CNC gears: types, processing and trends
CNC gears are important basic parts in industrial production. Their processing quality and processing capacity can reflect the industrial level at that time. The current development trend of gear processing is to realize the CNC and automation of gear processing, and the integration of processing and testing. This article will start with the CNC gear processing methods and gear types to help everyone understand the importance of CNC gear development to industrial production.
1.What is a gear?
A gear is a rotating mechanical device with teeth that can transmit torque and speed. Usually, mechanical gears are cylindrical and have several sets of teeth around the main body. When two or more gears work synchronously, they are in a transmission state. Power transmission is the cause of speed or torque changes.
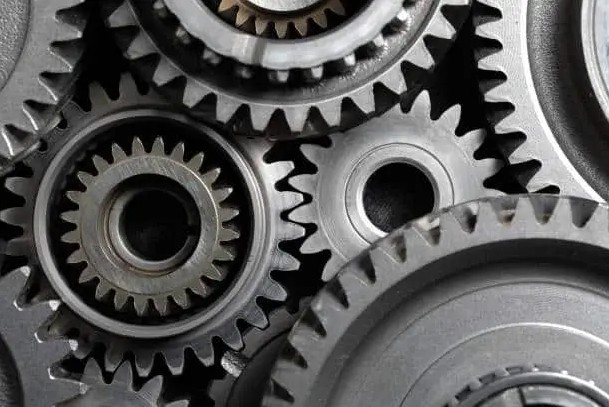
2.Methods of CNC gears processing
With the increase in the number and variety of gears, the requirements for gear precision are constantly improving, and new gear processing methods are constantly emerging. At present, CNC gears processing includes casting, cold rolling, hot rolling, stamping, die forging, powder metallurgy and cutting, etc. The most commonly used method is cutting. The main methods of CNC gears cutting include: gear hobbing, gear shaping, gear shaving, gear honing, gear grinding, gear grinding, gear milling, etc.
(1) Gear hobbing
Gear hobbing is currently the most widely used gear cutting method. Gear hobbing with a hob on a gear hobbing machine is equivalent to the meshing of a pair of helical gears. The hob and the workpiece maintain a strict speed ratio relationship, meshing in space, and completing various tooth shapes such as involute, cycloid, circular arc, rectangle, etc. according to the development motion. The gear hobbing accuracy is generally 7 to 9 levels. When high-precision hobs and high-precision gear hobbing machines are used, gears with a grade 5 accuracy can be hobbed.
The current advanced gear hobbing technologies include:
① Multi-head hobbing can greatly improve production efficiency.
② Hard tooth surface hobbing technology.
③ CNC gears hobbing can greatly improve CNC gears processing accuracy and efficiency and expand the processing range of machine tools.
④ Dry cutting process. It has high productivity, high precision and high workpiece quality.
(2) Gear shaping
Gear shaping is a widely used CNC gears cutting method, especially suitable for machining internal gears and multi-gears. The machining accuracy can be as high as 5-6 levels, generally 7-9 levels.
CNC trend of gear shaping technology:
① CNC gears shaping machine to facilitate machining of non-circular gears and CNC gears of special shapes.
② Increase the number of strokes of the gear shaping machine to improve gear shaping efficiency.
③ Research on the shaping process of hardened gears.
④ CNC helical gear shaping to improve the machining accuracy of helical gears.
(3) Gear shaving
The principle of gear shaving is that the staggered helical gear pair meshes without side clearance, and the gear shaving cutter drives the workpiece to rotate, generating relative sliding speed on the meshing surface, and removing material from the workpiece surface. Gear shaving is an efficient CNC gears finishing method.
(4) Gear honing
Gear honing is equivalent to the meshing transmission of a pair of staggered helical gears. Gear honing machine is a gear finishing machine tool, which is mainly used to improve the tooth surface quality of gears after heat treatment.
During processing, a plastic honing wheel (gear or worm shape) containing abrasive is used to mesh with the workpiece without gap and rotate freely, and the relative sliding speed between the tooth surfaces and the feed pressure are used for cutting.
(5) Gear grinding
Gear grinding is the most effective and reliable method to obtain high-precision CNC gears. Since hardened gears are now mostly used, gear grinding has become the main processing method for high-precision gears. There are many types of gear grinding methods, which can be divided into two categories: development grinding and form grinding.
