Best Guide to Aluminum Anodizing: Industries, Benefits, Applications
In the field of modern product manufacturing, aluminum anodization, as a key surface treatment process, plays a vital role in improving the durability and aesthetics of the material. Aluminum, one of the most commonly used materials for anodizing, offers many significant advantages. Next, this article will delve into the knowledge related to aluminum anodization.
1、What is anodizing?
Anodizing is a surface treatment process that changes the surface chemistry of metals and other substrates to provide corrosion protection, enhanced aesthetics and good scratch resistance.
2、Anodizing process
Step 1: Surface Preparation
Before aluminum anodizing, the aluminum parts must be thoroughly cleaned and treated to remove impurities that may interfere with the oxidation process and ensure a clean surface after oxidation.
Step 2: Anodizing Tank and Current
After the surface is prepared, the aluminum parts are immersed in an electrolyte, usually sulfuric acid. The parts are connected to the anode and a negative potential is applied to the plates in the electrolyte. This generates an electric current, causing positive ions to be attracted to the top of the electrolyte and negative ions to gather on the aluminum anode.
Step 3: Formation of the Oxide Layer
When the current flows through the aluminum parts, an oxide layer begins to form on the surface of the parts due to the excess positive ions. These oxide layers form a geometrically regular structure. The aluminum and negatively charged oxygen ions combine to form a barrier layer that prevents further chemical reactions.
Step 4: Hard Anodizing (Optional)
For applications that require greater durability, the anodizing process can be continued to form a thicker anodized layer. This step involves extending the energization time until the oxide layer exceeds 10 microns, which results in a hard anodized layer with excellent corrosion and wear resistance.
Step 5: Sealing and Finishing
Once the desired anodized layer thickness is achieved, the parts are sealed by flushing with water. This step stabilizes the anodized layer and further enhances corrosion resistance. Depending on the application, finishing methods such as polishing or sandblasting can also be used to achieve the desired surface finish.
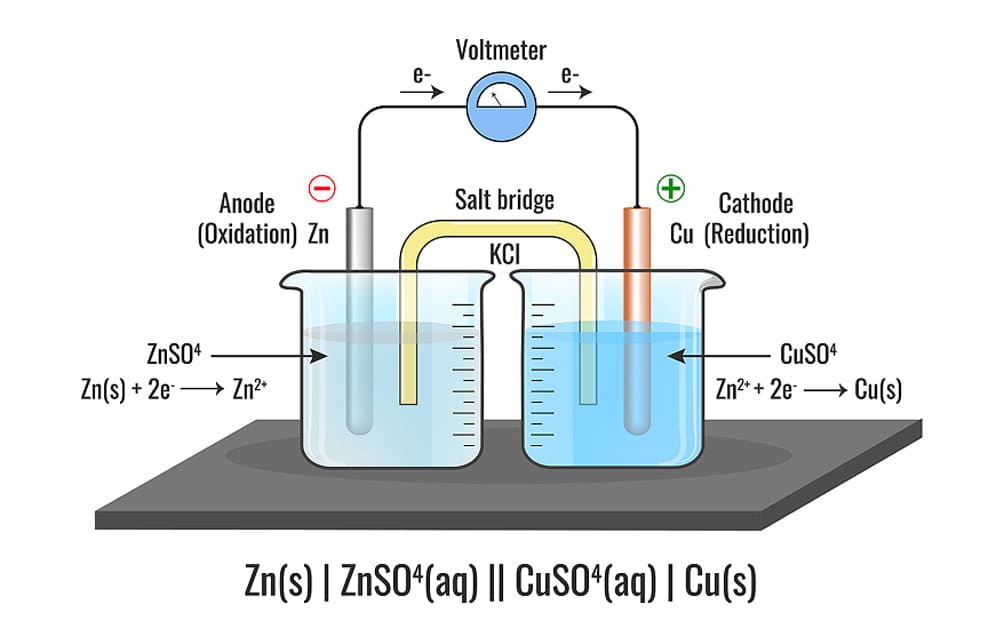
3、Types of Anodizing Processes
Type I: Chromic acid anodizing
Type I anodization, also called chromic acid anodization, creates a thin coating on the surface of aluminum parts. Although this coating improves corrosion resistance, it is primarily used in applications where a thick anodized layer is less necessary. It is commonly used in industries such as aerospace, which require non-reflective surfaces and precision machine components.
Type II: sulfuric acid anodizing
Type II anodization, also known as sulfuric acid anodization, produces a slightly thicker coating than Type I. This type of anodizing is widely used in many fields. Its anti-corrosion and wear resistance are quite good, and it can also present a range of bright colors. It is often found in industries such as consumer goods, construction and kitchen appliances.
Type III: Hard anodized
Type III anodized layer is also a hard anodized layer. Among the transparent anodized layers, its anti-corrosion and wear resistance are the most significant. This process requires continuous energization until the depth of the oxide layer exceeds 10 microns, allowing a thicker anodized layer to be formed. It is ideally suited for applications where extreme durability is required, such as explosion shields, mechanical transmissions and valves.
