A Comprehensive Guide to Casting Aluminum
Casting aluminum is an important part of the metal casting process, which refers to the process of pouring molten aluminum or aluminum alloy into a mold, cooling and solidifying to form an aluminum part of the desired shape. Due to its unique physical and chemical properties, cast aluminum is widely used in various industrial fields.
This article provides in-depth guidance for experts and practitioners in the CNC machining parts manufacturing industry, covering the definition of casting aluminum, its advantages, comparison with other metal materials, different casting processes, common casting aluminum alloys, methods for selecting casting processes, surface treatment of cast aluminum parts, application areas and common problems.
1.What is casting aluminum?
In simple terms, casting aluminum refers to aluminum parts produced using a casting process. During the casting process, molten aluminum or aluminum alloy is poured into a pre-designed mold, then cooled and solidified to form an aluminum product with a specific shape and size. The aluminum material used for casting is called a casting aluminum alloy, which usually contains various alloying elements to enhance properties such as strength, corrosion resistance and fluidity.
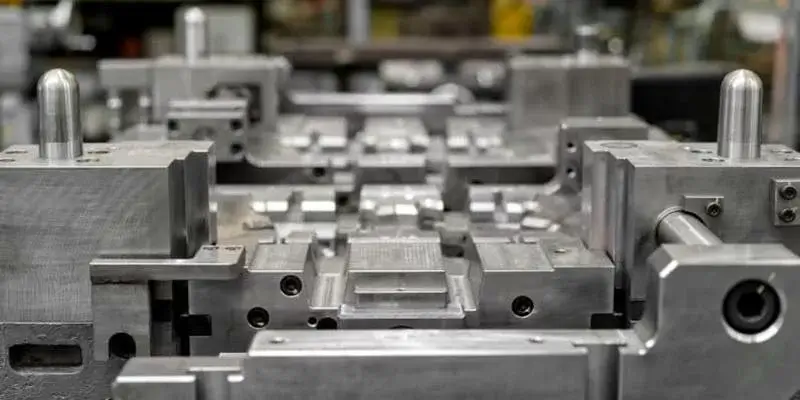
2.Advantages of Casting Aluminum
1) Ability to Create Complex Designs:
The casting process can produce parts with complex shapes and structures without complex machining or assembly processes. This ability gives cast aluminum a great advantage in designing and producing complex parts.
2) Lightweight and strong:
The density of aluminum is only about one-third of that of steel, but its strength is comparable to or even exceeds that of many alloy steels. Therefore, cast aluminum parts can significantly reduce the overall weight of the structure while maintaining sufficient strength, which is particularly important in the aerospace and automotive industries.
3) Excellent corrosion resistance:
Aluminum has good corrosion resistance and can maintain stable performance in humid, acidic or alkaline environments, which makes cast aluminum products widely used in chemical, marine engineering and other fields.
4) Fine surface treatment:
The surface quality of casting aluminum parts can be finely treated by various methods such as sandblasting and anodizing to enhance their appearance and durability. These treatments not only improve the appearance of the castings, but also enhance their corrosion resistance and wear resistance.
5) Faster production speed:
Compared with other metal processing methods, the casting process can quickly produce a large number of parts. This advantage makes cast aluminum popular in applications that require large-scale production.
6) Manufacturing cost-effectiveness:
Aluminum is abundant and relatively inexpensive, and the casting process has high material utilization and low scrap rates. These factors together reduce the production cost of cast aluminum products and make them price competitive.
3.Common problems and solutions for casting aluminum
1) Porosity:
Porosity is a common defect in casting aluminum parts and is caused by gas trapped during the casting process. Solutions include optimizing mold design, controlling pouring temperature, and using degassing technology.
2) Shrinkage:
Aluminum parts shrink during cooling, resulting in dimensional inaccuracies. Solutions include proper gate and riser design, controlling cooling rate, and using appropriate casting methods.
