Learn More About Machining Graphite and Its Benefits
Graphite machining is the process of shaping, casting, configuring, and cutting graphite materials to create a variety of industrial parts and components. Despite its soft nature, graphite is one of the most difficult materials to machine. Electro Tech Machining happens to be a leading supplier of graphite materials to industries such as aerospace. When machining these parts, machinists must make several decisions regarding cutting tools, coolant usage, and personal safety.
The type of tool used determines the success rate of machining graphite. To prevent chipping and breaking, manufacturers use specially developed cutting tools. In most cases, indexable carbide tools are used, which have shapes that are best suited for high-speed roughing.
1.What is graphite? What are its types?
Graphite is a type of carbon whose carbon atoms are arranged in layers, which gives it unique properties. Natural graphite is mined all over the world, but most of it is produced in China, Brazil, Canada, and Madagascar. It is found in metamorphic and igneous rocks and is formed when carbon in the earth’s crust is subjected to high pressure and temperature.
The carbon in synthetic graphite is of high purity and resistant to high temperatures and corrosion. Calcined petroleum coke and coal tar pitch contain graphitizable carbon and are the main raw materials for the production of synthetic graphite. The entire production process includes mixing, heat treatment, forming and baking.
The process of machining cast iron and machining graphite is the same. Chips or small fragments are removed in the form of fine powder. The tools used in the process do not grab the workpiece, but cut it like plowing snow. Graphite has high compressive strength and can be held in place by clamping force.
Graphite parts are used in various fields due to their chemical and physical properties. It has a low coefficient of thermal expansion, can be machined to tight tolerances, and has excellent stability at high temperatures. These properties make it ideal for specialized production applications.
The application range of graphite is wide, from pencil leads to the lining of nuclear reactors. Electrodes, brushes and plates of dry cell batteries are made of crystalline flake graphite. In addition, the application of graphite in electric vehicles is also a major new discovery.
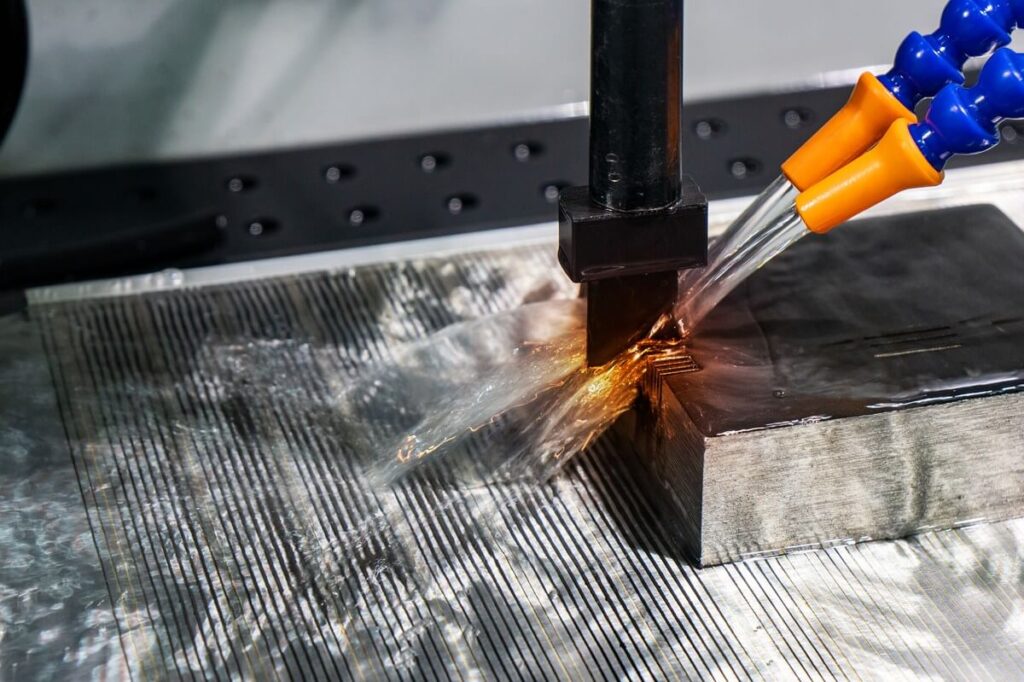
2.Types of graphite parts
1) Graphite lubricating blocks
Lubricating blocks are used in situations where wet lubricants cannot be used. They are mainly used in rotating equipment, including trunnion rollers, slip rings, tires and insert seals. Due to their weight, they are always in contact with the rolling surface, producing a thin layer of graphite. The important reasons why graphite is used in lubricating blocks are its wear resistance and long service life.
