Benefits of low volume CNC machining: The Ultimate Guide
While manufacturers often overlook low volume CNC machining, there are many benefits to adopting this process. Going directly from prototyping to mass production comes with risks and additional expenses. Low volume manufacturing is a bridge between the two processes.
Overall, low volume machining minimizes manufacturing risks, reduces time to market, and facilitates easy design modifications. In order to maximize the benefits of low volume CNC machining, it is important to understand how it works. There are some tips that should be followed to minimize time and budget when using CNC machining for small-scale production.
1.What is low volume CNC machining in CNC machining?
Low volume CNC machining is a machining service used to produce parts in quantities as low as 10 to 1,000. Most often, it acts as a link between prototyping and mass production of new and emerging products. This service is very important for companies that produce small batches of specialized parts.
In addition, it is an effective way to adjust certain production practices as production increases. With small batch production, manufacturers can test product defects before making a huge financial investment. Overall, low volume CNC machining can further save costs while manufacturing high-quality parts.
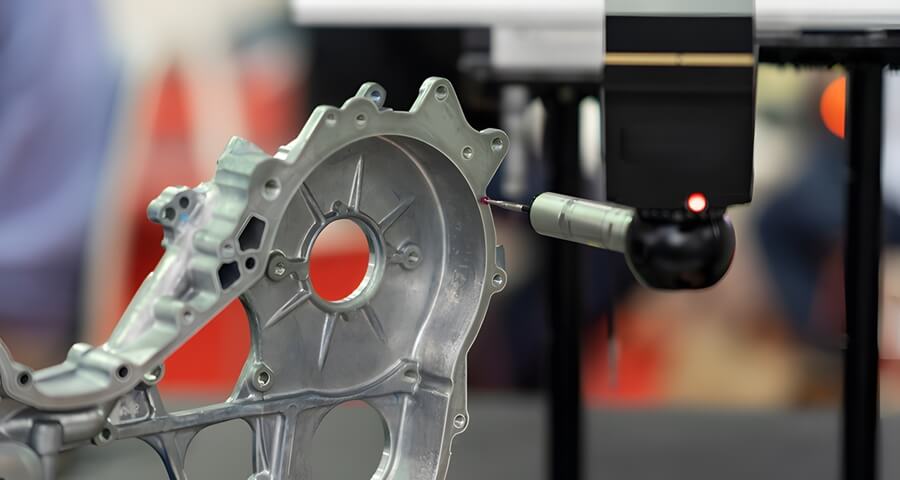
2.What capabilities are required for low volume CNC machining?
The capabilities required for low volume CNC machining include, but are not limited to, the following.
1) CNC milling
CNC milling involves using CNC tools to remove material from a workpiece. This gives the part the desired shape and design. The movement and operation of the cutting tool is fully automated.
From wood to plastic and metal, CNC milling machines can process a wide range of materials. Since the machine is automated, it is ideal for complex, low-volume operations.
2) CNC turning
CNC turning works similarly to CNC milling. In CNC turning, the cutting tool is stationary while the workpiece rotates to form the shape of the part.
Manufacturers use CNC turning to create high-precision parts for low volume CNC machining. It provides an excellent surface finish. However, the tool wears easily and may need to be replaced when mass production begins.
3) Coordinate Measuring Machine (CMM) Inspection
CMM inspection ensures the quality of low volume parts by detecting discrete points using a probe to measure dimensions. This process is very important for parts used in critical applications. By evaluating the parts after production, you can quickly identify and adjust errors. However, the person operating the machine should be skilled and experienced.
4) Mechanical Subassembly
The mechanical subassembly process is a critical aspect of low volume production. This process is very useful when the parts are too large. It involves creating small, precise parts before assembling them into a whole. Thus, mechanical subassembly ensures that the manufactured products are of the highest standard. Through this process, manufacturers can modify the design and functionality of the parts to meet the needs of the end user.
