Basic Guide to Machining Stainless Steel
Machining stainless steel is one of the most common processes in machining. This guide to machining stainless steel covers the various types of stainless steel as well as the different machining processes. We hope it will increase your knowledge of the metalworking process.
1.What is stainless steel?
Stainless steel is a strong and versatile iron-based alloy that contains at least 10.5% chromium. Chromium also makes this type of alloy extremely corrosion resistant. The secret of this high corrosion resistance is the formation of a thin layer, commonly known as the “passivation layer”.
To qualify as stainless steel, the alloy must also contain up to 1.2% carbon. Other elements that stainless steel can carry include titanium, molybdenum, nickel, silicon, and nitrogen. It is important to note that stainless steel is a mixture of metals and multiple elements. This is the main reason why this metal has different properties.
To this day, the demand for stainless steel is still growing, and it is estimated that the annual growth rate is 5%. These alloy grades may be relatively expensive, but they have some attractive properties. To add to the corrosion resistance and strength of the alloy, stainless steel grades have a modern look and are easy to maintain.
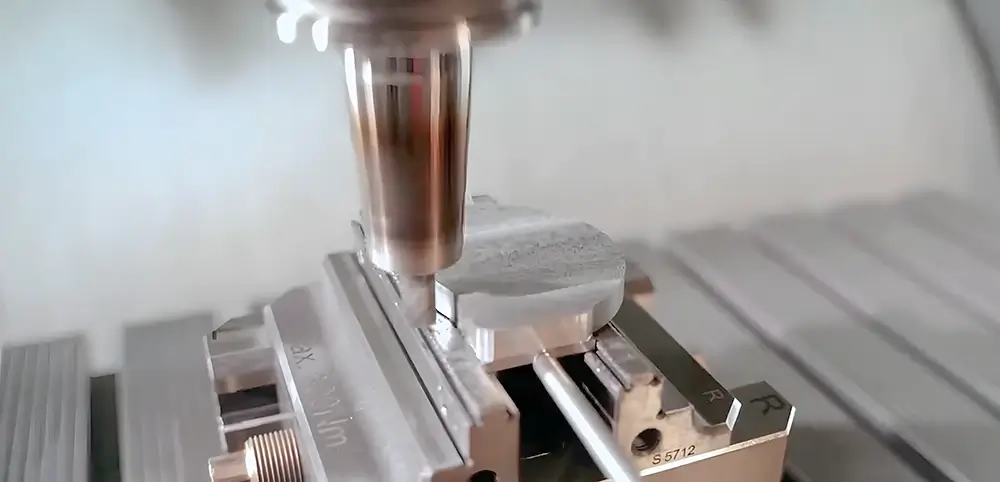
2.Types of Stainless Steel
There are five types of these stainless steels: Austenitic, Ferritic, Martensitic, Duplex, and Precipitation Hardening.
Here is an overview of each type.
1) Austenitic Stainless Steel
Austenitic stainless steel is undoubtedly the most popular type of stainless steel. It is characterized by high nickel and chromium content. This gives the metal excellent mechanical properties and corrosion resistance. Austenitic stainless steel is also known for work hardening.
Austenitic grade means that the stainless steel has an austenitic microstructure. The cells of the austenitic stainless steel microstructure are cube-shaped. There is an atom at each corner of the austenite alloy cell. Another atom is located in the middle of the cube. In crystallography, this is a face-centered cubic structure (FCC).
Austenitic stainless steel types:
1.304, 304L stainless steel,
2.310 stainless steel,
3.316, 316L stainless steel,
4.321 stainless steel,
5.347 stainless steel
6.904L stainless steel
2) Ferritic stainless steel
Ferritic stainless steels contain up to 0.1% carbon and between 10.5% and 27% chromium. They can also be called ferritic steels. Although this steel is not heat hardened, it is magnetic. The core reason for developing ferritic stainless steel is that the product is corrosion and oxidation resistant.
Another property of ferritic stainless steel is high ductility. The combination of all these properties produces a stainless steel that is very versatile. It is suitable for making a variety of items, including kitchenware and industrial equipment.
Although ferritic stainless steel cannot be heat hardened, it can be annealed or cold worked. This stainless steel is a good choice for budget-conscious projects.
