The Basics of CNC Milling Parts
CNC milling is one of the world’s most important manufacturing and engineering technologies. Machine shops near me are also very capable. CNC milling combines creativity with precision engineering, which complement each other to transform raw materials into finished parts.
With this guide, we hope to cover everything about CNC milling; everything a beginner needs to know and even tips that professionals already know about how to get the best and most accurate results in the machining process.
From understanding what these machines do at the simplest level to understanding the advanced methods used to manufacture complex components, this article should be your ultimate resource.
We will also look at the different types of materials that can be processed by CNC milling machines and the various possibilities that such equipment offers in a contemporary production environment
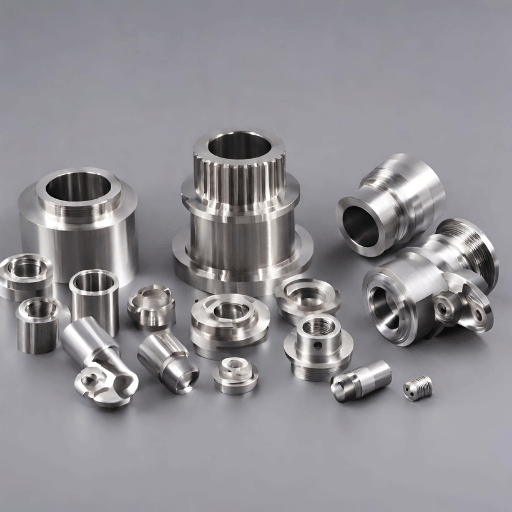
1.Understanding the Core Components of CNC Milling Machines
The interactions between the machine tool and the workpiece are crucial for CNC milling machines as they directly affect the quality, accuracy and efficiency of the machining process. These interactions involve various factors such as cutting forces, vibrations, material properties and surface finish requirements.
1) Cutting Forces
When a milling cutter engages with a workpiece, it applies forces in different directions. The magnitude and direction of the cutting forces depend primarily on the depth of cut, feed rate, tool rake angle, and the type of material being machined. These forces must be properly managed to prevent excessive tool wear or breakage and to ensure dimensional accuracy.
2) Vibration
In CNC milling, vibrations can be caused by a variety of reasons, including unbalanced rotating parts such as the spindle assembly or motor shaft, improper fixturing, unstable machine structure, worn bearings, or incorrect cutting parameters.
Vibrations can negatively affect surface finish as they produce chatter marks on the machined surface. In addition, they can also induce fatigue failures, which can shorten tool life.
3) Material Properties
Different materials have different properties that affect their machinability level. For example, some metals have high thermal conductivity, which causes heat to dissipate quickly during cutting operations, while other metals have low thermal conductivity, resulting in increased temperatures in the cutting zone.
In addition, differences in thermal conductivity between workpiece materials affect the rate of heat generation during milling and also affect chip formation patterns, so chip evacuation capabilities require appropriate feed speeds to be selected accordingly.
4) Surface Finish Requirements
The level of smoothness or roughness required for the finished component determines the specific surface finish that needs to be achieved through appropriate machining strategies, such as climb milling versus conventional milling (upcut/downcut).
Additionally, the workpiece may require features such as flatness within certain tolerances, perpendicularity between two surfaces, concentricity around a specified hole, etc., all of which must be considered when programming the CAM software path based on these geometric specifications to ensure accurate reproduction on the actual part.
During CNC milling machine programming, these machine tool and workpiece interactions should be fully understood to optimize machining parameters and obtain the best results.
In order to achieve precision in CNC milling, it is important to consider how the machine tool interacts with the workpiece. Having worked in this industry before, I can say that understanding this relationship is crucial to selecting the right equipment and successfully carrying out a project.
The quality of a product depends not only on its design, but also on how the tool contacts the material; beyond this, factors such as tool wear, machining efficiency, and overall productivity may also be affected.
It is crucial to ensure that the machine capabilities match the complexity of the workpiece, starting with the characteristics of the material used, to the geometric complexity involved, and so on.
In other words, harder materials will require machines with higher spindle power, which have powerful cooling systems that can manage heat well to extend tool life throughout the cutting process.
Likewise, when manufacturing complex parts, you need more flexible axis machines that allow for precise cuts at different angles.