3.Different types of CNC gears and their applications
In mechanics, gears are divided into different categories according to their configuration, purpose and direction of movement. The following are the most important types of gears.
(1) Spur gears
When two shafts (driving shaft and driven shaft) are parallel, spur gears transmit power in the same plane. The teeth of spur gears are parallel to the axis of the shaft. They are the most common form of gears and can be used in automobiles, conveying systems, gear pumps and motors, reducers, etc.
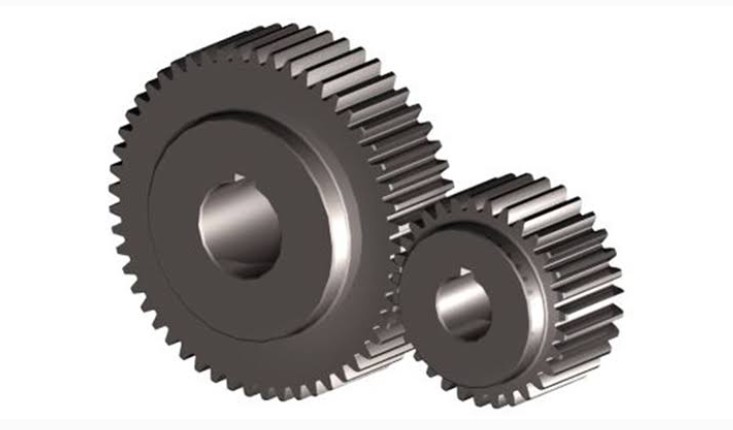
(2) Helical gears
Compared to parallel spur gears, helical gears have teeth at an angle to the shaft. They have multiple teeth in contact during transmission and can carry larger loads. Due to better load distribution and less friction, they operate with less noise and vibration and less wear and tear. The different types of helical gears are listed below.
① Single or double helical gears
Single helical gears have teeth in either a left-hand or right-hand spiral. However, double helical gears have teeth in both directions. Using double helical gears ensures more significant tooth overlap, resulting in a smoother transmission.
② Herringbone gears
Herringbone gears have two helical gears connected side by side. Due to the high production cost and manufacturing difficulty of this type of CNC gears, they are not common, although they are more suitable for vibration and high shock applications.
③ Helical gears
Helical gears are a pair of helical gears running at a 45-degree twist angle. They appear on non-parallel and non-intersecting shafts and have a lower load-bearing capacity due to single tooth contact. Therefore, these gears are not suitable for transmitting high power.
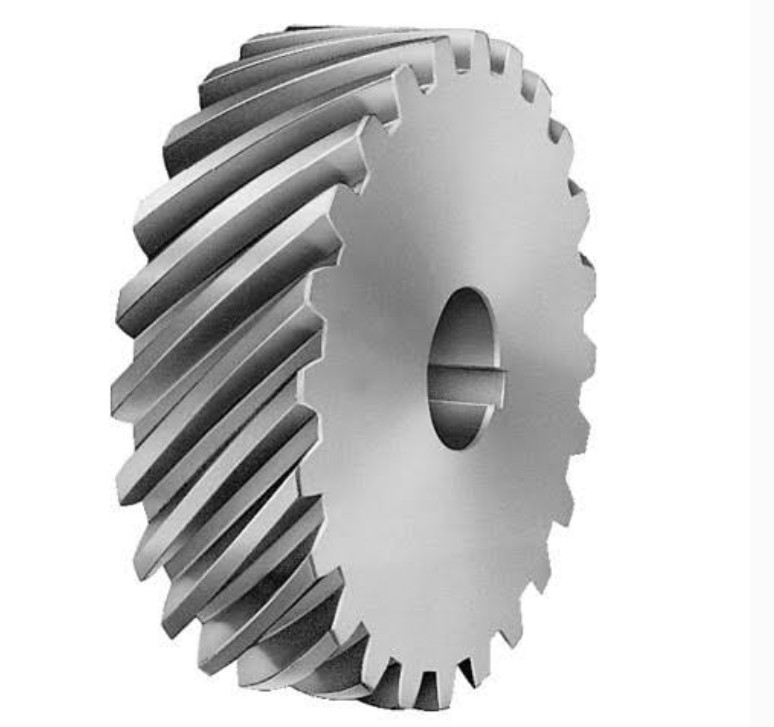
Applications of helical gears
Water pumps
Mixers
Automobiles
(3) Bevel Gears
Bevel gears are cone-shaped with teeth around the cone. They transmit forces between perpendicular axes. That is, axes that intersect at right angles (90 degrees). However, bevel gears are expensive and cannot transmit large torques by size as parallel axis configurations.
