Waterjet Machining Explained: All About the Process and Benefits
Waterjet machining is a CNC 2D manufacturing process that utilizes abrasives and high-powered water jets to cut metals, composites, plastics, and more.
This precise, efficient machining method improves the edge quality of cut parts, makes precise internal cuts to your exact specifications, and reduces thermal stress on certain materials. We proudly offer waterjet cutting as one of our many high-quality machining services.
In this comprehensive guide, we’ll take a deep dive into the world of waterjet machining, exploring its benefits, the process behind it, the materials it can cut, and its many applications.
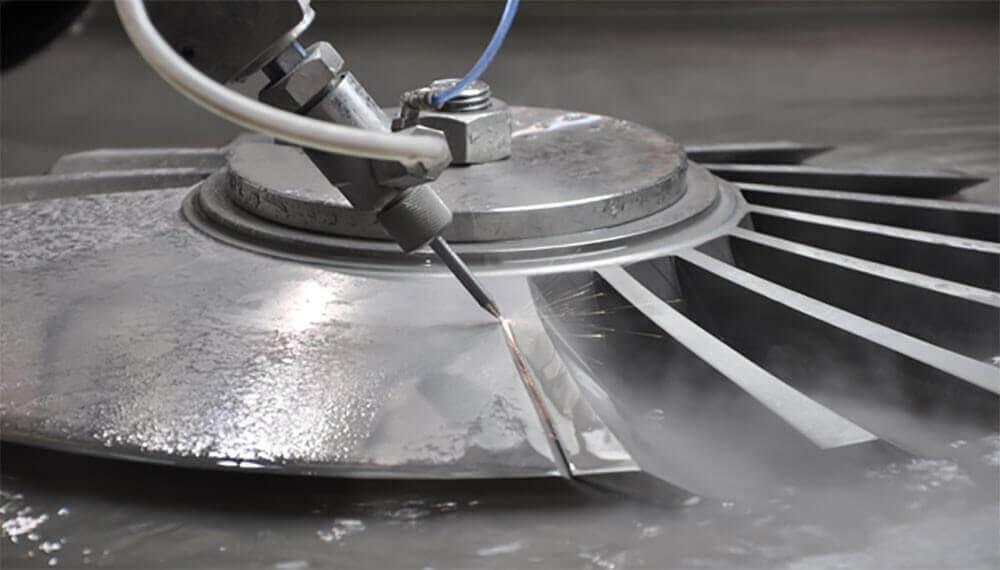
1.What are the benefits of using waterjet machining?
1) Versatile
Waterjet cutting is a versatile and precise machining technology that offers numerous benefits to a wide range of industries. This cold cutting process helps eliminate additional finishing steps, such as grinding or sanding, saving time and resources.
2) Environmentally Friendly
Waterjet cutting is environmentally friendly because it uses only water and a small amount of abrasive (if needed) as the cutting medium. This eliminates the harmful fumes or dust often produced in traditional cutting methods, promoting a safer, cleaner work environment.
3) High Precision
Waterjet cutting also offers high precision, enabling sophisticated and intricate designs with tight tolerances, making it ideal for precision-critical industries such as aerospace, automotive and electronics.
4) Reduced Waste
It also minimizes material waste, as narrow kerf widths ensure minimal material loss, ultimately reducing costs.
Another important benefit of waterjet cutting is its versatility, which can accommodate a wide range of material thicknesses, from thin sheets to thick plates, for a variety of applications.
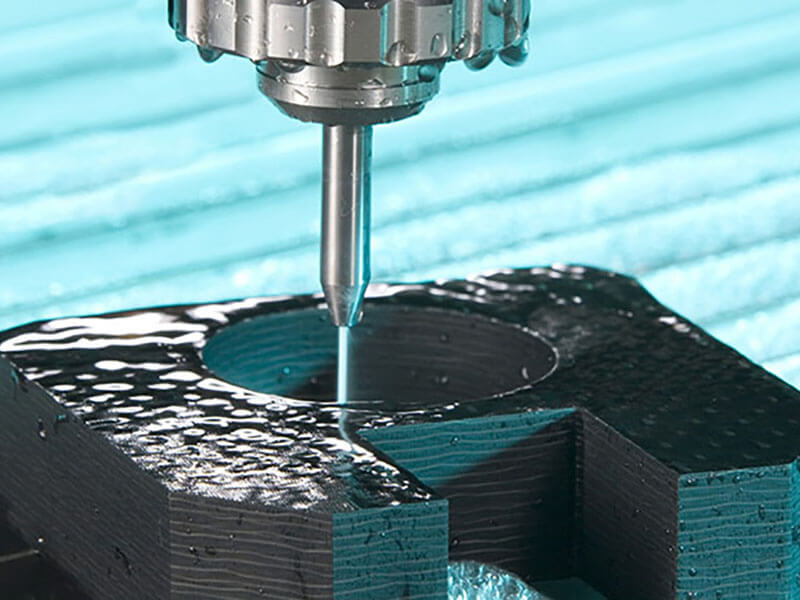
5) Enhanced Edge Quality
One of the standout benefits of waterjet machining is its excellent edge quality. The process minimizes the formation of the heat-affected zone (HAZ), which often occurs with traditional cutting methods.
