Sheet Metal Processing: Process Types, Benefits and Options
In the field of industrial machinery, sheet metal processing plays a vital role. Sheet metal processing covers the entire process from design to finished product, involving many key links such as material selection, process determination, and precision control. This article will deeply explore the common process types and significant advantages of sheet metal processing, helping users make more informed choices when choosing sheet metal processing.
1, Sheet Metal Processing Types
1.Laser Cutting
Laser cutting uses high-power industrial lasers to cut metal sheets into the desired shape and size. It is divided into two categories: melting cutting and ablative laser cutting.
Modern laser cutting machines mainly include CO2 lasers and fiber lasers. CO2 lasers use infrared light to cut materials. They have lower power and slower speed, but they have smoother surfaces when cutting thicker materials; fiber lasers are faster and more powerful and can cut thicker overall materials.
Advantages:
Compared with mechanical cutting, laser cutting is faster and more efficient, with better surface finish and can adapt to strict tolerance requirements. A variety of shapes can be obtained without custom molds, suitable for a variety of metals and other materials, and can cope with different material thicknesses. It is very suitable for operations such as metal annealing, etching and engraving serial numbers. With the help of modern CNC control, complex individual cuts and complex production runs can be performed.
Disadvantages:
Material may affect the quality of the final product due to heat-induced structural changes. Reflective materials are difficult to cut and are not suitable for most plastics or wood. Adjustments are required when cutting metal sheets of different thicknesses, and edge hardening may require additional treatment.
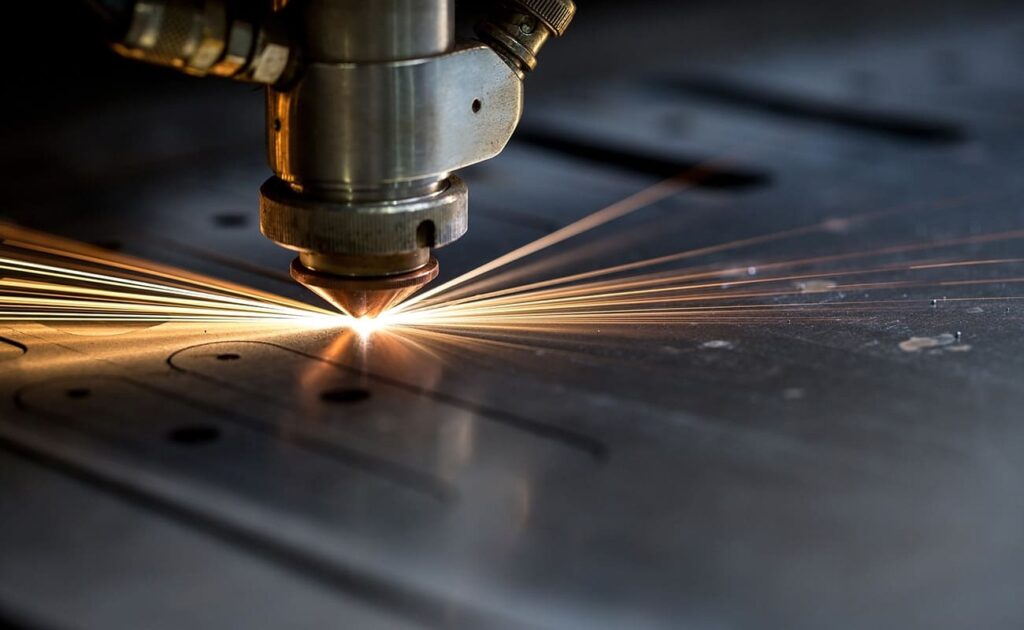
2.Plasma Cutting
Use an accelerated jet of hot plasma to cut conductive materials, such as metals. Compressed gas is ejected in the form of a high-speed jet toward the material being cut, generating an arc in the gas between the electrode and the conductive material, ionizing the gas to form a plasma jet, which is heated to a temperature sufficient to melt the material being cut, and the temperature can reach over 20,000°C.
Advantages:
Very neat edges can be obtained, the cutting speed is faster than many alternative cutting methods, the incision width is narrow, the precision is high, and the cost is lower than laser cutting and water jet cutting.
