Inconel Machining: Solving the Challenges of Inconel Machining
Inconel machining stands out in the field of advanced manufacturing and engineering. Because Inconel can cope with the challenges of the machining process with excellent performance, and machining inconel has a promising future at present.
Inconel, a name synonymous with strength, durability, and resistance to extreme environments, is one such material.
This guide delves into the complexities of Inconel machining, providing insights and strategies to effectively address its complexities.
1.What is Inconel?
Inconel is a nickel-chromium-based high-temperature alloy that is widely acclaimed for its ability to withstand extreme pressures and temperatures without losing integrity. Its resistance to oxidation and corrosion makes it a material of choice in challenging operating environments.
For machinists and engineers, Inconel is synonymous with durability and strength, providing solutions for some of the most demanding applications in industries such as aerospace, marine, and energy.
The alloy’s unique properties, including resistance to high temperatures and corrosion, make it an indispensable resource when seeking CNC machining materials that can maintain structural integrity in harsh conditions.
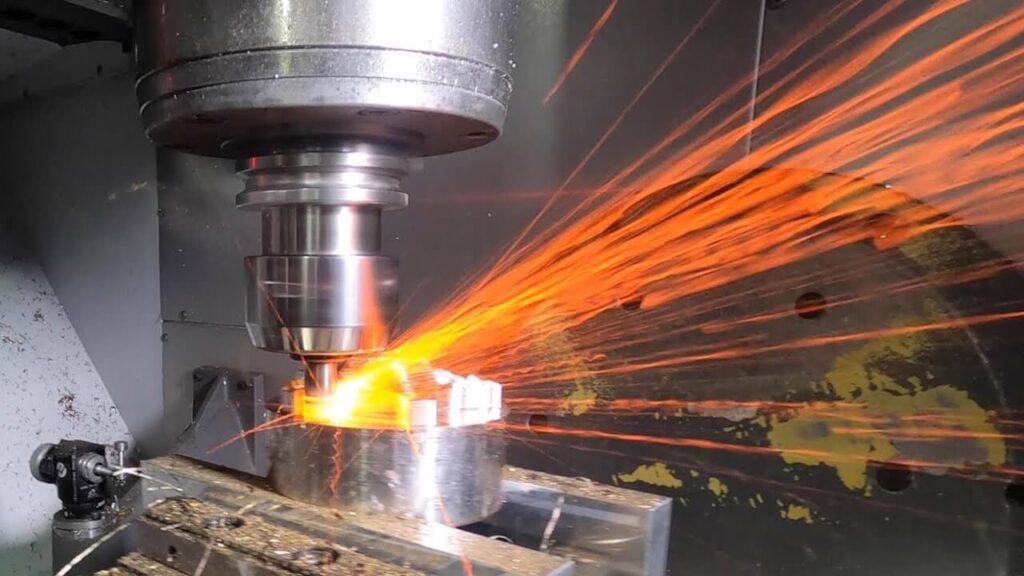
2.Is Inconel difficult to machine?
Yes, machining Inconel is a complex task that requires expertise and precision. While its renowned strength and resilience are beneficial for applications that face harsh environments, they present significant challenges when shaping the material into the desired shape.
The process requires not only specialized cutting tools, but also meticulous machining parameters to effectively manage the alloy’s work-hardening rate and high heat generation. The difficulty of machining Inconel presents challenges that only the most skilled machinists equipped with the right tools and knowledge can handle.
3.How Machinable Is Inconel?
In the realm of advanced materials, Inconel stands out with a machinability rating of 12% on the AISI Machinability Index. While this number may seem modest compared to aluminum and steel, it reflects Inconel’s unique position in the manufacturing industry and paves the way for a deeper exploration of its machining challenges and solutions.
4.What Makes Inconel Machining So Challenging?
The journey of machining Inconel is like navigating a maze of technical obstacles, each requiring a precise combination of skills, knowledge, and technology.
1) High work hardening rate
Inconel’s tendency to work harden similar to steel’s resistance to tempering presents a daunting challenge to machinists. This property requires a strategic approach to machining where understanding and prediction are as important as the cutting tool in hand.
2) High cutting forces and high tool wear
The toughness of Inconel means higher cutting forces, which accelerate the wear of cutting tools. This phenomenon not only tests the durability of the tool, but also the machinist’s ability to adapt and develop a longevity strategy.
