A Guide to Small Batch CNC Machining: Custom Manufacturing Solutions
Welcome to the precision of low-volume CNC machining! A defining feature of this rapidly evolving manufacturing industry is the increasing importance of low-volume production. Total Machining Solutions uses state-of-the-art precision machinery and manufacturing processes to manufacture your custom products.
In this blog, we will explore this important aspect of modern manufacturing and take an in-depth look at how small batch CNC machining is changing the way we produce goods.
1.What is Small Batch CNC Machining?
Small batch CNC machining is a manufacturing process that creates small batches of precision parts, typically ranging from one to several hundred. It is a popular choice for prototypes, custom orders, or small production runs that require high precision.
The process uses pre-programmed computer software to control the movement of machinery and tooling. Computer controls can operate complex machinery such as grinders, milling machines, planers, and lathes, allowing for high precision and repeatability in part manufacturing.
Small batch CNC machining is in stark contrast to mass production, which requires the production of thousands or millions of identical parts.
It provides a cost-effective solution for businesses that need high-quality, custom parts in small batches. High levels of customization, rapid prototyping, and reduced inventory costs make small batch CNC machining an attractive option for many businesses.
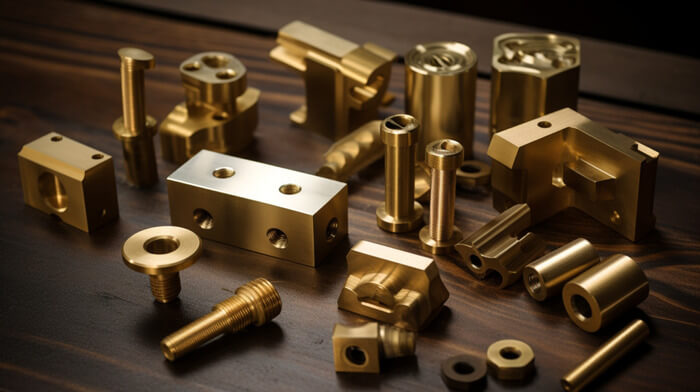
2.The Evolution of CNC Machining: From Mass Production to Small Batch
CNC machining has a long history, originating from the era of mass production. As technology advances and manufacturing complexity increases, there has been a clear shift in production scale toward smaller, more customized batches. This shift stems primarily from the growing demand for manufacturing precision and adaptability.
Driven by changing market trends and demand for customization, the manufacturing industry has shifted from mass production to agile small batch production.
Small batch production allows manufacturers to flexibly adapt to market fluctuations, thereby reducing inventory expenses and waste. This approach also facilitates rapid prototyping and customization, effectively meeting the needs of niche markets.
The adoption rate of small batch CNC machining has surged with technological advances, enabling efficient, precise manufacturing and ensuring fast delivery of products that meet unique customer specifications.
3.Advantages of Small Batch CNC Machining
Small batch CNC machining offers many advantages: greater flexibility, lower inventory costs, easier customization, rapid prototyping, and higher precision.
These advantages can result in significant cost savings and increased customer satisfaction, making small batch CNC machining an attractive option for many businesses.
1) Greater Flexibility
Unlike mass production, small batch CNC machining enables manufacturers to quickly and efficiently adapt to changes in design or customer requirements. This flexibility can provide a significant competitive advantage in markets where customer needs and trends evolve rapidly.
2) Reduced Inventory Costs
Small batch CNC machining enables manufacturers to produce the products they need on time. This strategic, just-in-time approach minimizes storage costs for both finished goods and raw materials, resulting in significant economic benefits.
3) Rapid Prototyping
Small batch CNC machining is ideal for prototyping. Companies can test multiple designs, quickly adjust, and then run a new batch of prototypes, speeding up the product development cycle.
4) Easier Customization
Since each batch is smaller, it is easier to customize each product batch to meet specific customer requirements. This is particularly beneficial in industries where customized solutions are the norm, such as medical device manufacturing or aerospace engineering.
5) Superior Precision
CNC machining offers high precision and consistency. This is essential for manufacturing high-quality parts. In small batch production, the quality of each part can be more closely monitored, ensuring that each part meets strict standards.
