What is Precision Machined: Definition, Benefits, and Applications
Our world is surrounded by fast-moving, complex technology. Central machining is a CNC machining production company that focuses on providing high-quality workmanship.
In our daily lives, we can see many complex parts, such as gears and components inside machines, which makes us wonder what it takes to make them.
For most of these products and how they are made, the answer is the same: CNC precision machined.
Computer numerical control (CNC) processes are the cornerstone of modern industry, automating the production of parts at unimaginable production speeds. CNC precision machined goes a step further, increasing accuracy and streamlining the manufacturing process.
This article will discuss precision machined, how to do it, the tools needed, and more.
1.What is precision machined?
Precision machined is a machining process that uses computer-controlled machine tools to produce parts. It is a high-speed machining process used to make parts that require tight tolerances, high complexity, or both.
Precision machined can be done by a skilled precision machinist operator or a high-speed robot.
It is a subtractive manufacturing process where a machine starts with a block of material and removes material from it using cutting tools. Precision machined is often used to make a variety of parts that fit and work together.
Successful precision machined relies on a combination of two factors:
1. First, high-quality precision machined requires high-end cutting tools that can carefully remove material to match the desired product dimensions.
2. Second, the process requires a computer numerical control (CNC) machine. CNC machines typically use high-speed robotic technology to automatically control the cutting tool, indicating where to cut/mill on the workpiece.
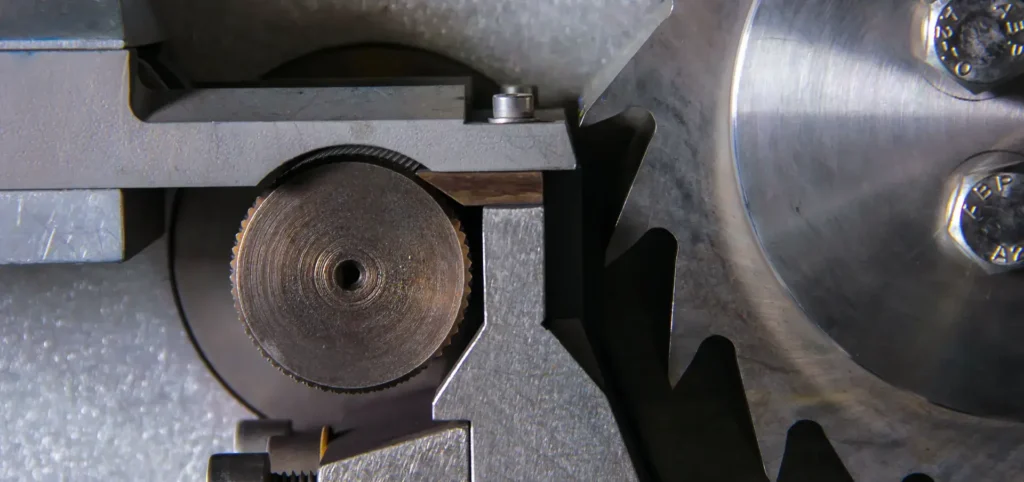
2.What are the steps in the precision machined process?
Most precision machined companies follow a similar series of steps for various types of parts.
1) Design a Graphic Model
A graphic model is required to create any part. This can be achieved through computer-aided design (CAD) software. CAD software enables designers to create 2D and 3D models of any part for manufacturing.
Designs usually start with hand-drawn sketches to understand the basic concept of the part. Computer-aided design (CAD) designers then refer to these sketches to create dimensionally accurate graphic models.
For computer-aided design, there are many popular software programs, both free and paid. Manufacturers can also outsource the design process for any complex design development.
2) Convert CAD to CAM
Computer-aided design creates a graphical representation of a part in a digital format. This representation is easy for designers, operators, and manufacturers to understand. However, the CNC machines used to manufacture the parts do not directly understand this digital format.
The machine understands coordinates in order to move the cutting tool or to move the workpiece. Therefore, CNC machines require that the part design is in a suitable format to provide the necessary manufacturing instructions.
