A Comprehensive Guide to CNC Machining Zinc: Tips, Techniques, Applications
In the field of modern precision manufacturing, CNC machining zinc has become an extremely common and vital processing method. This blog will explore the skills, technology, advantages and wide range of application scenarios of CNC machining zinc from all aspects to help readers gain a deeper understanding of this critical processing technology.
1、Common processing methods of zinc alloy materials
1.Milling processing
Milling is the cutting-edge method zinc machining, especially advanced 5-axis CNC machining, which is the first choice for producing complex parts. It has the capability to accurately machine complex and diverse parts with different shapes.
2.Turning processing
Turning is often used to make cylindrical parts. Today’s modern lathes offer multi-axis capabilities that even include turning and milling operations, greatly expanding the possibilities for CNC machining zinc.
3.Drilling processing
When there is a need for drilling, various drill bits with spiral grooves can play an important role. The use of water cooling, sharp drill bits, and loose cutting parameters can effectively prevent heat accumulation and achieve efficient material removal, which is especially critical in CNC machining zinc.
4.Die casting processing
Die casting is a highly efficient method of manufacturing zinc components with complex designs and tight tolerances. It has significant advantages in production efficiency and precision by utilizing molds or dies to cast the required parts.
5.Electrical discharge machining (EDM)
Although not a traditional machining process, EDM is an invaluable method for creating prismatic parts. Because zinc has excellent electrical conductivity, it is very suitable for EDM machining, providing another processing method for CNC machining zinc.
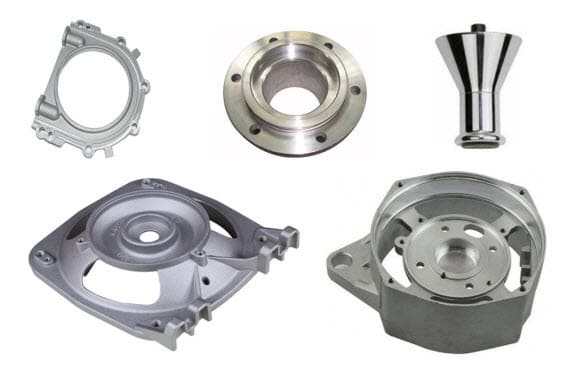
2、Choose the right zinc alloy
1.ZAMAK alloy
ZAMAK alloy is a mixture of zinc, aluminum, magnesium and copper. It has excellent strength, hardness and wear resistance, making it a popular choice for CNC machining zinc and is widely used in a variety of different application scenarios.
2.ZA alloy
When there are high requirements for strength and elasticity, ZA (zinc-aluminum) alloy is more powerful due to its higher aluminum content. It is more durable and more resistant to deformation, making it very suitable for heavy-duty tasks and the manufacture of high-temperature components.
3.Zinc-copper-titanium alloy
If you focus on strength, elasticity and corrosion resistance, zinc-copper-titanium alloy is undoubtedly the first choice. It has excellent dimensional stability and wear resistance, and is particularly suitable for applications that have strict requirements for performance stability, providing a high-quality material choice for CNC machining zinc.
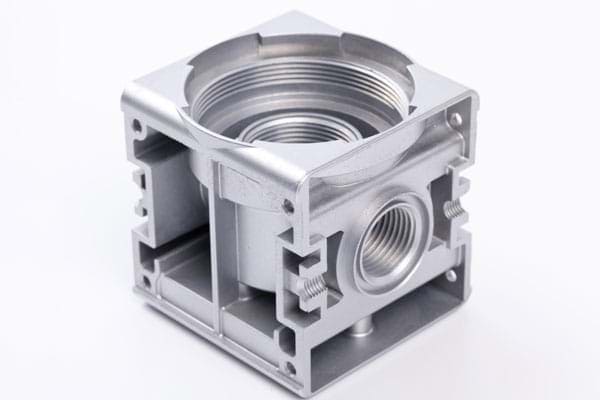
3、Surface treatment method for zinc alloy material processing
1.Electroplating
Electroplating with materials such as nickel and cobalt can produce a beautiful, corrosion-resistant and unique surface, greatly improving the quality and value of CNC processed zinc products.
2.Chromate conversion coating
This treatment can enhance corrosion protection and is available in a variety of colors, which is both beautiful and practical.
3.Powder coating
Powder coating provides a strong and textured appearance that can withstand harsh wear and tear, providing good protection for the product.
4.Anodizing
Forming a thin and strong oxide on the surface of the zinc alloy further enhances corrosion resistance and extends the service life of CNC processed zinc products.
5.Painting
Specific colors can be selected for painting according to specific needs to meet different design requirements and aesthetic needs.