6) Small batch production, cost-effective
For small-volume production, small batch CNC machining is more cost-effective than traditional methods. It saves initial setup costs without the need for physical tools such as molds or dies. This makes small batch CNC an affordable option for small-volume production.
7) Faster time to market
Small batch production can speed up product launch, providing companies with a key advantage in today’s fast-paced, competitive environment. By producing and delivering products faster, companies can respond to market demands more quickly.
8) Enhanced innovation
With small batch CNC machining, companies can innovate more frequently. It is easier to test and implement new design features or materials on a small scale before integrating them into wider production. As a result, companies can always stay at the forefront of technology and design trends.
9) Reduced risk
With small batch production, companies can reduce the risk of excess inventory when product sales do not meet expectations. In addition, it allows manufacturers to respond quickly to any design or functional defects discovered after the product is released, minimizing potential recalls or customer dissatisfaction.
By leveraging these benefits, companies can efficiently create high-quality, customized products that meet customer needs while managing their bottom line.
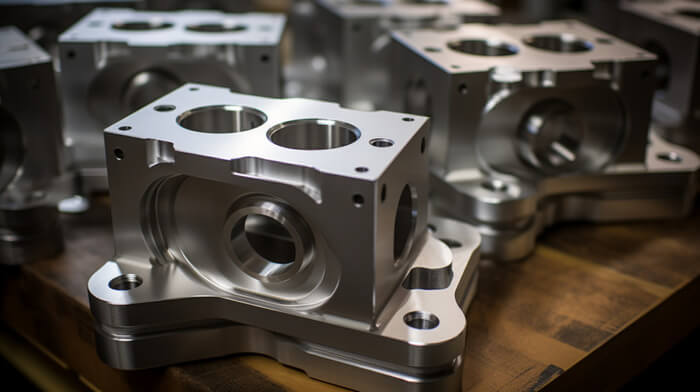
4.Limitations and Disadvantages of Small Batch CNC Machining
While the benefits of small batch CNC machining are numerous, it is critical to understand the limitations of low-batch CNC machining. Compared to mass production, challenges with low-batch machining include potentially higher unit costs and the need for more complex planning and management to ensure efficient operations.
1) Higher Unit Costs
In small batch production, unit costs may be higher because production expenses are spread over fewer items. This can pose challenges for businesses with lower profit margins or those producing cost-sensitive consumer products.
Despite these considerations, flexibility and customizability are often more valuable than increased unit costs.
2) Increased Management Efforts
Small batch CNC machining requires close management and monitoring to ensure efficiency. Each batch may require individual setup and programming, resulting in more complex logistics and the possibility of human error.
3) Dependence on Supplier Reliability
With just-in-time production, there is a heavy reliance on suppliers to deliver materials on time. Any delays or errors from suppliers can disrupt the entire production schedule.
4) Limited Economies of Scale
The economies of scale that typically come with mass production may not be realized with small batch production. This means that businesses may not be able to significantly reduce costs as production increases.
5) Inefficient Large-Batch Production
If your company needs to produce large quantities of the same product, small batch CNC machining may not be the most efficient or cost-effective method. In this case, traditional manufacturing methods may be more appropriate.
6) Skilled Labor Required
Skilled labor is required to operate and program CNC machines. Businesses must invest in training employees or hiring experienced operators, which increases overall operating costs. Understanding these limitations can help businesses make more informed decisions about whether small batch CNC machining is right for their specific needs and circumstances.
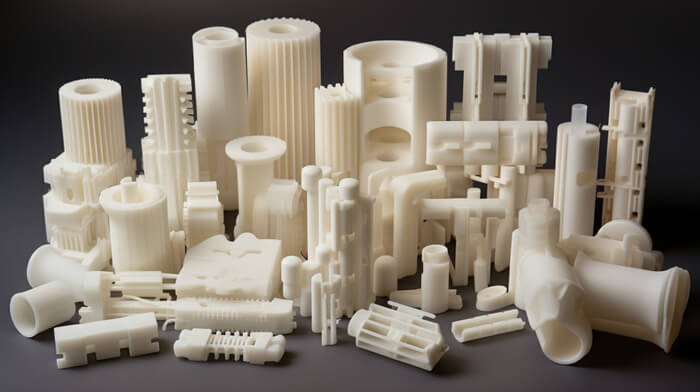
5.Precision is critical: The role of precision in small batch CNC machining
In the world of small batch CNC machining, precision is critical. The ability to perform accurate, repeatable cuts is integral to the quality of the final product.