3) High heat generation during machining
Inconel’s resistance to deformation at high temperatures is a double-edged sword, generating a lot of heat during machining. This thermal challenge requires a meticulous approach to cooling and tool selection to ensure that the integrity of the workpiece and tool is not compromised.
4) Risk of workpiece deflection
Inconel’s toughness also brings the risk of workpiece deflection, a subtle but critical factor that affects accuracy. This aspect requires a nuanced understanding of machining dynamics to ensure that every cut is precisely calculated and executed.
Key factors contributing to these challenges:
- The alloy’s inherent hardness and toughness
- Its tendency to harden rapidly
- High thermoelasticity that can be converted into heat during machining
- Material strength that poses a risk to tool integrity and workpiece accuracy
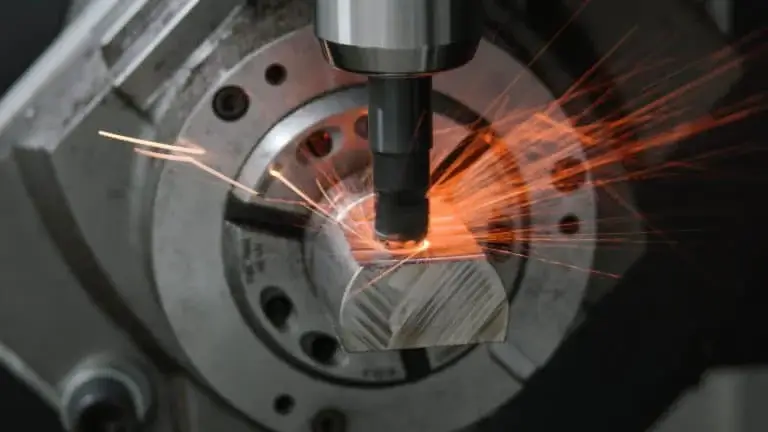
5.What tools are necessary for effective Inconel machining?
Proper tool selection is more than just advice; it is critical to the success of machining Inconel alloys.
1) Selecting the right cutting tools
The key to efficient Inconel machining is selecting the right cutting tools. These tools must not only withstand the hardness of the material, but also minimize the risk of work hardening, which can quickly degrade the tool and affect machining accuracy.
Specifications of an ideal cutting tool:
- Carbide tools: Select carbide tools with a high positive rake angle. This design helps reduce cutting forces and heat, minimizing the potential for work hardening.
- Coated tools: Tools coated with materials such as titanium aluminum nitride (TiAlN) can withstand the high temperatures generated when machining Inconel alloys.
- Geometry: The geometry of the cutting tool should be designed to effectively remove chips from the workpiece, preventing it from being cut again and generating additional heat.
2) The role of coolants in Inconel machining
Coolants are more than just an auxiliary agent in Inconel machining, they are also a key factor in controlling the intense heat generated during machining.
Recommended types of coolants:
- Emulsified coolants: These coolants effectively dissipate heat and help prevent tool wear and workpiece damage.
- High-pressure coolants: The use of high-pressure coolants can effectively penetrate the cutting zone, helping with chip evacuation and temperature control.
3) Optimizing machining parameters
The delicate balance between cutting speed, feed rate and depth of cut is key to machining Inconel alloys, and each parameter needs to be carefully adjusted to mitigate the challenges of the material.
Guidelines for adjusting cutting speed, feed rate and depth of cut:
- Cutting speed: below average to reduce heat build-up.
- Feed rate: optimized to ensure consistent tool engagement and avoid intermittent cutting that causes work hardening.
- Depth of Cut: Control the thermal and mechanical loads on the tool.
4) Ensure a Rigid Setup
A rigid setup is essential to counteract the forces encountered during Inconel machining, ensuring accuracy and integrity of the machined part.
Strategies to Reduce Deflection and Ensure Dimensional Accuracy:
- Tool Holding: Use hydraulic or shrink-fit toolholders to enhance grip and minimize vibration.
- Workholding: Securely hold the workpiece to prevent movement during machining.
- Machine Selection: Use machines with high rigidity and stability to withstand machining forces without compromising accuracy.