Computer-aided manufacturing (CAM) software is used to create a readable format for CNC machining. CAM software takes the CAD model and converts it into a CAM format that the CNC machine can understand.
Computer-aided manufacturing (CAM) software uses two types of codes – G and M codes. G codes control the coordinates of the cutting tool. M codes control auxiliary functions of the machine, such as turning the coolant flow on or off.
3) Machine setup
Once the design is ready in CAM format, it is time to perform machine setup. This usually requires calibrating the machine tool and mounting the workpiece on the machine.
The machine tool may vary depending on the workpiece material and the design of the final part. There are various precision machined tools that can be used for different purposes.
During this step, it is important to properly tighten all fixtures and ensure that machine parameters are acceptable, such as coolant levels.
4) Perform Machining
Once setup is complete, the machine program can be executed. Most CNC machines have displays to monitor the program and adjust various parameters. Once the program is executed, the CNC machine will begin the precision machined process.
5) Finishing
Once a part has been made using a precision machine, it can be removed. Depending on the requirements, the part may be sent for secondary processing, such as grinding or polishing.
However, in most cases, the finished product made using precision machined does not require any secondary processing.
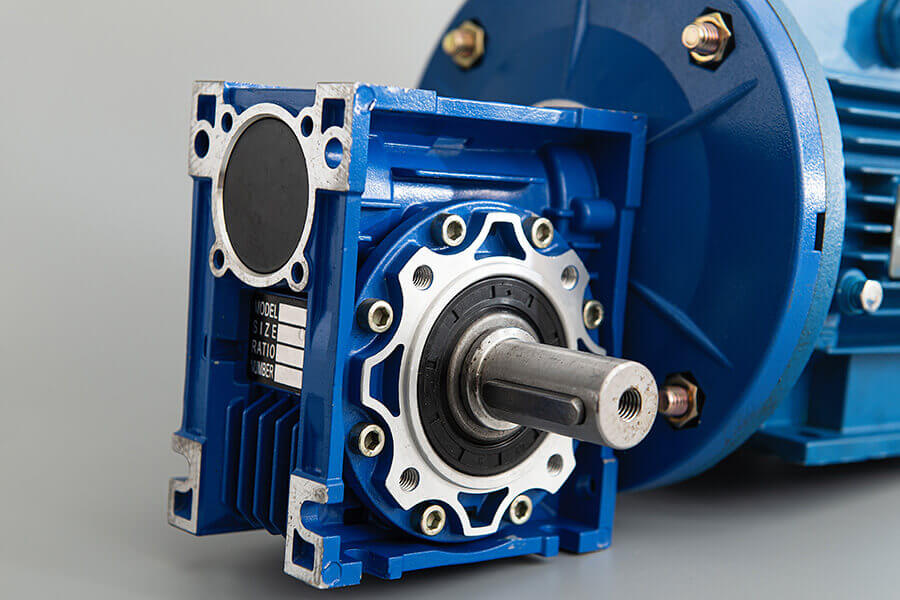
3.What are the different methods and equipment for precision machined?
Because precision machined has a wide range of applications, there are many types of machines and equipment for precision machined. Different parts require different types of cutting, so a range of cutting tools have been developed.
1) CNC Milling Machines
CNC milling is a subtractive manufacturing process that uses a rotating tool to remove material from the workpiece. The direction, angle, pressure, and speed of the cutting tool can be varied to produce different cutting effects.
There are many types of CNC milling machines such as bed-type, box-type, C-frame, floor-standing, gantry, horizontal boring, knee-type, planer, turret, and ram milling machines.
2) CNC Turning
In CNC turning, the workpiece rotates along a central axis and a linearly moving cutting tool removes material from the workpiece. Unlike CNC milling machines, the cutting tool is usually non-rotating. Most commonly, a single-point cutting tool is used in this process.
3) Precision Grinding Machine
Precision grinding is one of the final manufacturing processes after machining a part or component. In precision grinding, abrasive grinders or grinding wheels create a very flat surface on the machined part with a very smooth finish.
Also, precision grinding can help produce a surface with tight tolerances on the finished product by removing a small amount of excess material.
