Practical Applications of Brass Turned Parts
Brass turned parts are essential components in many industries and are known for their excellent mechanical properties, durability and beauty, brass turned parts uk is also very cost-effective.
This guide explores the basic aspects of brass turned parts, including their characteristics, manufacturing processes, applications and advantages, to fully understand their value and applications.
1.Properties of Brass
Brass is an alloy composed mainly of copper and zinc, and different proportions of brass can form different types of brass with different properties. Adding elements such as lead, tin and aluminum can further enhance specific properties.
Key properties of brass include:
- Corrosion resistance: Brass has excellent corrosion resistance, especially in saltwater and atmospheric conditions, making it suitable for marine and outdoor applications.
- Machinability: Brass is easy to machine, allowing the manufacture of complex and precise parts.
- Electrical conductivity: Brass has good electrical conductivity, making it an ideal electrical and electronic component.
- Thermal conductivity: Brass also has good thermal conductivity, making it suitable for heat exchange applications.
- Aesthetic Appeal: The golden appearance of brass adds a decorative quality that makes it popular in decorative applications and hardware.
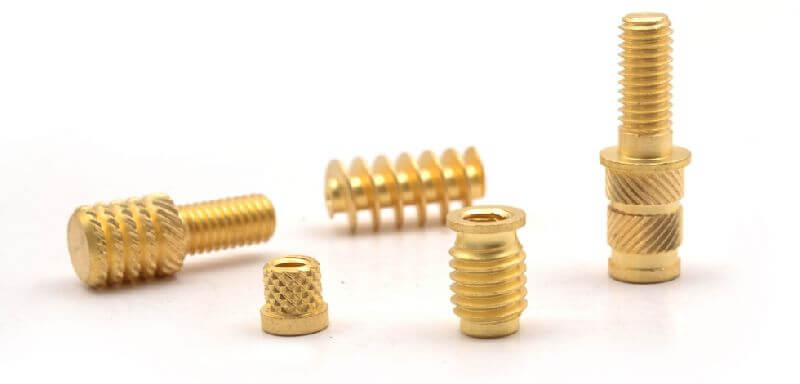
2.Types of Brass Alloys
Different brass alloys can be tailored for specific uses based on their properties:
- Yellow Brass: Brass contains about 60% copper and 40% zinc and is known for its high ductility and strength. It is often used in plumbing and musical instruments.
- Red Brass: Red brass has a higher copper content (usually around 85%) and a lower zinc content, which gives it excellent corrosion resistance and makes it suitable for plumbing and electrical applications.
- Ammunition Brass: This alloy contains about 70% copper and 30% zinc and is used in ammunition casings due to its excellent ductility and strength.
- Naval Brass: Naval Brass contains a small amount of tin and has strong resistance to seawater corrosion, making it ideal for marine applications.
3.Manufacturing Process of Brass Turned Parts
Manufacturing brass turned parts involves several precise steps to ensure quality and accuracy:
1) Material Selection
Choosing the right brass alloy based on the desired properties and application requirements is the first step. The choice of alloy affects the durability, machinability and corrosion resistance of the part.
2) Turning Process
- Setting up: The brass bar or strip is securely mounted on a lathe, a machine tool that rotates the workpiece while the cutting tool moves linearly to remove material.
- Cutting: Various cutting tools shape the brass into the desired shape, including rough turning to remove large amounts of material and finish turning for precision forming.
- Threading and Grooving: Additional operations such as threading (cutting threads in a surface) and grooving (cutting narrow grooves) enable specific design features.
3) Secondary Operations
- Drilling and Tapping: Holes can be drilled and tapped to install fasteners or connectors.
- Milling: Milling operations can create flat surfaces, slots or other complex features.
- Polishing and Deburring: Parts are polished to achieve a smooth surface and deburred to remove sharp edges or burrs.
- Quality Control: Strict quality control measures ensure that parts meet the required specifications, including dimensional inspections, surface finish inspections and material property testing.
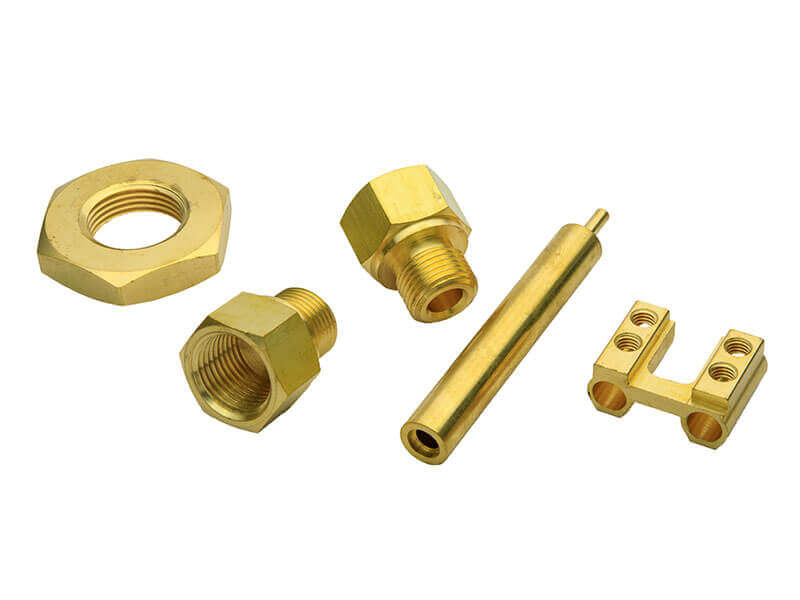
4.Applications of Brass Turned Parts
Brass turned parts are widely used in various industries due to their excellent properties.