5) Finishing Services
Post-manufacturing finishing is an important aspect of low volume CNC machining. Finishing services range from plating and etching to heat treatment and passivation. These different processes help improve surface defects, adhesion, chemical and corrosion resistance, and increase the hardness and durability of the parts.
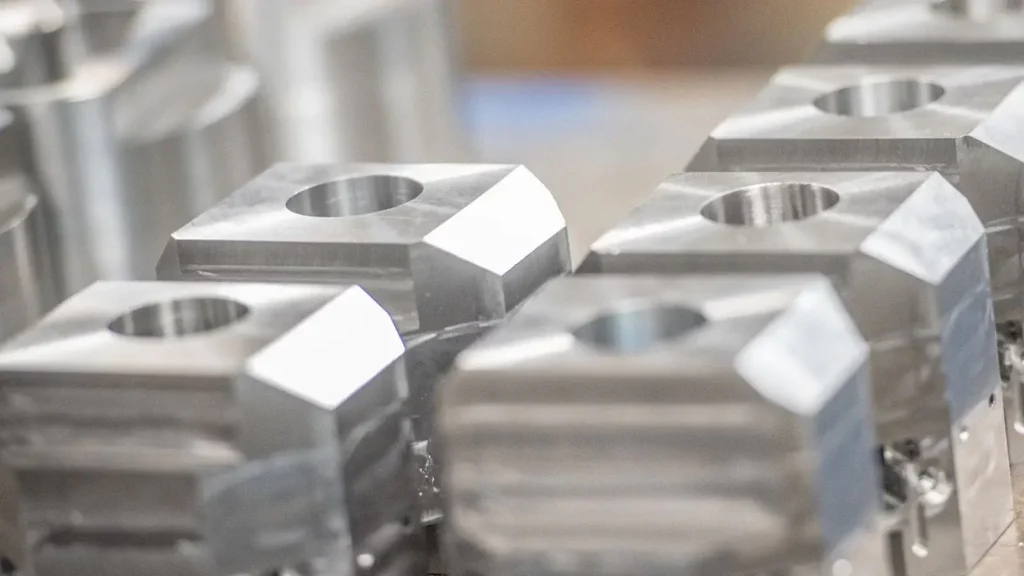
3.Advantages of Low Volume CNC Machining
Low volume CNC machining is essential for producing high-quality parts in a short period of time. This service has many advantages.
1) Short Lead Time
The time it takes to get a product to market can determine its success. Low volume CNC machining reduces lead time. This feature makes low volume production best suited for new designs.
Like other on-demand manufacturing services, you can produce parts in a very short time. With low volume CNC machining, you can ensure maximum profits before your competitors’ products hit the market.
2) More Precision
Low volume CNC machining is fully automated. Therefore, the process produces more accurate and precise parts. Also, it reduces the risk of physical and functional defects. Since the parts produced meet strict specifications, it is an ideal machining service for the aerospace and medical industries.
3) No Tool Investment Required
With low volume CNC machining, you do not need tools such as molds to produce parts. Usually, the cost of producing and maintaining these tooling systems is quite high.
In addition, tooling time can increase the lead time of the product. Low volume CNC machining does not have these disadvantages. This makes the process the most ideal process for manufacturing parts in a short time.
4) More Post-Processing Available
Surface finishing is crucial as it can determine the performance of the part. There are a variety of surface finishing processes to choose from for low volume CNC machined parts.
Anodizing, sandblasting, powder coating, and painting all help improve the aesthetics and functionality of a part. However, it is important to choose the most appropriate method because it will determine the function of the part.
4.Tips for low volume CNC machining to save time and cost
To get the best results from low volume CNC machining, consider the following points.
1) Choose the right material
For low volume CNC machining, using the wrong material can increase the cost of machining. While almost all materials are suitable for CNC machining, very hard materials require special attention. Ease of machining is a decisive factor when choosing a machining material.
