Detailed Explanation of Face Machining Operations in Mechanical Machining
Precision machining is complex. There are many operations and processes we need to understand and master in order to provide the best results for our customers, and obtaining nims certification machining is a great way to demonstrate our capabilities. In the past, we have discussed milling, turning and contour milling, but today, we want to talk about end machining.
1.Learn the ins and outs of 5-axis machining
Facing machining is a basic operation that is done in two basic ways: facing machining on a lathe and facing machining on a milling machine.
Both milling and turning involve removing material to produce a part with specific features. Facing machining is the process of removing material from the end or shoulder of a workpiece, using special tools to produce a smooth surface perpendicular to the workpiece’s axis of rotation.
When facing machining on a lathe, the machinist uses a facing machining tool to cut a flat surface perpendicular to the workpiece’s axis of rotation. The facing machining tool is then fed perpendicular to the axis. Facing machining will very precisely machine the workpiece to the finished length: depending on the amount of material that needs to be removed, the machinist can choose to do a rough or finish operation.

2.Facing machining on a Lathe
Facing machining on a Lathe allows the workpiece to rotate relative to the (stationary) cutting tool.
Several factors affect the performance of a lathe facing machining operation, including:
1. Type of workpiece material
2. Size and material of the cutting tool
3. How the workpiece is held
4. Speed of rotation
Whenever we talk about any facing machining process, especially facing machining processes on a lathe, we point out the importance of “surface pass”.
Simply put, surface pass is the process of removing microscopic errors from the surface of the workpiece to make the surface as uniform as possible. When this task can be completed, it is always a good practice for the machinist. However, if you are working with die-cast materials or forgings, surface pass may not be an option.
3.Facing machining on a Milling Machine
On the other hand, when facing machining on a milling machine, the “live” cutting tool moves and rotates around the workpiece.
1) How does face milling work?
When machinists face mill a workpiece, they divide the process into four parts. These include:
1. Workpiece positioning
Before starting the process, they make sure the workpiece is securely fixed to the machine table. They need to secure the workpiece firmly to the table to prevent it from sliding off.
2. Positioning the Milling Machine
Next is to make sure the milling machine is in the correct position. The machinist will position the milling machine perpendicular to the workpiece. This way, the top of the cutter is acting on the material.
3. Adjusting the Feed Rate and Spindle Speed
Next is to adjust the feed rate and the speed at which the machine moves the cutter (spindle speed). These two items are critical to ensuring that the machine cuts in the correct position.
4. Machining
Once the machine is set up, the machining begins. Since the computer has been fed the machining process code for the CNC machining, it does all the work and machines the desired shape and form on the workpiece.
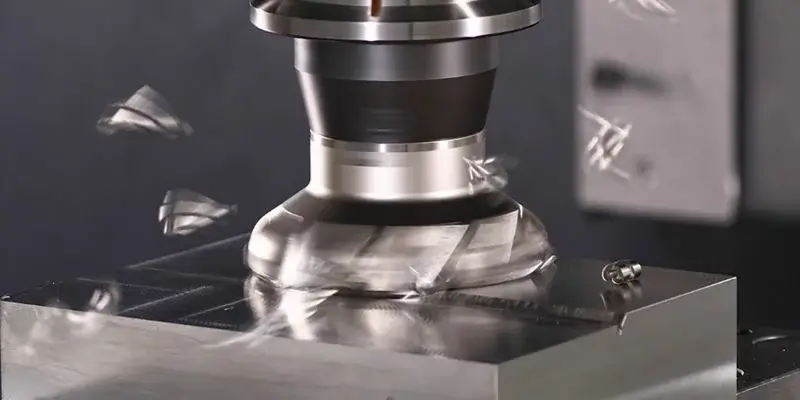
2) Choosing the Right Face Milling Cutter
The success of any face milling process depends on the tool used. Before we get into tips to help choose the right cutting tool, we need to understand the different tools used for face milling. There are three main machine tools used for face milling: shell mills, end mills, and fly mills.
1. Shell Mills
Shell mills are the tool of choice for face milling. Shell mills have multiple teeth with inserts on the cutting edges, making them ideal for producing a consistent surface finish. This is because its design allows for control over the amount of material that can be removed each time. It is also suitable for machining a wide range of materials. However, depending on the hardness of the material, it may require constant replacement of the blade.
2. End Mills
End mills have cutting edges and are suitable for performing intricate machining on a workpiece. However, it is not a good choice when large chunks of material need to be removed from the workpiece. In addition, the tool is not very strong, so its choice of materials that can be machined is limited.
3. Flying Shears
Unlike end mills and shell mills, fly cutters have only one cutting edge and one blade. However, their advantage is that they can achieve a fine surface without consuming much power. In exchange for power, they run at much lower speeds. Therefore, if you want to achieve a finer surface with less power consumption, fly cutters are a viable option.
3) Tips for Choosing the Right Tool
Now that we have explained the various types of face mills, we can now explain how to choose the best tool for different types of face milling operations.
1. The best face mill when cutting hard materials is a shell mill. Its multiple cutting edges enable it to remove a larger piece of material at a time.
2. Fly cutters are the best face milling cutters for machining softer materials.
3. When using a face milling cutter to make aesthetically pleasing designs, the best face milling cutter tool is an end mill. This cutter has multiple teeth on the shank, making it suitable for making a variety of designs.