This also means that your composite parts have a lower risk of delamination, which occurs due to increased material stress. As a result, your cut edges remain smooth and burr-free, with little to no additional finishing required.
6) Cost Savings
Although waterjet cutting has historically been one of the more expensive 2D machining methods, we invest a lot of time and effort to provide you with quality waterjet cut parts at a very low cost. Our fast, automated process means you’ll see savings on every part you order.
7) Improved Efficiency
Waterjet machining excels in efficiency because it can make high-speed cuts without compromising accuracy and precision. Since the kerf of a waterjet cutter is relatively small, it is able to make more precise cuts.
So waterjet machining can minimize material waste, which helps reduce costs and improve efficiency with the remaining material.
8) Precise Internal Cuts
Waterjet machining is known for its ability to make precise internal cuts, even in materials with complex geometries.
And because waterjet machining is great for cutting thick metals with ease, it’s easy to make more complex cuts and designs even on thicker sheets.
9) Reduced Restrictions on Material Thickness
As we mentioned, waterjet machining can cut thick materials almost effortlessly, providing versatility and flexibility in your material selection.
Since this process doesn’t use heat, the internal stress of the material is also reduced compared to other machining processes.
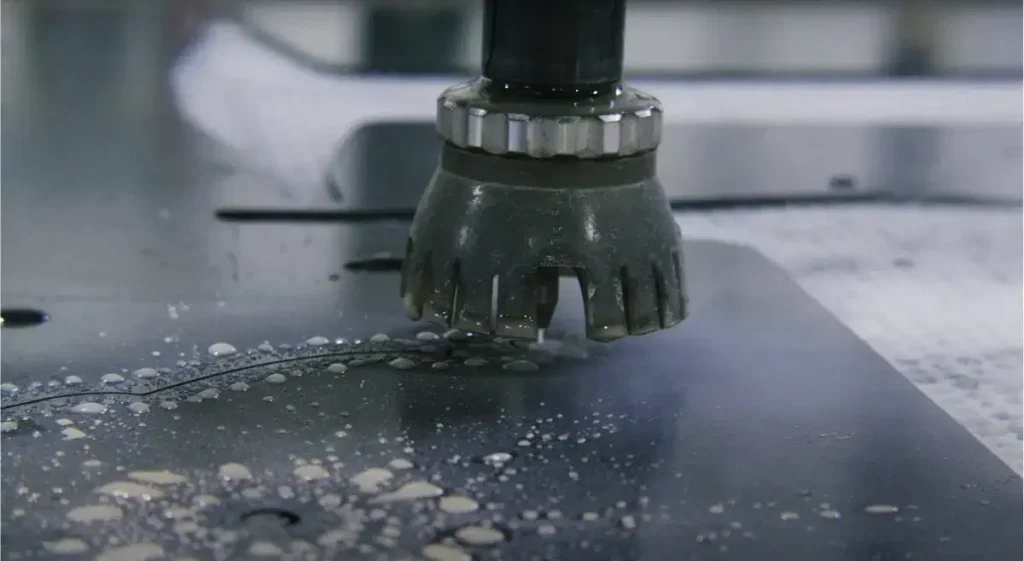
2.Understanding the Waterjet Machining Process
Each shop prepares its materials and machines for waterjet cutting differently, and each shop has a process that works for them.
The steps listed below are generally how waterjet machining works from start to finish.
Step 1: Material Preparation
The waterjet machining process begins with material preparation. The material to be cut is securely secured to the cutting table to ensure stability during the cutting process.
Step 2: Pressurized Water
High pressure water is then generated using a specialized pump system. In abrasive waterjet machining, this pressurized water is often mixed with abrasive particles to enhance its cutting capabilities.
Step 3: Nozzle and Focusing Tube
The pressurized water passes through a nozzle and focusing tube, which narrows the water stream into a high-speed jet. Precise control of the nozzle ensures accurate cutting.
Step 4: Cutting
The focused water jet or waterjet/abrasive blend is directed at the material, effectively cutting through it. The controlled movement of the nozzle determines the shape and depth of the cut.
Step 5: Quality Check
Once the cutting process is complete, a quality check is performed to ensure that the cut meets the required specifications. Any finishing touches or additional processes are performed if necessary.
