Metal Machining: A Comprehensive Overview
Metal machining is the process of shaping and cutting metal using different tools and machines. It is versatile and can be used to produce simple or complex parts.
Machining process is a key manufacturing technology. Machining is a subtractive manufacturing process where metal is removed from the workpiece to form the desired shape.
In this blog, we will discuss the different machining processes, materials used in metal machining, and why you should consider manufacturing as a service of machining operations.
1.Types of Metal Machining Processes
1) Turning
- Description of Turning
Turning is a machining technique that uses a lathe to rotate the metal while the cutting tool cuts and removes material in a diameter direction to form a cylindrical shape. It is considered a basic machining job.
Machinists can produce different workpieces by orienting the cutting tool in different directions, using either a traditional lathe (which requires constant supervision) or an automatic lathe. Nowadays, CNC lathes or computer numerically controlled machines have become popular.
Turning is generally used to produce rotational and axisymmetric parts. Skilled machinists use turning to create a variety of features, including holes, grooves, threads, diameter steps, and curved surfaces, and entire workpieces can be produced by turning.
- Turning Use Cases
Precision turning is used to manufacture shafts, crankshafts, camshafts, bowls, valves, gears, furniture components, and threaded fasteners. This versatile machining process is used across a wide range of industries to create a variety of components with precise dimensions, smooth surfaces, and intricate details.
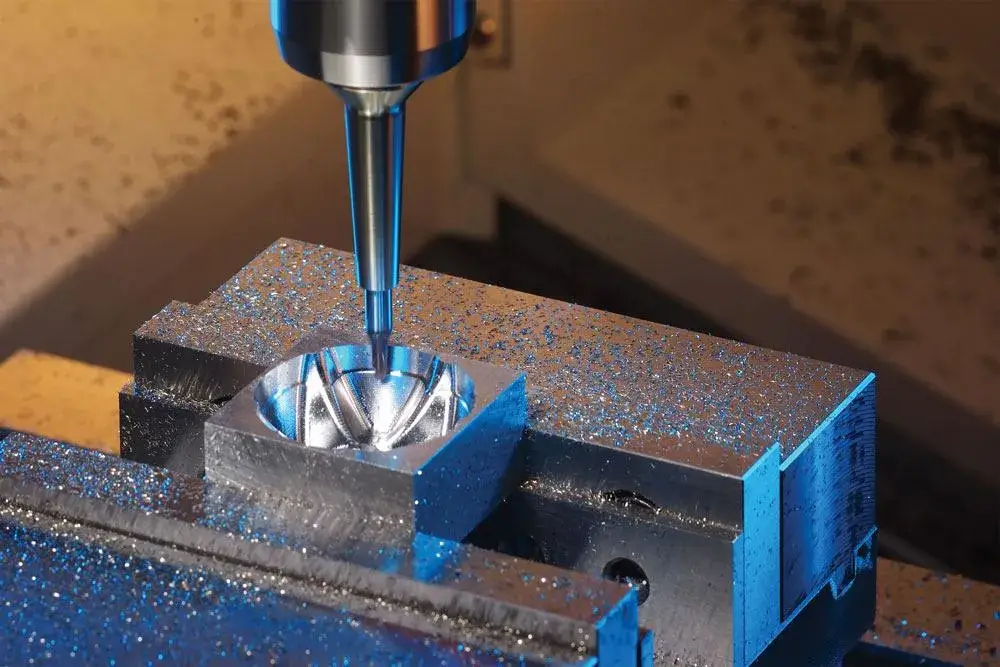
2) Milling
- Description of Milling
Milling is a machining technique that uses a multi-point cutting tool to remove material from a workpiece. In CNC milling, the workpiece is usually fed to the cutting tool in the same plane as the cutting tool rotates. However, in manual milling, the machine feeds the workpiece in the opposite direction of the cutting tool.
Milling machines can be positioned vertically or horizontally. Basic milling machines have three-axis motion, and more advanced models have additional axes.
- Use Cases for Milling
Manufacturers use milling to make gears, create slots or grooves in workpieces, create flat and uneven surfaces, and create complex shapes.
