Plastic CNC Machining:6 Things You Need to Know
CNC machining is a common rapid prototyping process because of its accuracy, precision, compatibility with complex designs, and more. It is a subtractive process that involves computers controlling CNC tools through milling, turning, and other techniques to remove a portion of the workpiece used to form the desired product.
CNC machines are compatible with a wide range of materials, such as metals, plastics, and wood. However, with the rapid development of polymer plastics, many plastic product manufacturers now use plastic CNC machining, which involves using different CNC machine technologies to manufacture plastic products.
There are many aspects to plastic CNC machining. Therefore, this article will cover seven basic things you need to know about the process.
1.Can plastics be CNC machined?
Yes, plastics can be CNC machined. For most people who are familiar with the process, soft metals are the most common workpiece materials in large CNC shops. This is because most rapid prototyping service providers prefer to use injection molding and 3D printing to manufacture plastic products.
However, this does not mean that plastic polymers cannot be machined. Currently, many CNC machinists prefer to use plastics because the advantages of the process complement the inherent properties of plastics. For example, plastics are easier to cut, which improves precision, accuracy, and tight tolerance. As a result, plastics are becoming increasingly popular among quality-conscious businesses.
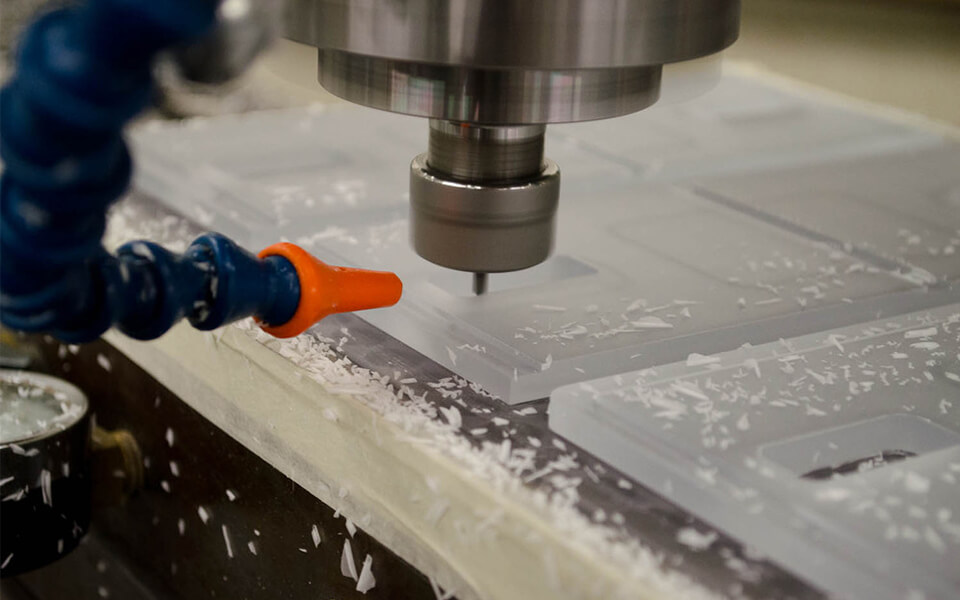
2.Which plastics are best for machining?
Thermoplastics are the most commonly used plastic polymers in CNC plastic machining. This is because they retain their original properties after being melted and reshaped.
To better understand and know which plastic polymers to use, you can check out our CNC material list. However, here are some common plastics that are suitable for many products.
1) Polyoxymethylene (POM)
Polyoxymethylene resin is a thermoplastic known for its rigidity and strength. It is a good plastic CNC machining material because it can perform well in high tensile stress situations. It is heat resistant (but cannot withstand temperatures greater than or equal to 121°C (250°F)).
2) Nylon (Polyamide)
Nylon is a high-purity semi-crystalline CNC plastic machining material known for its excellent heat, mechanical, and chemical resistance. CNC machining of nylon is very simple because the material has tight tolerances due to its physical properties and dimensional stability.