Disadvantages:
Not suitable for non-conductive materials, high temperatures may cause problems with the material being cut, and it is not suitable for thin and medium-thin metal parts. It will generate radiation, and workers need to wear protective equipment. It is less accurate and slower than laser cutting, and post-processing may be required at the cut edge.
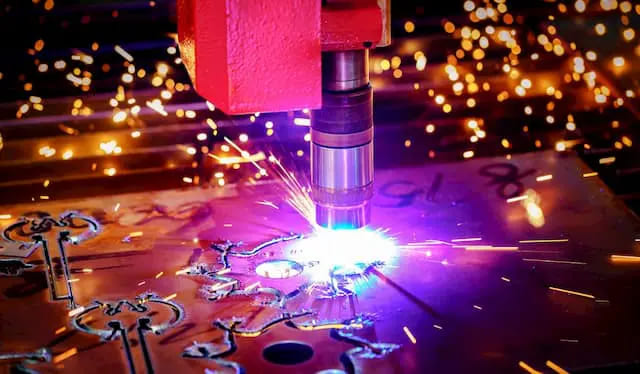
3.Water jet cutting
Water jet cutting uses a mixture of high-pressure water and abrasive to cut metal. Under the action of a hydraulic pump, the water pressure is increased to 60,000 psi, and the metal surface is cut through abrasion in the form of a fine jet.
Advantages:
Highly accurate, complex cutting can be performed, avoiding the influence of heat-induced structures on metal plates, small incision width, suitable for a variety of metals and other materials, smooth cutting edges, and reduced post-processing requirements.
Disadvantages:
Cutting time is slower than other methods, thick cuts are not as clean as other methods, edges often taper, and post-processing is required to obtain the best results. It may be more expensive than other cutting methods. Due to cost and installation time, it is not suitable for small-scale production.
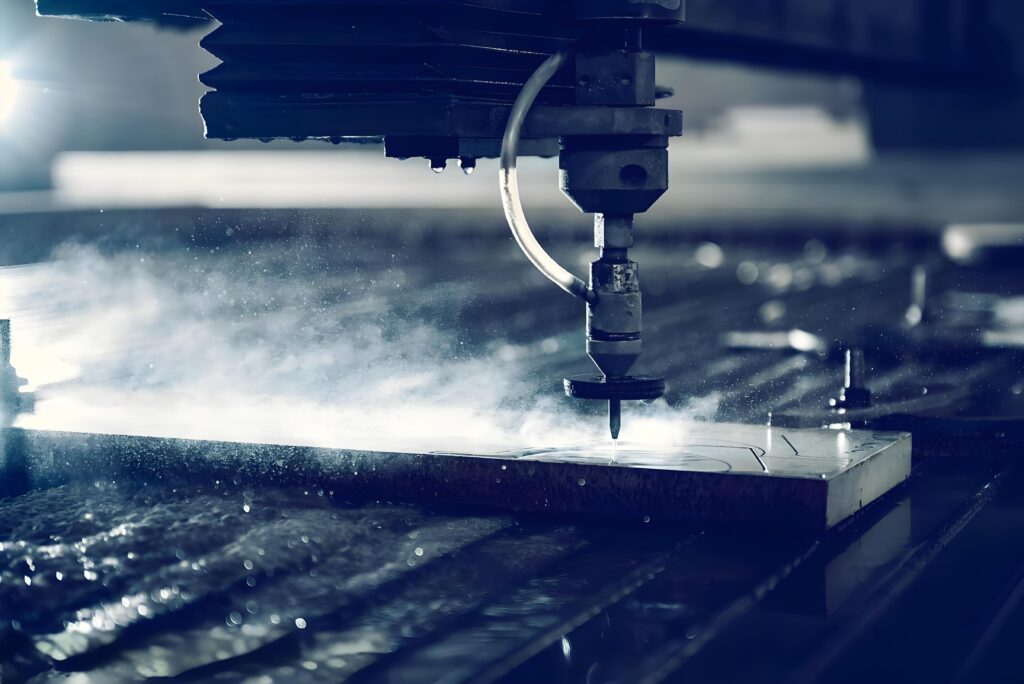
4.Mechanical Cutting
Mechanical cutting uses a machine with a powered moving cutting edge to shape the metal to the design specifications, removing material from the metal sheet through mechanical action. Common mechanical cutting machines include lathes, milling machines, drilling machines, grinders, saws and planers.