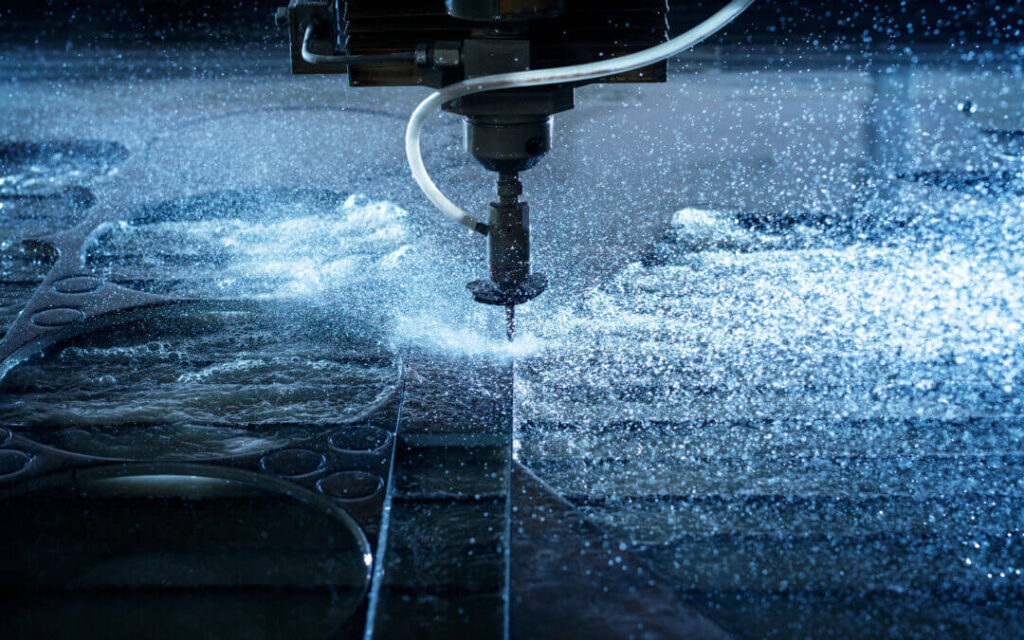
3.What Materials Can a Waterjet Cutter Cut?
- Metals: Waterjet machining works very well on a wide range of metals, including steel, aluminum, and titanium. Its cold cutting process eliminates the risk of thermal deformation, making it ideal for heat-sensitive metals. Waterjet machining is also well suited to machining extreme thicknesses of metal, no matter what the metal is.
- Plastics: Plastics such as acrylic, polycarbonate, and PVC are easily cut by waterjet machining. Since no heat is generated, there is minimal risk of melting or warping.
- Composites: Composites such as carbon fiber and fiberglass benefit from waterjet cutting due to their high precision and low delamination. Since there is no heat or blade involved when cutting composites with waterjet machining, no harmful dust or particles are generated during the process, making it better for the environment and workshop working conditions.
- Foam and Rubber: Waterjet machining excels at cutting foam and rubber materials, ensuring clean edges without compression or deformation.
- Glass: Glass is fragile and brittle, requiring a method to relieve thermal stress. Waterjet machining achieves this, providing precise glass cutting without cracking or chipping.
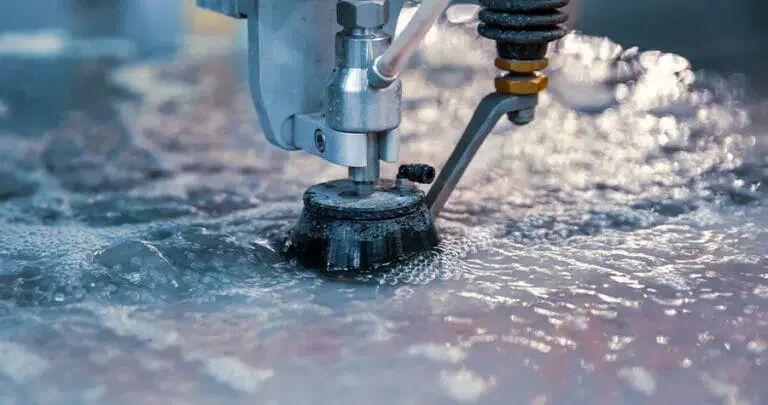
4.Types and Applications of Waterjet Machining
There are several types of waterjet machining. One uses abrasive media to increase the cutting force and one uses only a water stream.
1) Pure Waterjet Machining
- Method: Pure waterjet machining utilizes a high-pressure water jet with no abrasive additives. This method is well suited to softer materials such as rubber, foam, and plastic. It is particularly suitable for projects involving heat-sensitive materials that cannot withstand the heat-generating process.
- Application: Pure waterjet machining can be applied to the aerospace industry, automotive industry, and medical fields, where precision and material integrity are critical.
2) Abrasive Waterjet Machining
- Method: Abrasive waterjet machining involves introducing abrasive particles into the water jet to increase its cutting ability for hard materials such as metals and ceramics. It is a versatile method that works well with a variety of materials.
- Application: This method is widely used in industries such as architecture, construction, and manufacturing, where versatility and precision are critical.
If you are looking for an experienced machining manufacturer, Xavier is your ideal choice. The Xavier team is well-equipped to provide high-quality machining solutions. If you need more information or to discuss your machining needs with us, please feel free to contact us.