The inherent precision of CNC machining shines in small batch production, providing excellent repeatability even for complex designs.
1) Quality Assurance
One of the main benefits of small batch CNC machining is the ability to maintain consistent high quality across all production units. CNC machines follow programming instructions exactly, which means that each part will accurately match the original design.
This level of precision ensures that each part produced is virtually identical to the last, providing consistent quality, which is critical in industries such as aerospace, medical, and automotive where even minor errors can cause serious problems.
2) Reduced Waste
Maintaining precision significantly reduces errors and defective parts. When precision is maintained, errors and defects are greatly reduced. This means less waste and more efficient use of materials. This saves on raw material costs and is also beneficial for sustainable development.
3) Enhanced Complex Design Capabilities
The high precision of CNC machining allows for the production of complex designs that would not be possible through manual processes. This capability opens up new possibilities in product design, allowing manufacturers to create parts with complex geometries, tight tolerances, and intricate features.
4) Improved Customer Satisfaction
When people receive a product, they expect it to work properly. Being precise during the manufacturing process means there is less chance of errors. As a result, customers will be happier and trust your product more.
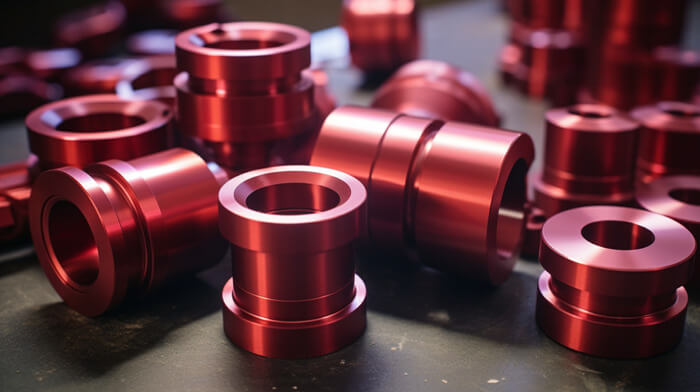
6.Customization and Flexibility of Small Batch CNC Machining
One of the great benefits of small batch CNC machining is its customizability and flexibility. With this approach, manufacturers can quickly adapt to design changes and meet niche or unique customer requirements, providing customized solutions that meet customer needs.
1) Customization
In manufacturing, customization refers to modifying the design, features, or specifications of a product to meet specific customer requirements. In small batch CNC machining, the level of customization that can be achieved is very high.
With CNC machines, you are not limited by fixed molds or tools. As long as your design can be programmed into the CNC machine, you can create it.
This is particularly beneficial in industries such as medical technology, where customized, patient-specific implants can significantly improve treatment outcomes.
For example, a company that produces prosthetics can use small batch CNC machining to create a one-of-a-kind product for each customer. By taking precise measurements and translating them into digital designs, they can create prosthetics that fit the customer exactly, improving comfort and functionality.
2) Flexibility
Manufacturing flexibility refers to the ability to adjust the CNC machining process to changes in design, order volume, or materials without incurring significant costs or delays. This is where small batch CNC machining really shines.
Take, for example, a company that produces custom automotive parts. With the flexibility of the CNC machining process, the company can quickly switch between different designs.
If a customer requests a design or material change after the first batch is produced, the company can reprogram the CNC machine to accommodate these changes.
Compared to other production techniques, small batch CNC machining avoids costly and time-consuming re-machining.
Similarly, imagine a startup electronics company launching a new product. By leveraging small batch CNC machining, they can generate initial prototypes, conduct tests, collect user feedback, and modify the design based on that feedback.
This flexibility allows for fast and efficient iterations until the final product meets both their quality standards and market expectations.
