Introduction to Brass CNC Turned Parts and Their Applications in Various Industries
Explore the world of brass CNC turned parts in this comprehensive guide. Learn how precision engineering improves the durability and efficiency of these components, making them ideal for complex applications such as gears and valves.
Learn about the benefits of using brass, the CNC turning process, and the customization possibilities to suit your specific needs.
1.Learn about Brass CNC Turned Parts
These components or parts are created, produced, and manufactured with extreme precision, accuracy, and perfection using automatic and semi-automatic machines. They are labeled as “brass” because brass is the primary material used to make these parts.
2.Benefits of Brass for Machining
Of all the different types of metals and alloys, brass tops the list as one of the best, easiest, and most machined materials.
Brass has high tensile strength and is very convenient to work with. This is one of the reasons why brass is known as a great material for low-friction, complex components such as bearings, gears, locks, valves, and other outdoor parts.
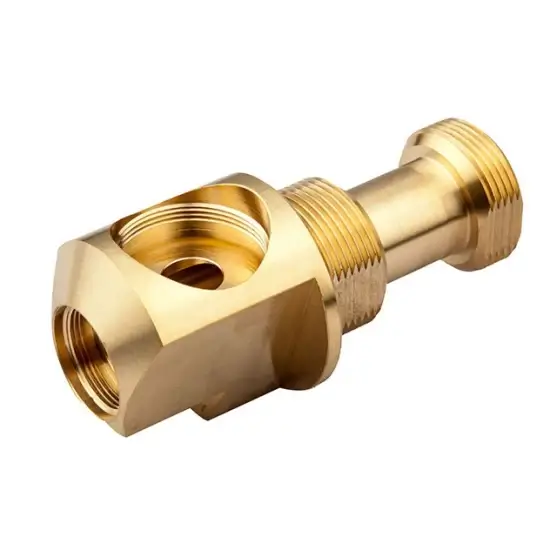
3.Comparing CNC Turning and CNC Milling
Perhaps the most common misconception people have is that they are the same. However, this is not the case. In fact, while both CNC milling and CNC turning are subtractive manufacturing processes, they are actually two completely separate processes.
In CNC turning, the material is rotated and rests against the cutting tool. However, in milling, the cutting tool is rotated and rests against the workpiece or material.
1) Advantages of CNC Turning
The following are the advantages and benefits of CNC turning over traditional or manual turning processes:
- Faster and more accurate assembly
- It produces few defects and produces materials precisely
- CNC machining produces no scrap material regardless of the process
- Reduced energy consumption
- The process requires less manpower
- Faster processing and better results
- And many more
2) Disadvantages of CNC Turning
In contrast, the following are some of the disadvantages and drawbacks of CNC turning:
- They have higher upfront costs and expenses
- The person operating the machine needs to be trained
- Higher installation and application costs
4.Different Types of Turning
While the main task of turning is to reduce the workpiece or subtract material from it, turning is generally divided into two types: roughing and finishing.
Rough turning is the process required to machine and finish a workpiece to bring it to a predetermined thickness. This is done by subtracting the maximum amount of material in the quickest and tightest time possible without regard for surface and overall accuracy.
Finishing or fine turning is a finishing process whose ultimate goal is to ensure that the surface of the workpiece or material is accurate and precise. It does not matter how long the process takes.