Advantages:
Mechanical cutting methods can be set up quickly and are suitable for small-scale production runs. The cutting machine has high accuracy. It can be used for a variety of metals and other materials, usually without custom tools, and is easy to produce prototypes with mechanical cutting methods.
Disadvantages:
It may be necessary to combine several different mechanical cutting processes to complete the production of parts, usually requires post-cutting processing, may require specialized labor, and has a slow processing time, which is not suitable for large-scale production runs.
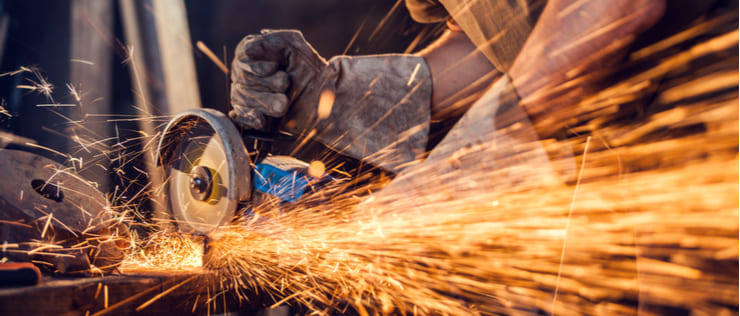
5.CNC Plate Bending Machine
CNC plate bending uses a CNC press or press brake to bend metal into a two-dimensional or three-dimensional shape. It can be used in the early stages of manufacturing or to adjust the finished product.
Advantages:
High precision, high-volume production in a short time, low cost, minimal tooling cost, and multiple custom shapes can be created through a series of bending processes.
Disadvantages:
May produce indentations or marks at the bending points of the product, not very suitable for mass production, custom molds are required for specialized bending projects, sheet metal parts need to be positioned when bending to prevent sliding, hard metals are prone to breakage when bent parallel to the rolling direction, and features such as holes and slots near the bend may be deformed.
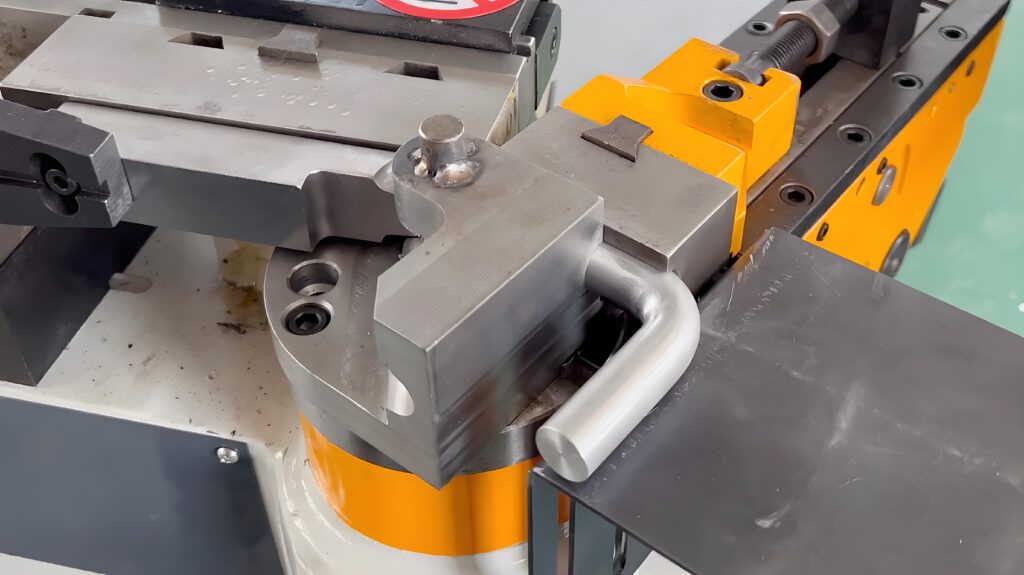
6.Shearing Sheet Metal Processing
Shearing applies force to the metal sheet through a die, punch or blade to break it apart at the desired location. It is usually used for straight cutting and can also produce angle cutting.