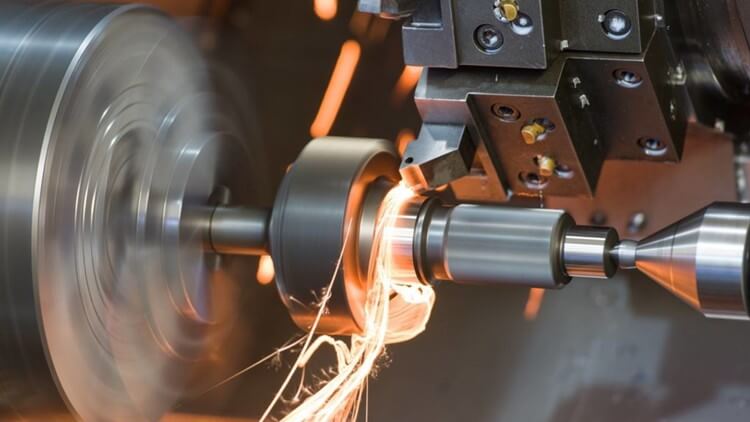
3) Drilling
- Description of Drilling
Drilling is the process of drilling a cylindrical hole in a solid material using a drill. A drill is a rotating cutting tool used to drill a cylindrical hole in the cross section of a metal workpiece. It is one of the most widely used types of machining processes.
The size of the drill determines the size of the hole in the workpiece. Drills can drill holes in a variety of materials and come in a variety of sizes and shapes, from small handheld drills to large industrial drills. Machinists attach the drill to a drill rig, which rotates and provides the torque and axial force required to drill the hole.
The operator presses the drill bit against the workpiece and then rotates it rapidly, at hundreds to thousands of revolutions per minute. This forces the drill to cut off the chips on the drill. The speed at which the drill rotates depends on several factors, such as the material and hole size.
Drilling is a simple process that involves rotating the drill bit and feeding it into the workpiece. Machinists adjust the cutting speed and feed rate of the drill bit. Common drilling techniques include tapping, countersinking, reaming, counterboring, and countersinking.
Drilling uses it to create holes in different surfaces as well as pivot holes for screws, threads for nuts, and countersunk holes.
- Drilling Use Cases
Drilling is used to create precise cylindrical holes in various materials, which is essential for applications such as fastener installation and component assembly.
4) Grinding
- Description of Grinding
Grinding is a machining process that uses a grinding wheel to remove workpiece material. The grinding wheel removes workpiece material as it rotates, resulting in a smooth surface texture.
The principle of grinding is simple: a rotating tool acts on the workpiece with abrasive grains to remove material. You can think of each abrasive grain as a cutting tool.
We can classify commercial grinding into:
- Rough grinding removes the most metal but reduces the surface finish. The surface finish of a rough-ground workpiece is usually in the range of 10 to 100 micro-inches.
- Finish grinding produces a smoother surface finish in the range of 0.1 to 1 micro-inch.
- Precision grinding is the middle link between metal removal and part dimensional control. It lays the foundation for creep-feed grinding, groove grinding, and efficient deep grinding.
- Ultra-precision grinding involves no actual grinding, but rather produces a high finish through the sliding action of very fine particles.
- Grinding Use Cases
Machiners use grinding machines to remove material from a variety of surfaces such as metal, wood, and plastic. It is a precise process that creates smooth surfaces with tight tolerances. Technicians utilize field grinding for repair and maintenance tasks, while machinists use machine shop grinding for finishing operations.
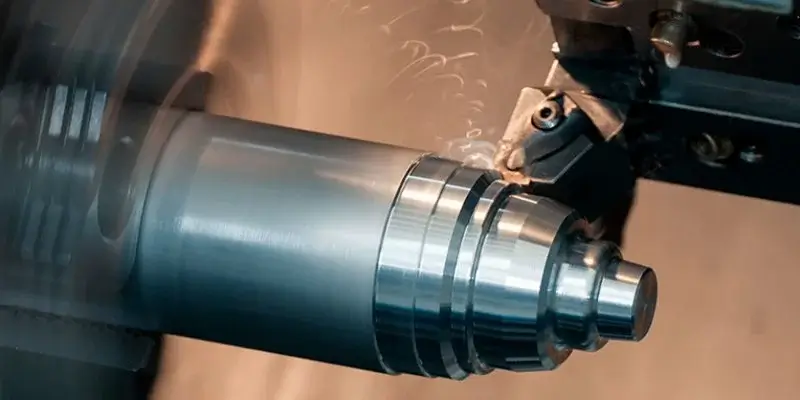
2.Advanced metal machining techniques
Advanced metal machining has changed the way we machine workpieces into complex precision components. These processes increase machining speed and accuracy. This makes it possible to manufacture complex components that were previously impossible to manufacture.
1) Computer numerical control (CNC) machining
① Description of CNC machining
Computer numerical control (CNC) is a manufacturing method in which machine tools can move precisely with the help of embedded pre-programmed computer software. Manufacturers use CNC machines to make machine parts made of metal and plastic.
