Precision Machining: The Best Guide to Processes, Benefits, and Applications
Manufacturing has changed dramatically over the past century. Previously, our machines were simply configured to handle hand-made parts with ease – precision was not important.
As technology and mobility advanced, more critical moving parts were manufactured – aircraft and automotive parts, where even the slightest deviation could be fatal. The critical need for accuracy gave rise to the discipline of precision machining.
This article focuses on the broad concept of precision machining in manufacturing, emphasizing the key processes and tools that help achieve this precision.
1.What is precision machining?
CNC precision machining is a subtractive manufacturing process that utilizes high-speed CNC machines to create complex geometries with excellent accuracy and tight tolerances.
The idea is to create a part that is very close to the digitally designed dimensions. Tolerances are extremely low, ideally to one thousandth of an inch. The method uses state-of-the-art CNC precision machines that take instructions from a computer system and reproduce the same dimensions in the final part.
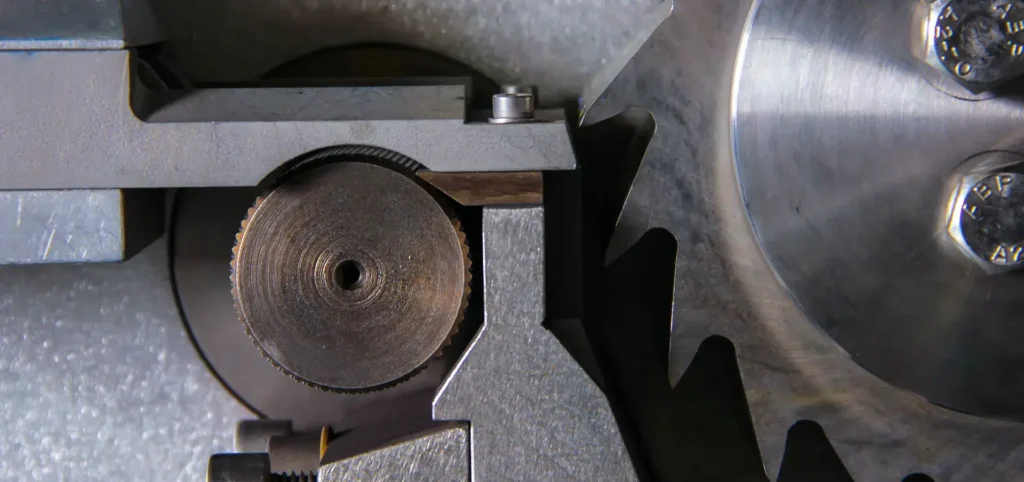
2.Importance of Precision Machining in Modern Machining
The machining accuracy of precision machining determines the operational integrity, safety, and market viability of manufactured products. This accuracy is essential to ensure that engineering parts function to their design specifications without the risk of failure.
In safety-critical fields such as aerospace and medical devices, even minor deviations from specified dimensions can lead to serious consequences, including potentially life-threatening system failures. Therefore, the machining and manufacturing accuracy of these parts is critical to ensure perfect integration and reliable performance under stringent conditions.
In addition, the advancement of high-tech components relies heavily on the ability to perform precision machining. This technology is key to producing complex micro-components that are essential for emerging technologies in areas such as electronics and quantum computing.
Finally, maintaining strict accuracy in machining processes is essential to meeting the highest quality standards. This not only helps maintain the manufacturer’s reputation, but also helps to build and maintain consumer trust in a highly competitive industry.
3.Overview of Precision Machining Process
Precision machining is a series of carefully planned steps that work together to produce a part that perfectly matches its design.
1) Design using CAD (Computer-Aided Design)
The process begins with a sketch of the part. Engineers then use CAD software to create a graphical model that lays the foundation for the design. Popular CAD tools include AutoCAD and SolidWorks – the latter is known for its powerful 3D design capabilities.
2) Conversion to CAM (Computer Aided Manufacturing)
A CNC machine cannot interpret a graphical model directly; it requires machine-readable code. It comes as a separate module, but most modern CAD software now includes CAM functionality.
With a single command, the software converts the 3D model into a series of lines of code, including G-code and M-code. G-code defines the cutting tool path and coordinates, while M-code manages all auxiliary functions, such as tool changes and coolant flow.
3) Material Selection and Preparation
The choice of material depends primarily on the requirements of the part, machinability, and cost. In most applications that require hardness and strength, steel is usually the first choice. When weight is a concern, such as in aerospace applications, manufacturers may choose lightweight aluminum. This is covered in more detail in subsequent sections.
