CNC Precision Machining Detailed Guide
Many industries around the world today rely on CNC precision machining to develop high-quality custom parts that meet detailed requirements. Among them, kibblewhite precision machining tools have a certain reputation. Precision is critical for a variety of applications and parts need to meet strict tolerances.
Precision CNC machining involves the use of computer programs to produce parts that meet precise specifications. It combines various techniques and materials. Therefore, a detailed understanding of the concept is required to help you get the most out of your project.
This guide discusses the precision machining process, the different machine tools used, their benefits, and applications. If you want to get custom precision machined parts, read this article till the end.
1.What is CNC precision machining?
CNC precision machining refers to the process of creating components by cutting and shaping raw materials. Computer-aided design (CAD) and computer-aided manufacturing (CAM) blueprints help specify the appropriate cutting process.
These programs are crucial during the design phase as they often contain detailed 3D outlines that ensure the successful creation of the part.
High-precision machining is now an important aspect of the manufacturing industry. It requires the collaboration of professional designers and expert engineers. Designers are responsible for creating the design and translating it into manufacturing instructions.
Machinists then send the final coded instructions in machine language to the CNC equipment to begin the manufacturing process.
Additionally, there are many parts that require precision machining, including automotive parts, medical devices, electrical components, and more. Using advanced machine tools in precision machining processes will help in manufacturing complex parts with complex geometries.
Typical CNC machines have a tolerance standard of +/-0.005 inches. However, CNC precision machining can achieve tolerances of +/-0.002 inches to +/-0.0002 inches.
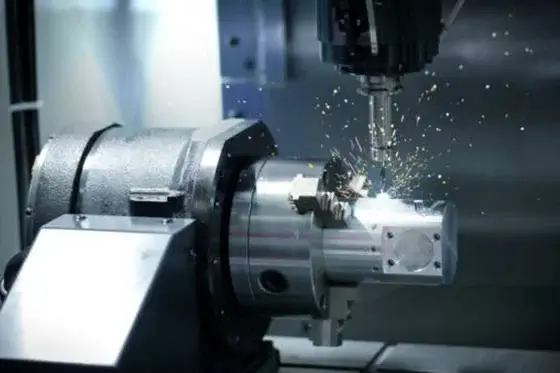
2.Common Types of Precision CNC Machine Tools
Precision machining processes use a variety of techniques to deliver quality parts. Each technique uses different machining equipment to achieve quality results. Some processes involve one CNC machine while some involve multiple machines.
Some of the machines used for effective CNC precision machining operations include:
1) CNC Milling Machines
These machines feature the ability to reshape stationary raw materials using a rotating cutting tool. These machines help in producing a variety of shapes, primarily face milling features and perimeter milling features.
Face milling features include flat surfaces and shallow cavities, while perimeter milling features are deeper cavities such as threads and grooves. Precision CNC milling machines mainly help to manufacture square and rectangular parts with various features.
2) CNC Lathes and Turning Machines
Unlike milling machines, these machines turn or rotate the raw material while the cutting tool remains stationary during the operation.
In this case, the cutting tool moves linearly along the turning bar stock. Therefore, they are able to remove material around that circumference to achieve the desired diameter and features.
CNC Swiss Lathes are a type of CNC lathe. These machines rotate the workpiece and slide it axially into the machining tool via a guide bushing.
With a CNC Swiss Lathe, you can ensure that the workpiece is better supported while the machine forms the part. This allows for tighter tolerances on the component.
CNC Lathes can machine both external and internal features on parts. These features include holes, reaming and drilling, broaching, tapers and threads, tapping, and slots. Therefore, you can machine parts such as bolts, screws, valve cores, shafts, etc. on these machines.
3) CNC Drilling Machines
Drilling is a precision machining process that uses a rotating drill to machine a cylindrical hole in the material. These drill bits are multi-point devices that keep chips away from the workpiece, ensuring advanced holemaking.
Common examples of drill bits for precision CNC machining include:
- Pilot drills. They help to drill shallow or pilot holes.
- Drill presses. These are important for custom drilling tasks.
- Screw machine bits. They can drill holes without an initial pilot hole.
- Clamp-on reamers. They help to enlarge previously created holes.
- Peck drills. They reduce the amount of chips generated from the workpiece.
4) Electrical Discharge Machine (EDM)
Electrical discharge machining (EDM) involves using controlled electrical sparks to shape a material into a desired shape. Many machinists also refer to it as spark etching, spark machining, die carving, or wire cutting. During this process, a technician places the part under an electrode wire.
The programmed machine then sends an electric current from this wire, generating high heat. The heat melts the material, which is then flushed with an electrolyte to form the desired feature or shape.
Additionally, EDM can create precise slots, micro-holes, angled or tapered features, and a variety of other complex features on a workpiece. It is an ideal process for hard metals that are typically difficult to machine.
