Grinding Machining: Everything You Need to Know
Grinding machining remains one of the most effective machining processes used in different industries to produce quality parts as manufacturing has evolved into a more complex environment that requires tight tolerance control for multiple custom parts or prototypes.
Therefore, manufacturers must adopt the right machining technology to produce components that meet standard requirements. This article will explore the various types, working principles and applications of Grinding machining. Let’s get started.
1.What is grinding machining?
Grinding machining is a grinding machining process that focuses on manufacturing and finishing parts with very close tolerances. Generally, grinding machining is a subset of metal cutting processes in manufacturing and toolmaking.
In production, grinding machining is used to process a variety of materials, especially for making shallow cuts to produce fine surfaces, shapes and sizes.
However, some industrial manufacturing processes require precision and accuracy, so there is little room for production errors, which applies to situations where the goal is to manufacture specific components without compromise.
Therefore, precision grinding machining provides a viable solution to the tight engineering tolerance and finishing problems faced by most manufacturers. This grinding machining operation can remove material to produce custom parts with tight tolerance dimensions or high-quality surface finish.
More specifically, high-precision grinding machining can machine workpieces with complete accuracy, achieving very precise tolerances, with diameter tolerances ranging from +/- 13 microns to +/- 1.3 microns and roundness tolerances ranging from +/- 2.5 to 0.25 microns.
Likewise, the method can also achieve typical surface accuracy with tolerances ranging from 0.20 to 0.81 microns.
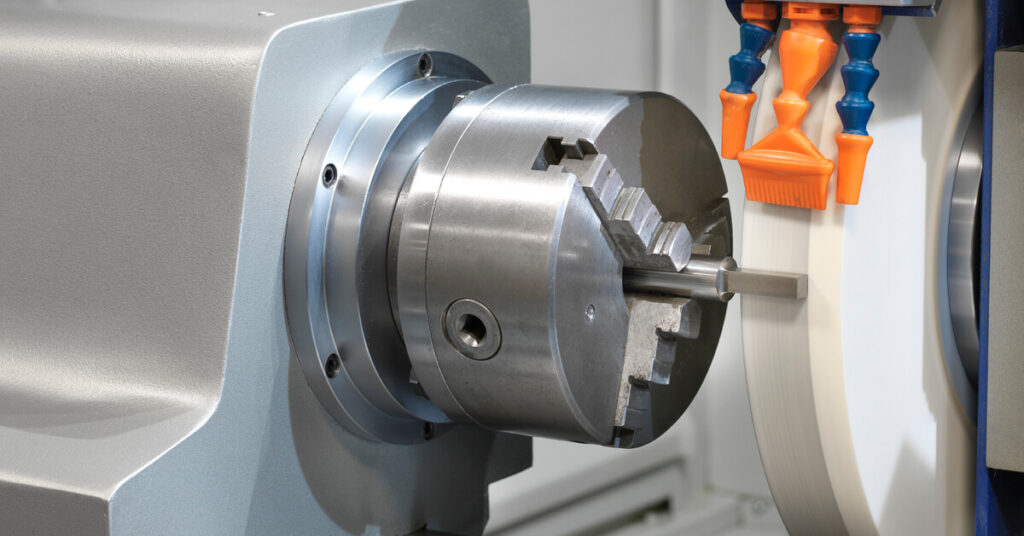
2.Benefits of grinding machining
Grinding machining offers certain advantages in the manufacturing process. Check out the following:
1) Cost-effectiveness and accuracy
To a large extent, high-precision grinding machining guarantees accuracy while providing a cost-effective method of producing different parts. Most metal manufacturers use this machining method to reproduce the specific dimensions of complex parts within an acceptable level of variation.
Apart from this, grinding machining operations help improve the efficiency of manufacturing precise parts while making quality control more consistent and easier. In short, grinding machining is an efficient manufacturing process.