① Straight Bevel Gears
Straight bevel gears are the most common configuration of bevel gear teeth. The reason for this is the simplicity of design and ease of manufacturing. When properly matched, the straight helical teeth mesh together instantly rather than gradually.
② Spiral Bevel Gears
Spiral bevel gears are mechanical gears with curved tooth lines that have a better tooth surface contact ratio than straight bevel gears. Therefore, this CNC gears has superior efficiency and strength and produces less vibration and noise. However, they have manufacturing difficulties.
③ Zerol® Bevel Gears
This gear incorporates the characteristics of straight and spiral bevel gears. Therefore, this gear is suitable for both applications. However, their torsion angle is zero, so the teeth can rotate in either direction.
④ Miter gears
Miter gears are a special type of bevel gear. They are unique because they have a gear ratio of 1. In contrast, other bevel gears have gear ratios ranging from 10:1 to 500:1.
⑤ Crown gears
Crown gears, sometimes called face gears, also have teeth at right angles to the wheel face. In industry, crown gears mesh with other bevel gears or spur gears in a power circular motion.
⑥ Hypoid gears
Hypoid gears look similar to spiral bevel gears, but they operate in non-crossing axes. They operate at 90 degrees and are common in the automotive industry.
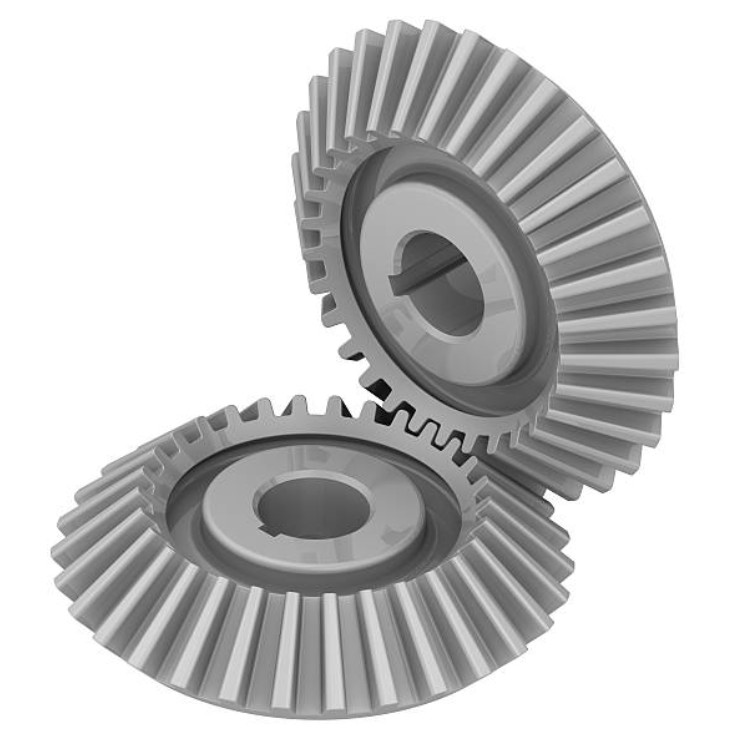
Applications of bevel gears
Mixers
Watering systems
Pressing plants
(4) Worm gears
Worm gears consist of a spiral cut on the shaft (worm) and the mating gear (worm wheel). These types of gears work by sliding contact with less friction, rather than rotating smoothly and quietly. Therefore, they are suitable for high-impact applications. However, their lower efficiency limits their use to low-power applications.