5) CNC Plasma Cutters
These tools use a high-powered, computer-controlled plasma torch to help cut the material. These plasma torches can reach temperatures of over 50,000 degrees Fahrenheit. As a result, they can easily melt the workpiece and create cuts in the material.
The materials used by plasma cutters must be conductive. Such materials include steel, aluminum, stainless steel, copper, and brass.
6) CNC Precision Grinders
If you need CNC precision machining that meets smooth surface roughness requirements, you will need precision grinders. These grinders are essential for making parts with exceptional precision.
Typically, CNC lathes and CNC milling machines usually create a rough surface first. Then, grinders are needed for the final surface finishing.
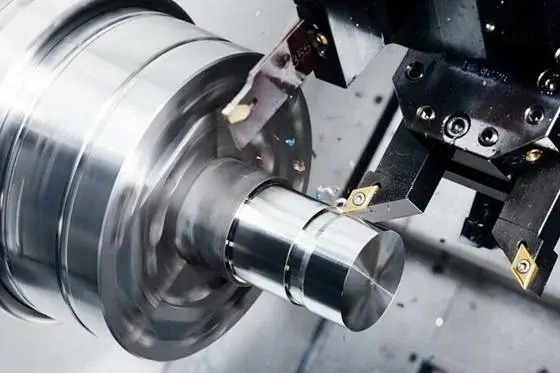
3.Materials Used in CNC Precision Machining
Precision machining processes can handle a wide variety of materials. These CNC machining materials are generally classified into the following categories:
1) Metals
CNC precision machining is suitable for a wide range of metals, regardless of their hardness or strength. The process uses advanced technology to ensure that these metals are effectively machined.
Common metals for CNC precision machining are:
- Aluminum
- Steel
- Stainless steel
- Copper
- Brass
- Bronze
- Titanium
2) Plastics
CNC precision machining can process basic or engineered plastic materials. Regardless of the plastic you choose, the process provides a quality product at a competitive price.
Some plastic CNC machining raw materials include:
- Acrylonitrile Butadiene Styrene (ABS)
- Polycarbonate (PC)
- Polymethyl Methacrylate (PMMA)
- Polyoxymethylene (POM)
- Polyamide (PA)
We have highlighted the most common precision CNC machining materials. However, Xavier offers a comprehensive and extensive list of materials to meet custom precision machining needs.
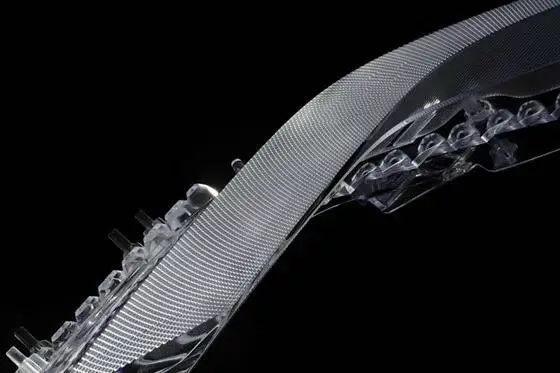
4.Advantages of CNC Precision Machining
Precision and repeatability are critical requirements for cost-effective and high-quality machining. Generally speaking, CNC precision machining excels in multiple aspects that help meet performance and quality requirements.
Some of the advantages of the process include:
1) Best-in-class machining technology
CNC precision machining equipment is an advanced technology that meets the standards of Industry 4.0. It eliminates the need for excessive labor and operating heavy machinery.
Regardless of the CNC machine tool used, computer programs now automate most operations. They are “live operators” who can manipulate cutting tools and process different raw materials into the desired finished products.
2) Improved performance and reliability
While some applications can accept traditional machining results, other applications have strict tolerance requirements. These requirements require high-precision machining.
In addition, most industries often require many identical parts. This is only possible through the repeatability of CNC precision machining. Quality processes are always in place, and CNC machines cut similarly and maintain the same quality for all parts.
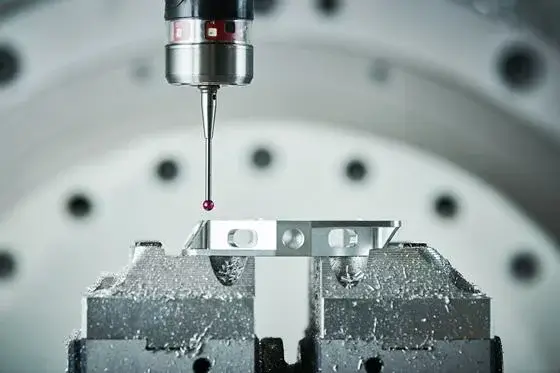
3) Wide range of applications
Precision machining processes are compatible with a wide range of materials, including high-grade metals and plastics. This flexibility helps businesses of different sizes compete and offer custom designs and parts.