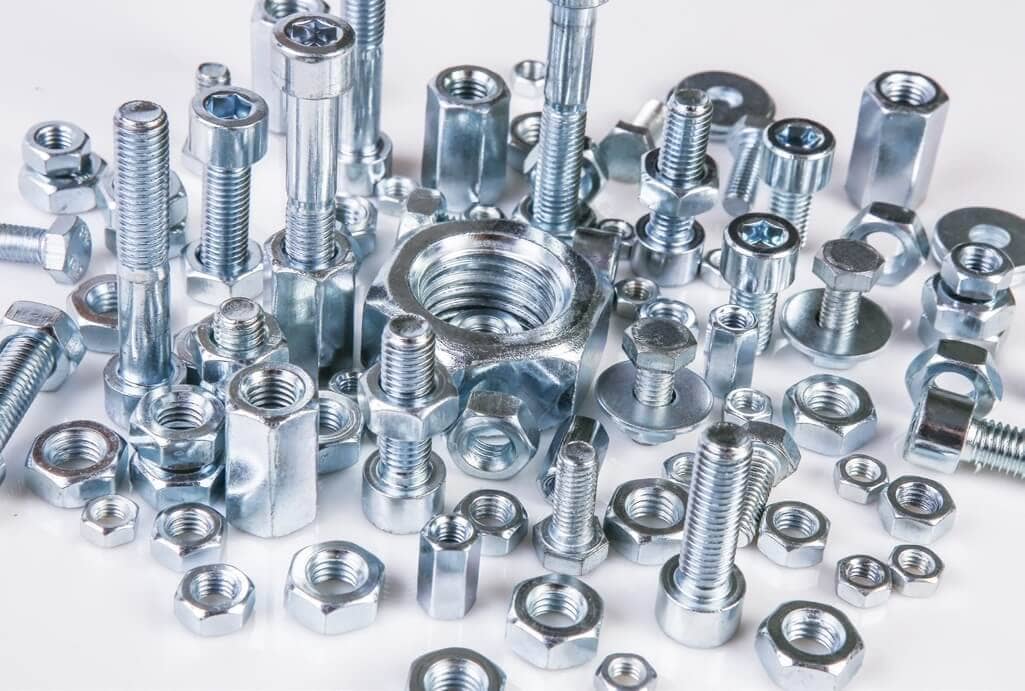
4、Zinc alloy material processing design skills
1.Adding draft angles
Adding draft angles to the design ensures that the parts eject smoothly from the mold, thereby reducing the risk of warping and improving the production efficiency and product quality of CNC zinc processing.
2.Uniform wall thickness
Adhering to the design plan of uniform wall thickness can avoid warping or cracking of parts due to uneven cooling, ensuring the stability and reliability of the product.
3.Fillet processing
Rounding the edges of the parts can avoid stress points caused by sharp corners, effectively prevent cracks or failures, and improve the strength and durability of the product.
4.Feature positioning
Features such as ribs, bosses and through holes need to be reasonably positioned to align them with the expected loads and stresses, thereby ensuring that the parts are strong and durable and meet different usage requirements.
5.Pay attention to undercuts
Minimize undercuts in part design to avoid damaging CNC zinc processing plans, reduce additional tools or steps, and reduce production costs and processing difficulties.
5、Other tips to ensure effective zinc processing
1.Alloy selection
Choosing alloys that are easy for machinists to handle, such as Zamak 3 or Zamak 5, can improve dimensional accuracy and save processing time, improve production efficiency and product quality.
2.Keep the tool sharp
Ensuring that the cutting tool is sharp can reduce tool wear, produce short chips that are easy to fall off, and improve the accuracy and efficiency of processing.
3.Reasonable use of coolant
Using a large amount of coolant, such as the commonly used water-based coolant, can reduce friction and control temperature, improve surface finish and chip generation, improve product quality and processing stability.
4.Cutting speed adjustment
When the zinc alloy heats up, slightly increasing the cutting speed can reduce the cutting temperature, promote better heat dissipation of the chips, and improve the efficiency and quality of the processing.
5.Correct tool selection
Carbide tools are well suited to machining zinc alloys due to their excellent wear resistance and thermal stability, while high-speed steel (HSS) is suitable for lighter tasks and works well with different grades of zinc alloys, providing a suitable tooling option for CNC machining zinc.