4) CNC Drilling Machine
In a CNC drilling machine, the workpiece remains stationary while a rotating drill moves around and drills holes in the workpiece. These holes may be used for part assembly or aesthetic purposes.
CNC drilling machines can create holes of different sizes by changing the size of the drill bit. Hole depth can be adjusted by controlling the machine calibration.
5) Multi-axis CNC machining
Multi-axis CNC machining is a complete set of machining systems. The cutting tool can move in four or more directions. Multi-axis CNC machining can use a variety of cutting tools and processes to create complex parts, such as milling, water jet cutting or laser cutting.
6) Electrospark machining
In electrospark machining (EDM), metal is shaped with the help of electric sparks (sparks). Other aliases for this process include spark machining, die engraving, wire cutting, wire cutting or spark etching.
EDM is only suitable for metals because metals conduct electricity. It uses two electrodes – the tool electrode and the workpiece electrode. This machining method brings the two electrodes close to each other, but they do not make physical contact.
This creates an arc between the electrodes, which increases the temperature of the tool electrode and melts the metal. EDM applications usually involve the hardest metals because machining these metals using milling machines is difficult. EDM is often used to create holes, slots and tapers on gears.
7) Swiss Machining
Swiss machining is an improvement over traditional lathes. It uses a specialized Swiss-made CNC lathe to cheaply and accurately machine parts.
In traditional lathes, the headstock is fixed and simply rotates the workpiece. However, in Swiss machining, the headstock allows linear motion, providing more precise and complex machining options.
In addition to the moving headstock, there is a sliding guide sleeve that moves along the longitudinal axis of the workpiece. The guide sleeve provides support for the workpiece to achieve high-precision machined.
8) CNC Laser Machine
CNC laser machining uses a high-frequency laser beam to cut or engrave materials. Unlike EDM machining, laser machining can machine non-metals as well as metals.
9) Mill-Turn CNC Center
CNC mill-turn centers, or CNC mill-turn machines, combine milling and turning operations. Traditionally, milling and turning are done on separate CNC machines.
However, merging them into one machine can greatly simplify the manufacturing process. CNC mill-turn centers come in two configurations – vertical and horizontal. Vertical configurations are considered more stable due to the effect of gravity on the setup.
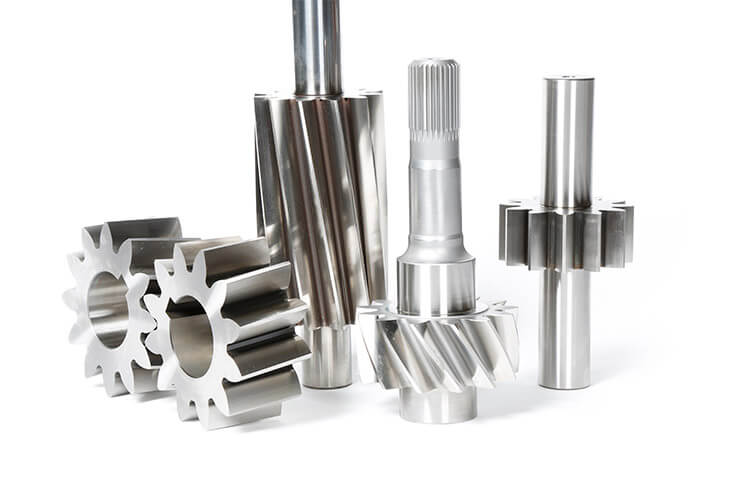
4.What are the benefits of CNC precision machined?
The cost of CNC precision machined may be slightly higher than traditional machining methods. However, the benefits brought by the process are worth the extra investment. Here are some of the benefits:
1) Tight tolerances
Tight tolerances are the main reason for using CNC precision machined. Tolerance is also called dimensional accuracy. It refers to the slight deviation between the dimensions of the machined part and its CAD blueprint.
CNC precision machined uses specialized processes and cutting tools to minimize tolerances. This improves the accuracy of the part compared to the original blueprint.
① What are precision machined tolerances?