So we can say that having a deep understanding of these relationships allows us to optimize production methods, reduce errors during machining operations, and manufacture parts that meet exact dimensions.
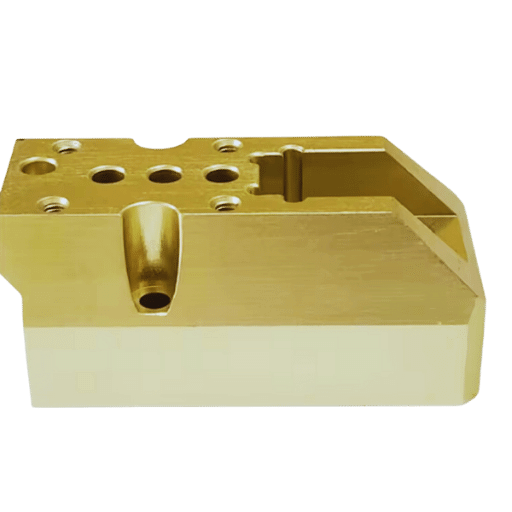
2.How G-code and CNC Programming Affect Milling
In CNC programming, G-code is the language used by the machine. It is the basis of all programs used in CNC machining. This means that it is responsible for translating complex design instructions into specific commands that tell the milling machine how to move itself.
For example, spindle speed and direction can be specified as well as tool paths or depth of cut, among other things. Manufacturers who are familiar with g-code can create complex designs very accurately; they are able to reduce production time by optimizing cutting paths while still achieving high precision during machining.
More advanced programming techniques combined with g-code allow for customization so that each workpiece can be given its own set of operating steps as needed, ensuring that design specifications are met.
3.Tool Changers and Custom Parts: Making the Most of Machine Time
The use of tool changers in CNC milling processes greatly improves machine time utilization, as manual tool changes take longer, resulting in downtime.
These automated systems allow switching between different types or sizes within a single cycle, which makes manufacturing cheaper because the setup costs for each batch produced are reduced.
In addition, other operations such as drilling, tapping and milling can also be simplified when manufacturing custom parts that require multiple tools for various processes. This feature becomes more important, especially when many precise parts need to be produced in a short period of time.
While increasing production, it can also reduce delivery time and meet the demand for high-precision engineering components. Therefore, incorporating these facilities into a CNC machining setup can increase the overall production efficiency flexibility during manufacturing activities.
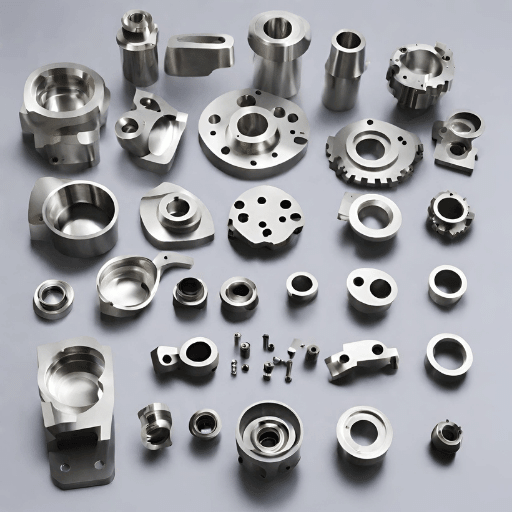
4.Different Milling Operations Require Different Machining Methods
Different requirements require different milling methods as milling involves a wide range of operations that vary greatly from each other and only require slight modifications to the feeds, speeds and tools used, but still keep the feed rate or stepover proportional to the entire part surface area that needs to be machined.
For example, face milling cutters are mainly used when flat surfaces need to be created on the surface of the workpiece, while end mills are used to machine pockets, etc.
Furthermore, slab milling is ideal when large pieces of material need to be removed quickly and therefore should not be used only for finishing, whereas ball end mills produce 3D shapes and therefore may require more precise stepovers.
It is therefore important to understand what is required for each type, including cutting speeds, chip loads and toolpath strategies to achieve the highest levels of precision and surface finish quality, considering that advanced simulation planning software can also help optimize these operations, thus ensuring accuracy throughout each stage of the process until the part is exactly to the required standard.