2) Graphite-containing bearings
Bearings are manufactured to minimize friction between two surfaces. Therefore, when the bearing is in contact with another moving object, the bearing can provide load support. Graphite is well suited for use in bearings because of its self-lubricating properties, extended service life, and ability to withstand harsh conditions.
3) Low-porosity graphite brushes
Graphite brushes are square in shape and are used to conduct electricity through electric motors. They provide consistent current transfer between commutator segments and wear to maintain their condition. They are made of natural or synthetic graphite with a bitumen or resin binder. Environmental variables do not contaminate graphite brushes.
3.Considerations for machining graphite
While graphite has a variety of uses in multiple industries, it still needs to be carefully matched to ensure the best results.
The following are factors that should be considered:
This material is very conductive. Protecting electrical and electronic components from damage by tiny graphite particles is a major concern for machine tool manufacturers. Machining graphite on CNC machines requires special modifications to handle graphite dust, which can cause expensive damage and even void the warranty.
If electrical parts are not properly selected and protected, graphite dust can accumulate on them and cause short circuits, which can irreparably damage the parts. Machines must have proper enclosures and guards as well as dust collection technology, as prolonged exposure to graphite dust can cause respiratory problems.
These particles are very lubricating and their deposition on the shop floor can make the floor slippery and cause people to fall. Special electrical cabinets and panel coolers for control systems and drives are needed to protect these devices. Drive components require unique coverings. Graphite is best cut dry.
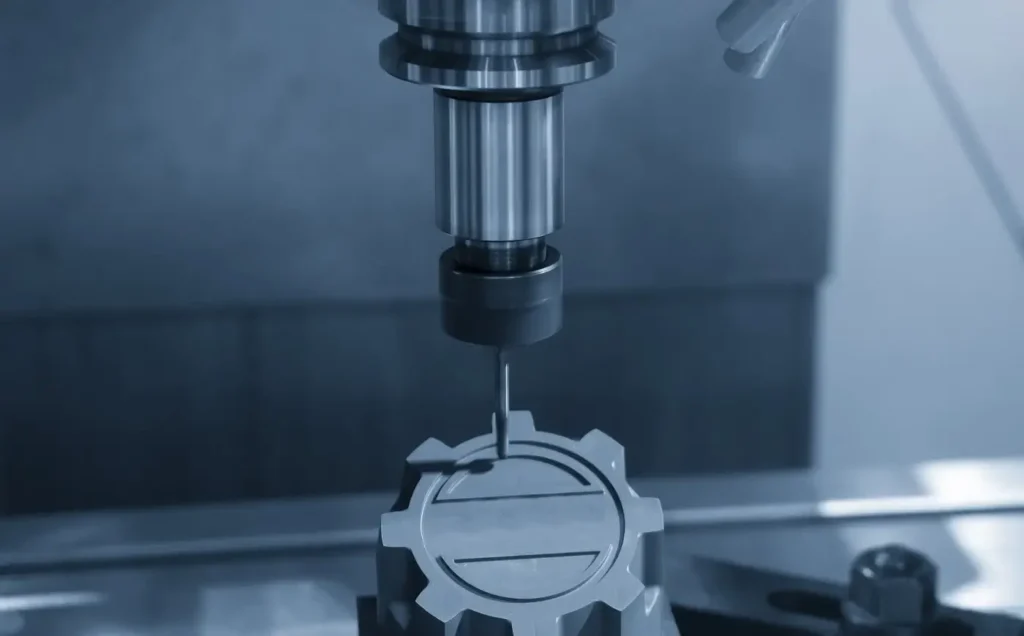
4.Various types of machining graphite processes
The machined graphite parts and components come in a variety of shapes and sizes. The process used to machine these parts and components depends on the specifications of the manufactured component. Extrusion, isostatic pressing, vibration and molding are all methods of machining graphite.