There are four different types of machining tolerances in commonly performed precision machined:
1. One-sided tolerance: In this type of tolerance, the dimension is allowed to vary in only one direction. The tolerance limit can be higher or lower than the expected dimension.
2. Two-way tolerance: In this type of tolerance, the dimension is allowed to vary in both directions. The tolerance limit can be higher or lower than the expected dimension.
3.Compound tolerance: The compound tolerance is the final tolerance calculated by adding or subtracting the tolerances of the different sizes that make up the part.
4.Limit size: Instead of defining the size of the required dimension, it defines the upper and lower limits of the dimension. For example, the preset dimension can be in the range of 20 mm to 22 mm.
2) High accuracy
Strict tolerances directly mean that the final product produced by precision machined will have high accuracy. Precision machined is usually used for parts that need to interact with other parts and components.
Therefore, high accuracy is essential for these specific parts to function perfectly in the later stage.
3) High repeatability
The concept of repeatability is one of the important cornerstones of modern manufacturing. Every part manufactured by a certain process is designed to look exactly like other parts to the end user.
Any deviation from such a replica is usually regarded as a defect. Precision machined is attractive in this regard. With high-precision CNC machining, each part is exactly the same as the original, and the deviation is negligible.
4) Low production cost
Since precision machined has no deviation, there are fewer production defects. Therefore, the process reduces the rejection rate of parts. Therefore, the material cost is low.
In addition, as an automated computer-aided manufacturing process, labor costs can be reduced. The reduction in labor and material costs means that CNC machining has a lower production cost than any alternative.
5) Speed and Efficiency
Precision machined involves high-speed robots that can make parts faster than manual manufacturing on traditional lathes.
In addition, parts have high precision and close tolerances, so no secondary processing is required. This can reduce production time and increase productivity and efficiency in the shop.
6) Safety
CNC machines replace manpower with computer numerical control systems, eliminating the risk factor of human error in the cutting process. Workers can switch to technology-intensive work such as CNC design operations.
5.What are the applications of precision machined?
Precision machined is the foundation of many industries, whether it is used to process tools or manufacture final products.
Some applications of precision CNC machining include:
1) Prototypes
Precision machined is used to make prototypes for all industries. Prototypes need to reproduce the intended design with high accuracy to depict product features. Precision machined is an ideal way to meet these standards.
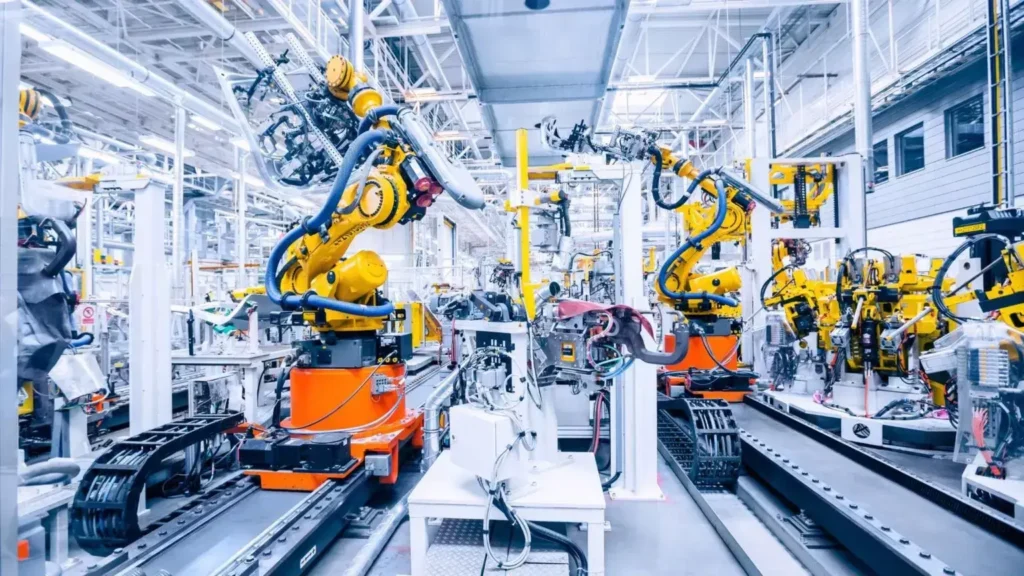
2) Automotive
The automotive industry requires complex parts such as gears and engine components, axles, nuts, etc. These parts for two-wheelers, cars, trucks, ships, and airplanes are all made with precision machined tools.