4) Precision Machinery Configuration
Machine setup involves selecting and accurately calibrating precision machine tools, checking fluid and coolant levels, and possibly performing dry runs to ensure everything is set up correctly.
5) Machining Execution
Once everything is set up, the machining process can begin. During this process, the initial stages of the machining process are monitored. Some machines may require technician attention to make adjustments, such as calibrating tool position or modifying feed rates to accommodate changes in material hardness or tool wear.
6) Post-processing steps
Although precision-machined parts are usually close to their final shape when they come out of the machine, some parts may require additional finishing, such as polishing or grinding. The final step is a quality assurance check to confirm that each part meets the exact dimensions specified.
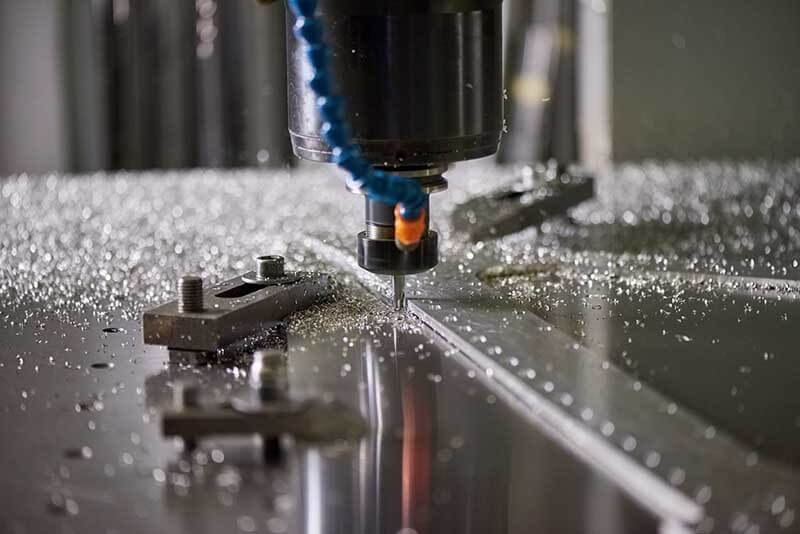
4.Explore the types of precision machining machinery
There is a lot of debate about precision machining technology, but people may be curious about the machine settings that achieve such precision. Therefore, here is a brief introduction to some CNC precision machining equipment.
1) CNC milling machines
CNC milling machines use rotating tools to remove material from the workpiece. These machines are controlled by CAD/CAM software, which enables them to perform different operations, such as pocket milling, contour milling, and surface profiling.
They are ideal for mold machining and creating complex features on metal and plastic parts. Different configurations include vertical milling machines, bed milling machines, turret milling machines, C-frame milling machines, and gantry milling machines.
Advantages:
- Can produce parts with tolerances up to 0.0004”.
- Compatible with a wide range of materials, including metals, plastics, and composites.
- Great for surface contouring and making pockets.
Disadvantages:
- More material waste compared to additive processes such as 3D printing.
Applications:
- Automotive parts, aerospace components, complex parts in molds.
2) CNC Turning Centers (Lathes)
In a CNC lathe or turning center, the workpiece rotates relative to a fixed cutting tool to form a precise symmetrical shape, such as a shaft. Some lathes also have integrated live tooling capabilities, allowing them to perform other processes besides turning. For example, a Y-axis lathe allows you to offset the center to create complex geometries. It also allows tapping, milling, drilling, and turning.
Advantages:
- High accuracy in creating symmetrical parts.
- Live tooling enables multi-process machining.
- Suitable for large-scale production.
Disadvantages:
- Less versatile for non-cylindrical parts.
Applications:
- Symmetrical parts: shafts, rods, cylindrical parts.
3) Swiss-Type Lathes
Swiss-Type Lathes differ from conventional lathes in that the headstock moves linearly, rather than being stationary. Guide bushings behind the headstock allow for precise movement of the workpiece. These machines are ideal for machining extremely small and complex parts.
Advantages:
- Close tool and workpiece distances minimize the risk of tool deflection.
- Parts with tolerances up to 0.0001” can be produced.
- Higher RPMs can be run compared to conventional lathes.
Disadvantages:
- Higher tooling costs.
- Limited bar stock sizes.
Applications:
- Implants, surgical instruments, and microelectronic components.