You will come across the following five groups of ferritic stainless steels:
Type 1.409 / 410L
Type 2.430
Types 3.430Ti, 439 and 441
Types 4.434, 436 and 444
Types 5.446, 445 and 447
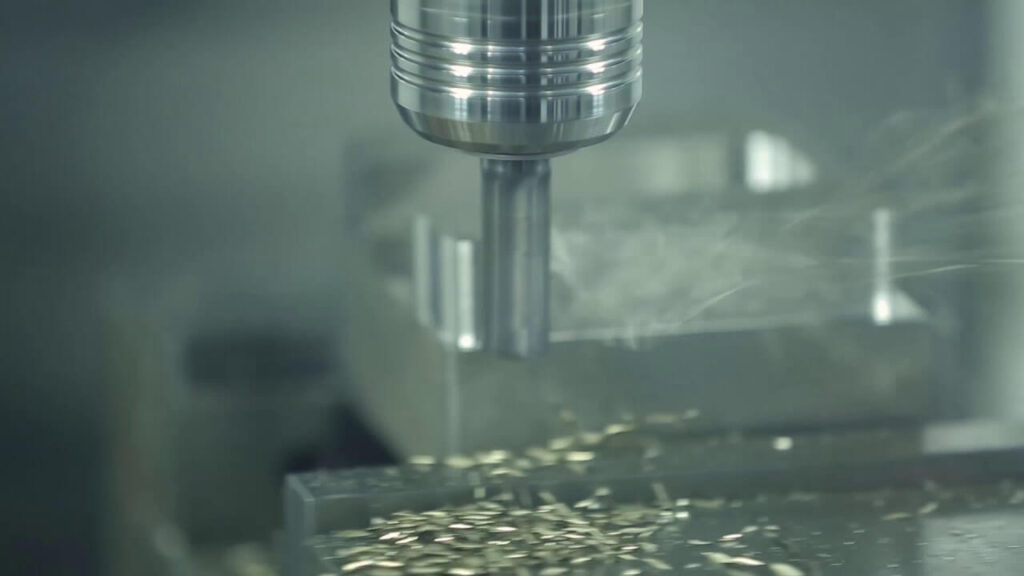
3) Martensitic stainless steels
When stainless steel was developed for commercial use, this was the first type to appear. The most common use for this steel is cutlery. Martensitic stainless steels have a relatively high carbon content, between 0.1% and 1.2%.
They are comparable to ferritic stainless steels, with a higher chromium content, ranging from a minimum of 12% and up to 18%.
Common grades in this category are 440C stainless steel and 420 stainless steel. They are wear-resistant and suitable for engineering parts, respectively.
Martensitic stainless steels are becoming increasingly popular across industries. The automotive industry is a good example of a wide range of applications for this material.
4) Duplex Stainless Steel
Duplex stainless steel is created when austenite and ferrite microstructures are combined. This type of steel has a high chromium content of 28%. However, the nickel content in duplex alloys is low, ranging between 4.5 and 8%.
Since the nickel content is not high enough, a true austenitic structure cannot be obtained. Instead, a new microstructure is formed – a duplex structure.
As you can guess, this type of stainless steel combines the properties of both ferritic and austenitic stainless steels. They include corrosion resistance, weldability, and formability. Their yield strength and tensile strength are higher than both ferritic and austenitic steels.
The most popular metal under this category is 2205 stainless steel. It is mainly used in refineries and related equipment.
5) Precipitation Hardening Stainless Steel
The precipitation hardening stainless steel (PHSS) class has the properties of both austenitic and martensitic stainless steels. These grades are heat treatable and corrosion resistant.
Precipitation hardening is a heat treatment process that increases the tensile strength and yield strength of the material. It also improves the material’s machinability and wear resistance.
This explains why precipitation-hardened stainless steels are suitable for aerospace, automotive, oil, and many other industries.