2) Reliable machining alternative
Grinding machining is used by professional machinists when other machining methods or techniques such as milling and turning cannot be used.
This is usually due to the following reasons:
1. Type of material
2. Quality of surface finish required
3. Need to produce parts with small diameter and tight tolerances.
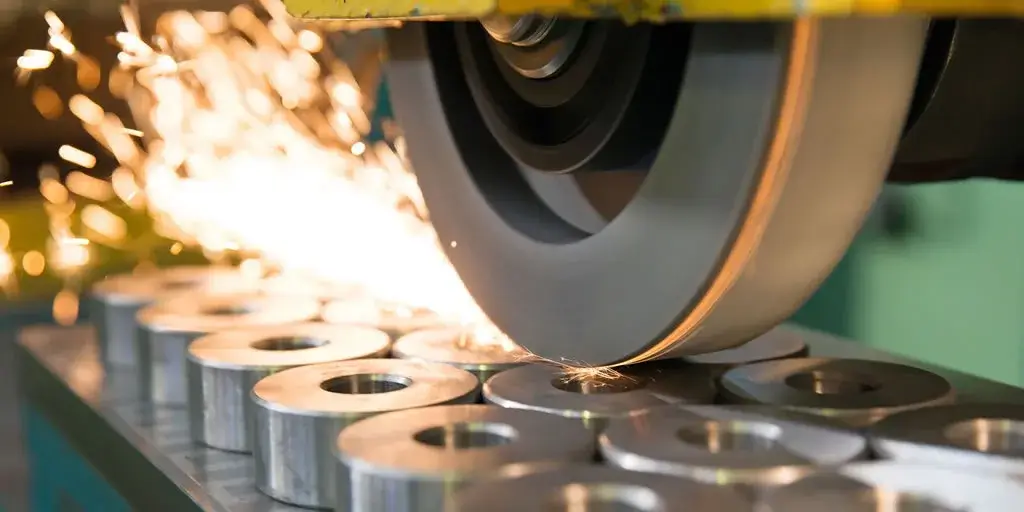
3.Types of grinding machining
There are various types of grinding machining processes that can be used to achieve precise surface finish and dimensions of various components. The characteristics of these grinding machining operations determine their respective applications in specific machining projects.
Therefore, manufacturers must select the appropriate grinding machining operation based on the size, shape, finishing features and required productivity of the part.
Below are some of the most common types of grinding machining processes.
1) Surface grinding machining
Surface grinding machining is a machining process that produces a smooth surface on a flat surface to give it a more refined appearance or add specific features. It involves using a rotating wheel coated with coarse abrasive particles to remove tiny chips or excess material from the surface of the workpiece.
In addition to the grinding machining wheel, the surface grinder includes a chuck and a table that uses magnets to hold the material.
The integration of CNC provides automation that allows for consistent material removal, ensuring high-volume production.
However, most precision surface grinding machining processes are usually used to make the ends of metal parts perpendicular to the outer diameter. In other cases, it is used to achieve parallelism or squareness of cubic parts.
When CNC turning and milling processes are not precise enough for a manufacturing project, manufacturers use precision surface grinding machining as an excellent alternative. This is because grinding machining operations can achieve micron-level production tolerances and surface finishes as low as 0.2 microns.
Note that the quality of surface finish obtained by surface grinding machining depends on factors such as grinding machining wheel speed, feed rate, grinding machining wheel size, abrasive, and material type.
In addition, surface grinding machining is well suited for materials that are easily clamped by magnetic chucks without clogging the grinding machining wheel. These materials include cast iron and many steel grades. Other materials such as aluminum, brass, and plastics clog the grinding machining wheel, making it impossible to cut. Therefore, only professional machinists can perform surface grinding machining operations on these materials.