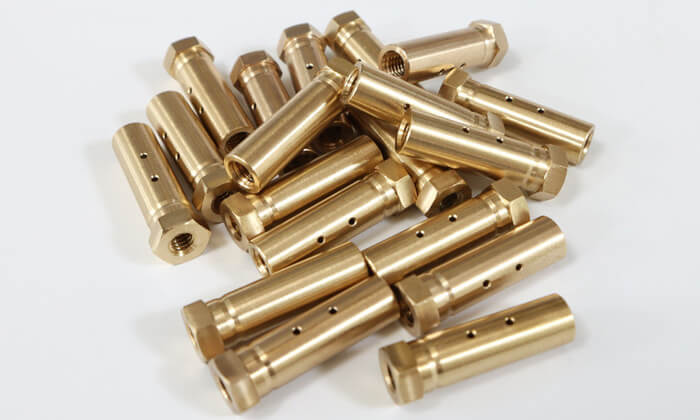
7.Small batch CNC machining in different industries
Small batch CNC machining is a revolutionary machining process that is transforming industries around the world, from aerospace to medical and automotive.
Its wide range of applications and adaptability have become an important factor in driving industry progress, promoting global innovation, and improving efficiency across the board.
1) Aerospace
Due to the critical nature of the products, this industry has extremely high requirements for precision and quality. With small batch CNC machining, aerospace manufacturers can produce highly complex parts with tight tolerances, such as turbine parts or lightweight structural components.
2) Medical
Small batch CNC machining is essential for the production of medical devices, especially those that require customization, such as prosthetics or implants.
For example, a company specializing in prosthetics can use small batch CNC machining to produce customized parts based on each patient’s unique anatomy, thereby improving fit and comfort.
3) Automotive
In the automotive industry, small batch CNC machining is used to prototype new parts, customize components for high-performance vehicles, and manufacture complex components such as engine parts.
For example, a custom car shop can use small batch CNC machining to create customized parts to meet specific customer requirements.
4) Electronics
Electronic component and device manufacturers often use small batch CNC machining to prototype and produce parts such as housings, connectors, or heat sinks.
A startup developing a new smartphone might use small batch CNC machining to prototype various designs before settling on the final product.
5) Energy
Companies in the energy sector, especially those in renewable technologies such as wind or solar, use small batch CNC machining to produce efficient and reliable components.
A wind turbine manufacturer might use small batch CNC machining to produce custom gear parts to increase energy production efficiency.
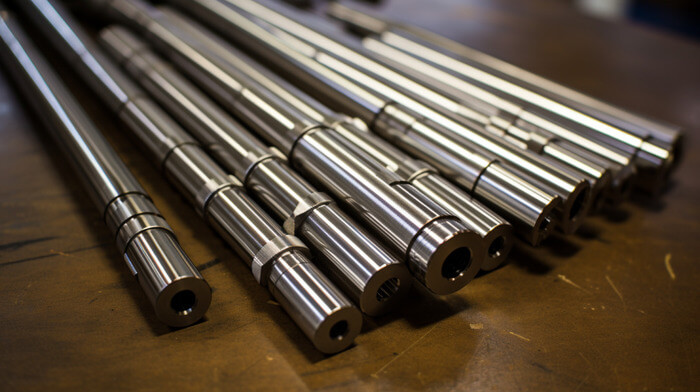
8.What design criteria need to be considered for small batch CNC machining?
When performing small batch CNC machining, specific design criteria must be considered. These considerations include the materials used, the complexity of the design, tolerances, and finishing processes.
Keep in mind that these criteria may vary depending on the specific requirements of each project.
1) Understanding Material Properties
Different materials behave differently during machining. It is critical to understand the properties of the materials used, such as hardness, brittleness, and heat resistance, as these properties affect the design and CNC machining process.
2) Specify tolerances only when necessary
Overspecifying tolerances can increase costs and production time. Use standard tolerances whenever possible and specify tighter tolerances only for critical features.
3) Consider tool accessibility
Make sure all areas of your design are accessible to standard CNC tools. Complex internal features or undercuts may require specialized tools, which can increase costs.
4) Simplify your design
Strive for simplicity in your design while maintaining functionality and aesthetics. Strive to eliminate unnecessary complexity, as complexity can make the CNC machining process more challenging and can increase costs.