4) Multi-Axis Machining Centers
Generally speaking, machining allows movement in three axes: X, Y, and Z. Multi-axis machines allow machining in 4 or more axes; up to 12-axis machines are available. Multi-axis machines are able to perform multiple operations on a single machine. For example, one machine can perform water jet cutting, engraving, and milling.
Advantages:
- Complex parts can be machined without repositioning the workpiece.
- Reduce overall production time and improve workflow efficiency.
- Increased innovation potential in part design due to fewer geometric constraints.
Disadvantages:
- Higher initial investment.
Applications:
- Prototyping, aerospace, automotive parts, and complex medical devices.
5) Mill-turn CNC Center
A multi-axis machine that integrates CNC milling and turning functions into one machine. It allows both workpiece rotation and cutting tool movement. Live tooling capabilities are also provided.
Advantages:
- Lower space requirements than separate milling and lathes.
- Improve product consistency by minimizing handling between operations.
Disadvantages:
- Complex configuration and setup.
Applications:
- Cylindrical parts that require keys and slots.
6) CNC Grinding Machine
Precision grinding machines use grinding wheels to achieve high-precision surface finishes and tight dimensional tolerances on parts. They are often used to perform finishing operations on machined parts after milling or turning operations to obtain a smoother surface or specific dimensional tolerances. Surface grinders, cylindrical grinders, and centerless grinders are a few common types.
Advantages:
- Automated machines; can run continuously for weeks.
- Provide good repeatability.
- Compatible with a wide range of materials.
Disadvantages:
- Time-consuming process
Applications:
- Finishing of automotive parts such as gears, shafts, etc.
7) CNC Drilling Machines
CNC drilling machines feature a stationary workpiece that rests on a small fixed bed and the drill bit rotates (from the top) to form precise holes. Their main use is to drill holes for fasteners or assembly operations. These drills come in various types, including vertical, bench, and radial drilling machines, and are suitable for CNC operations.
Advantages:
- Hole location and size have high accuracy and repeatability.
- Automated operations reduce human errors and increase production efficiency.
Disadvantages:
- Only drilling operations are available.
Applications:
- Hole for fasteners in metal products; Wood industry
8) Electrical Discharge Machine (EDM)
EDM machines use electrical discharge/sparking to remove material to form. They help to precisely machine metals (even hard metals) and can produce complex designs that are difficult to achieve with traditional machining. There are two types of EDM machines, including wire-cut EDM machines and forming EDM machines.
Advantages:
- Ideal for hard or brittle materials that cannot withstand mechanical stress.
- Provides micron-level accuracy.
- Good at cutting materials with sharp corners and intricate internal details.
Disadvantages:
- Slow compared to other machining methods.
- Only suitable for conductive metals.
Applications:
- Molds, fixtures and precision parts manufacturing, holes less than 0.1mm
9) Laser Cutting and Engraving Machines
Laser cutting machines use a high-powered laser beam as a cutting tool to cut, engrave or mark materials. These machines can cut and engrave metals and non-metals. Available in a variety of configurations, from flatbed lasers for sheet materials to 3D lasers for cutting and engraving complex shapes, desktop lasers are also available.
Advantages:
- Slower than other processing methods.
- Applicable only to conductive metals.
Disadvantages:
- Limited to certain material thicknesses and types.
Applications:
- Manufacturing of industrial parts, decorative items, and crafts
10) Waterjet Cutting Machines
Waterjet cutting is a non-thermal cutting method that uses a high-pressure (up to 60,000 psi) stream of water, mixed with abrasive particles, to cut the material. Because the process does not introduce heat, it prevents deformation of the material and changes in its inherent properties.
Advantages:
- Versatile and can cut most materials.
- Leaves a smooth surface that often eliminates the need for secondary processing.
- Environmentally friendly and does not generate hazardous waste.
Disadvantages:
- Higher operating costs due to the use of abrasives and high water consumption.
Applications:
- Cutting of all types of materials (metal, plastic, stone, etc.)
5.Selection of precision machining materials
Precision materials are suitable for a variety of materials. The following table lists common materials, properties and end uses.