3) Cold shut:
Cold shut occurs when two streams of molten aluminum fail to fuse properly, resulting in a weak joint. Solutions include increasing pouring temperature, improving mold design, and ensuring proper gate and venting.
4) Thermal cracking:
Thermal cracks are caused when aluminum parts are subjected to tensile stress during solidification. Solutions include using alloys with lower thermal crack sensitivity, optimizing cooling rate, and minimizing casting stress.
5) Surface defects:
Surface defects such as roughness, pits and inclusions affect the appearance and performance of cast aluminum parts. Solutions include proper mold preparation, controlling the pouring process and applying surface treatments.
In short, casting aluminum has a wide range of advantages and applications in various industries. By understanding the different casting processes, choosing the right casting method and solving common problems, manufacturers can produce high-quality cast aluminum parts that meet specific requirements and standards.
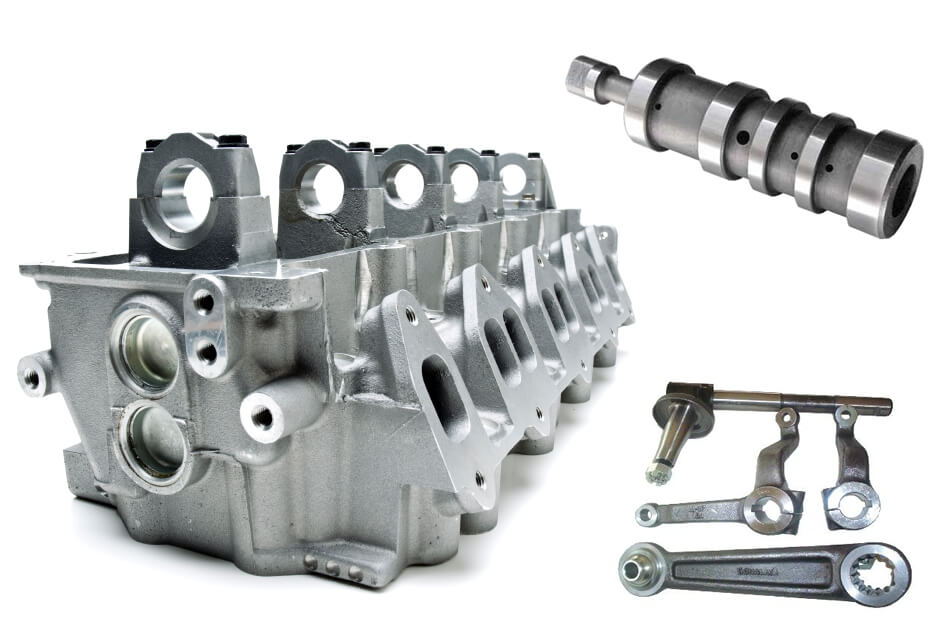
4.Casting aluminum vs. aluminum
Casting aluminum differs from traditional aluminum in performance and use. Cast aluminum refers to aluminum parts produced by casting, and the shape and size are determined by the mold. Traditional aluminum is usually a product formed by processes such as rolling and extrusion. Cast aluminum has higher design flexibility and a wider range of applications, but the cost is relatively high. Traditional aluminum is cheaper, but the shape and size are more limited.
5.Casting aluminum vs. cast iron
1) Weight:
The density of casting aluminum is much lower than that of cast iron, which gives cast aluminum parts a significant weight advantage. In applications where weight reduction is necessary, cast aluminum is a more suitable choice.
2) Dimensional tolerance:
Casting aluminum and cast iron have different characteristics in terms of dimensional tolerance. Cast aluminum parts usually have higher dimensional accuracy and can meet stricter tolerance requirements. In contrast, cast iron parts have relatively low dimensional accuracy.
3) Precision and accuracy:
The casting process can produce parts with higher precision and accuracy, which are suitable for applications with higher precision requirements. In contrast, the precision and accuracy of cast iron parts may be lacking.