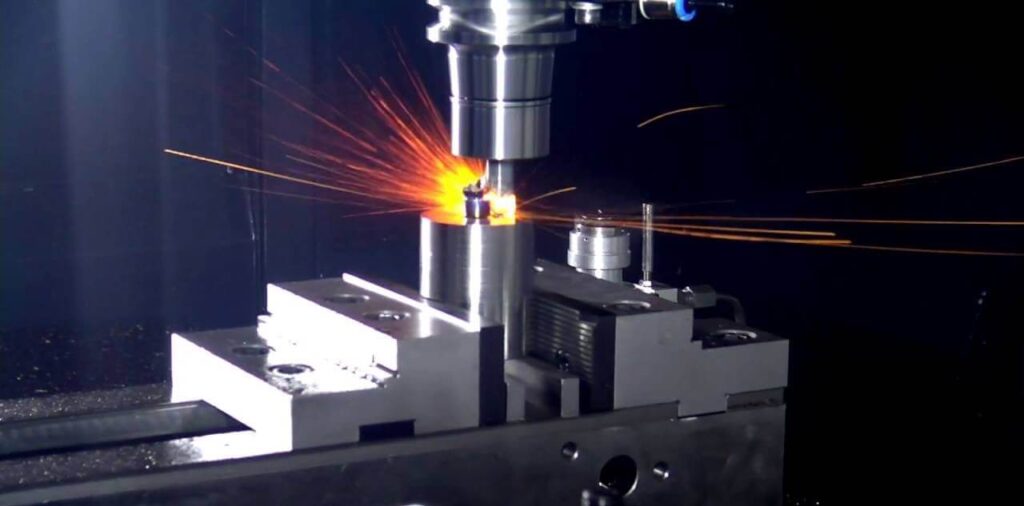
6.What are some advanced tips for machining Inconel?
Now, let’s discuss some advanced tips that can significantly improve the efficiency and quality of Inconel machining.
1) Regularly Check Tool Wear
When machining Inconel, vigilance in monitoring tool wear is non-negotiable. Given Inconel’s tendency to work harden and its abrasive nature, tools wear faster than when machining less challenging materials.
- Importance of Monitoring and Changing Tools
Regular inspections help detect early signs of wear, ensuring that tools are replaced or maintained before they affect machining quality. This proactive measure not only maintains the integrity of the machining process, but also extends tool life, thereby improving cost-effectiveness.
2) Start with Solution Metal
Machining Inconel while it is in solution significantly improves its machinability. The technique involves heating the alloy to a high temperature and then rapidly cooling it to homogenize its microstructure.
- Advantages
Starting with solution metal results in a more uniform grain structure, which reduces the amount of work required to machine the material. This preparation results in improved surface finish, easier chip breaking, and reduced tool wear, making it a vital step for those seeking to optimize their Inconel machining operations.
3) Continuous Cutting with Ceramic Cutting Tools
When continuous cutting is required, ceramic cutting tools are a strong choice due to their robustness and ability to maintain performance at high temperatures.
- Advantages
Ceramic tools are praised for their efficiency in maintaining cut quality over time. Its excellent hardness and heat resistance make it particularly suitable for long, uninterrupted cutting of Inconel, ensuring consistent machining quality without frequent tool changes.
4) Strategies to avoid pecking drilling
While pecking drilling can effectively control chip breaking and heat buildup in some cases, it is not always the best method for Inconel as it may introduce work hardening and reduce machining efficiency.
- Technology
To avoid the challenges posed by pecking drilling, it is recommended to use a drill equipped with internal coolant channels. This design can enhance chip evacuation and heat management, resulting in more efficient drilling operations.
In addition, optimizing feed rates and using drills with appropriate geometry can promote smoother chip evacuation and reduce heat buildup, eliminating the need for pecking drilling.
5) Post-processing operations for Inconel alloys
After the primary machining process is completed, Inconel parts often require additional finishing to meet stringent specifications. These post-processing operations are essential to enhance the physical properties and performance of the final product.
- Grinding and honing
These processes are essential to achieve the required surface smoothness and dimensional accuracy. Given that Inconel is susceptible to work hardening, selecting the proper grinding wheel and honing tool is critical to preventing further hardening and achieving the required tolerances.