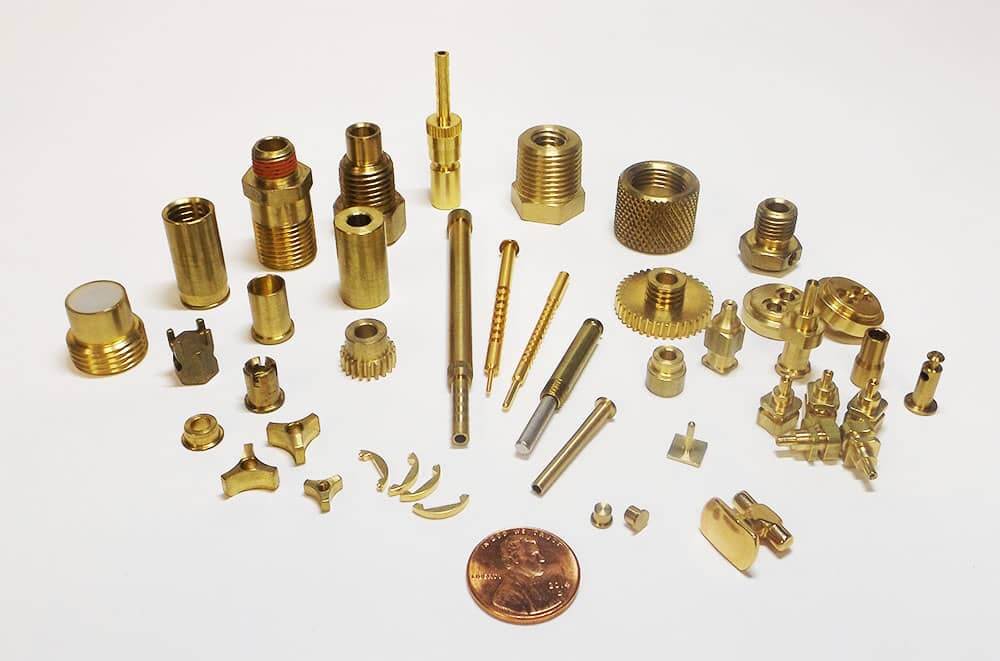
5.Manufacturing Process of Brass CNC Turned Parts
The manufacturing of brass CNC turned parts involves several key steps to ensure the precision and accuracy of the final product.
The process begins with the selection of high-quality brass material, which is known for its excellent machinability and corrosion resistance. The brass material is then loaded onto the CNC lathe, where a series of operations are performed, including:
1) Preparation
The brass material is securely clamped to the lathe, ensuring stability during the turning process. The tools and cutting inserts required for the specific part design are selected and installed.
2) Rough Turning
During this initial stage, the CNC lathe removes excess material from the brass workpiece, forming a rough shape and ensuring the right size. This step helps minimize the amount of material that needs to be removed later, thereby reducing processing time.
3) Finish Turning
Once the rough turning is completed, the CNC lathe performs precise finishing operations. This step involves using specialized cutting tools to achieve the desired size, surface finish, and tolerance. CNC machines use programming instructions to control tool movement, producing accurate and consistent parts.
4) Thread Cutting
If a brass CNC turned part requires threaded features, the CNC lathe will be equipped with thread cutting tools. These tools create internal or external threads with the desired pitch, depth, and shape, ensuring compatibility with other parts.
5) Surface Treatment
After the turning process, some brass CNC turned parts may be surface treated to enhance their visual appeal or improve their functionality. Common surface treatments include polishing, plating, anodizing, or applying a protective coating.
By following this manufacturing process, brass CNC turned parts have precision, reliability, and consistency, making them ideal for demanding applications across a variety of industries.