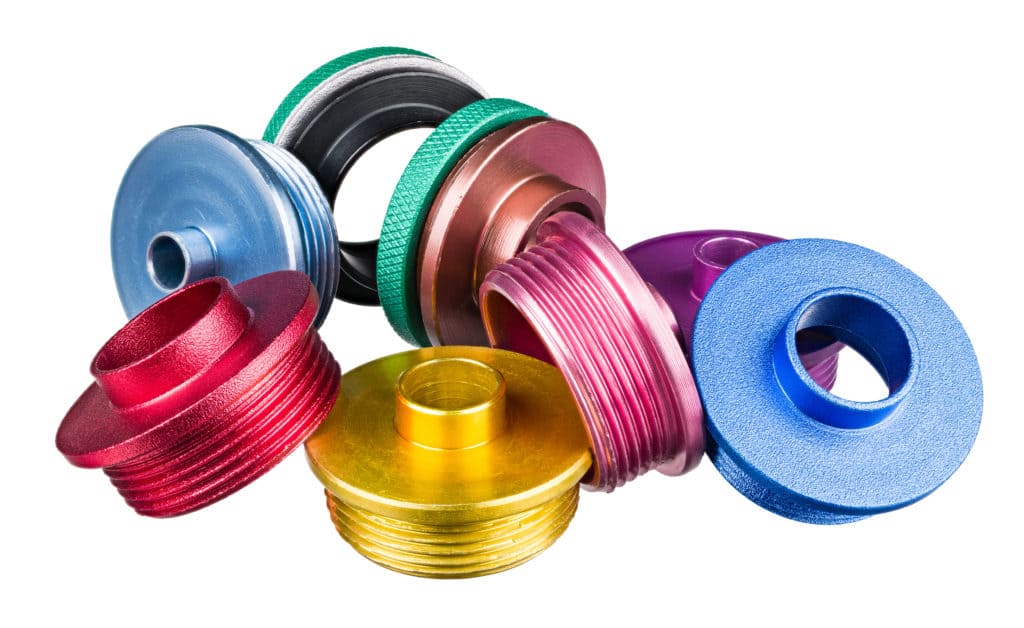
4、Advantages of Aluminum Anodizing
In the modern industrial field, aluminum anodizing has shown many outstanding advantages.
1.Improved adhesion
Aluminum anodizing can enhance the adhesion of paint primers and glues, providing better bonding for subsequent coatings or adhesives.
2.Anti-corrosion
Aluminum anodizing gives aluminum parts an additional layer of anti-corrosion protection, allowing them to easily withstand a variety of harsh environmental conditions such as acid rain and salt water. Moreover, the surface after anodizing will form a passivation state, which can effectively prevent further chemical reactions and extend the service life of aluminum parts.
3.Enhanced durability
Aluminum anodizing greatly improves the material properties of aluminum parts. The coating it produces is extremely strong and scratch-resistant, with a hardness of up to 9 (out of 10) on the Mohs hardness scale, close to the hardness level of diamond. This excellent durability makes anodized aluminum ideal for a variety of wear-resistant applications.
4.Aesthetics
One of the attractive points of aluminum anodizing is its colorability. The surface produced during the anodizing process can introduce hues or pigments to form a variety of bright colors. And unlike surface coatings, the color is hidden deep inside the material and has strong resistance to scratches and fading.
5.Scratch resistance
The hard anodized layer formed by aluminum anodizing has excellent scratch resistance and is very suitable for applications with high durability requirements.
6.Thermal and electrical insulation
The anodized layer has thermal and electrical insulation properties, so anodized aluminum is suitable for electrical applications.
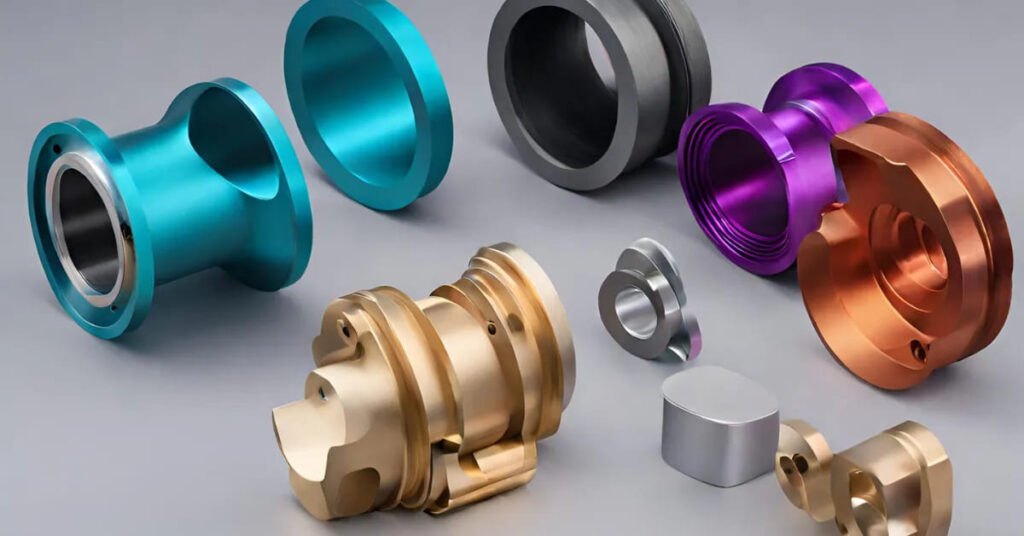
5、Application of Aluminum Anodizing
The unique durability and aesthetics of anodized aluminum are used in various industries.