1) Extrusion method
Extrusion is a typical process in polymer manufacturing. In the graphite production process, graphite powder is mixed with a binder, placed in a hopper, fed into the barrel of an extruder, and then pushed down the barrel to the die by a piston.
After leaving the extruder, the formed body is fired at 2000C (3632F), impregnated, fired again and graphitized. Extruded graphite sheets are extremely cost-effective.
2) Isostatic Pressing
Isostatic pressing applies uniform pressure to fine-grained graphite powder. After pressing, the workpiece is heat treated to fully solidify, densify, change and purify it to form the final crystal structure. The process can be cold or hot.
3) Solidified and Vibrated Graphite
Vibrated graphite is a cost-effective production method for large-scale, low-density graphite when high strength is not required. The finished product has a consistent structure and a low ash percentage. The paste is poured into a mold and a thick plate is placed on it. The mold is vibrated until the paste freezes, causing the material to solidify.
5.Machining Graphite Forming
The machining graphite forming process produces parts of comparable quality to the isostatic pressing process. The graphite powder mixture is continuously extruded into a mold and remains there for a long time. The final product lacks the high quality of the isostatic pressing process, but is suitable for mass production of tiny parts such as washers.
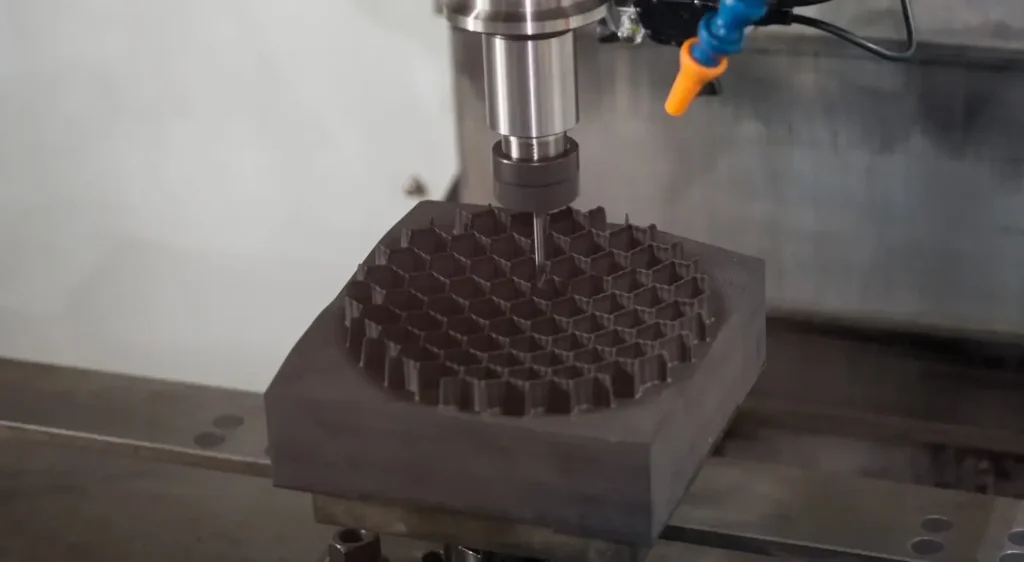
6.Challenges of machining graphite and how to deal with them
Graphite material has special characteristics, so machining it into graphite parts is a challenge. What makes graphite difficult to machine?
First, graphite is strong, but soft and brittle. It breaks easily. Graphite is abrasive and can cause severe tool wear. Graphite is often machined at high speeds without coolant. The spindle speeds on our machining centers are high, which produces a lot of dust.
