Lathe Cutting Tools: A Guide to the Best
Lathe cutting tools are critical in CNC machining, and they have a significant impact on the quality and efficiency of shaping, cutting, and finishing precision parts. This article will comprehensively explore the types, applications, geometries, and considerations of lathe cutting tools to help manufacturers, machinists, and engineers make informed decisions to ensure optimal performance in operations such as custom CNC machining.
1、What is a lathe?
A lathe is a versatile machine tool used in the manufacturing industry that performs operations such as cutting, grinding, knurling, drilling and turning by rotating a workpiece around a fixed cutting tool. It is essential for producing high-precision and high-accuracy CNC machined parts, and can process a variety of materials such as metals, plastics and composites. It is widely used in industries such as automotive, aerospace, electronics and medical device manufacturing.
2、Types of CNC lathes
1.Flatbed CNC Lathe
The flatbed design has high flexibility and is suitable for processing larger workpieces. It is often used in general processing and can handle a variety of materials and operations. In the application of lathe cutting tools, flatbed CNC lathes need to choose the right tools according to different processing needs.
2.Slant Bed CNC Lathe
The slant bed design can improve chip discharge and provide a better ergonomic experience. It is an ideal choice for high-speed, high-precision processing and is popular in industries that require precision parts. The requirements for lathe cutting tools are also more stringent, requiring higher precision and stability.
3.Swiss CNC Lathe
Designed for small precision parts, it can produce complex parts with strict tolerances. Suitable for industries such as medical device manufacturing and electronics.
4.Vertical CNC Lathe
Designed with a vertical twist direction, it is used for large and heavy workpieces that are difficult to install on horizontal lathes. Commonly used in industries such as aerospace and automotive manufacturing. When processing large workpieces, lathe cutting tools need to have greater cutting force and stability.
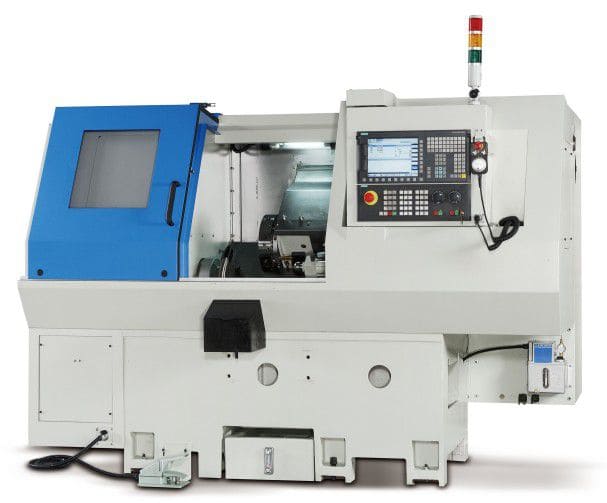
3、Main parts of lathe
1.Bed
It is the foundation of the lathe, providing support for other parts and ensuring the stability of the machining operation.
2.Spindle box
It is used to rotate the workpiece and contains a motor to control the rotation speed.
3.Tailstock
It is located on the side of the spindle box, provides support for the workpiece during machining, and can carry a variety of tools.
4.Tool holder
It moves along the bed and carries the tool, responsible for the longitudinal movement of the tool to achieve cutting along the length of the workpiece.
5.Horizontal slide
It is located on the top of the tool holder, allowing the tool to move horizontally and accurately control the cutting depth.
6.Tool holder
It is used to fix the tool and facilitate the rapid replacement of the tool during machining.
7.Chuck
It is installed on the spindle to firmly fix the workpiece during rotation.
8.Lead screw
It drives the slide and the horizontal slide to enable the cutting tool to move in a controlled manner to achieve precise operations such as thread machining.
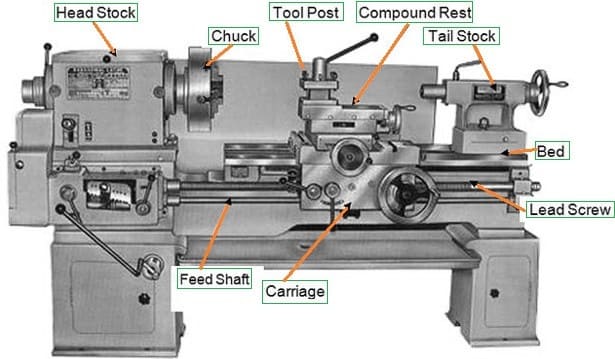
4、Lathe tool types
Category 1: Classification by material
High-speed steel (HSS): widely used in general machining, with good toughness, wear resistance and heat resistance, can cut a variety of materials, and is affordable.