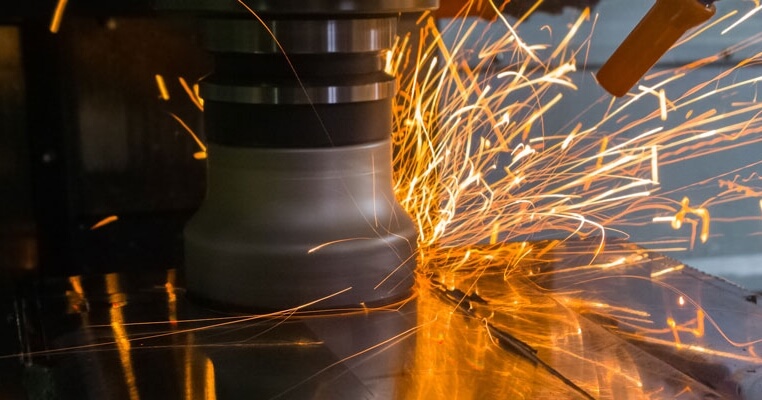
7.Machining Specific Inconel Grades
Due to the different physical and chemical properties of Inconel, different grades of Inconel present unique challenges and opportunities during machining. Understanding these differences is key to optimizing the machining process for each specific Inconel.
1) Inconel 600
Inconel 600 is known for its resistance to oxidation and corrosion, especially in extreme environments. The high nickel content of this grade helps it resist chloride ion stress corrosion cracking.
- Applications: Its high temperature and corrosion resistant material properties make it ideal for use in the chemical industry, aerospace applications, and heat treatment equipment.
- Challenges: Machining Inconel 600 requires tools that can withstand the material’s strength and hardness. In addition, its high nickel content causes wear and work hardening, so hard, lubricated tool materials and appropriate machining parameters must be used.
2) Inconel 625
Inconel 625 has molybdenum and niobium added to the alloy mix to enhance its strength and corrosion resistance without heat treatment.
- Application: Due to its excellent resistance to a variety of severe corrosive environments, this grade is widely used in the marine and chemical processing industries, as well as in aerospace and nuclear reactors.
- Challenges: Similar to other grades, machining Inconel 625 involves managing work hardening and selecting cutting tools that can withstand the abrasiveness of the material. The presence of niobium and molybdenum requires careful control of machining speeds and feed rates to prevent tool wear.
3) Inconel 718
Inconel 718 is characterized by its high yield, tensile and creep rupture properties at temperatures up to 1300°F. This makes it a top choice for high-temperature applications that require high strength.
- Application: Its resilience and strength are well suited for aerospace components, including gas turbine engines and cryogenic tanks.
- Challenges: The machining of Inconel 718 presents great challenges due to its toughness and tendency to work harden. Advanced tool material and coolant technology, as well as a controlled machining environment, are necessary to efficiently machine this grade.
8.What are the machining benefits of Inconel 625 and 718?
Despite the challenges, machining Inconel 625 and 718 offers significant advantages:
- Enhanced durability: Components made from these grades withstand extreme environments, ensuring longevity and reliability.
- Superior corrosion resistance: Its composition offers unmatched resistance to corrosion and high temperatures, making it ideal for critical applications in the aerospace, marine, and chemical processing industries.
By mastering the intricacies of machining different Inconel grades, manufacturers can leverage their unique properties to meet the demanding requirements of a variety of industries.
9.What are the applications of machining Inconel alloys across industries?
Here, we explore the diverse applications of Inconel across industries:
- Aerospace: Turbine blades, exhaust systems, and engine thrust reversers benefit from Inconel’s high-temperature resilience.
- Automotive: High-performance exhaust systems and turbocharger rotors utilize Inconel to withstand the heat and pressure of racing conditions.
- Oil and Gas: Downhole tubing and safety valves in sour gas environments rely on Inconel’s corrosion resistance.
- Power Generation: Gas turbine components, including combustion chambers and rotor blades, are made from Inconel to handle high-temperature operation.
- Chemical Processing: Reactor cores and containment vessels use Inconel to resist corrosive substances and maintain integrity under thermal stress.
- Marine: Propulsion motors and Navy submarine components are made from Inconel for its strength and corrosion resistance in saltwater environments.
- Medical Devices: Surgical and dental instruments benefit from Inconel’s strength and biocompatibility.
- Nuclear: Control rods and reactor cores utilize Inconel to withstand the extreme conditions within nuclear reactors.