4) Thermal resistance:
The thermal conductivity of aluminum is much better than that of iron, so cast aluminum parts have better heat dissipation performance. In occasions where rapid heat dissipation is required, casting aluminum is a more suitable choice.
6.Casting aluminum vs. forged aluminum
1) Different product forms:
Casting aluminum parts are produced by casting, and the shape and size are determined by the mold; forged aluminum parts are formed by forging, and have higher density and strength.
2) Different alloying elements:
Casting aluminum and forged aluminum differ in the selection of alloying elements. Cast aluminum alloys usually contain various alloying elements to improve fluidity, strength and corrosion resistance. Forged aluminum alloys focus more on improving strength and toughness.
3) Different product features:
Casting aluminum parts are light in weight and have good corrosion resistance while maintaining sufficient strength; forged aluminum parts have higher strength and toughness, but are relatively heavy.
7.Different aluminum casting processes
1) Die casting
- Advantages:
High production efficiency: Die casting can produce a large number of parts in a short time.
High precision: Die castings have high dimensional accuracy and surface quality.
Low cost: Die casting molds can be reused, reducing production costs.
- Disadvantages:
High mold cost: The design and manufacturing of die casting molds are complex and costly.
Limited applicability: Die casting is suitable for the production of parts with relatively simple shapes.
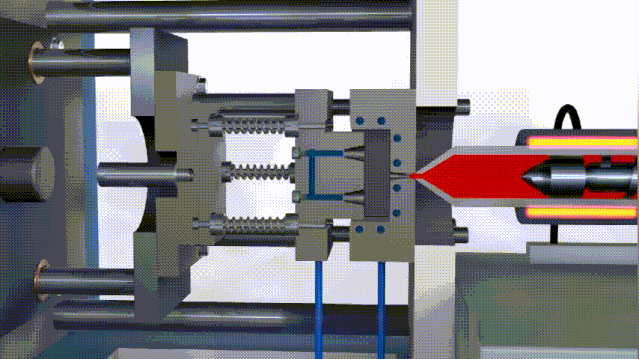
2) Sand casting
- Advantages:
Low cost: The materials used for sand casting molds are cheap and easy to obtain.
Simple process: Sand casting is relatively simple and suitable for the production of various parts with complex shapes.
- Disadvantages:
Low surface quality: Sand casting parts have high surface roughness and require post-processing to improve surface quality.
Limited dimensional accuracy: Due to the limitations of sand casting molds, the dimensional accuracy of sand castings is relatively low.
3) Permanent mold casting
- Advantages:
High precision: Metal mold casting can produce parts with high dimensional accuracy and good surface quality.
Reusability: Permanent molds can be used multiple times, thereby reducing long-term production costs.
- Disadvantages:
High mold cost: The design and manufacture of permanent molds are expensive and time-consuming.
Poor flexibility: Once the mold is made, it is very expensive to change the design or produce different parts.
4) Shell mold casting
- Advantages:
High precision: Shell mold casting can produce parts with very high dimensional accuracy and surface quality.
Suitable for complex shapes: Shell mold casting can produce parts with complex shapes and thin-walled structures.
- Disadvantages:
Complex process: The manufacturing process of shell molds is complex and requires precise control.
High cost: Shell mold manufacturing costs are high and are not suitable for mass production.
5) Plaster mold casting
- Advantages:
Low cost: Plaster mold material is cheap and suitable for small batch or prototype production.
Good reproducibility: Plaster molds can replicate complex shapes well.
- Disadvantages:
Low strength: Plaster molds have low strength and are not suitable for the production of large or heavy parts.
Poor durability: Plaster molds have limited durability and need to be replaced frequently.