Advantages:
It can produce long straight lines, suitable for soft metals, cost-effective for high-volume projects, and suitable for cutting small lengths or different shapes of materials.
Disadvantages:
The cutting type and complexity are limited, mainly used for straight cutting, burrs or other defects will be generated at the cutting end, not suitable for all materials, including hard metals and large diameter parts, slower and less accurate than other cutting methods.
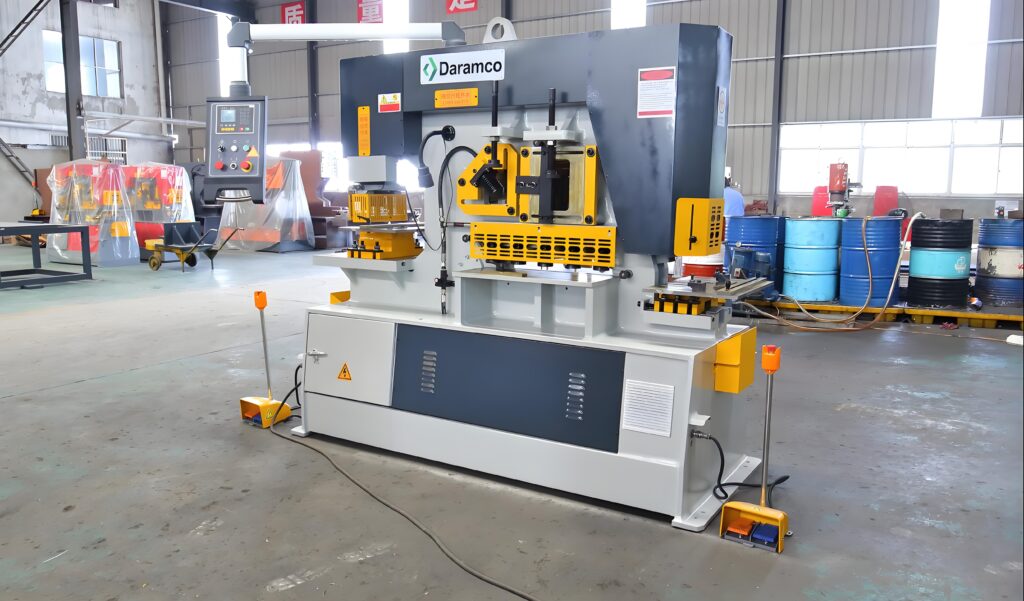
7.Roll Forming
In roll forming, a long strip of sheet metal passes through a series of paired rollers, each pair of rollers partially bends the sheet metal until it reaches the final shape, and then cuts it into finished products.
Advantages:
Fast production speed, low cost of large-scale production, less post-processing requirements, can incorporate secondary operations such as punching, better results than some sheet metal extrusions, and can produce highly complex shapes through a relatively simple production process.
Disadvantages:
The production setup process is complex and can be expensive, metal springback can cause production difficulties, some shapes cannot be formed by rolling, the end pieces of the sheet metal strip may be of poor quality, and the production facility occupies a large area and may not be suitable for narrow or short parts.
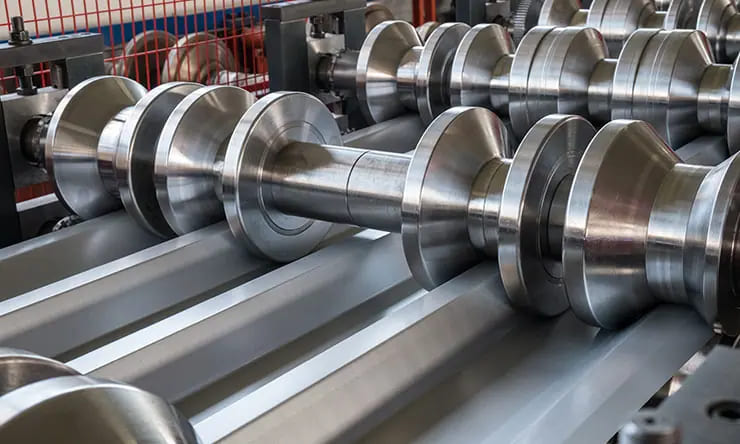
8.Precision manual stamping
Stamping uses mechanical or hydraulic stamping to form metal. Dies are used to bend, stamp, and process metal parts. Customized dies are created for individual production runs and need to be precisely manufactured.
