What is CNC Machining Center: A Brief Introduction Guide
In today’s world, the industrial field has higher and higher requirements on the performance of various machines and tools. In order to meet this requirement, multifunctional equipment is integrated to operate as a unit. They are capable of automated machining.
The typical representative of this concept is the CNC machining center, which performs the tasks of multiple CNC machines simultaneously as a unit. In this article, you will find information about CNC machining centers.
1.What is a CNC machining center?
A CNC machining center is a machine tool that integrates the functions of CNC machines. It can perform CNC lathe operations, CNC milling tasks and CNC drilling activities simultaneously.
Its automatic tool changing mechanism enables it to use cutting tools within the setup, thus producing a high-quality end product with greater accuracy, precision and smooth surface finish.

2.How does a CNC machining center work?
The operation of a CNC machining center depends on the synchronized operation of its six components. Let’s delve into their workings to understand their mechanisms:
- Key elements
- CNC system
- Spindle section
- Other tools
- Automatic tool change system
- Feed structure
1) Key elements
These are the components of CNC machining centers, including:
- Work table
- Column
- Bed
Their main role is to withstand the cutting and static loads generated during machining, thereby providing sufficient strength. These components are usually made of welded or cast iron parts.
2) CNC system
The CNC system of CNC machining centers mainly consists of the following components:
- Servo drive unit
- Control panel
- PLC (Logic Controller)
- Numerical Control Device (NCD)
This system acts as a central control unit and performs processing operations.
3) Spindle section
The spindle area consists of the following parts:
The main components include motor, spindle, spindle box, wear-resistant belt and power lock. The spindle section provides space for the cutting tool. It directly promotes its high-speed rotation.
4) Auxiliary equipment
The auxiliary device consists of machine tool system, hydraulic system, lubrication mechanism, cooling system, detection system, etc. Although these components are not directly involved in the cutting process, they are key components to ensure machining accuracy and efficiency and to ensure the production of the final product.
5) Automatic tool
The replacement system consists of a manipulator and a tool. During a machining operation that requires tool replacement, the CNC system issues a command to let the manipulator take the tool from the tool magazine and put it into the spindle hole.
6) Key elements of the feeding structure
The displacement measurement component, transmission device, and feed servo motor are used to move the worktable and spindle axially during the machining process to ensure the quietness of the machining process.
When we focus on CNC machining centers, we mainly focus on machining workpieces such as plastics and metals. The workpiece is fixed in a fixture and machined by tools that remove a large amount of material. The machine’s computer is responsible for programming tool speed and movement. The operator accesses the tool and fixture through a door.
Different machining centers perform machining across planes and axes for mold cutting or part machining, such as drilling and tapping. Therefore, the parts produced have precision and tolerance.
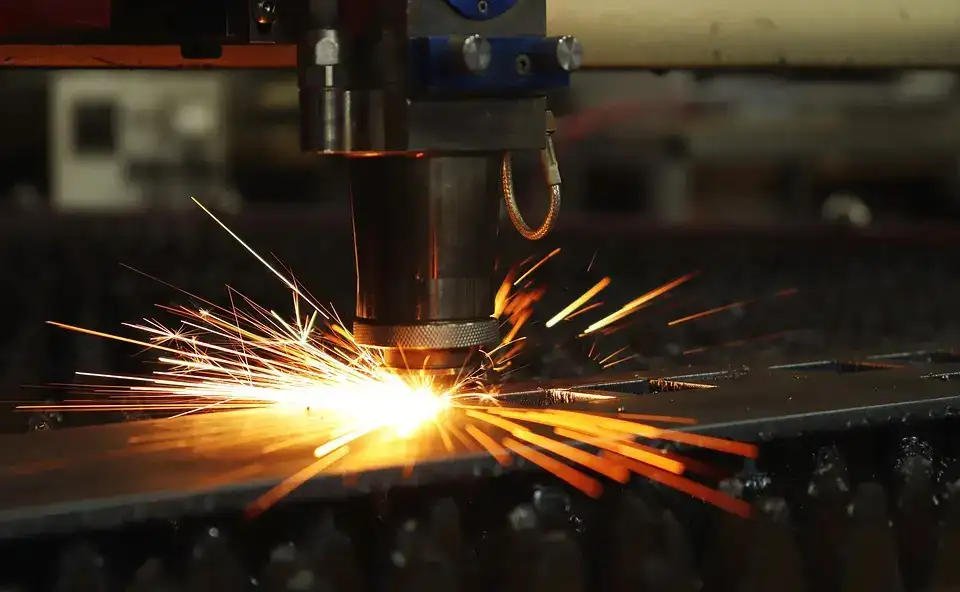
3.What are the key features of CNC machining centers?