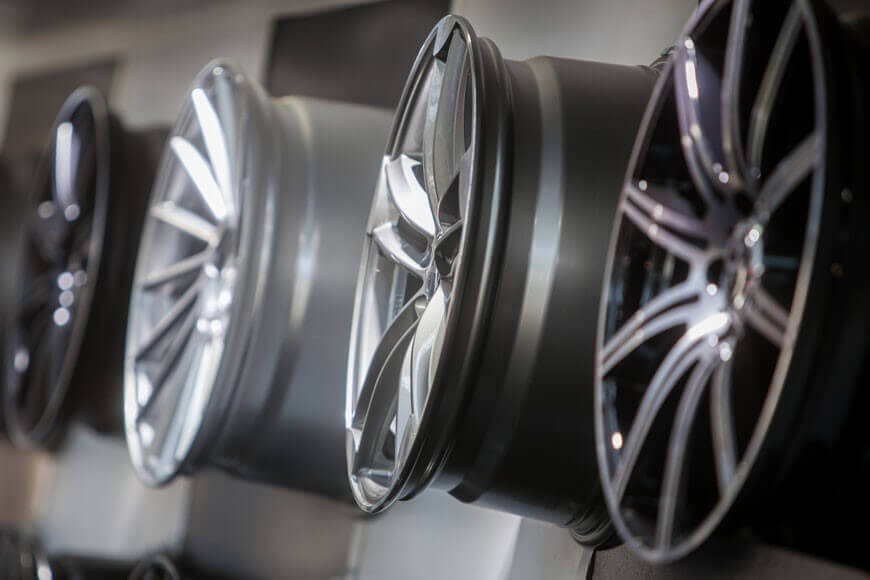
8.Common cast aluminum alloys
1.A356 aluminum alloy:
A common cast aluminum alloy with excellent casting performance, high strength, and good corrosion resistance. It is widely used in automobiles, motorcycles, aerospace and other industries.
2.A360 aluminum alloy:
A cast aluminum alloy with good fluidity and low thermal cracking tendency. It is suitable for the production of parts with complex shapes and large wall thickness variations, such as engine cylinders.
3.A380 aluminum alloy:
A cast aluminum alloy with a high silicon content and good wear resistance and thermal cracking resistance. It is often used for parts that require high temperature resistance and wear resistance, such as engine pistons.
- A383 aluminum alloy (ADC12): A commonly used die-casting aluminum alloy with good fluidity and filling properties, which can produce die-casting parts with complex shapes and high surface quality.
9.How to choose the right aluminum casting process?
1) Design complexity:
The design complexity of the part is the primary consideration in choosing a casting process. For parts with complex shapes and precise structures, high-precision processes such as shell mold casting or die casting may be required.
2) Production speed:
Production speed is also a key factor. If a large number of parts need to be produced quickly, die casting or sand casting may be more suitable.
3) High quantity:
For large-scale production, it is crucial to choose a cost-effective casting process. Sand casting is low-cost and flexible, making it suitable for large-scale production.
4) Material characteristics and properties:
Different casting processes can affect the properties of the material. For example, shell mold casting can produce parts with high strength and toughness, while die casting is suitable for parts with complex shapes and not particularly high strength requirements.
5) Prototyping:
During the product development stage, plaster mold casting is favored for its low cost and rapid prototyping capabilities.
6) Strength and surface treatment:
Select the appropriate casting process based on the strength and surface treatment required for the part. For example, parts that require high strength and good surface treatment may be suitable for shell mold casting.
7) Cost considerations:
The final selection of the casting process also needs to consider cost factors, including mold cost, production cost, post-processing cost, etc.