Advantages:
Quick and cost-effective production of medium and large batches, accurate production of complex shapes, large quantities of identical parts can be produced quickly after die manufacturing, suitable for high-precision production of small parts, multi-purpose process, can perform a variety of processing such as punching, and residual materials can be recycled.
Disadvantages:
Customized die pre-production time is long, which may take more than 45 days. Die changes are expensive and affect production schedules. Stamping tools are relatively fragile and their lifespan is easily affected by repeated changes. Die errors can lead to errors in the entire production. Parts may require additional sheet metal processing. Small order production is less cost-effective.
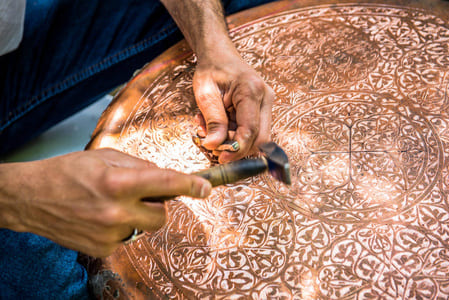
9.Precision progressive stamping
In precision progressive stamping, the metal strip passes through a series of stamping machines with sequentially arranged dies, is processed in multiple stages, and finally cut into finished products.
Advantages:
It can create more complex shapes than manual stamping or other methods, is cost-effective for large-scale production, has low cost per piece, accurately produces complex shapes, has fast production speed, is suitable for high-precision production of small parts, and can reduce scrap rate.
Disadvantages:
Die production is time-consuming and may require more than 50 days of delivery time. Molds and tools are expensive to produce and require large initial investments. Changing the mold after it is created is expensive and destructive. Stamping tools are fragile and their lifespan is easily affected. Errors in the mold will lead to errors in the entire product. Parts may require additional sheet metal processing. Stamping dies need to be regularly maintained and monitored. The material needs to be sufficiently ductile.
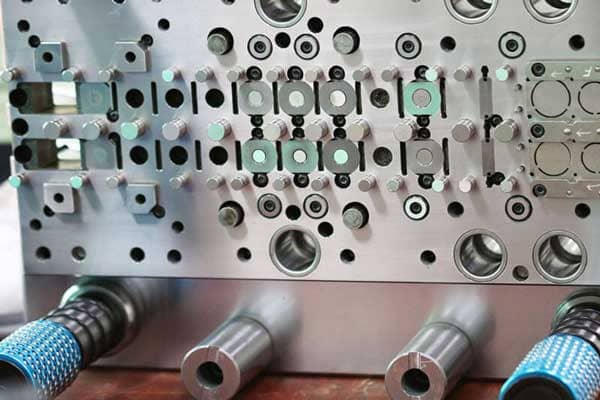
10.CNC punching
CNC punching uses a punch press to push the metal sheet into a die to create holes or cuts, and can also be used for secondary processing.
Advantages:
Strong cutting force, suitable for all kinds of metals. Fast and efficient punching, can process square and other shapes. Suitable for medium to large quantities. High precision, uniform cutting level. There are standard punches available. Complex designs can be made.
Disadvantages:
Not suitable for complex shapes. There are burrs on the edges, and secondary finishing may be required. The hole diameter should generally not be smaller than the metal sheet gauge.
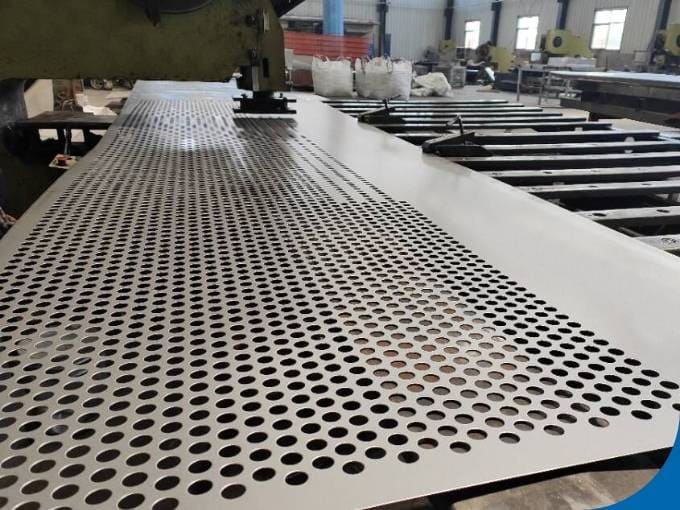
2,What factors should be considered when choosing sheet metal processing?