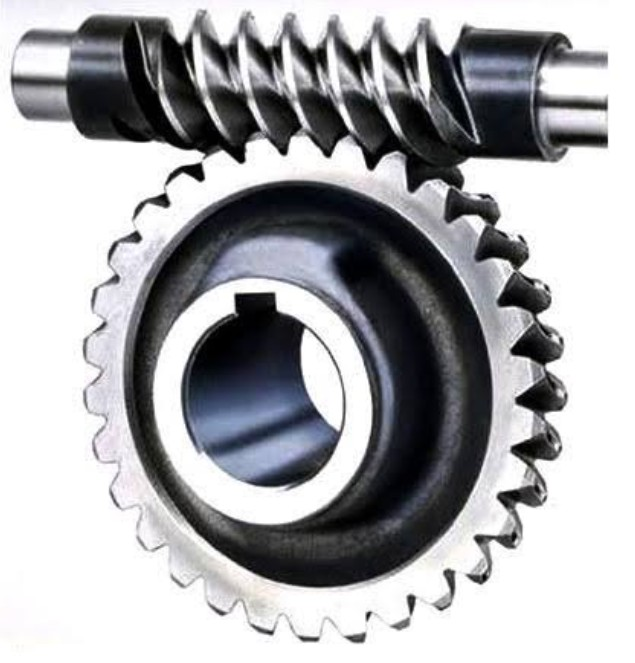
Application of worm gear
Agricultural machinery
Small conveyor
Packaging equipment
Gear Type | Features | Material Application |
Spur gears | a. Most common gear form. b. Easily manufactured. c. Used in parallel axis gear configurations. d. Round gear body. | a. Clock b. Small conveyor c. Car |
Helical gear | a. Round gear body. b. Less efficient than spur gears. c. Parallel shaft configuration. Smoother operation and less noise. | a. Water pump b. Mixer c. Car |
Bevel gear | a. Bevel gear body. b. Intersecting shaft configuration. c. Available in linear, helical and Zerol® bevel designs. | a. Mixer b. Watering system c. Crusher |
Worm gear | a. The gear pair consists of circular gears and helical gears. b. Inefficiency. c. Non-parallel and non-intersecting configuration. | a. Agricultural machinery b. Small conveyor |
Rack and Pinion | a. Gear pair consisting of rack and cylindrical gear. b. Parallel axis configuration. c. Converts rotary motion into linear motion and vice versa. | a. Car steering b. Weighing scale |
4.Advantages and disadvantages of CNC gears
Advantages of CNC gears
- Gears are mechanically strong and can lift higher loads.
- With the help of gearboxes, they allow speed ratios to be changed.
- They work well at low speeds.
- Efficient power transmission.
- They are ideal for transmission of high torque values.
- Little attention is paid to maintenance, CNC gears only require daily lubrication.
- Durable, the gear system has a long service life
Disadvantages of gears
- Gears are not suitable for long-distance motion transmission.
- They are not flexible.
- Gears are noisy, especially at high speeds.
- They are not suitable when the shaft is far away.
5.Development trend of CNC gears processing technology
The development of CNC gears processing technology is in the continuous pursuit of improving processing accuracy and processing efficiency, which is specifically manifested in the following aspects:
(1) CNC.
CNC gears can improve processing accuracy and processing efficiency.
(2) Intelligence.
According to the stress, strain and temperature rise of the machine tool, the cutting process parameters of the machine tool are dynamically adjusted.
(3) High speed.
The maximum speed of gear shaping can reach 1000-2500 times/min stroke number, and the cutting speed of high-speed steel hobs can reach 100-200 m/s.
(4) Integration.
Gear machine tools (especially large gear machine tools) tend to integrate multiple processes.
(5) Environmental protection.
For example, the adoption of dry cutting processing technology avoids oil pollution of air and environment due to the absence of cutting fluid.
(6) New processes continue to emerge
Abrasive flow finishing process and grinding-honing combined process are emerging processes for gear finishing.
6.Summary
Gears are difficult to manufacture due to their complex shapes and many technical problems. In the face of various problems, the gear manufacturing process can still develop, which is largely due to the development of CNC gears technology that has improved its accuracy level and production efficiency. Therefore, it is particularly important to flexibly use gear CNC technology.
If you are looking for an experienced CNC machining manufacturer, Xavier is your ideal choice. The Xavier team is well-equipped to provide high-quality CNC machining solutions. If you need more information or to discuss your machining needs with us, please feel free to contact us.