Some of the key features include:
1) Coolant System
It is used to manage fluctuations during operation. It helps to maintain cooling, thereby automatically preventing overheating. This helps maintain the accuracy and durability of the tool.
In addition, the removal of chips keeps the machining environment clean.
2) Multi-axis System
These systems mainly consist of multi-axis setups such as 3-axis systems. In this setup, the cutting tool moves along three axes X, Y, and Z.
This enables the tool to reach all sides of the workpiece. In CNC machining centers, 5-axis or 6-axis systems have been introduced to create complex geometries.
3) Automation and Safety
CNC machining centers are equipped with automated operations to complete machining tasks. This eliminates the need to handle the workpiece and tool during machining, ensuring that there is no risk of damage during machining.
4) Automatic Tool Changing
The tool is automatically switched by the tool changer after each machining operation. This eliminates the need to change the tool. This speeds up production by efficiently producing a variety of products in a shorter time.
4.What are some common uses for CNC machining centers?
CNC machining centers are widely used tools. The features they offer include:
1) Mass Production
CNC machining centers simplify tasks through automation, making them ideal for mass production of parts.
2) Mold Manufacturing
These machines utilize CNC milling and drilling technology to create molds and dies necessary for producing products such as rubber products, aircraft sheet metal parts, and automobile engines.
3) Manufacturing Parts
Due to their precision and accuracy, CNC machining centers are favored for manufacturing parts with complex geometries.
5.What types of CNC machining centers are there?
The different categories of CNC machining centers include:
1) CNC Vertical Machining Centers
Vertical models feature a design with a rectangular table and a fixed column. They use a directional spindle to cut from the top of the workpiece. While easy to use, they can pose challenges when it comes to removing chips during operation.
2) CNC Horizontal Machining Centers
These machines consist of a table, a column, and a horizontally placed spindle. This setup allows the workpiece to be machined at an angle, making it easy to remove chips from the table. They are often used for shaping surfaces and milling slots and grooves.
3) General Purpose Machining Center
This type of machining center features a spindle that can be controlled vertically and horizontally by a computer program. It has 5 or more axes that can perform a range of milling operations. The machine can machine the sides of a workpiece in one go, simplifying the machining process.
6.Classification by Machining Method

1) Milling
In milling operations, a rotating cutting tool is used to remove material from a workpiece. This type of cutting tool is called a milling cutter and is ideal for machining rough or flat surfaces.
In some areas, CNC milling is a machining method that relies on computer control to produce custom parts. To start the process, a digital representation of the desired part is made using CAD software.
The subsequent steps are consistent with this framework. CAM software is used to design tool paths and instructions so that the CNC machine monitors feed rates and spindle speeds well. These instructions detail the movement of the cutting tool in the X, Y, and Z axes.
2) Boring
Boring machines are used to enlarge existing holes in a workpiece through a boring process using a single-point cutting tool.
Types of machining centers classified by tool changing method
- Machining center with robot tool changing
- Machining center without robot tool changing
7.Types of machining centers classified by accuracy
- Ordinary precision machining center: The positioning accuracy of this center is about 10μm, the feed speed is 15-25m/min, and the resolution is 1μm.