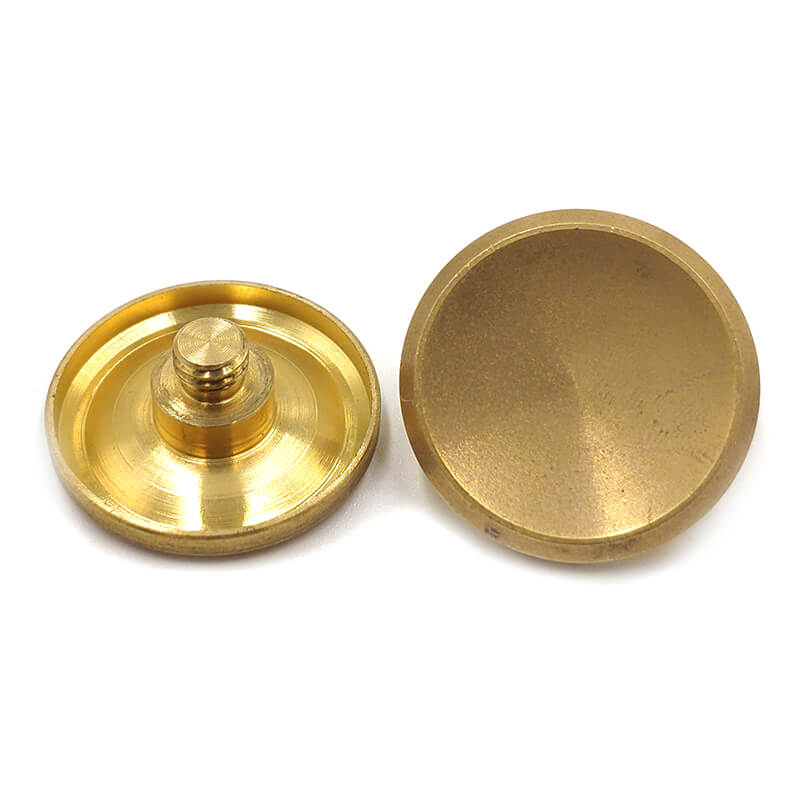
6.Turning Process Products
Typically, the turning process is used to produce small parts or mechanical components for heavy equipment. The most common parts and components you can produce include:
- Flat surfaces
- Threads
- Screws
- Brooches
- Nuts and bolts
- Geometric surfaces
- Cufflinks
- Belt buckles
- Bow ties
- Bracelets
7.Applications of Brass CNC Turned Parts
Brass CNC turned parts are widely used in different industries due to their superior performance and versatility. Here are some key industries that can benefit from using these components:
1) Automotive Industry
In the automotive industry, brass CNC turned parts are used in several key components. These include fittings, connectors, couplings, and valves. Brass’ corrosion resistance and excellent machinability make it ideal for ensuring durability and reliability in a variety of automotive systems.
2) Electrical and Electronics
The electrical and electronics industry relies on brass CNC turned parts to produce connectors, terminals, housings, and other important components. Brass’ high electrical conductivity, coupled with its ability to resist heat and corrosion, makes it ideal for such applications.
3) Plumbing and HVAC
Brass CNC turned parts are widely used in plumbing and heating, ventilation and air conditioning (HVAC) systems. Brass fittings, valves, adapters and connectors are essential to ensure efficient fluid flow, leak-free connections and long life in these applications.
4) Medical Devices
The medical industry requires precision and reliability in the components used in medical devices. Brass CNC turned parts meet these requirements and can be used in medical devices, surgical tools, implants and diagnostic equipment. The biocompatibility of brass and its corrosion resistance make it suitable for a variety of medical applications.
5) Industrial Equipment
From machinery to tools, brass CNC turned parts play a vital role in a variety of industrial equipment. These parts include bearings, dowel pins, bushings and gaskets. The inherent strength, machinability and wear resistance of brass make it an excellent choice for heavy industrial applications.
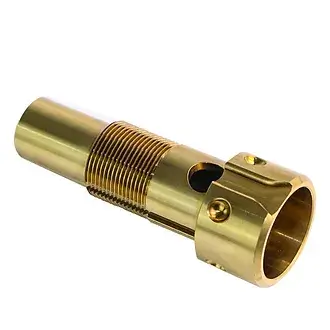
8.Importance of Brass CNC Turned Parts
Brass CNC turned parts play an important role in modern manufacturing processes. Their versatility, precision, and durability make them an integral part of a wide range of industries.
Here are some of the key reasons why these parts are highly valued:
1) Precision and Accuracy
CNC technology enables precise and accurate machining, ensuring brass turned parts meet tight tolerances and dimensional requirements. Using CNC machines eliminates human error and ensures consistent quality across production batches.
2) Cost-Effectiveness
Due to brass’s good machinability, brass CNC turned parts offer manufacturers a cost-effective solution. Efficient production processes and the ability to create complex shapes and features reduce waste, shorten production time, and lower overall costs.
3) High-Quality Materials
Brass is known for its excellent properties, including good thermal conductivity, electrical conductivity, and corrosion resistance. These properties make brass CNC turned parts suitable for a wide range of applications across a variety of industries, ensuring long-lasting performance and reliability.
