The Basics of Machining Polycarbonate
Polycarbonate is a popular CNC machining material that is suitable for manufacturing a variety of structural components across different industries due to its unique combination of mechanical properties. Machining polycarbonate provides many custom PC parts using CNC milling technology.
Although polycarbonate is easy to machine and is less likely to chip or crack during machining, understanding the process of machining polycarbonate is essential to achieving the desired results.
This guide provides a detailed introduction to polycarbonate, its properties, and commonly used polycarbonate grades. Continue reading to the end for more common applications and expert tips on machining polycarbonate.
1.What is polycarbonate?
Polycarbonate (PC) is an amorphous thermoplastic that softens before melting and has no specific melting point. Polycarbonate is primarily available in black and clear rod and sheet forms.
Likewise, when you need a part with excellent light transmittance, polycarbonate is a versatile and durable alternative to standard glass thanks to its amorphous composition, excellent clarity, low weight, and relatively low crystallinity. Unlike other plastics such as acrylic, polycarbonate is heat and impact resistant.
2.Properties of Polycarbonate
PC is a widely used engineering plastic with excellent material properties. Although polycarbonate is available in different grades, here are some of its common mechanical properties:
- High fracture toughness and impact resistance: Polycarbonate is known for its excellent toughness and impact resistance, making it a popular material for high-performance applications.
- Resistance to UV radiation: Specific grades of polycarbonate have excellent resistance to UV rays because they are specially designed to resist 100% of sunlight exposure.
- High ambient temperature and fire resistance: Polycarbonate can withstand temperatures up to 140°C, making it ideal for medical applications that require repeated sterilization.
- Chemical resistance: Polycarbonate has high chemical resistance to alcohols, oils, mineral acids, and aliphatic hydrocarbons.
- Excellent dimensional stability: This engineering thermoplastic has a low shrinkage of between 0.6 – 0.9% and can maintain its dimensions under most conditions.
- Translucency and optical clarity: The amorphous structure of polycarbonate thermoplastics gives it excellent transparency and optical clarity. Additionally, it will achieve a precise 90% light transmittance with a refractive index of 1.548, making it a widely used glass replacement.

3.Commonly Used Polycarbonate Types
Polycarbonate plastics are available in a variety of grades, each with a unique combination of mechanical properties that are suited for specific uses in various industries.
The following are typical polycarbonate grades used in CNC machining:
1) General Purpose Polycarbonate
This grade of polycarbonate has extremely high toughness and a transparency similar to glass. General purpose polycarbonate is ideal for aesthetic purposes due to its polished surface. Additionally, its excellent UV resistance makes it a suitable material for outdoor applications.
2) Glass Filled Polycarbonate
Glass-Filled Polycarbonate is a strong polycarbonate with high impact strength and toughness, making it a perfect replacement for engineering plastics and metals. Since it contains 10-40% glass fibers that enhance the strength of standard polycarbonate, it is an ideal replacement for metal when manufacturing industrial-grade parts.
3) Mechanical Grade Polycarbonate
This polycarbonate grade offers excellent dimensional stability, superior electrical properties, high elastic modulus, and impact resistance. Components made with mechanical grade polycarbonate are often used in applications that require extensive manufacturing work.
4) AMGARDTM Polycarbonate
AMGARDTM Polycarbonate is an extraordinary engineering plastic that has silver ions added to the material to prevent microbial growth on the surface. This polycarbonate is ideal for manufacturing medical devices and equipment, protective shields, and similar applications that require bacteria-free or mold-free surfaces.
5) TUFFAK Polycarbonate
TUFFAK is a versatile polycarbonate plastic variant that is twice as strong as glass. It is compatible with a variety of manufacturing techniques, such as CNC machining and thermoforming. TUFFAK polycarbonate has impressively high dimensional stability and good compatibility with adhesives, coatings, and solvents.
4.Advantages and Limitations of Machining Polycarbonate
Machining polycarbonate parts offers several advantages, such as:
- Polycarbonate is available in a variety of formulations, including FDA-compliant and glass-filled formulations. Therefore, you can find the formulation that best suits your project needs.
- Machined polycarbonate parts have minimal moisture absorption and a high melting point.
- Polycarbonate has high impact resistance and tensile strength, making it suitable for demanding applications such as protective gear and bulletproof glass.
- Polycarbonate variants are transparent and lightweight in nature, transmit light efficiently, and accept color without compromising its transparency.