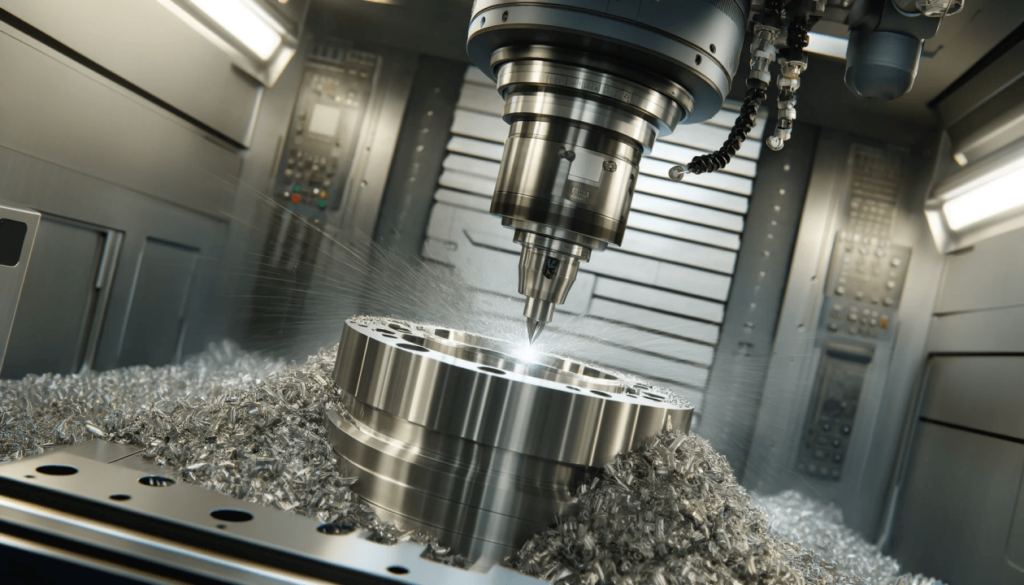
3.Processes for machining stainless steel
1) Milling
Milling is the process of removing parts of a workpiece using a rotating tool in a milling machine. In its traditional form, the process involves a workpiece fixed to a moving table. The rotating tool removes material from the workpiece as the table moves.
CNC machining, milling, and other processes can be problematic in stainless steel. Some precautions need to be considered and taken. The choice of cutting tool is particularly important due to tool wear issues.
There are several reliable cutting tools available for this process. For 304 and other conventional stainless steels, carbide tools can help. Sometimes HSS tools are also useful.
2) Turning
During turning, the workpiece rotates about its axis while the tool is stationary. Turning stainless steel can be challenging. The difficulty depends on the alloying elements present, the manufacturing process used, and the heat treatment used.
To effectively implement a steel CNC machining project, operators must consider the following points:
- The cutting force of the CNC lathe must be in the range of 1800 to 2850 N/mm²
- The chips of stainless steel should be short
- Adding sulfur to some steels (such as 303) may help improve machinability
- The Rockwell hardness of martensitic and ferritic stainless steels should be 55 HRC or higher to make the turning process effective
3) Drilling
The hardness of stainless steel is the biggest challenge when drilling. Typical drill bits and drilling methods may not be able to successfully complete this process. Therefore, make sure you have the right drilling tools, accessories, and skills.
The ideal drill bit for stainless steel is a coated HSS drill bit. For harder stainless steel grades, consider investing in a cobalt drill bit.
4) Threading
For parts or components that require fasteners or screws, stainless steel threading is essential. The process can be performed inside or outside the workpiece. Tubing is the most common workpiece type for threading.
Similar to other processes, stainless steel threading is not easy, especially hardened stainless steel. If the feed rate and cutting speed are not balanced, heat will be generated. However, the right technique and tools can make a difference.
5) Laser Cutting
Stainless steel can also be cut with lasers, a process that requires a strong beam of light. However, laser cutting of stainless steel is only effective for thin sheets. One might say that carbide tools can do the same job. However, these tools wear badly.
However, laser cutting also has its disadvantages. In addition to requiring skilled manpower, this process is costly.
6) Grinding
Grinding is a viable technique if you want to improve the surface finish of stainless steel or increase the accuracy of the part. This method of machining stainless steel is defined by the grinding wheel rubbing the surface. It can create a smoother surface and remove welding flaws and other defects.
7) EDM (Electrical Discharge Machining)
For the EDM process, high-frequency and high-voltage electrical pulses cut stainless steel by melting. Again, the thickness of the metal will limit the use of this process.