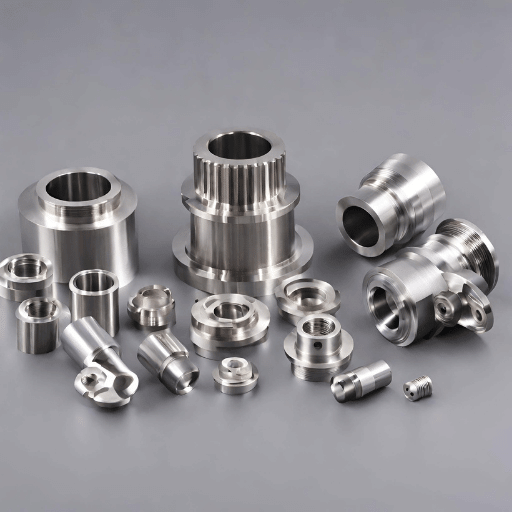
5.Types of CNC Milling Machines and Their Applications
1) From 3-Axis to 5-Axis: Navigating the Different Milling Capabilities
When it comes to CNC milling machines, it has a wide range of capabilities from basic 3-axis machines to more complex 5-axis configurations.
3-axis machines offer movement and cutting capabilities in three directions (X, Y and Z axes) and are suitable for most common milling tasks where the parts do not have complex geometries or intricate details.
In contrast, a 5-axis milling machine has two additional axes of motion, allowing it to approach the workpiece with a cutting tool from any direction.
This enables highly complex parts with tight tolerances and complex geometries to be machined in a single setup, increasing efficiency and accuracy.
Choosing between these two types depends on a variety of factors, such as the volume of production required, the type of material being machined, the complexity required, and budgetary constraints.
2) The Special Role of CNC Lathes and Mills in Milling
Although not usually associated with traditional milling operations, CNC lathes and routers play a special role in the broader context of the technology.
For example, while primarily used for turning operations, lathes can also be set up to perform milling tasks, enabling the precision manufacture of cylindrical parts with complex features.
This flexibility is particularly beneficial in shops that need turning and milling capabilities but lack sufficient space or funds to purchase multiple machines.
Routers, on the other hand, are specifically designed for high-speed cutting of soft materials such as wood, plastic foam, etc.
With their fast and accurate cutting capabilities, they are indispensable tools in industries that require fine finishes or detailed designs, such as sign making, furniture manufacturing, prototyping, etc.
In summary, CNC lathes and routers may serve niches within the overall machining process, but each expands the work that can be done within a given facility by increasing efficiency and enabling a wider range of applications.
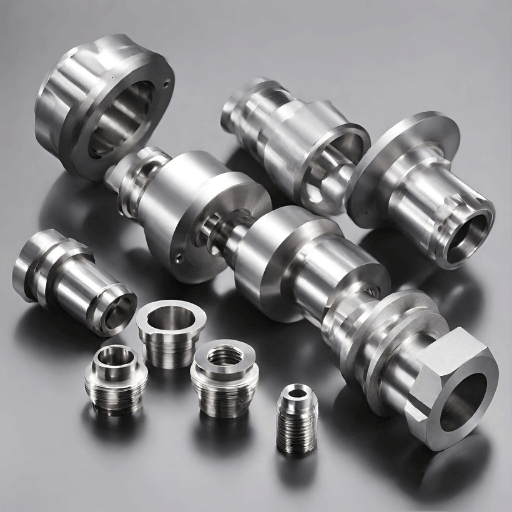
6.Choosing the Right CNC Milling Machine for Your Machining Process
To choose the most appropriate CNC milling machine for your machining process, you must first determine what exactly it needs to do.
If the parts you intend to manufacture are complex, then a 5-axis machine may be required, rather than just a 3-axis machine. Another factor is production volume, as large batches require faster processing speeds as well as automation, which can increase productivity levels within an organization.
It is also worth considering the type of material, as harder materials may require a more robust milling machine that can withstand more power and be durable enough when milling.
Furthermore, budget should not be overlooked, as investing in advanced machinery should be matched with the expected return, namely higher quality output as well as time saved during operations.
Ultimately, the right CNC milling machine will not only fit current business activities, but also allow for expansion when needed as well as handling future complex projects.