It also behaves like a metal, which is evident in the popular saying, “Machining nylon is like machining brass.” CNC tools used to machine nylon materials should be tungsten carbide tools.
3) PMMA (Acrylic)
Acrylic is a plastic material suitable for CNC machining that is lightweight, has high tensile strength, good wear resistance, and strong rigidity. It has high machinability, but you need to pay attention to some conditions. For example, for CNC cutting, the cutting tool must be a carbide tool with a sharp and sharp blade to obtain a perfect surface finish.
4) PTFE (Teflon)
PTFE (Polytetrafluoroethylene) Teflon is a heat-resistant, water-resistant, electrical-resistant, and chemical-resistant plastic known for its extremely high tensile strength. It is a common CNC plastic due to its density and softness.
However, it has a high coefficient of friction and stress creep properties, which makes it difficult to achieve tight tolerances. Therefore, you or the rapid prototyping service you hire should understand the meaning of its properties and the tools required before machining.
5) PEEK
PEEK, or polyetheretherketone, is a class of high-performance plastics known for its high melting point, corrosion resistance, and excellent mechanical properties. PEEK is more popular for 3D printing; however, its inherent properties along with the accuracy, repeatability, tight tolerances, and other advantages of CNC machines make it ideal for machining.
While PEEK is a popular plastic CNC machining material, you should understand its properties to reduce cracking caused by heat and internal stress.
6) Ultra-high molecular weight polyethylene
UHMW is another CNC plastic machining material that has high tensile strength, corrosion resistance, and other excellent mechanical properties. These properties make it a popular material for rapid prototyping.
However, machining UHMW is not an easy task because it is unstable. Since molding is not possible, machining remains a better option. Therefore, it is best to outsource the material to a service that is experienced in material machining.
7) Prince Edward Island
Polyetherimide, also known as PEI, is a high-performance plastic that is used in a wide range of applications due to its excellent mechanical properties, thermal stability, and chemical resistance. It provides mechanical properties and excellent strength and stiffness to other plastics, making it useful in most applications.
PEI has high operational stability, mechanically and chemically, and maintains stable properties even when used in temperatures up to 340 F (170 C). They include flame retardancy, as it is inherent in the composition, and limited smoke emissions.
The low coefficient of expansion of PEI for CNC machining means that the material remains stable with minimal dimensional changes, making it an ideal choice without the need for constant adjustments. Due to these properties, PEI has become the material of choice for aerospace, automotive, and medical device projects.
Polyamide-imide (PAI) is a plastic with high mechanical properties, high thermal stability, and excellent wear resistance. Due to its heat resistance, it can easily hold up to high temperatures (500°F (260°C)), making it a cut above many other plastics.
Some of the key properties of this plastic include low coefficient of thermal expansion and high dimensional stability, which are great for precision CNC machining work to achieve tight tolerances without deforming the material. Its ability to withstand chemical and abrasive environments makes it ideal for use in aerospace applications, automotive, and manufacturing industries.
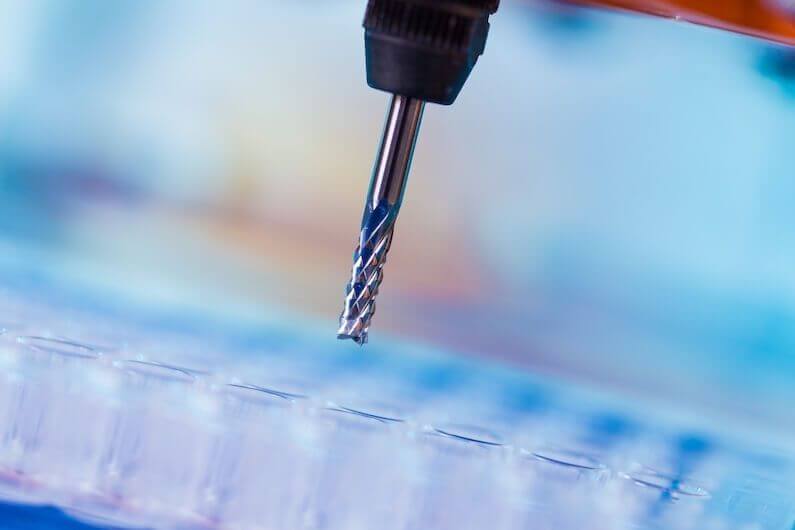
3.How is plastic machined?