CNC can also automate cutting equipment, including milling machines, lathes, planers, drills, grinders, water jets, and lasers. It can control machine tools such as welding, electronic assembly, and filament winding equipment.
G-codes and M-codes control CNC machines. M-codes manage non-moving tasks, while G-codes control how CNC machines move and perform.
② The advantages of CNC machines are:
- Precision: Use CNC machines to make parts with high tolerances.
- Reduced costs: CNC machines can reduce waste due to their high precision. Energy consumption is reduced due to higher productivity, greater scalability, and less material waste.
- Reduced waste: The software that runs CNC machines uses simulation and optimization exercises, resulting in almost no waste in the production process.
- Complexity: You can use CNC machines to make complex parts.
- Reduced human errors: CNC provides better precision, speed, flexibility, and repeatability by eliminating human errors in the manufacturing process.
③CNC machine tool use cases
Some applications of CNC machining include precision machining, prototyping and rapid manufacturing, mass production, woodworking and furniture manufacturing, metal manufacturing, and electronics and PCB manufacturing.
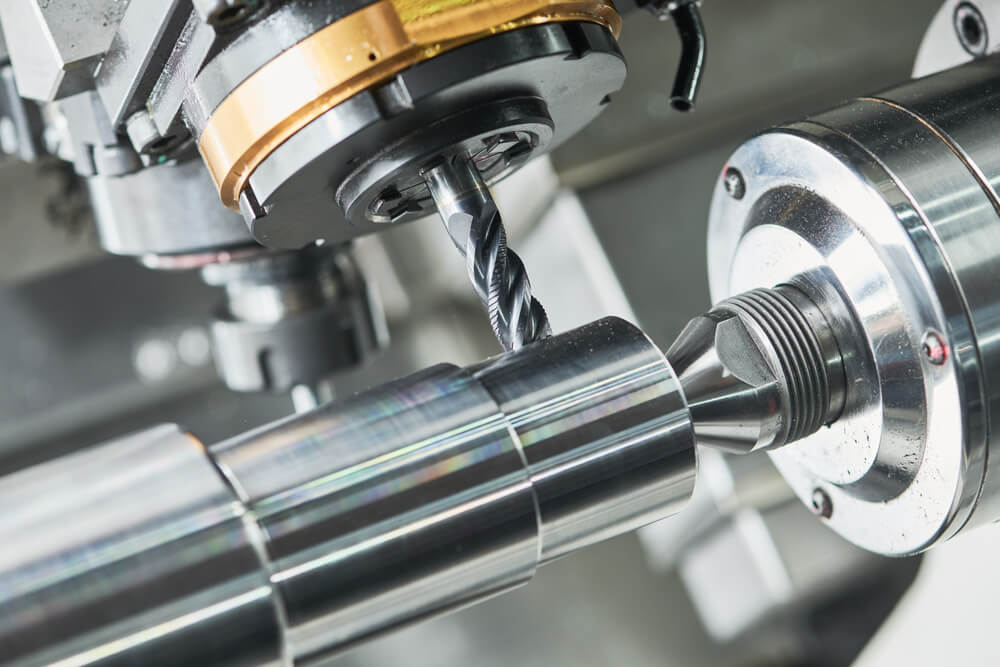
2) Electric discharge machine (EDM)
①Description of electric discharge machine (EDM)
Electronic discharge machine (EDM) or spark machine is a metal processing process that uses sparks to obtain the desired shape. Rapid current discharge between electrodes removes material, while dielectric fluid acts as an electrical insulating fluid to separate the two electrodes.
The workpiece acts as an electrode and must be a good conductor of electricity. High voltage sparks are applied between the electrode and the workpiece. The spark erodes the workpiece.
During this process, the workpiece acts as an anode and the tool acts as a cathode. Controlled sparks help in the machining of the workpiece. The dielectric fluid washes away the debris and helps control the temperature and sparks during machining.
②The advantages of EDM are:
- Applicable to different materials: EDM can effectively process a variety of materials as long as the material is a good conductor of electricity. You can process materials made of tungsten or titanium. You can use EDM to machine hardened materials.
- No mechanical force required. Since no mechanical force is involved, you don’t have to worry about fragile contours or mechanical stress.
- Achieve a variety of shapes: You can use EDM to cut unconventional shapes that cannot be achieved with traditional machines.
③Applications of EDM
Includes injection molding, small hole drilling, and die casting.
If you are looking for an experienced machining manufacturer, Xavier is your ideal choice. The Xavier team is well-equipped to provide high-quality machining solutions. If you need more information or to discuss your machining needs with us, please feel free to contact us.