Class | Material | Characteristics | Machinability | End uses |
Aluminum | Lightweight, corrosion – resistant | Easy | Automotive parts, aircraft components | |
Stainless Steel | High corrosion resistance, excellent mechanical properties | Varies by alloy | Food industry, medical devices, and marine applications. | |
Metal | Brass | Good corrosion resistance, excellent machinability | Very easy | Plumbing fittings, electrical connectors, decorative items. |
Copper | Excellent electrical and thermal conductivity | Moderate | Electrical wiring, heat exchangers, roofing. | |
Bronze | Strong, corrosion – resistant | Difficult | Bushings, bearings, coins, marine hardware. | |
Titanium | Lightweight, strong, corrosion – resistant | Difficult | Aerospace structures, medical implants | |
Plastics | ABS | High strength, toughness, good heat resistance | Easy | Automotive components, consumer goods, electronic assemblies. |
PC (Polycarbonate) | Impact – resistant, transparent | Moderate | Safety equipment, optical lenses, electronic enclosures. | |
PMMA (Acrylic) | Transparent, lightweight | Easy | Signage, displays, light fixtures. | |
POM (Acetal) | High stiffness, low friction, wear resistance | Moderate | Precision gears, bearings, electrical engineering components. | |
PA (Nylon) | Strong, wear – resistant, low friction | Moderate | Gears, bearings, automotive components. | |
PEEK | High temperature and chemical resistance | Difficult | Aerospace parts, medical equipment | |
Composites | FRP (Fiberglass Reinforced Plastic) | Good strength – to – weight ratio, corrosion resistance | Moderate to difficult, abrasive on tools | Automotive body panels, marine vessels, construction. |
Ceramics and advanced materials | Alumina | Excellent hardness, wear resistance, electrical insulation | Very difficult | Cutting tools, wear – resistant components. |
Zirconia | High strength, toughness, heat resistance | Very difficult | Dental implants, cutting tools, ball bearings. | |
Silicon Carbide | Extremely hard, thermal and wear resistance | Very difficult, and requires specialized equipment | High – performance applications like aerospace, and nuclear parts. |
1) Material selection considerations
When selecting materials, consider machinability, physical properties, cost and application. Typically, manufacturers are interested in two physical properties, strength and hardness – machinability depends on these two quantities. The higher the hardness, the more difficult it is to machine. However, such difficult-to-machine materials are very suitable for use as tools. Cost is also an issue, especially in large-scale production.
6.Multiple applications of precision machining in various industries
Precision machining can be applied in various fields where parts need to fit seamlessly. Some applications include:
Industry | Specific Applications |
Aerospace Industry | Aircraft engines, structural components, landing gear |
Medical Industry | Surgical instruments, implants, prosthetics |
Automotive Industry | Gear components, engine parts, couplings |
Electronics Industry | Connectors, circuit boards, enclosures |
Tool and Die Making | Molds, dies, cutting tools, jigs and fixtures |
Energy Sector | Turbine components, drilling equipment |
Defense Sector | Weapon prototypes, missile systems, armored vehicle parts |
7.Advantages of using precision machining technology
Manufacturers turn to precision CNC machining technology because of its many advantages:
1) High precision and small tolerances
The main advantages of precision machining processes are their high precision and small tolerances, with a standard tolerance level of about 0.005 inches. Tolerance refers to the amount of variation allowed in part dimensions.
Generally speaking, there are four standard types of machining tolerances:
- Single-sided tolerance, which allows variation in one direction;
- Double-sided tolerance, which allows deviation on both sides of a specified dimension;
- Composite tolerance, which represents the net tolerance obtained by adding and subtracting all dimensional tolerances of the part;
- Limit tolerance, which specifies the dimension as a range, such as 10 to 12 mm.
2) Complexity and flexibility of precision machining in manufacturing
Precision machining enables manufacturers to create complex geometries with high accuracy and repeatability, which is critical for industries such as aerospace, medical and automotive that require precise dimensional tolerances and complex features.
In addition, the precision machining flexibility provided by CNC machine tools means that designs can be quickly adjusted by simply changing software parameters. This adaptability reduces the time and cost required to create and modify tools or molds, facilitating efficient prototyping and customization. This combination of sophistication and flexibility greatly improves manufacturers’ ability to effectively meet diverse and changing product demands.
3) Efficiency and Speed
With automation and control systems running in the background, CNC precision machining greatly speeds up machining time. It is estimated that CNC machines are 200 to 300 times faster than traditional machines.
In addition, machine configuration, programming, and CAD/CAM software integration keep everything under control. This means minimal setup time, which increases the speed and efficiency of the product.
4) Improved Quality and Reliability
In addition to speed, computer control ensures that every part manufactured is exactly the same and meets the specified dimensions. Tight control over the machining process also reduces errors in the production process.