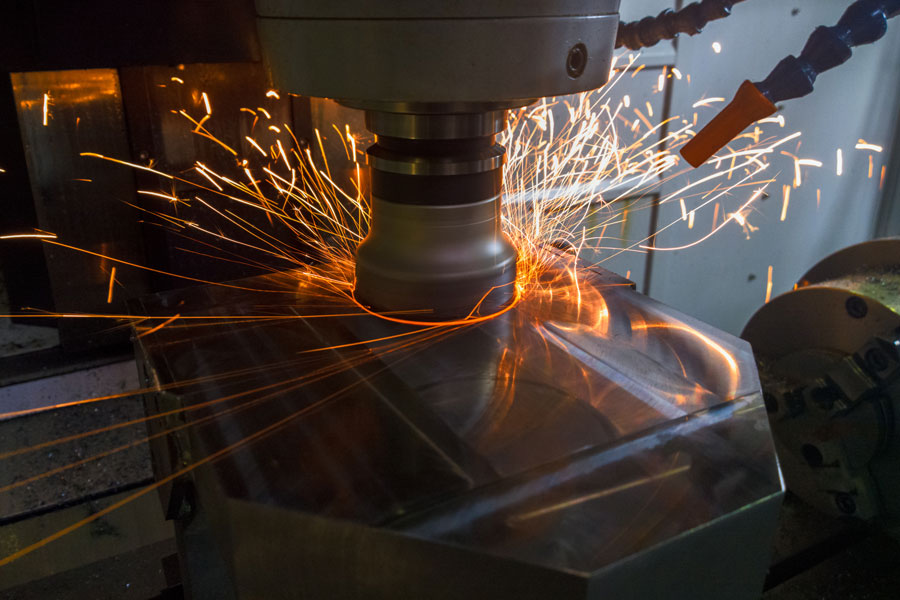
10.How Much Does Inconel Cost to Process?
The cost of processing Inconel is affected by a number of factors and is therefore generally higher than the cost of processing other materials.
Understanding these factors can help in planning and budgeting projects involving Inconel.
- Material Hardness and Work Hardening: Inconel’s hardness and tendency to work harden require slower machining speeds and more frequent tool changes, increasing operating costs.
- Tool Wear: The abrasive nature of Inconel alloys causes increased wear on cutting tools, necessitating the use of premium (and often more expensive) tool materials such as carbides or ceramics.
- Machining Time: Longer machining times due to the need for lower feed rates and speeds to prevent work hardening and tool degradation further increase costs.
- Specialized Equipment: In some cases, machining Inconel requires specialized equipment that can handle its unique characteristics, which is an additional investment for manufacturers.
- Comparative Analysis with Machining Other Materials: Compared to more traditional materials such as steel or aluminum, machining Inconel can be significantly more expensive due to the factors listed above. However, in applications under extreme conditions, the superior performance characteristics of Inconel parts often justify their higher costs.
11.How to Choose an Inconel Machining Service Provider?
The stakes are always high when you enter the Inconel machining service market.
Here are things to consider:
- Technical Capabilities: Advanced equipment is a must for machining Inconel. Look for a service provider equipped with the latest CNC machinery that can handle the precision and rigidity required for Inconel machining. Technologies such as 3-, 4-, and 5-axis CNC milling machines and tools capable of holding tolerances to within ±0.01 mm are indicative of a supplier’s capabilities.
- Industry Experience: Inconel machining means more than just having the right tools; it means knowing how to use them. Experience in a specific industry can significantly impact the success of a project. Suppliers with a proven track record of providing high-quality parts for aerospace, marine, or other industries that frequently use Inconel are more likely to understand your unique needs and challenges.
- Quality Assurance: Consistent quality is non-negotiable. Suppliers should have a rigorous quality management system in place and comprehensive inspection capabilities such as Hexagon CMMs (coordinate measuring machines) and Olympus XRF analyzers to ensure that every part meets your specifications and is defect-free.
- Rapid Prototyping to Serial Production: Whether you need a one-off prototype or serial production, the right service provider will provide scalable solutions. This flexibility allows you to test and validate prototypes before moving on to full production, ensuring that the final product meets all requirements.
- Delivery and Turnaround Time: In today’s fast-paced market, every day counts. Suppliers who can guarantee fast delivery without compromising quality can give you a competitive advantage.
12.Conclusion
Choosing the right Inconel processing service provider is critical. The provider’s technical capabilities, industry experience, commitment to quality, flexibility in order size, and ability to meet tight deadlines play a key role in the success of your project.
As you move forward, consider consulting experts and relying on the expertise of a proven service provider to ensure that your Inconel processing needs are met with precision and care.