Take steels, for example, they are perfect for any part of a car due to their high strength and durability. However, high carbon steels are not easy to machine. It is important to use the most affordable and durable functional materials.
2) Avoid thin walls
CNC machining is a time-consuming process, especially for novices. To maximize time, it is necessary to avoid thin and high wall thicknesses. Furthermore, low volume parts with too thin walls require more capital investment and may negatively impact turnaround time.
In addition, thin wall machining requires considerable expertise and a high degree of accuracy and precision. This is because the part may bend or deform under pressure. If this cannot be avoided, use the right materials and tools for thin wall machining.
3) Keep the design simple
It is important to keep the design simple and standard. When the part is complex, it is recommended to make it in a smaller size first and then assemble it.
In addition, the complexity of the part determines the type of tooling. Very complex designs require additional CNC machining tools. In addition, complex designs may increase the risk of inconsistency and human error.
4) Use only necessary post-manufacturing finishing
Surface finishing is the last step in low volume CNC machining. There are many finishing options to choose from. To avoid unnecessary expenses, it is important to use the most appropriate option for the part. Cost, product functionality, and durability issues may influence your choice.
For example, anodizing and powder coating, which increase hardness, may be best suited for parts used outdoors.
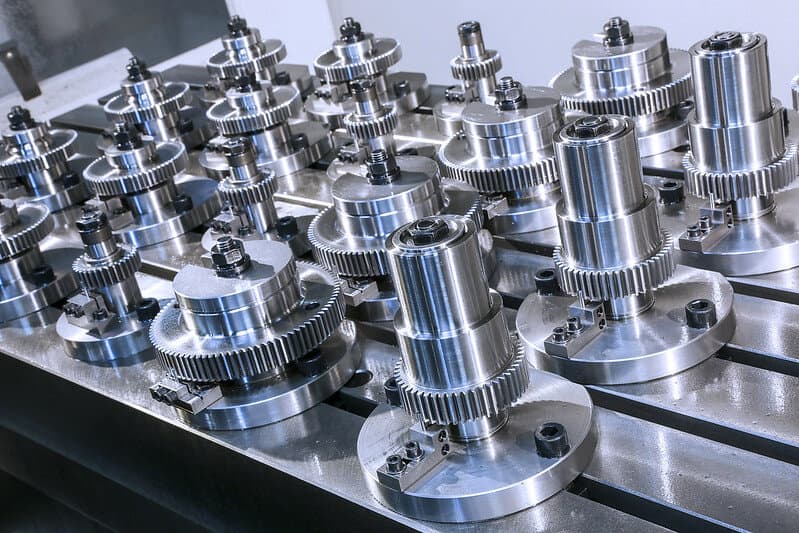
5.Other low volume CNC machining processes
In addition to custom CNC machining, rapid prototyping and 3D printing are the most common processes used by manufacturers for low volume production.
1) Low volume 3D printing
This additive manufacturing process provides rapid production for small-scale manufacturing. With 3D printing, the design is not subject to any restrictions. Each production stage can be completed quickly and you can manufacture parts in a few hours.
In addition, 3D printing can easily modify the part design and hardly any waste is generated. However, 3D printing is not compatible with many materials and the size of the printed parts is limited.
2) Low volume injection molding
This involves different manufacturing processes such as low volume injection molding or die casting, which require high-precision tools to manufacture parts. Usually, the material is melted before molding.
Rapid prototyping is an excellent way to manufacture parts with complex shapes and geometries. However, high mold investment and high design modification costs are important disadvantages of injection molding.
6.Conclusion
Low volume CNC machining is a way to test product functionality and customer preferences before mass production. The service helps manufacturers gradually increase the volume of their products in the market while making necessary modifications.
If you are looking for an experienced CNC machining manufacturer, Xavier is your ideal choice. The Xavier team is well-equipped to provide high-quality CNC machining solutions. If you need more information or to discuss your machining needs with us, please feel free to contact us.