Plastic machining involves a variety of processes, depending on the material and the product being manufactured. Among the many processes used in popular rapid prototyping services, the following are three of the most popular plastic machining processes:
1) CNC Turning
CNC turning involves spinning a plastic polymer on a CNC lathe while a stationary CNC tool cuts away portions of it to form the desired shape. The process is well suited for processing a wide range of shapes, although the most common workpiece shape is cylindrical.
Choosing whether CNC turning is the right process requires you or the prototyping service to understand several factors, such as the desired production rate, the outer diameter of the plastic polymer, etc.
2) CNC Milling
CNC plastic milling is the opposite of CNC turning, as the tool rotates while the material is fixed. As with CNC turning, there is a high degree of precision and accuracy as well as uniform productivity due to the corresponding cutting speed of the tool. CNC milling is also suitable for machining flat surfaces and irregular shapes.
The process involves the use of a single-point cutting tool that works on multiple axes (3 axes is common). The number of axes supported determines the flexibility of the process and its suitability for manufacturing complex components.
3) CNC Drilling
CNC drilling involves drilling holes in a material using a cutting tool in the form of a drill. Depending on the type and shape of the drill, holes of varying cross-sections are formed in the material.
CNC machines used for drilling are versatile as they can also perform some milling and turning operations. They also come in different sizes and require experts to ensure cost-effectiveness when manufacturing plastic parts.
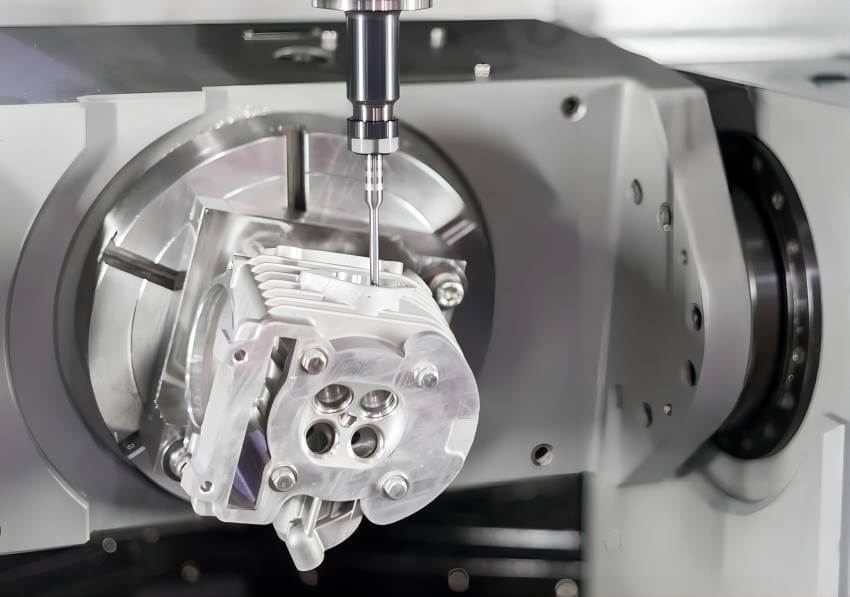
4.How to achieve a perfect finish on plastic parts?
The key to achieving a perfect finish in CNC plastic machining lies in the technology used and the understanding of the material properties. To avoid this situation with plastic products (i.e., to achieve a perfect surface finish), follow these guidelines:
- Avoid using any cutting tools with complex geometries.
- Do not exceed the recommended feed rate for the material being used.