1.Process cost
Cost is often the key factor when choosing the right sheet metal processing process. The production method that can meet the minimum quality standard of the part at the lowest cost should be selected. However, cost selection is complicated by production volume and manufacturer capabilities. Output is an important factor. Some production methods such as stamping and progressive stamping are low-cost in large-scale production, but expensive in small batches. Manufacturers who specialize in certain production methods may reduce the corresponding costs.
2.Tolerance
When selecting a process, it is necessary to consider the level of accuracy required for the finished sheet metal part, which is critical to the performance of the finished part and subsequent assembly calibration. The tolerance range that can be achieved by different sheet metal processing processes varies.
3.Tool requirements
Different sheet metal processing processes require different tools. Some sheet metal cutting and forming processes require custom tools. For example, stamping almost always requires custom tools. Custom tools may be expensive and require lengthy identification processes to ensure accuracy. When considering process selection, the relationship between the cost of custom tools and production needs should be weighed.
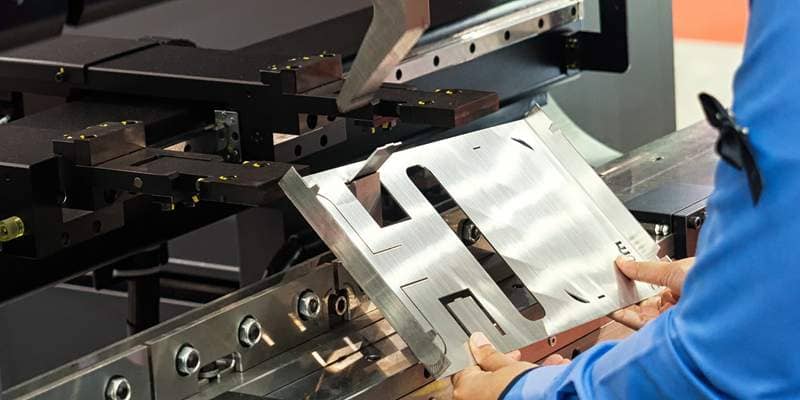
4.Thickness requirements
The thickness of the finished product of different sheet metal processing processes is different. The thickness of the processed metal plate is a problem that needs to be considered, mainly considering whether thick metal plates need to be processed. Among the common processes, only laser cutting and CNC bending can be used for metal sheet parts over 4 mm.
5.Minimum order quantity
When selecting a sheet metal processing process, the minimum order quantity needs to be discussed with the manufacturer. Some processing methods are not suitable for small batches. For example, stamping is usually not suitable for small batches because it is time-consuming and expensive to create custom tools and plan the production process. Progressive stamping is suitable for large-scale sheet metal applications.
6.Delivery time
The delivery time is related to production requirements. Processes that do not require custom tools and simple setup procedures have short delivery times, such as laser cutting, which can be directly input into the design and production, and the delivery time is very short. Processes that require planning, custom tools, professional equipment or training of staff have long delivery times. Large orders may also require longer delivery times. When selecting a sheet metal processing process, you should consider whether the delivery time can meet the requirements of the production plan.
3,Summary
Choosing the right sheet metal processing technology is of great significance to the manufacture of sheet metal products. This article details a variety of sheet metal processing technologies, such as laser cutting. When choosing a sheet metal processing technology, you should consider factors such as cost, tolerance, minimum order quantity and delivery time.
If you need an experienced CNC processing manufacturer, Xavier is your best choice. The Xavier team is well-equipped to provide high-quality CNC processing solutions to meet your personalized processing needs. For more information or to discuss your processing needs with us, please feel free to contact us.