1.Photography
Camera bodies and accessories are usually made of anodized aluminum, which is both durable and beautiful.
2.Aerospace
In the aerospace industry, anodized aluminum is widely used for parts that need to be resistant to corrosion and wear, such as aircraft parts and precision machine parts.
3.Automotive industry
In the automotive industry, anodized aluminum is used for parts that need to withstand complex environmental conditions, such as engine parts and decorative edges.
4.Construction
Due to its durability, corrosion resistance and aesthetics, anodized aluminum is often used in the construction field, such as window frames, exterior walls and other structural elements.
5.Consumer
In the consumer field, anodized aluminum is widely used, such as kitchenware, electronic products, furniture and sporting goods, which can provide a durable and beautiful surface and improve the overall quality of the product.
6.Electronic products
Because of its electrical insulation properties and corrosion resistance, anodized aluminum is used in electronic housings and components.
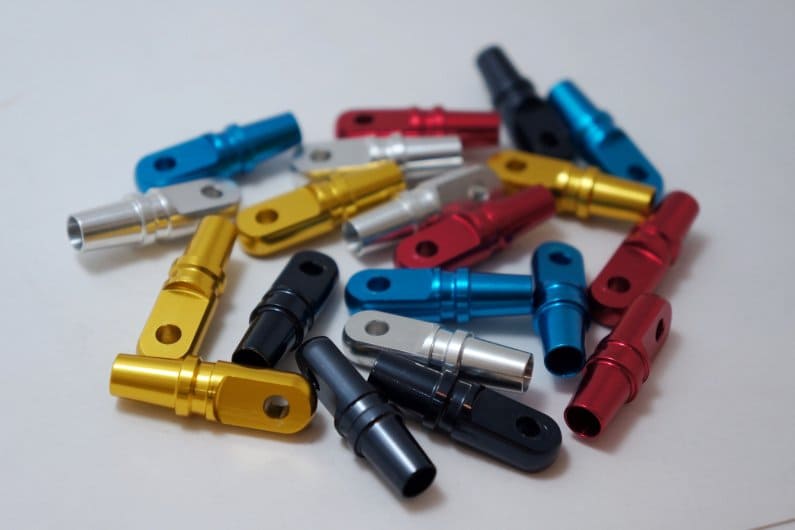
6、Factors to consider when purchasing anodized aluminum workpieces
1.Tolerances
Anodizing adds a layer to the aluminum component part, which will affect the size of the part. Therefore, it is necessary to consider the possible increase in size during the design phase.
2.Sharp corners
To avoid overheating during the anodizing process, the corner radius of the part should be designed to be at least 0.5 mm, and burr-free design is a better choice.
3.Surface treatment
If you want a completely uniform surface treatment, you may need some additional mechanical finishing processes such as polishing or shot peening before anodizing.
4.Batch processing
When coloring aluminum parts, it is easier to achieve higher color consistency if the anodizing is carried out in small batches. At the same time, anodizing small batches of small parts is an ideal way to achieve uniform color.
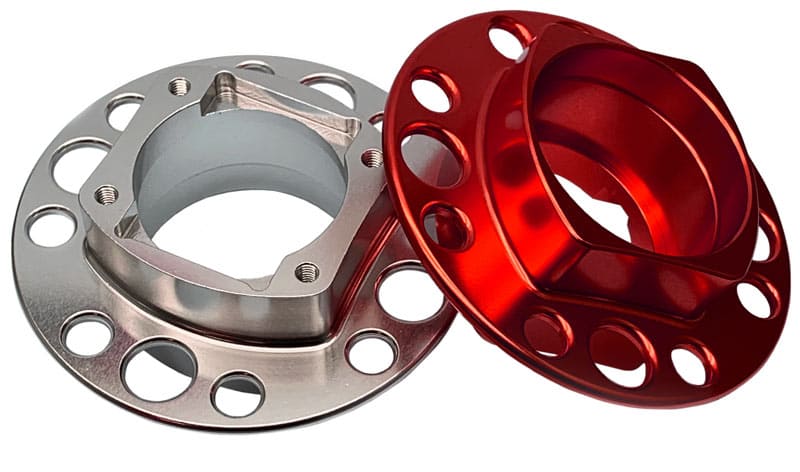
7、Conclusion
In summary, aluminum anodizing, as an important surface treatment process, can effectively enhance the durability, corrosion resistance and aesthetics of aluminum parts.
If you are looking for an experienced surface treatment manufacturer, Xavier is your ideal choice. Our professional team is well-equipped to provide high-quality CNC machining solutions. We understand the importance of meeting your individual needs and are committed to exploring cost-effective solutions that optimize system performance. If you need more information or to discuss your processing needs with us, please feel free to contact us.