7.Evolution of CNC Milling Parts in Precision Machining
1) Development of Cutting Tools and Surface Finishing Methods
The development of cutting tools has greatly changed the landscape of precision machining, bringing materials such as polycrystalline diamond (PCD) and cubic boron nitride (CBN), both of which have extremely high durability and high-speed machining accuracy.
Another development in surface finishing technology is laser texturing, which enables ultra-smooth surfaces, which are essential for aerospace or medical components such as implants.
Compared with traditional finishing methods, these advances not only improve the quality and function of parts manufactured by machining, but also save time and money.
2) Using New Technologies to Improve Tool Life and Machine Efficiency
New technologies applied in precision engineering have changed the way we extend tool life and improve machine efficiency. For example, cryogenic machining utilizes extremely low temperature cutting fluids, while advanced coatings such as titanium aluminum nitride (TiAlN) are used to extend tool life.
In addition, real-time monitoring systems are now installed on machines, allowing operators to know when maintenance is required, thus significantly reducing downtime through predictive maintenance through IoT (Internet of Things) systems, which can also optimize performance by addressing wear issues before they become serious; this also saves costs because repairs are only carried out when necessary.
With these improvements, the service life of the machine will be greatly extended, thereby increasing the productivity level of all manufacturing processes and improving overall quality standards.
3) How Materials and Design Affect Precision During Machining Processes
The level of precision achieved during machining processes depends largely on the design of the machine and the materials used.
To minimize vibration during operation, some machines are designed with rigid structures, while others use linear guides that are more accurate than traditional machines.
Rigidity helps to keep the tool aligned with the workpiece, so that the required size can always be achieved when making multiple cuts on different parts made from the same material batch number, etc.
Thermally stable materials should also be considered, as they can offset dimensional errors caused by temperature changes inside machine parts during production runs, where carbon fiber composites or ceramics are used as insulators to prevent heat transfer between different parts of the machine.
These materials have better thermal properties compared to metals. The increased accuracy enables the continuous production of parts with tight tolerances to meet aerospace industry specifications and other demanding specifications such as those for precision medical devices.
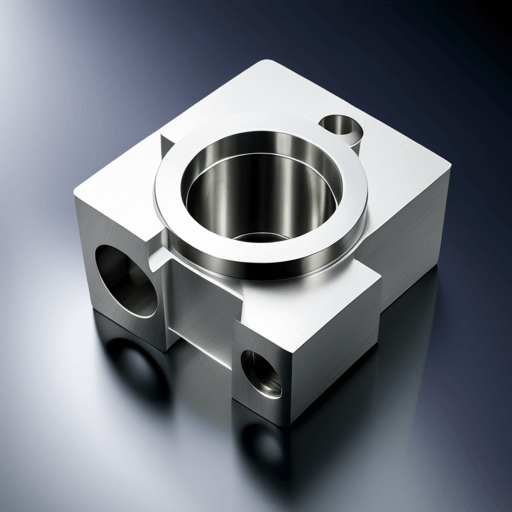
8.Regular Checks: Spindle Health, Coolant Levels, and Control Panel Performance
Performing regular diagnostic checks that focus on key components such as spindle health, coolant levels, and control panel performance is essential to keeping your CNC milling machine in tip-top shape.
Machining accuracy and increased machine life can be achieved by ensuring that the spindle is running smoothly and without any vibration or noise.
It is also important to maintain the proper amount of cooling lubricant to promote effective heat dissipation, thereby preventing overheating and the potential damage that can result from it.
Finally, frequent testing of control panel functions ensures accurate response to commands, thereby minimizing errors that can cause unexpected interruptions to production activities.
If these maintenance practices are performed on an ongoing basis, the reliability and efficiency of the equipment will be improved, thereby maximizing productivity while minimizing repair costs.
9.Dealing with Common Milling Problems: Faults and Machining Errors
Common milling problems such as faults and machining errors can be resolved with an organized approach to troubleshooting.
When encountering a fault, first check the mechanical components for signs of wear and then check that the electrical system is functioning properly. It is also recommended to calibrate the machine regularly to achieve accuracy during operation.
In addition, updating the CNC software can help fix errors that may interfere with its performance. Predictive maintenance strategies implemented using sensors and IoT technology will reduce downtime by detecting potential failures early before they develop into full-blown emergencies.