3) Medical Industry
Medical technology is becoming increasingly complex. There are automated tools and equipment in the medical industry that can even perform surgery. These devices require complex machining at a microscopic level, and precision machined makes it possible.
4) Aerospace
The aerospace industry uses some of the most advanced equipment, materials, and technology. It requires a machining process that is not only highly accurate but also capable of handling the toughest materials.
Precision machined provides a simple solution to manufacturing a wide range of parts in the aerospace industry, from prototypes to full-size parts.
5) Defense Industry
The defense industry has similar requirements to the aerospace industry. It requires the toughest materials and requires high-quality precision machined. The applications range from new weapon prototypes to entire missile systems.
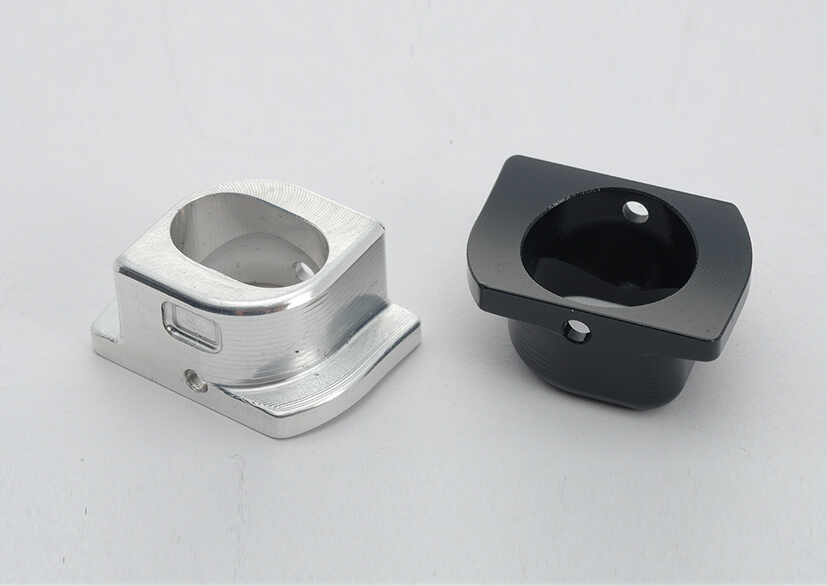
6.Materials Suitable for Precision machined
Precision machined is suitable for hundreds of different metals, plastics, and other composite materials. Here is a list of some common materials that are precision machined:
1) Metals and alloys
1. Aluminum
2. Bronze
3. Brass
4. Copper
5. Titanium
6. Steel
7. Stainless steel
8. Carbon steel
9. Tool steel
10. Exotic alloys
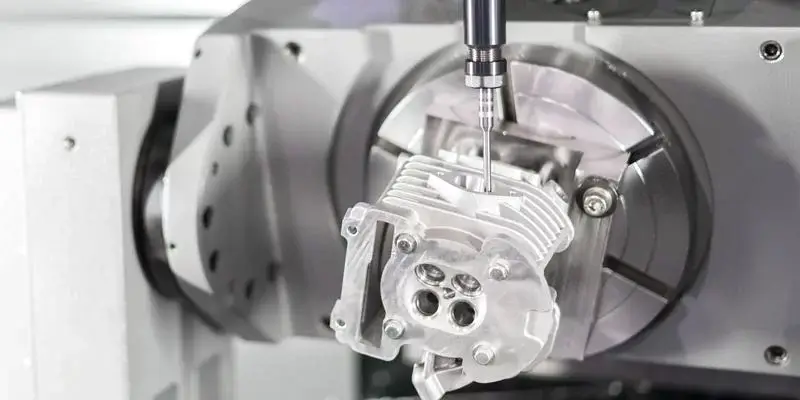
2) Plastics and other non-metals
1. Polyamide (PA)
2. Polycarbonate (PC)
3. Acrylonitrile butadiene styrene (ABS)
4. Polymethyl methacrylate (PMMA)
5. Polyoxymethylene (POM)
6. Glass
7. Graphite
7.What is the typical cost of precision machined?