Notable applications include:
1) Automotive Industry
- Fuel Systems: Brass parts are used in fuel injection systems, fuel pumps, and carburetors due to their corrosion resistance and machinability.
- Sensors and Connectors: Brass parts are integral to various sensors and electrical connectors within vehicles, ensuring reliable performance and conductivity.
2) Electrical and Electronic Industry
- Connectors and Terminals: Brass is commonly used in electrical connectors and terminals due to its good conductivity and ease of machining.
- Housings and Enclosures: Brass housings protect electronic components while maintaining good conductivity and shielding properties.
3) Plumbing Industry
- Fittings and Valves: Brass’ corrosion resistance and durability make it an ideal choice for plumbing fittings, valves, and connectors.
- Water Meters and Fixtures: Water meters and various plumbing fixtures use brass parts to ensure their reliability and durability.
4) Aerospace Industry
- Precision Components: The aerospace industry relies on brass turned parts to manufacture precision components that require high reliability, such as connectors and fasteners.
- Hydraulic Systems: Brass parts are used in hydraulic systems due to their strength and corrosion resistance.
5) Medical Industry
- Surgical Instruments: Brass is used to manufacture surgical instruments and medical devices because it is biocompatible and can be easily sterilized.
- Diagnostic Equipment: Brass parts are needed in diagnostic equipment because precision and reliability are critical.
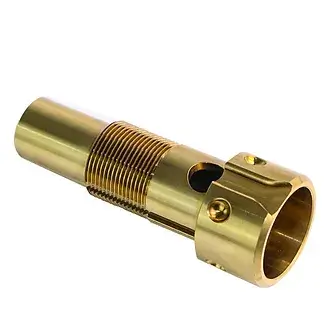
5.Advantages of Brass Turned Parts
Brass turned parts have many advantages that make them a top choice for many applications:
- Durability: Brass parts are strong and durable, and they have a long service life, providing reliable performance for a long time.
- Versatility: The properties of brass make it suitable for a wide range of applications in various industries.
- Cost-effectiveness: Brass is relatively cheap compared to other metals with similar properties, making it a cost-effective choice.
- Recyclability: Brass is fully recyclable, contributing to environmental sustainability.
- Customizability: Brass can be easily machined into complex shapes and designs, allowing for a high degree of customization and precision.
6.Considerations for Choosing the Right Brass Alloy
Choosing the right brass alloy is critical to ensuring optimal performance.
Consider the following factors:
- Mechanical Properties: Evaluate the application’s requirements for strength, hardness, and ductility. Different brass alloys have varying levels of these properties.
- Corrosion Resistance: Consider the environmental conditions in which the part will be used. Marine or outdoor applications require alloys with higher corrosion resistance.
- Machinability: Depending on the complexity of the part, select an alloy with good machinability for precision and ease of fabrication.
- Electrical and Thermal Conductivity: For electrical or thermal applications, select an alloy with suitable electrical conductivity properties.
- Aesthetic Requirements: If the appearance of the part is important, select an alloy with the desired aesthetic qualities.
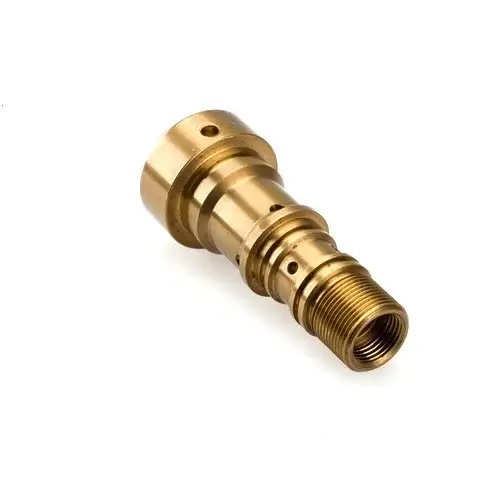
7.Conclusion
Brass turned parts are essential components in a wide range of industries, combining durability, machinability, and aesthetics. By understanding the properties, manufacturing processes, applications, and benefits of brass turned parts, you can make an informed decision to meet your specific needs.
Whether you work in the automotive, electronics, plumbing, aerospace or medical industries, brass turned parts offer a reliable and cost-effective solution to your precision component needs.