5) Avoid thin walls and fine features
Thin walls and fine features can be difficult to machine and may lack durability. If your design requires such features, you must consider the limitations of your chosen material and the capabilities of your CNC machine.
6) Avoid sharp internal corners
Rounding internal corners enhances part strength and increases tool life.
7) Optimize multi-axis machining
If you are using a multi-axis CNC machine, design your part to take full advantage of the machine’s capabilities. This helps reduce the need to reposition the part, saving time and reducing errors.
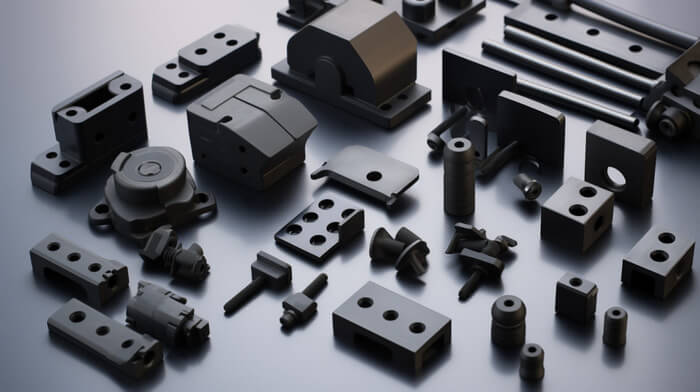
9.How to Choose the Best Small batch CNC Machining Service Provider from China?
China is a big player in the CNC machining space, but choosing a CNC machining service provider can be a daunting task. Key factors to consider include quality assurance, pricing, production capabilities, customer service, and feedback from previous customers.
1) Experience and Expertise
Look for a supplier with a proven track record in small batch CNC machining. They should have experience in your specific industry and be familiar with the types of materials and designs you will be working with.
2) Quality Assurance
Quality is critical to CNC machining. Ask potential suppliers about their quality control procedures. They should have strong measures in place to ensure consistency and accuracy, such as regular equipment maintenance and inspection processes.
3) CNC Machining Capabilities
It is critical that the supplier has advanced CNC machines that can handle the complexity of your design with the highest precision. If your parts require special capabilities such as multi-axis machining or high-speed machining, confirm that the supplier is equipped with the necessary machines.
4) Communication
Smooth communication is key to a smooth manufacturing project. Your supplier should respond quickly when you have questions, keep you informed of how things are going, and be ready to work with you to resolve any issues that arise. Keeping an open dialogue shows that they value your business and care about your satisfaction.
5) Turnaround Time
If you need parts quickly, ask about the supplier’s typical delivery time. However, remember that quality should never be sacrificed for speed.
6) Cost
While cost shouldn’t be your only consideration, it’s still important. Request detailed quotes from several suppliers to ensure you’re getting a fair price. But be wary of suppliers that offer significantly lower prices than others, as this may indicate lower quality.
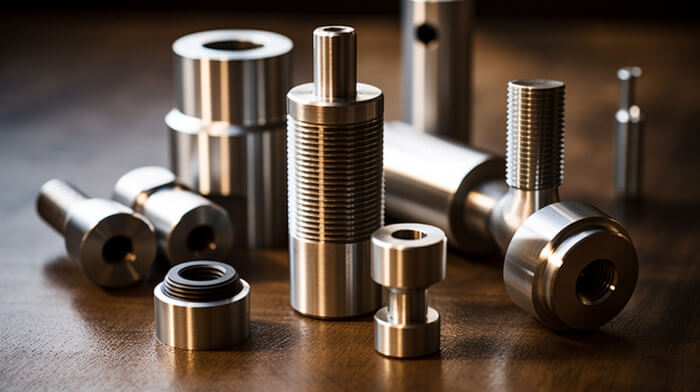
10.Conclusion
In this exploration of small batch CNC machining, we uncovered its fundamentals, highlighted its benefits, touched on its limitations, and demonstrated its wide range of applications across different industries. We offered wisdom on effective design strategies and provided insights into selecting an exceptional service provider.
If you are looking for an experienced CNC machining manufacturer, Xavier is your ideal choice. The Xavier team is well-equipped to provide high-quality CNC machining solutions. If you need more information or to discuss your machining needs with us, please feel free to contact us.
1 Comment