Proper operator training on routine maintenance procedures, coupled with emergency response skills, can reduce the likelihood of costly mistakes due to failures, thereby maintaining continuous production quality and efficiency.
10.Extending the Life of CNC Milling Machines Through Proper Maintenance
Extending the life of CNC milling machines depends on careful maintenance and preventive measures. This means maintaining the machine regularly; lubricating joints that move against each other or rotating parts that often rub against each other; regularly checking coolant levels to avoid overheating due to low coolant levels; ensuring that the control panel is functioning well for precise operation, etc.
When solving typical milling challenges, a comprehensive inspection is required to detect wear on components and calibration exercises are performed to ensure accuracy.
Using IoT technology during predictive maintenance will be of great help because it can detect potential problems before they escalate into large issues, leading to machine failures that will negatively affect productivity.
All of these methods work together to improve equipment efficiency, minimize failures, and extend service life, thus providing value for money.
11.Future Trends in CNC Milling and Manufacturing Processes
Integrating Automation and Artificial Intelligence (AI) into CNC Machining for Improved Accuracy. With the adoption of automation and artificial intelligence (AI) in CNC machining, the accuracy and efficiency of the manufacturing industry has been greatly improved.
The use of robots and more advanced machines has made it possible to speed up production by streamlining different processes. Moreover, this has created scope for handling repetitive tasks at unimaginable speeds while always maintaining consistency.
As if that wasn’t enough, once AI is involved, intelligent decision-making becomes part of computer numerical control technology; it can foresee tool wear, optimize real-time cutting paths, and even predict potential failures of the machine.
Therefore, this means that both technologies must work together so that the products produced by the machine tools are in perfect condition while minimizing human errors, thereby increasing productivity levels and reliability in the manufacturing environment.
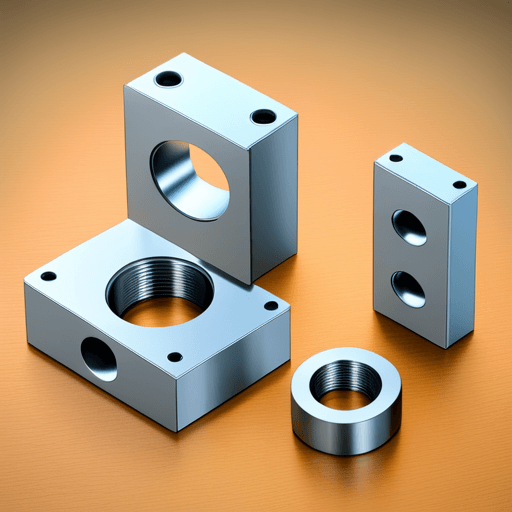
12.Sustainable Manufacturing: How CNC Supports Eco-Friendly Production
CNC technology is one of the key drivers of sustainable manufacturing as its accuracy and efficiency significantly reduce waste in the production process.
CNC machining complies with green or eco-friendly principles through material optimization and minimization of the frequency of errors, thereby reducing rework.
Furthermore, this advancement in machinery allows for the use of recyclable materials, thus enhancing sustainable practices in industries that involve manufacturing work, such as metal cutting, which typically uses plastics.
In addition, integrating energy-efficient motors and adopting low-power methods during machining also helps reduce carbon footprint, thus positioning CNC systems as key to achieving industrial sustainability goals.
13.How 3D Printing and Additive Manufacturing Impact CNC Milling
The introduction of 3D printing and additive manufacturing has brought huge benefits to CNC milling, as there is a complementary relationship between them in terms of their application in this field.
CNC milling machines are known for their high levels of precision and reliability in subtractive machining processes, but creating complex custom shapes using traditional methods alone can be difficult or even impossible, which is where 3D printers come in handy.
This means that manufacturers can now use both technologies together when necessary – for rapid prototyping purposes, detailed designs can only be achieved through additive processes such as printing, and then milling machines are used to cut out large quantities that require high precision.
Furthermore, AM pushes the boundaries of the materials used in manufacturing, thus diversifying the applications of CNC systems in modern engineering, such as incorporating new substances into traditional methods, thus extending their capabilities and broadening the range of products produced by these machines.