- The plastic material to be processed must be properly fixed. Improper material clamping can lead to vibrations, which in turn can result in imperfect plastic surfaces.
- The cutting speed must also be within the recommended range and also varies for different plastics.
These factors depend on the understanding of the different properties of plastic materials. However, you can further improve the surface finish of any plastic product using finishing techniques such as annealing, sandblasting, powder coating, etc.
5.Why do people prefer CNC plastic machining over other methods?
Plastic polymers are often used with other rapid prototyping methods such as injection molding and 3D printing. However, people have recently started turning to CNC plastic machining due to its advantages.
All three methods are fast and common, and each has its own advantages, but many people now prefer CNC plastic machining capabilities for the following reasons:
1) Precision and Accuracy
CNC plastic machining has unparalleled precision and accuracy. Among the three rapid prototyping methods, the high precision and accuracy ensure high repeatability, as the quality of different plastic products made with this process is similar.
2) Suitable for complex designs
Plastic polymers can be used to make complex and simple products. CNC plastic machining is suitable for making plastic products with complex designs. Although 3D printing also has strong complex design capabilities, the precision and accuracy provided by CNC machines make this process more advantageous.
3) Tight tolerances
CNC plastic machining is the best of the three methods for making products with tight tolerances. This is also due to its high accuracy and precision, making it an important process for most plastic manufacturers.
4) Compatible with different plastic polymers
All methods are suitable for a wide range of materials. However, CNC plastic machining can handle a wider range of plastics well, especially hard plastics, without too many problems.
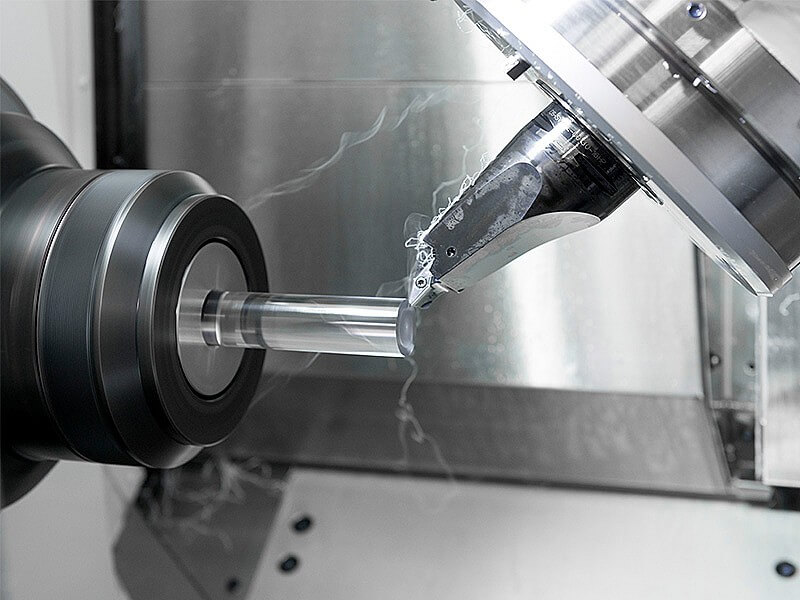
6.What are the common applications of CNC plastic parts?
Plastic polymers have different properties and therefore different uses.
Here are some common applications for CNC plastic parts:
- Production of medical devices and implants.
- For the manufacture of plastic parts used in the food and beverage industry.
- Manufacturing of insulating parts for electrical equipment
- Manufacturing of automotive and aircraft parts
- Production of lenses (acrylic, for example, is known for its optical activity)
7.Conclusion
Plastic polymers are used to manufacture different industrial and household products. For some products, a high level of precision, accuracy, tight tolerances, etc. is required. Therefore, plastic CNC machining is the first choice for many people who want to work with durable and high-quality plastic polymers.
If you are looking for an experienced CNC machining manufacturer, Xavier is your ideal choice. The Xavier team is well-equipped to provide high-quality CNC machining solutions. If you need more information or to discuss your machining needs with us, please feel free to contact us.