In addition, because parts are precisely cut with fine tools, the final surface rarely requires secondary finishing. Precision also reduces waste and reduces the likelihood of producing unqualified parts.
5) Cost-effectiveness
Although the initial setup of precision machining may seem expensive, precision machining is cost-effective for both large-scale and customized production.
While traditional manufacturing methods may require multiple stages and machines to produce a single component, precision machining typically requires only a single setup to complete a part.
In addition, each component is cut to exact dimensions, so material waste is minimal. Automation eliminates much of the manual labor and reduces the error rate.
8.Accuracy vs. Precision in Precision Machining: A Comparative Analysis
In the field of machining, precision and accuracy are often used interchangeably, but they describe different aspects of measuring quality.
Precision refers to how close the dimensions of a machined part are to the reference values listed in the design specification. If a part matches the CAD design exactly to the millimeter, it is considered to have high precision.
In contrast, accuracy measures the consistency of the output of multiple production runs of the same part. If a machining process produces parts that are nearly identical to each other but not necessarily close to the design specifications, it is considered accurate. Precision refers to the repeatable accuracy of the machining process, not how close it is to a specific value.
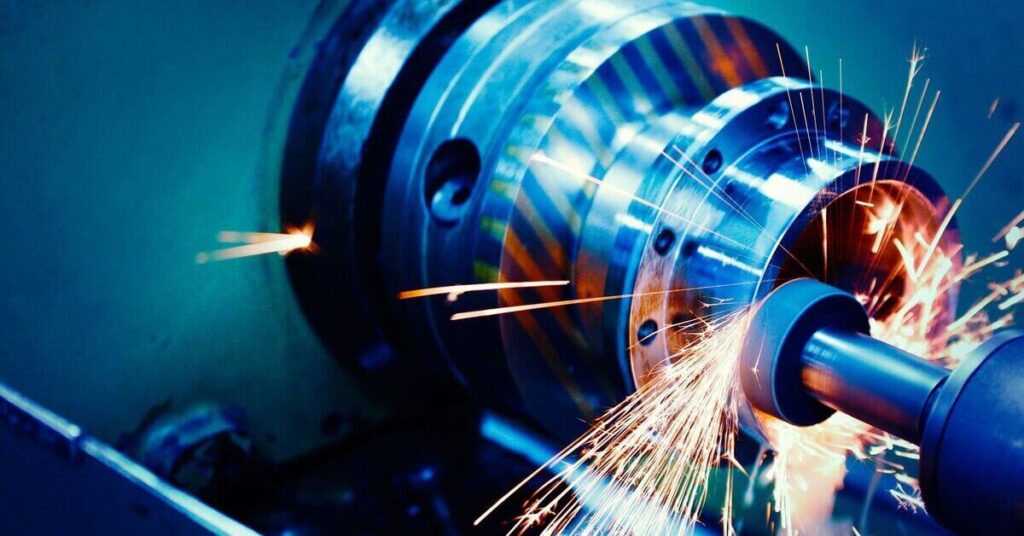
9.Potential Disadvantages of Precision Machining
Precision machining has its highlights in various aspects, but there are also some disadvantages.
1) High initial investment
Due to the advanced capabilities of CNC machine tools, their initial cost is much higher than that of traditional machine tools. Industrial-grade CNC machines start at around $100,000, with some models going as high as $500,000.
2) Complex Setup and Operation
Compared to traditional machines, CNC machines are more complex to set up, primarily because of their complex tooling setup. Additionally, operating these machines requires a skilled precision machinist, which increases overall labor costs.
3) Economic Scalability
CNC precision machining is well suited to producing specific batches of products, but may not be economical for large-volume production. This limitation is due to the high setup costs and the time required to configure the machine for each new job.
10.Conclusion
Today’s machines are complex assemblies made up of numerous microscopic parts, each of which must be perfectly synchronized to function as a whole. Precision machining is critical here – it ensures that each component is manufactured to exact dimensions.
There are a variety of CNC machining equipment to choose from to perform specific cutting tasks. As the world continues to move toward more advanced technology and micro systems, the importance and use of CNC precision machining will only increase.
If you are looking for an experienced CNC machining manufacturer, Xavier is your ideal choice. The Xavier team is well-equipped to provide high-quality CNC machining solutions. If you need more information or to discuss your machining needs with us, please feel free to contact us.