- High-precision machining center: These centers provide positioning accuracy of about 2μm, a feed speed range of 15 to 100m/min, and a resolution of 0.1 m.
- Precision machining center: The accuracy of these centers is within ±5μm, and the resolution ranges from 2 to 10μm.
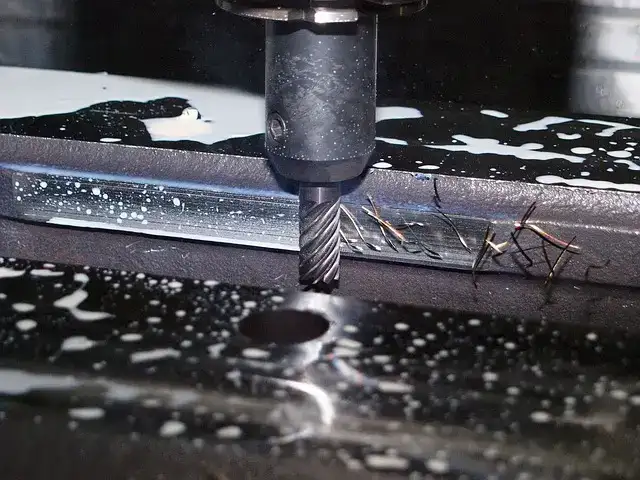
8.Difference according to the number of controlled axes
- Three-axis machining center: This type operates by moving the spindle in three directions. X, Y and Z axes.
- Four-axis machining center: In 4-axis CNC machining, the cutting tool moves along four axes. X, Y, Z and A axes.
3.5-axis machining center: They involve a cutting tool that moves in five different directions. X, Y, Z, A and B axes are used to cut materials.
4.6-axis machining center: They have six axes of movement, including three A, B, C axes and three linear X, Y, Z axes.
According to the type of the number of workbenches, it can be divided into workbench machining center, double-table machining center and multi-table machining center.
9.What is the price of CNC machining center?
As for the cost of CNC machining center:
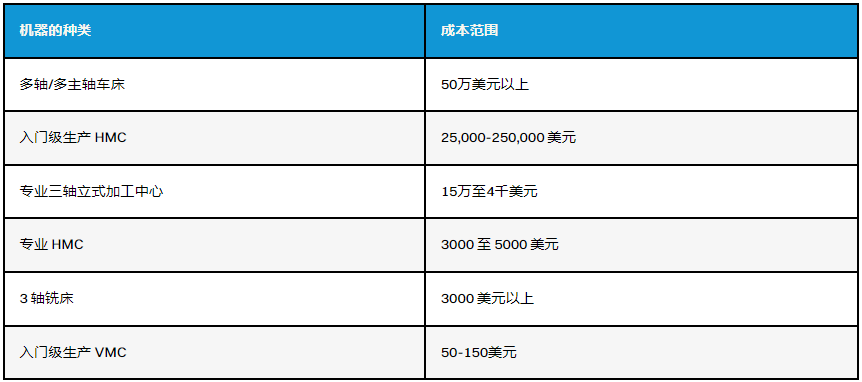
The cost of CNC machining depends on factors such as brand reputation, size, power, speed and durability. If these factors are high, the cost will automatically rise. CNC machining centers produced by well-known brands tend to be more expensive than CNC machining centers produced by cheaper brands with fewer functions.
10.Summary
In essence, a CNC machining center is a machine tool used to quickly produce parts with features. Its various components collaborate to perform CNC tasks such as milling and drilling, demonstrating machining capabilities due to its outstanding functions.
These machining centers are affordable and can efficiently handle a range of machining tasks, making them ideal for producing high-precision and intricate parts.
If you are looking for an experienced CNC machining manufacturer, Xavier is your ideal choice. The Xavier team is well-equipped to provide high-quality CNC machining solutions. If you need more information or to discuss your machining needs with us, please feel free to contact us.