4) Customizability
CNC turning can easily create complex and customized designs. Manufacturers can produce brass turned parts to specific customer requirements and meet unique project needs. Customization options include different sizes, shapes, thread patterns, and surface finishes.
5) Sustainable Solutions
Brass is a recyclable material, which makes brass CNC turned parts an eco-friendly choice. The ability to recycle brass without compromising its properties helps reduce waste and minimize the environmental impact of the manufacturing process.
9.Cost Considerations When Customizing Brass CNC Turned Parts
Several factors need to be considered when calculating the cost of custom brass CNC turned parts. These are industry-specific parameters such as brass material, design complexity of the part, machine setup and programming tooling needs, batch size, precision tolerances, surface finish, lead time, supplier selection, shipping costs, etc.
Effective cost management requires effective collaboration with manufacturers, clear communication of specific project requirements, and joint search for low-cost, quality-related, off-the-shelf solutions.
10.Custom Brass CNC Turned Parts from Manufacturers
To order custom brass CNC turned parts from a manufacturer, follow these steps:
- Specify Requirements: Clearly define your project requirements.
- Research Manufacturers: Look for reputable manufacturers.
- Request Quotes: Get specific quotes from multiple manufacturers.
- Evaluate Quotes: Consider price, time to market, and product quality.
- Visit the facility: Optional tour of their facility.
- Design and Prototyping: Collaborate on design and prototyping.
- Negotiate terms: Discuss contract and payment terms.
- Place the order: Clarify the order and indicate the specifications.
- Quality Assurance: Establish quality inspections and tests.
- Production and Communication: Maintain contact during production.
- Inspection and Acceptance: Inspect and accept the parts.
- Payment: Pay as agreed.
- Feedback: Provide feedback on their performance.
- Maintain the relationship: Build a good working relationship for future endeavors.
By following these steps, you will be able to effectively order brass CNC turned parts from manufacturers.
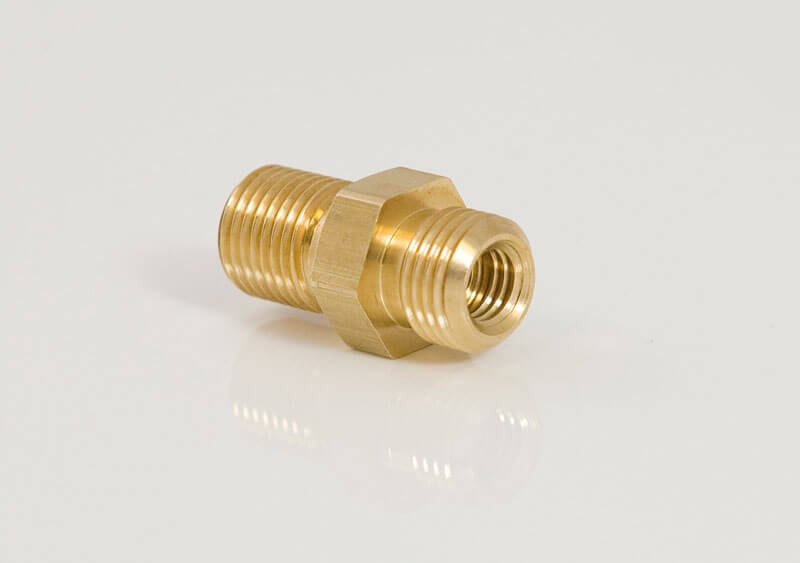
11.Conclusion
This guide provides important information about brass CNC turned parts and their manufacturing procedures, pointing out the special features of using CNC turning processes. It differentiates between CNC turning and milling.
The guide also highlights cost-related considerations and defines the manufacturing process for CNC turned parts. It enables readers to gain the necessary knowledge needed to make better decisions in CNC machining.
In conclusion, brass CNC turned parts embody precision engineering and play a vital role in various industries such as automotive, electrical, plumbing, medical, and industrial.
Their manufacturing process ensures accuracy and consistency, while their superior performance makes them ideal for demanding applications. With their cost-effectiveness, customizability, and sustainability, brass CNC turned parts continue to be a reliable choice for manufacturers in different industries, contributing to the advancement of modern technology and infrastructure.