In addition to all these challenges, most graphite applications require a good surface finish.
1) Tool Wear When Machining Graphite
Because graphite material is extremely abrasive, the tools we use to machine graphite parts wear out quickly. However, using the right tools can minimize the need for machine maintenance.
To achieve the best results when machining graphite and with minimal wear on the machine, we use carbide or diamond coated tools. This coating prolongs tool life and performs well when machining graphite parts.
When tool life and wear are critical when machining graphite, CVD diamond coating is recommended to improve tool life and performance. This coating is grown directly onto the carbide tool, increasing its hardness and creating a coating that is five times thicker than PVD diamond coating.
Even though these tools don’t provide the sharpest cutting edge, CVD diamond coatings provide longer tool life than other diamond coatings due to the thicker diamond layer.
2) Dust from machining graphite
Dry machining, i.e., machining without coolant and at high speeds, produces a lot of dust. Compressed air can be used to reduce tool wear and help prevent premature tool failure.
A powerful dust collection system is essential to our needs, both to ensure worker safety and to reduce scrap rates and waste.
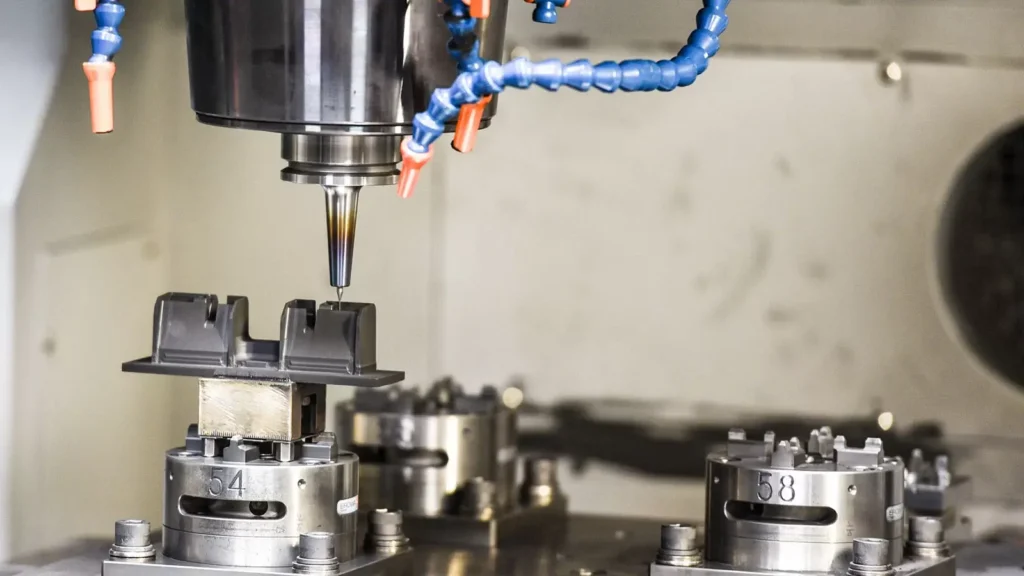
3) Complex geometry of graphite parts
Workpiece geometries range from simple to extremely complex. While we machine simple geometries, more often we machine complex parts whose elements cannot be easily manufactured with traditional tools and ordinary milling machines.
Use the proper cutting tools, running with the correct cutting data and specialized geometries and coatings to meet the challenges of machining complex graphite parts.
4) Workholding of Graphite Materials
One of the most important aspects of graphite machining is proper workholding. Since the machines run at such high speeds and exert extreme forces, a strong clamping or vacuum fixturing is essential.
Proper and well-functioning fixturing not only helps improve machined surface finish, but also minimizes vibrations, allowing for complex and precise cuts.
If you are looking for an experienced machining manufacturer, Xavier is your ideal choice. The Xavier team is well-equipped to provide high-quality machining solutions. If you need more information or to discuss your machining needs with us, please feel free to contact us.