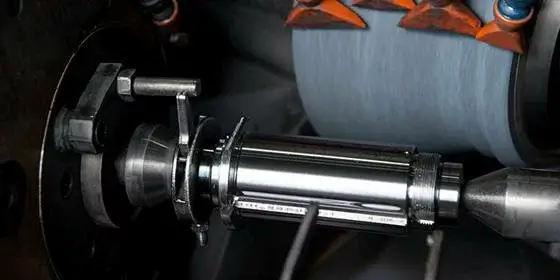
2) Cylindrical grinding machining
This grinding machining operation is also called center grinding machining and is suitable for cylindrical surfaces and shoulders of suitable workpieces. Cylindrical grinding machining machines consist of a Grinding machining wheel, a chuck, two centers to hold the workpiece, and other features for driving the workpiece.
Furthermore, most cylindrical grinders come with a rotary unit for making tapered pieces. The abrasive or grinding machining wheel can also come in different shapes. Machinists use standard disc wheels to make tapered or straight workpieces, while profiled wheels help to make odd-shaped workpieces.
In short, in cylindrical grinding machining operations, the workpiece is fixed on a center and rotated by a lathe jaw or center drive. The workpiece and the grinding machining wheel use separate rotating motors at different speeds. More importantly, the grinding machining wheel and the workpiece move parallel to each other in the longitudinal and radial directions.
Typically, precision cylindrical grinding machining provides a smooth surface finish for round objects. Moreover, the standard precision tolerances for cylindrical grinding machining are 1.3 microns in diameter and 0.25 microns in roundness.
There are two main types of cylindrical grinding machining, which are:
1. ID or bore grinding machining
As the name suggests, this cylindrical grinding machining type removes excess material on the inside diameter (ID) of a tube or other part feature, including holes or bores. Manufacturers use ID grinding machining and honing to produce smooth surface finishes and parts with tight tolerances. Both ID grinding machining and honing processes involve holding the workpiece in place and rotating it to limit the size of the part’s inner diameter to less than the grinding machining wheel diameter.
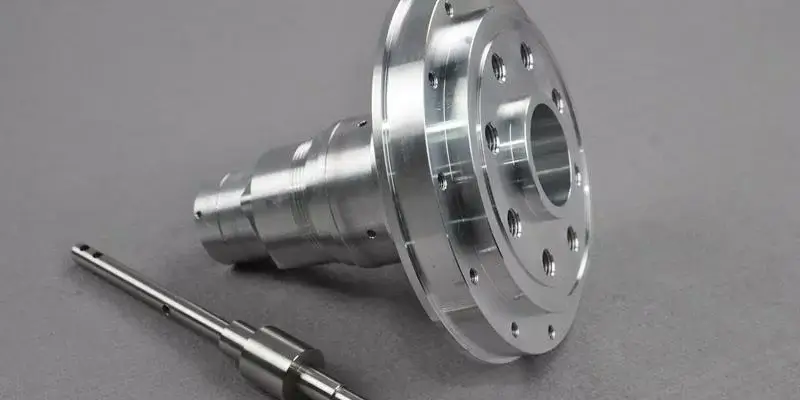
2. Outside Diameter or OD Grinding machining (OD)
Outer diameter (OD) grinding machining uses a single grinding machining wheel to shape the outer surface of a workpiece that is held by a center. During OD grinding machining, both the grinding machining wheel and the workpiece are continuously rotated around a central axis in the same trajectory. While OD grinding machining is suitable for a variety of part shapes, such as cylinders, ovals, and cams, note that the workpiece must have a fairly large central axis diameter so that it can rotate unhindered.
3) Centerless grinding machining
This grinding machining operation requires the removal of minute amounts of material to produce a specific finish on the outer diameter or perimeter of a small cylindrical workpiece. In most cases, manufacturers use centerless grinding machining to enhance the surface finish of turned parts to achieve higher precision.
In contrast to traditional OD grinding machining operations, centerless grinding machining does not hold the workpiece between centers or chucks. Instead, centerless grinders use support blades to support the workpiece on the outer diameter.