Carbide: Known for maintaining a sharp cutting edge at high temperatures, it is suitable for high-speed machining and high-precision applications. It is more expensive than high-speed steel, but has a long tool life and excellent performance.
Diamond tools: are the hardest cutting tools, used for ultra-precision machining of non-ferrous metals and finishing operations that require excellent surface finish, but are not suitable for machining ferrous metals.
Cubic boron nitride (CBN): used for machining fastened ferrous metal materials such as nitrided steel and cast iron, with good wear resistance, suitable for high-speed and high-precision machining.
Ceramic products: used for machining hard materials, with excellent heat resistance, faster cutting speeds than carbide tools, but brittle and prone to breaking under heavy loads or intermittent cutting.
Category 2: Classification by operation
Rough turning tools: designed for rapid removal of large amounts of material, with strong cutting edges that can withstand heavy cutting loads.
Finishing tools: used for final machining to achieve the required surface finish and dimensional accuracy, with sharper cutting edges and lower cutting speeds and feeds.
Chamfering tools: used to form bevels or chamfers on workpieces, which can remove sharp edges or prepare for assembly.
Thread cutting tools: used to process threads on the internal and external surfaces of workpieces. The type of tool depends on the type of thread to be cut.
End machining tools: used to machine the end faces of workpieces to make them flat and smooth, usually as a preliminary operation before other machining operations.
Forming tools: used to form specific shapes on workpieces, used in applications requiring precise geometric shapes.
Grooving tools: used to cut narrow channels on the surface of workpieces for specific applications.
Boring tools: used to enlarge existing holes on workpieces, used in applications requiring high precision and tight tolerances.
Knurling tools: used to form texture patterns on the surface of workpieces to improve grip or increase aesthetics.
Taper turning tools: used to process tapered surfaces on workpieces, used in applications such as specific mating components.

Category 3: Classification by structure
Single tool: only one cutting tool is installed at a time, which is widely used, but tool replacement is time-consuming.
Welded lathe tools: Cutting edges are welded to the steel shank, which is cost-effective and customizable, but not as durable as solid tools and need to be sharpened or replaced frequently.
Clamped lathe tools: Use interchangeable blades, clamped to the tool holder, provide flexibility and cost savings, and are widely used in CNC machining.
Category 4: Classification by feed direction
Right-hand lathe tools: Designed to cut while moving from right to left on the workpiece, they are a common type and suitable for a variety of operations.
Left-hand lathe cutting tools: Designed to cut while moving the workpiece from left to right, they are used in applications with specific workpiece directions or setup requirements.
Round nose lathe cutting tools: With round cutting edges, they can be used for general turning, end machining and profiling. They are versatile tools that can perform roughing and finishing.
5、Things to consider when choosing lathe tools
1.Workpiece Material and Characteristics
The workpiece material (such as steel, aluminum or plastic) determines the type of tool material and geometry. Hard materials may require carbide or CBN tools, while soft materials can be processed with HSS tools. The characteristics of the workpiece material must be fully considered when selecting lathe cutting tools.
2.Required Surface Finish and Tolerance
Surface finish and dimensional tolerance requirements will affect the selection of tool geometry and operating parameters. Finishing tools with sharp cutting edges are preferred to achieve high-quality surface finish. Surface finish and tolerance requirements are important considerations in the selection of lathe cutting tools.
3.Cutting Speed, Feed Rate and Cutting Depth
These parameters must be optimized based on the tool material, workpiece material and desired results. Roughing is suitable for higher speeds and feeds, while finishing is used for lower speeds and feed depths. In the use of lathe cutting tools, the proper adjustment of cutting speeds, feed rates and cutting depths is the key to improving processing efficiency and quality.