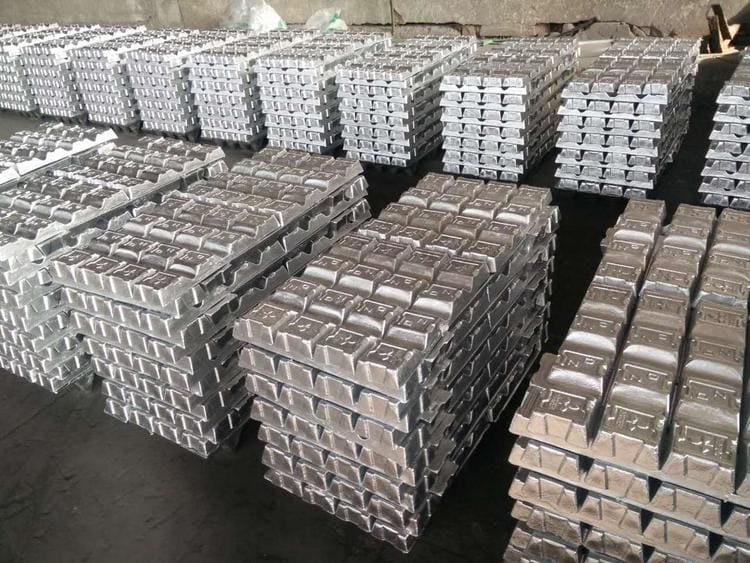
6、Advantages of CNC Machining Zinc
1.High accuracy
CNC machined zinc delivers impeccable dimensional accuracy, an advantage that is particularly valuable in precision-critical industries such as aerospace, automotive and medical devices.
2.Ability to handle complex processes
CNC machined zinc is good at handling complex shapes and designs, and has significant advantages in making customized parts to meet the individual needs of different customers.
3.High efficiency
The low melting point of zinc and the high efficiency of CNC machining can reduce tool wear, energy consumption and waste, making it highly cost-effective.
4.Green and environmentally friendly
Zinc is recyclable, and CNC machining zinc is environmentally friendly, produces little waste, and is a sustainable processing option.
7、Uses of CNC machined zinc parts
1.Automotive Industry
Zinc parts are widely used in engine blocks, gearbox housings, and high-performance components due to their strong, durable, and corrosion-resistant properties.
2.Aerospace Industry
High precision and reliability make it an ideal choice for brackets, housings, and connectors. Its strength-to-weight ratio and corrosion resistance ensure performance under extreme conditions.
3.Medical Equipment
With its high precision and reliability, it is an ideal choice for brackets, housings, and connectors. Its strength-to-weight ratio and corrosion resistance ensure excellent performance under extreme conditions.
4.Electronics and Telecommunications
Due to its excellent conductivity and shielding properties, it is widely used in electronics and telecommunications such as electrical connectors, radiators, and protective shielding.
5.Architectural Applications
The strong corrosion resistance and durability make it used in structural elements and decorative parts in the architectural field, adding beauty and practicality to the building.
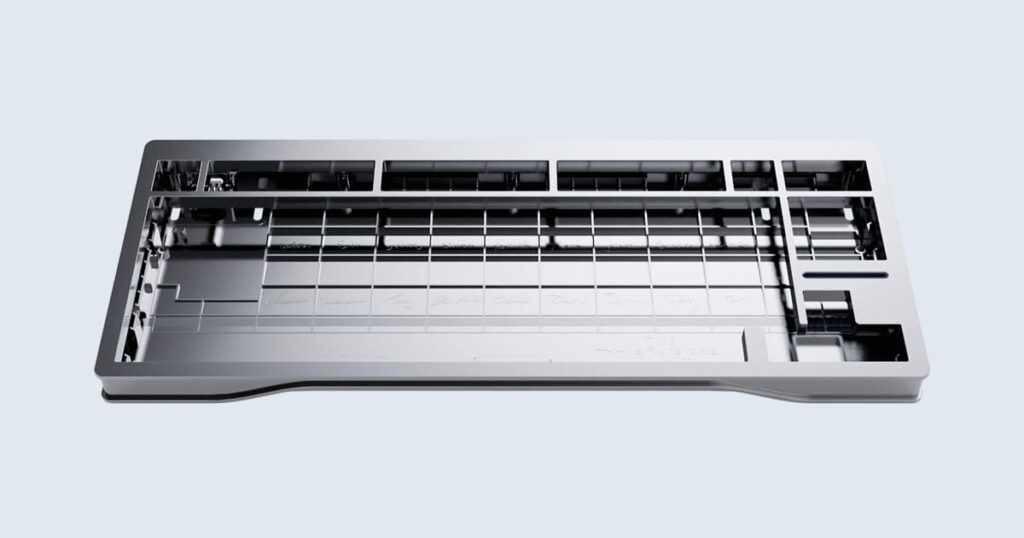
8、Conclusion
In summary, CNC machining zinc offers many significant advantages, and its versatility has found applications in a wide range of industries. CNC machined zinc is a smart choice for projects that require parts that are strong, corrosion-resistant, and have precise tolerances.
If you are looking for an experienced CNC machining manufacturer, Xavier is your ideal choice. The Xavier team is well-equipped to provide high-quality CNC machining solutions. If you need more information or to discuss your machining needs with us, please feel free to contact us.