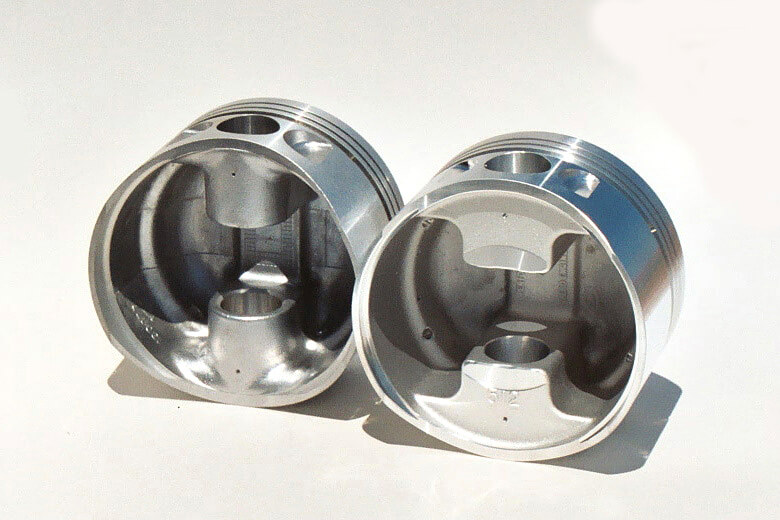
10.Surface treatment of cast aluminum parts
1) Powder coating:
An environmentally friendly and durable surface treatment method. Powder coating is applied to the surface of aluminum parts by electrostatic spraying and then cured to form a hard coating. This method improves the corrosion resistance and aesthetics of aluminum parts.
2) Painting:
A simple and flexible surface treatment method. Appropriate paint and color can be selected for painting as needed. However, the durability and corrosion resistance of the paint coating may not be as good as other methods.
3) Electroplating:
The process of plating a layer of metal (such as chromium, nickel, etc.) on the surface of aluminum parts. Electroplating improves corrosion resistance and aesthetics and provides specific surface properties (such as conductivity, reflectivity, etc.).
4) Anodizing:
An electrochemical process that forms an oxide film on the surface of aluminum parts. The anodized layer improves the corrosion resistance, wear resistance and aesthetics of the parts and can also provide a variety of colors.
5) Sandblasting:
A surface treatment method that uses high-speed sand particles to remove surface contaminants and form a uniform surface. Sandblasting can improve the adhesion of subsequent coatings and provide a matte surface effect.
11.Application areas of cast aluminum
1) Automobile industry:
Cast aluminum is widely used in the production of various automotive parts, such as engine blocks, cylinder heads, intake manifolds and wheels. Cast aluminum is lightweight and corrosion-resistant, which helps improve vehicle performance and fuel efficiency.
2) Aerospace industry:
Cast aluminum plays a vital role in the aerospace industry, and lightweight and high-strength materials are essential. It is used to manufacture aircraft structural components, engine components and landing gear components.
3) Construction Industry:
Cast aluminum is used to produce building materials and structural components such as doors, windows, curtain walls, and handrails. Cast aluminum is lightweight and corrosion-resistant, making it an ideal choice for construction applications.
4) Marine Industry:
In the marine industry, cast aluminum is used to manufacture ship components such as hulls, propellers, and deck fittings. Its corrosion resistance and lightweight properties make it well suited for marine environments.
5) Electronics Industry:
Cast aluminum is used to produce electronic housings, heat sinks, and components for various electronic devices. Its excellent thermal conductivity and electrical properties make it valuable in the electronics industry.
6) Consumer Products:
Cast aluminum is used to produce a variety of consumer products such as cookware, furniture, and sports equipment. Cast aluminum is a popular choice for consumer products because of its lightweight, durability, and aesthetics.
7) Medical Devices:
Cast aluminum is used to manufacture medical devices and instruments such as surgical instruments, imaging equipment, and mobility aids. Its biocompatibility, light weight, and corrosion resistance make it well suited for medical applications.
12.Conclusion
As an important metal casting material, cast aluminum has shown unique advantages and broad application prospects in various industrial fields. From precision instruments in the medical industry to power cores in the automotive industry, from cookware in the cooking industry to flight equipment in the aerospace industry, cast aluminum is recognized for its lightness, strength, corrosion resistance and flexible design.
With the continuous advancement of technology and innovation in manufacturing processes, cast aluminum will play an increasingly important role in more fields and make more contributions to the development of modern industry.