts, the complexity of the design increases the cost and time required for manufacturing.
This problem requires professional machinists to operate the machines and produce parts with complex geometries.
In some cases, design complexity is unnecessary and can be avoided to reduce cost and time. For example, for internal components, the airflow will not be affected by the internal geometry of the part, so in this case, we do not need to make special surfaces inside the part.
There are also some limitations in choosing a CNC machine for manufacturing aircraft parts. Because there are millions of parts in an aircraft, both small and large parts.
In both cases, the choice of CNC will vary depending on the size of the part. The product can also be made cost-effective by varying the manufacturing process based on the machining facilities available.
In some cases, it is difficult to avoid the complex geometry of aerospace parts, so in such cases, 5-axis CNC machines are the first choice for part manufacturing.
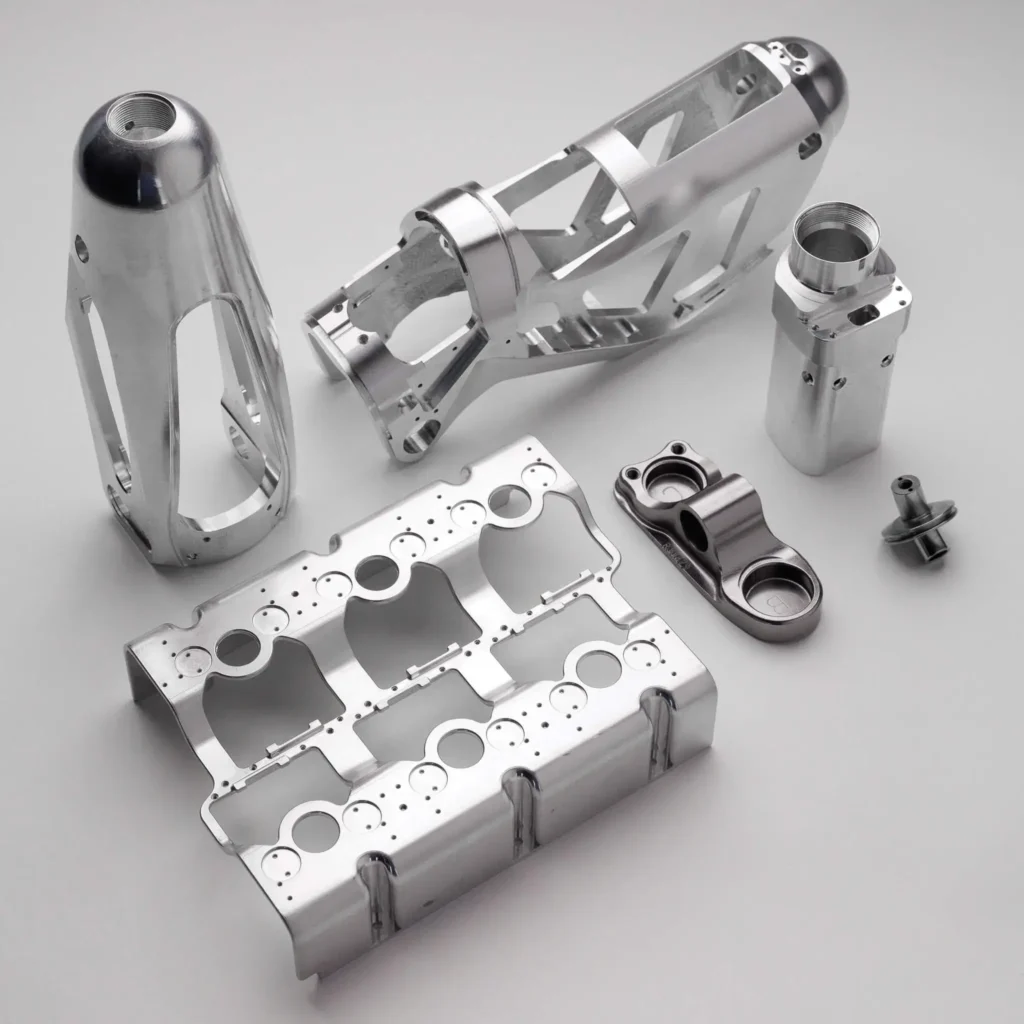
4.Conclusion
To summarize, in the aerospace industry, all the parts of an aircraft must meet all the quality standards to function properly. Depending on the requirements, the parts can be made through different processes and different materials.
In addition, different tools are selected depending on the material used to manufacture the part. There are many challenges in the manufacturing process, such as handling different materials, complex geometries of the parts, and tight tolerances.
To address these issues, Computer Numerical Control (CNC) machines are the first choice for manufacturing various aerospace parts. Using precision machining processes, CNC machines are able to produce parts with complex geometries with high quality and higher productivity.