In general, there is no exact cost for precision machined because the cost varies based on a variety of factors. CNC machining has many different components that have a variety of cost options.
For example, the number of axes in a precision machined device is optional. A multi-axis machine can cost two to three times as much as a three-axis machine based on an hourly rate.
There are many other costs, such as the fees paid to the designer for the computer-aided manufacturing (CAM) blueprints, the hourly labor cost of the precision machinist based on the precision machinist’s skills, and so on.
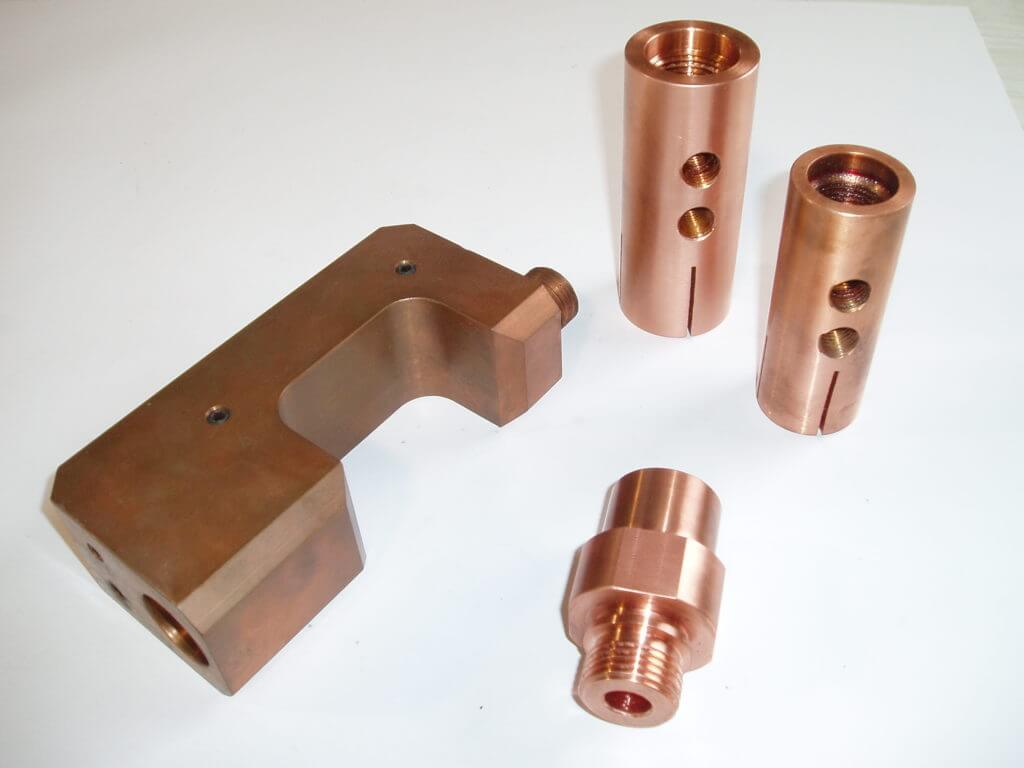
8.Conclusion
Now you know the answer to the question: What is precision machined? and how most precision machined companies operate. Precision machined is no longer an optional manufacturing process that can provide better results.
It has become a must-have technology for complex CNC machining tasks that must work together. When perfection is required on a microscopic level, every millimeter counts. The only way to achieve this perfection is through precision machined. Precision machined is the best way to get the most bang for the buck without compromising dimensional accuracy. That’s why this process has become the preferred manufacturing method for making prototypes or mass-produced parts.
If you are looking for an experienced precision machining manufacturer, Xavier is your ideal choice. The Xavier team is well-equipped to provide high-quality precision machining solutions. If you need more information or to discuss your machining needs with us, please feel free to contact us.