4.Machine Tool Performance and Limitations
The performance and limitations of the CNC lathe should be considered when selecting cutting tools, such as spindle speed, power and rigidity. Overloading a machine tool can result in poor surface finish, tool wear, and even machine damage. When selecting cutting tools for a lathe, it is important to fully consider the capabilities and limitations of the machine tool.
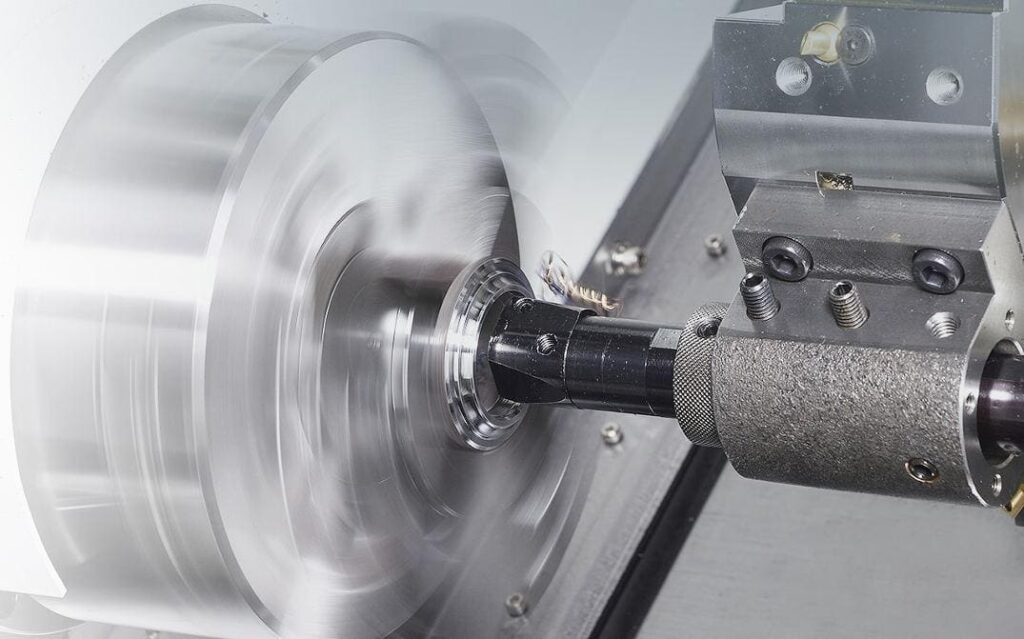
6、How to choose suitable lathe cutting tools?
1.Lathe tool coatings
Coatings such as titanium nitride (TiN) or aluminum oxide (Al2O3) can extend tool life and improve performance. Coated tools are suitable for high-speed machining and machining abrasives.
2.Workpiece material
The workpiece material determines the best cutting tool material and geometry. For example, hard materials such as hardened steel require tools with high hardness and wear resistance, such as cemented carbide or CBN.
3.Type of turning operation required
Specific turning operations (such as roughing, finishing, threading or slotting) will affect the selection of cutting tool geometry and materials.
4.Required part geometry
The complexity and accuracy of the part geometry determine the type of tool geometry required. Complex features or tight tolerances may require tools with special geometry.
5.Computer-aided design (CAD) and simulation
CAD and tool simulation can be used to optimize tool selection and processing parameters before actual production, reducing trial and error and improving efficiency.
6.Sensor integration
Integrating sensors into the machining process can provide real-time feedback on parameters such as tool spindle and cutting force, which helps optimize tool selection and performance.
7.Additive Manufacturing
Advances in additive manufacturing technology have made it possible to manufacture customized cutting tools with complex geometries, which are difficult to achieve with traditional manufacturing methods.
7、 Final
In summary, lathe cutting tools are key components in CNC machining, directly affecting the quality, efficiency and precision of finished parts. Understanding the different types of lathe cutting tools is essential to achieving the best results in any machining operation.
If you are looking for an experienced CNC machining manufacturer, Xavier is undoubtedly your best choice. Xavier has a professional team, equipped with sophisticated equipment, and has the ability to provide high-quality CNC machining solutions. If you would like to learn more or discuss your machining needs with us, please feel free to contact us.