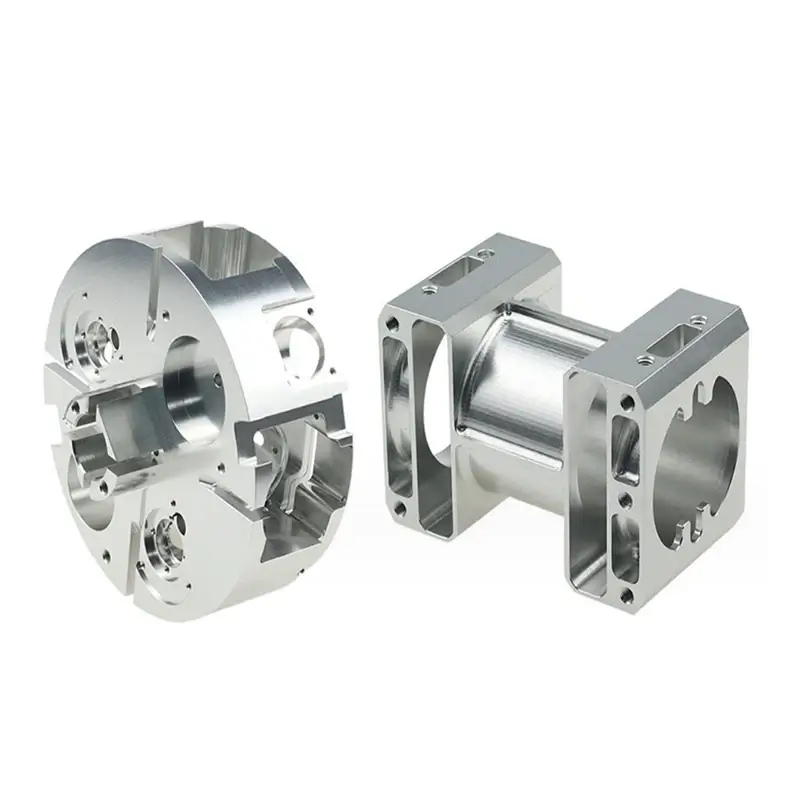
4.Surface treatment of stainless steel machined parts
1) Polishing
As a subsequent process of machining stainless steel, polishing may be necessary to achieve aesthetic and practical purposes. This process can be done by hand or machine.
For larger projects, it is best to machine polish stainless steel. The requirement for polishing remains, but a polishing wheel replaces the hand. Once completed, the surface should be free of streaks, marks, and excess polish.
2) Sandblasting and pickling
Sandblasting and pickling are essential to remove residue from earlier processing of stainless steel. Sandblasting can effectively clean the surface, leaving it clean and fresh. The processed stainless steel parts can also be placed in a pickling tank. The tank helps remove impurities such as rust, stains, and coatings.
3) Brushing
The material is brushed to achieve a unique parallel-marked look. A 120-180 grit wheel or belt is very useful in this process. Surface treatment is popular in the construction, sports equipment, and automotive industries.
5.Machining Stainless Steel Applications
Stainless steel is used in the following industries due to its strength, corrosion resistance, and other desirable properties:
- Medical – MRI scanners, dental equipment, replacement joints, surgical platforms
- Automotive – exhaust systems, body frames, containers
- Construction – handrails, storage equipment, pressure vessels
- Aviation – aircraft frames, engines
- Manufacturing – heat exchangers
- Food – cutlery, refrigerators, kitchen countertops, pots and pans
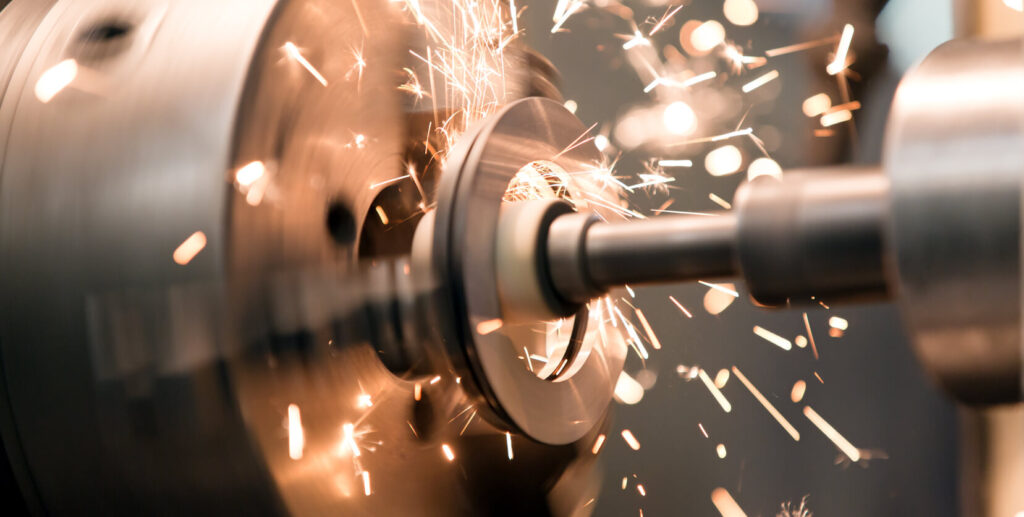
6.Challenges in Machining Stainless Steel
Given the diversity of stainless steel, it may not always be easy to produce custom stainless steel parts.