4. Another factor to consider when choosing a cutter is the angle at which the cutter enters the workpiece. Most cutters enter at 45° or 90°. However, some cutters also fall within the 10 – 65° range.
5. When performing face machining, you must ensure that the spindle and machine speeds match. Otherwise, the face milling cutter is prone to wear.
6. Using CNC mode for face machining is better than manual mode. This is because, with manual face milling, you are constantly exiting and exiting the cutting path, which puts pressure on the cutting edge on the workpiece.
7. Finally, you should not mill holes or slots in the workpiece because this causes the workpiece to exit and re-enter.
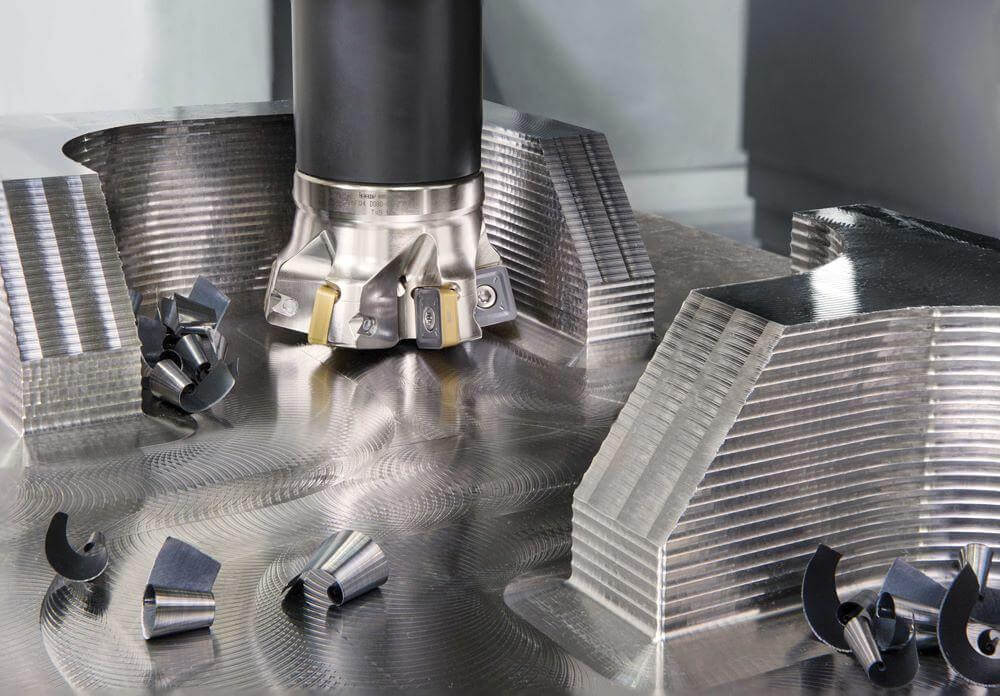
4.4 Types of Face Milling Operations
Machinists often use different types of face milling operations. This section will explain these different procedures and the best optimization tips for each procedure.
1) General Face Milling
This operation is just a general face milling operation and no special considerations are needed. In a general face milling operation, the lead angle is very important and it is best to use a face mill with a lead angle of 45°.
Some other tips to optimize a general face milling procedure include:
1. The diameter of the cutter should be larger than the workpiece (at least 20% and up to 50%).
2. The entry point into the workpiece should be off-center to ensure that the exit chips are as thin as possible.
3. Don’t forget the spindle size and horsepower of the machine.
2) Heavy Face Milling
This type of face machining requires a lot of material and a large machining center. In this type of face machining, the machinist needs to remove a lot of material, requiring huge horsepower.
For this operation, face mills with a lead angle of 60° are the best choice. They have a higher feed rate, which increases productivity and allows them to cut more material.
Other tips to optimize a heavy face milling procedure include:
1. This process generates a lot of heat. Wear gloves if you need to change the insole midway.
2. The process generates a lot of chips. These chips can clutter the workspace and re-enter the cutting path on the workpiece. Constantly re-cutting chips can cause the blade to wear. Therefore, be sure to clean up the workspace.
3) High feed milling
High feed milling involves processes that require high cutting speeds and feed rates. Usually it involves cutting speeds of more than 1000m/min. Face milling cutters with high feed rates and small lead angles are the best choice for this process.
The only thing to pay attention to for this process is the lead angle. Since it allows for high feed rates, it is best to use a lead angle of around 10°.
4) Finishing with Wiper Blades
Using scraper blades and standard blades, you can also use face milling to achieve beautiful surface finish designs. Scraper blades are mainly used for surface finishing. They usually come in different lengths and are available in left-hand and right-hand versions.
For this process, the necessity of a scraper blade depends on the type of standard blade used. The higher the feed per revolution produced by the standard blade, the greater the need for a scraper blade.
To achieve the best surface finish, it’s best to have the machine feed the table: CNC machines and newer manual machines have this capability, but older machines generally don’t.
There’s also a specific type of face milling called countersinking, which faces localized areas, such as a bolt head or a bearing surface where a washer will sit. Facing machining is a basic machining process, but they form the basis for other, more complex machining processes. By creating a large, smooth surface quickly, we’re able to move on to other CNC operations and manufacture precision parts to spec. It’s all thanks to facing machining.
If you are looking for an experienced machining manufacturer, Xavier is your ideal choice. The Xavier team is well-equipped to provide high-quality machining solutions. If you need more information or to discuss your machining needs with us, please feel free to contact us.