In addition, repeatedly achieving tight engineering tolerances helps build customer confidence. CNC precision machining benefits multiple industries, including automotive, metalworking, aerospace, marine, agriculture, consumer goods, and more.
4) Reliable part quality
CNC precision machining quality is unmatched. It eliminates any variation produced in traditional machining due to the use of computer numerical control.
The process can run for hours with minimal maintenance and advanced software to meet design needs.
Therefore, even the most complex parts can be manufactured with advanced processes to ensure the highest quality that exceeds customer expectations.
5) Reduced cycle time and reduced labor costs
CNC precision machining can meet higher production needs because it has enhanced machining automation and programming capabilities without interrupting the use of the machine. High-precision machines are designed with high accuracy to provide repeatable results.
However, traditional machining requires manual monitoring and adjustment of tools and operating speeds. CNC machines can run programs created offline.
One machine operator can switch machining centers and run various productions. The operator maintains the load parts and tools and performs offline deburring and quality control.
Therefore, the structure requires only a few operators to monitor the process, thereby reducing labor costs. Likewise, it ensures faster creation of components, regardless of quantity.
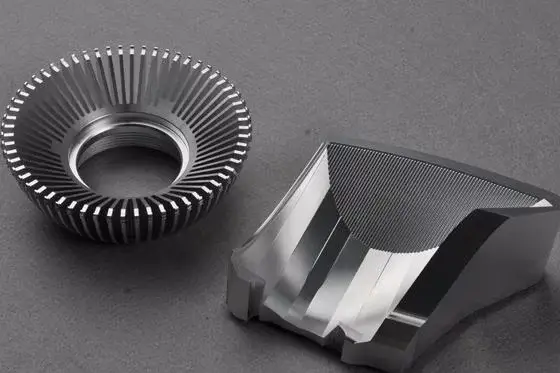
5.Applications of CNC Precision Machining
CNC precision machining has become a well-known technology in various industries due to its fast production speed, cost-effectiveness, wide range of applications, and high product quality. Its advantages are very useful in these industries.
1) Automotive Industry
The automotive industry is a revolutionary field in today’s world. New innovative automotive parts are introduced every day, and vehicles are constantly updated.
Automotive companies prefer to use CNC precision machining to develop quality prototypes before going into full production. This allows for functional market testing and changes to the design if necessary.
2) Medical Industry
Equipment in the healthcare industry requires the highest level of precision due to its tolerance specifications. Tools such as orthotics, safety enclosures, implants, MRI matches, etc. usually have tight tolerances.
Only CNC precision machining can help achieve this.
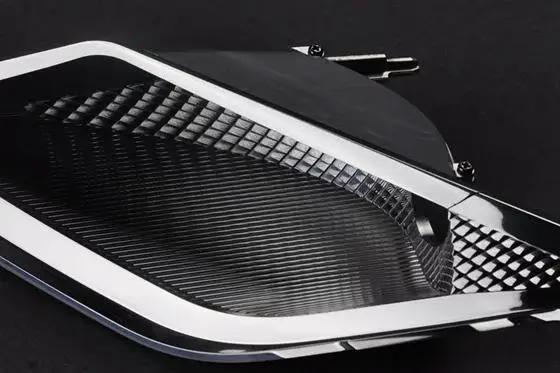
3) Aerospace Industry
Like automobiles, aircraft and other aerospace vehicles also require high precision. Any error in these parts can endanger people’s lives.
Therefore, CNC precision machining helps in manufacturing parts for this industry. These components include landing gear ports, bushings, manifolds, airfoils, etc.
4) Electronics Industry
The consumer electronics industry is currently experiencing massive miniaturization, requiring smaller and more powerful components. These components are designed to be compact and lightweight.
CNC precision machining can meet these requirements while maintaining very tight tolerances, even for high-volume production. CNC machines are able to produce components such as semiconductors, heat sinks, circuit boards, and other consumer electronics components.
5) Military and Defense Industry
Defense systems in various countries now have new designs for defense systems, and CNC precision machining is the most relevant process to bring these designs to life.
Multiple components can be manufactured using a variety of materials and techniques, including ammunition, communication components, planning parts, etc.
6.Conclusion
CNC precision machining is an effective technology for manufacturing customized precision machined parts. In addition to producing quality parts, it can also save costs and help you get your products to market faster.
Therefore, a precision CNC machine shop can ensure better part performance, thereby increasing the profits of your business.
If you are looking for an experienced CNC machining manufacturer, Xavier is your ideal choice. The Xavier team is well-equipped to provide high-quality CNC machining solutions. If you need more information or to discuss your machining needs with us, please feel free to contact us.