In addition, centerless grinding machining uses the action of two wheels: an abrasive grinding machining wheel and a regulating wheel. Although both wheels rotate in the same direction, the grinding machining wheel rotates at a higher speed than the regulating wheel. This allows the centerless grinding machining operation to grind very small parts.
Unlike other grinding machining processes, the workpiece does not require a fixture or motor when it moves on a centerless grinder. Instead, the grinding machining operation controls the movement through the so-called “magic angle” between the two wheels.
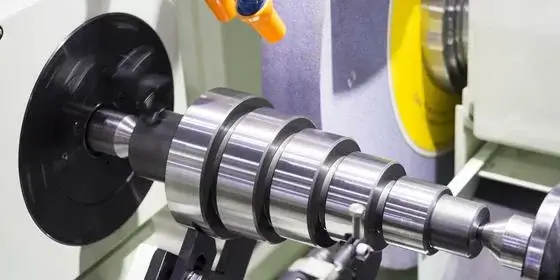
4.Application of grinding machining in manufacturing
In most manufacturing industries, grinding machining is often used as a final processing procedure for various parts of various sizes to ensure accuracy and high productivity. They include automotive, aerospace bearings, electrical, medical, etc.
The following are some common applications of grinding machining:
1. Micro-finishing of flat and cylindrical surfaces
2. Grinding machining of external circles, holes, and hole systems
3. Grinding machining of bearing surfaces
4. Precision machining of aerospace fasteners, tubes, rods, wires, bladed tools, etc.
5.Working principle and precautions of precision grinders
Precision grinders use rotating grinding machining wheels composed of abrasive particles to remove material from the workpiece. In addition, the grinder contains an electric motor that provides motion to the grinding machining wheel through a belt and pulley system.
Most grinder motors have speeds of 150 to 15,000 rpm, depending on the type of grinding machining project.
6.Precautions for using a grinder
There are several safety measures that you must follow to use a grinder safely. You should always wear personal protective equipment (PPE) before operating a grinder.
They help protect you from sparks and other flying particles while Grinding machining. PPE includes aprons, safety glasses, gloves, dust masks, hearing protection, safety boots, etc.
There are the following precautions for safe use of a grinder:
1. Make sure the grinding machining shield is properly installed.
2. Use the appropriate grinding machining wheel for each grinding machining operation.
3. Ensure the flange and other parts are properly assembled and tightened.
4. Secure the workpiece to prevent deflection while grinding machining.
5. Check and adjust the grinding machining speed to the appropriate intensity.
6. Make sure the work area is clean.
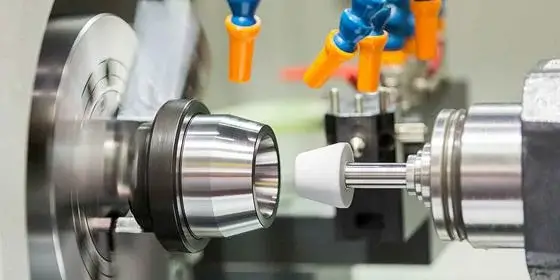
7.Main components of a grinder
A typical grinder consists of several parts. Take a look at the main components below:
1. Grinding machining wheel
2. Wheel guard
3. Grinding machining wheel head
4. Traverse wheel
5. Grounding
6. Table
7. Column
8. Coolant supply nozzle
8.Conclusion
Grinding machining remains one of the most effective and efficient machining techniques for manufacturing and finishing parts with tight tolerance requirements. It offers advantages such as cost-effectiveness and accuracy, simple quality control, and increased productivity. Therefore, grinding machining is now used in many industries to produce high-quality surface finishes.
If you are looking for an experienced machining manufacturer, Xavier is your ideal choice. The Xavier team is well-equipped to provide high-quality machining solutions. If you need more information or to discuss your machining needs with us, please feel free to contact us.