- Polycarbonate has good machinability as well as excellent heat deflection temperature.
Despite the many benefits of using polycarbonate in CNC machining projects, there are some common limitations:
- Polycarbonate parts are easily scratched and are only compatible with a few surface treatment options, such as coatings and vapor polishing.
- Polycarbonate tends to soften and deform at high temperatures. Excessive heat generated during machining can lead to poor dimensional accuracy, surface finish issues, and part deformation.
- PC is an abrasive that causes rapid tool wear during machining. This increases tool costs and may require frequent tool changes or the use of special tool coatings.
- CNC machined polycarbonate parts can turn yellow due to prolonged exposure to UV rays.
- Large polycarbonate parts can be difficult to machine because the material tends to bend or deform under its own weight or during clamping.
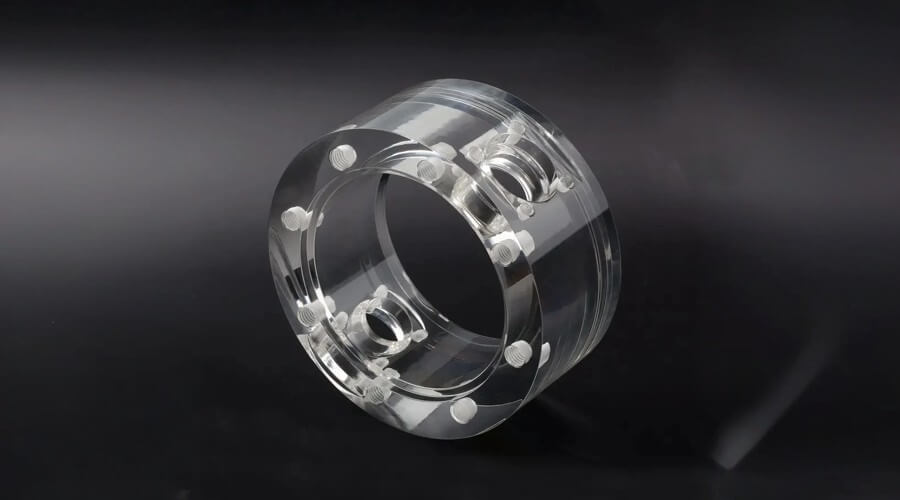
5.Applications of Machining Polycarbonate Parts
Machining polycarbonate parts are commonly used in different industries because polycarbonate grades have various desirable properties.
The following are typical applications for CNC polycarbonate parts:
1) Automotive
Polycarbonate has excellent impact strength and fracture toughness, which are necessary for manufacturing high-quality and reliable automotive parts. Automotive industry manufacturers often use polycarbonate when producing transparent or translucent parts that can withstand high impact, such as bullet-proof windows, turn signal lenses, and headlights.
2) Healthcare
Machined polycarbonate parts are used in different areas of the healthcare sector, from dialysis machine housings to incubators. In addition, polycarbonate has excellent dimensional stability, heat resistance, and toughness. Therefore, machined medical PC parts can withstand FDA-approved sterilization methods such as autoclaving and radiation.
Surgical instruments, blood filters, oxygenators, and reservoirs are typical polycarbonate parts used in the medical industry. Additionally, the transparency of polycarbonate helps doctors monitor and track blood transfusions more easily.
3) Household appliances
Polycarbonate is an ideal material for the production of household appliances such as electric shavers, hair dryers, blenders, and refrigerators. Other common uses for polycarbonate include food containers, fuse boxes, guards, TV housings, greenhouses, skylights, machine guards, and roofs.
6.Finishing options for machining polycarbonate parts
Since polycarbonate material scratches easily, it is compatible with some surface treatments. These surface treatments help improve the physical properties of machining polycarbonate parts to suit the end use.
The following are possible surface treatment options for polycarbonate:
1) Post-machining
Machining is a standard and cheaper surface treatment that eliminates the need for further post-processing of machined parts. Although machined parts may have tiny and visible surface tool marks or scratches, finishing represents a more economical and faster manufacturing option.
However, finishing after machining does not provide an optically clear surface on polycarbonate parts, although machining polycarbonate using diamond tools can provide optical clarity. Therefore, customers must specifically request this finishing during the quote process, as it may increase the cost of the machining.
2) Vapor Polishing
CNC machined parts often have visible tool marks, which can affect the appearance of the product. Vapor polishing is usually used to remove tool marks and scratches by exposing the machined PC part surface to a solution, which reacts with the part surface and melts, causing the material to flow and fill the visible tool marks.