When machining stainless steel, you may encounter the following challenges:
1) Overheating in Machining Stainless Steel
Stainless steel has relatively poor thermal conductivity. During CNC machining, stainless steel heats up quickly. Using a slow-speed tool is a good solution to the problem of overheating when machining stainless steel. In addition, when machining stainless steel alloys, you need to minimize the force applied to the cutting tool. This minimizes excessive vibration that can cause overheating.
2) Difficult Surface Treatments
Besides the time-consuming CNC machining process, stainless steel also requires a very high surface finish, and not many machinists can perfect this material even with the best efforts on surface finish.
3) Technical Expertise
Not everyone enjoys machining austenitic stainless steel or any other type of stainless steel. An experienced machinist is needed because there are so many factors to consider – tool speed, drill type, feed rate, etc. Also keep in mind the danger of stress corrosion cracking, which can be introduced when machining stainless steel if the workmanship is poor.
4) Poor Machinability of Stainless Steel Alloys
The relatively sticky nature of stainless steel is a big challenge in the custom CNC machining process. Rapid hardening makes the problem worse, as it can even affect the life of the tool. The choice of cutting tool is very important, as it can mean the difference between machinable stainless steel and unmachinable stainless steel.
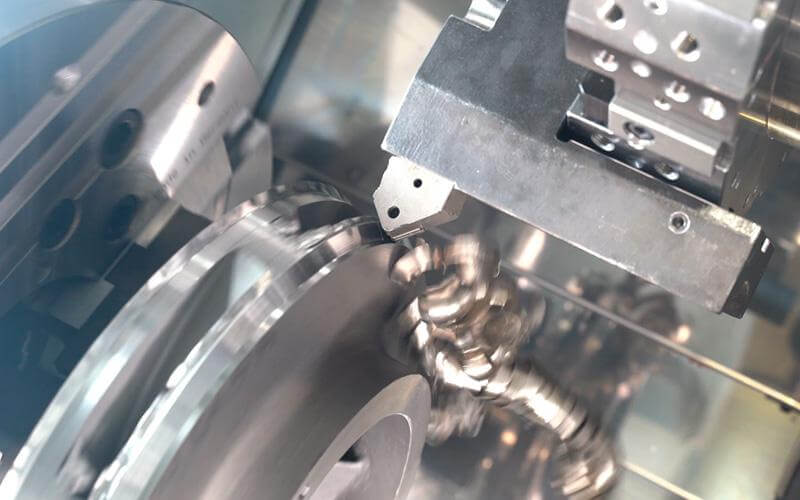
7.In summary
Machining stainless steel offers endless opportunities for professionals and beginners alike. Its unique properties and various machining processes make it possible to manufacture different stainless steel parts and items. These products can withstand harsh environments and have other features.
Whether you are looking for custom CNC machined stainless steel alloys for automotive, aerospace or architectural applications, our custom machined stainless steel products are the ideal choice. Partner with us to gain deeper insight into the world of machining stainless steel and other materials.
If you are looking for an experienced CNC machining manufacturer, Xavier is your ideal choice. The Xavier team is well-equipped to provide high-quality CNC machining solutions. If you need more information or to discuss your machining needs with us, please feel free to contact us.