While the surface of CNC machining polycarbonate parts is usually translucent, it becomes nearly opaque if it melts during machining.
Vapor polishing is an ideal post-processing option to flatten the surface of the part to give it a uniform high-gloss or optically clear appearance. However, this surface finish is not suitable for applications that require components with optical clarity.
3) Polishing
This mechanical polishing improves the surface of machined polycarbonate parts by removing tool marks. It involves buffing the surface of the part with a rapidly rotating cotton polishing wheel.
This method is very effective for finishing large parts with simple outer surfaces. However, polishing does not produce as clear a finish on machined polycarbonate as vapor polishing.
4) Anti-Scratch Coating
One of the drawbacks of using polycarbonate is that it scratches easily. Applying a coating to your CNC machining polycarbonate parts helps enhance its scratch resistance and optical clarity.
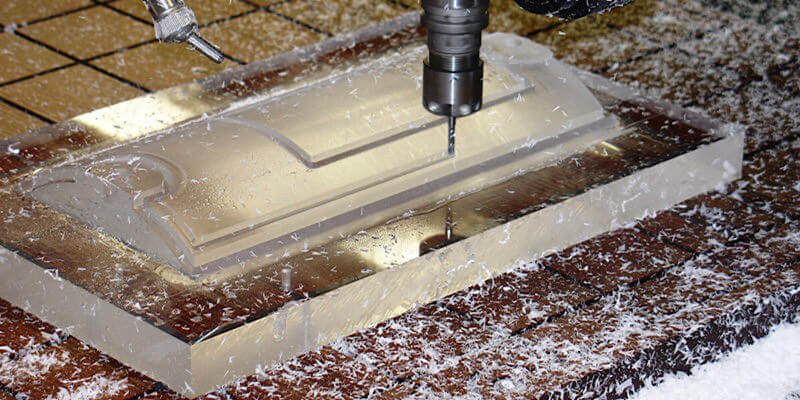
7.Expert Tips for Machining Polycarbonate
Polycarbonate is one of the relatively high-cost CNC plastics. Here are some expert tips for achieving the best results in machining polycarbonate:
1) Milling in multiple steps
Professional machinists recommend milling thicker polycarbonate sheets in multiple steps to achieve clean and consistent edge results. You can mill thin sheets of about 5 mm in thickness in one go. However, you must mill in the opposite direction of the cutting tool rotation to achieve a cleaner milled edge.
2) Use CNC Cutting Tools with Sharp Edges
In addition to polycarbonate’s tendency to chip and stress crack during machining, using blunt/dull-edged tools can also damage the surface of machined polycarbonate parts.
Despite PC’s good machinability, sharp CNC cutting tools must be used to ensure smooth polycarbonate machining and reduce stress on the material.
Additionally, you can use a vacuum cleaner or blower to extract the debris that may accumulate and interfere with the machining process.
3) Choose the right cutting tool with a compatible diameter
Using CNC tools with the right diameter will achieve the best results in machining polycarbonate. Experts generally recommend using single-edge carbide (HSS) milling polycarbonate CNC tools to achieve perfect results.
- When machining panels with a thickness of 5 mm or less, use a tool with a diameter of 4 mm.
- When machining panels with a thickness between 5 – 10 mm, choose a tool with a maximum diameter of 6 mm.
- Use tools with a diameter between 8 – 10 mm for panels thicker than 10 mm.
4) Apply cutting fluid
Using cutting fluid during machining of polycarbonate helps alleviate heat build-up, extract chips, and avoid melting of the material. Machining experts use non-aromatic water-soluble coolants when machining polycarbonate.
It helps achieve the desired surface finish and tighter tolerances for machined polycarbonate parts. More notably, using coolant during machining of polycarbonate ensures extended tool life.
5) Set Proper Stepover and Speed
It is recommended to start machining polycarbonate at the maximum RPM (revolutions per minute) and feed rate that will achieve the best machining accuracy. Then, slowly reduce the feed rate and speed to achieve the best machining results.
However, depending on the type of tool, the required cut-in rate may vary from 20 to 120 IPM.
8.Conclusion
Machining polycarbonate is a popular manufacturing process that produces precision plastic parts using standard cutting tools such as drills and end mills. When the machining parameters are appropriate, the process becomes relatively easy to machine acrylic and other common thermoplastics.